Top Performance
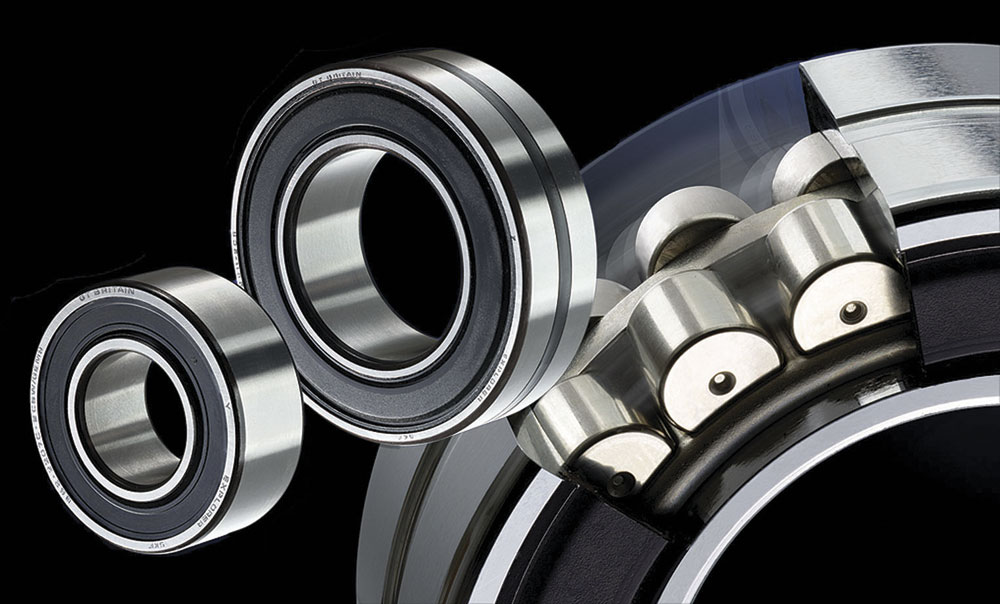
Phil Burge, communication manager for SKF, takes a look at the technology that has shaped the unobtrusive but non-stop bearing component
Millions of bearings are sold globally each year and they are used in almost every item of machinery, frequently becoming ‘fit and forget’ components. The high level of performance in bearings has only been achieved through continuous material development and innovation in their construction.
High maintenance
Improvements in bearing performance have correlated closely with the increasing demands on machinery and equipment, as the quarrying industry complies with stricter, safer and more efficient working practices. Although quarry operators have always paid close attention to cost control, this challenge has become ever greater in recent years, with the need to stay competitive in a climate of economic downturn and spiralling energy costs.
Indeed, taking measures to reduce costly downtime, especially when unplanned machinery failure occurs, offers significant gains. Statistics suggest that maintenance in the quarrying sector represents a significant proportion of operating costs, with figures ranging from 20% to 50% – the highest ratio of all the manufacturing and heavy industries.
Reducing this drain on operational costs not only depends upon the performance of larger engines and gearboxes, but also includes smaller, hard-working components, including bearings. Having recognized this, leading bearing manufacturers have developed a new generation of products, specifically for use in heavy industrial applications, which are virtually maintenance -free and offer a far longer operating life under a wider range of demanding environmental conditions.
So, what is it that makes a simple bearing component succeed under these tough conditions?
Bearing improvements
Bearing materials have come a long way in specification and include the use of high-grade homogenous steel that is more resistant to the effects of wear. The steel has high dimensional stability even at elevated temperatures with enhanced durability and hardness properties to resist long-term wear. As a result, these advanced grade steels offer increased service life, especially in conditions affected by high contamination and/or poor lubrication.
In particular, crack testing carried out on the new high-grade steels prove that they will accommodate far greater depth of cracks before they fail. In an operational context, catastrophic bearing failure can be avoided due to the increased strength of the new material. For medium and large quarry process equipment, this extended time from initial spall through to fracture provides an opportunity to schedule downtime and maintenance activities.
Additionally, the structure of the internal roller and raceway geometries are refined to ensure bearing osculation is kept to its optimum, while higher contact interface tolerances help bearings run smoother and function more effectively with reduced friction, even at exceptionally high or low speeds. Precision manufacturing to optimize internal design has also been responsible for improving the surface characteristics of rollers and raceways to promote efficient oil film build-up during use.
Component design
As well as bearing material specifications and dimension tolerances, design has also been an integral part of improving the efficiency of interacting bearing components, helping to eliminate friction and maintain a lower operating temperature that protects lubricant life for longer and, ultimately, increases bearing reliability.
For example, bearing cages in self-aligning roller bearings are designed to support and retain the roller elements, but crucially, guide and provide space for roller lubrication, preventing contact between the elements. In addition, the effect of roller skew is controlled through self-guiding rollers influenced by internal frictional forces.
Correct positioning
Under operating conditions it is important to understand how the interaction between bearing components ensures efficient functionality. The floating guide ring controls unloaded rollers in position, while maintaining the correct axial loading of the bearings.
Under load conditions, self-aligning rollers ensure the load is evenly distributed over the roller length, irrespective of whether the inner ring is axially displaced and/or misaligned with respect to the outer ring. Maintaining correct roller position under load, especially where loading is offset, reduces friction, wear and risk of smearing while maintaining a stable temperature within the bearing.
Indeed, misalignment has led leading bearing manufacturers to develop bearing systems that are specifically designed to compensate for axial misalignment caused by thermal expansion and movement in rotating equipment. The specially designed, compact CARB toroidal-type bearing combines the self-aligning capability of the spherical roller bearing with the unconstrained axial displacement ability of the cylindrical roller bearing.
The unique design of this bearing type permits smaller, lighter, simplified bearing arrangements to be used without compromising performance. The single-row bearing benefits from long, slightly crowned symmetrical rollers, while the raceways of both the inner and outer rings are concave and situated symmetrically in the bearing centre. The attained optimal combination of both raceway profiles provides a favourable load distribution in the bearing as well as low frictional running.
This critical area of bearing design is a contributing factor in reducing vibration and noise levels and ensures safer, more efficient operation that minimizes the load on the bearing.
Return on investment
Machinery and equipment used daily in the quarrying sector has to continue to meet the challenge of, first, combating tough working environments such as contamination and/or poor lubrication, and secondly, enduring erratic heavy vibrating loads. In these conditions, making the right choice of longer- lasting bearing components is a contributory factor in reducing high operational costs due to regular replacement of lower wearing bearing parts, as well as labour and downtime, therefore lowering the total cost of ownership.
Thanks to the latest bearing technology, maintenance engineers can ensure machinery and equipment benefit from improved performance and greater loading capacity, allowing quarries to operate within the growing regulatory requirements, safety legislation and environmental protection. This is a step in the right direction as the aggregates industry becomes more accountable for efficient use of energy, raw materials and waste.
For more information contact: phil.burge@skf.com