Top Gear
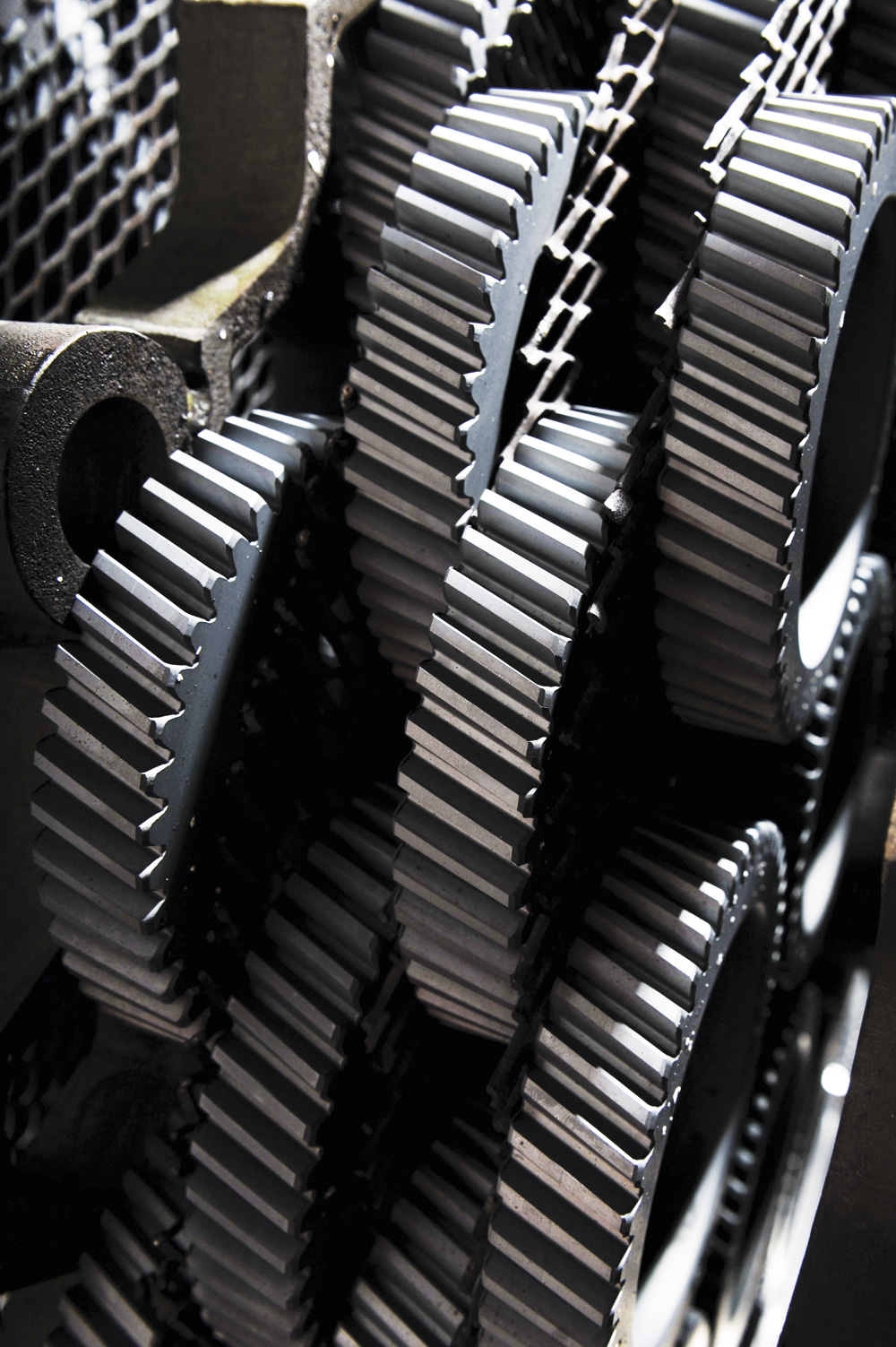
Keighley Laboratories discuss heat treatment services for gears
Gears, particularly load-carrying power transmission units, play a vital role in many industrial applications. Each gear wheel’s performance characteristics, with regard to its load-carrying capacity, operating environment, applied stresses and design life, are determined by the microstructure and grade of ferrous-alloy typically employed, the type of gear and its mechanical specification, the actual gear cutting process and the choice of heat treatment method to achieve the required physical properties.
Engineering studies have found that heat treatment is a core competency that represents around 30% of typical gear manufacturing overheads, so selecting the right heating and quenching process is vitally important for durability, reliability, cost control and the avoidance of over-engineering.
Keighley Laboratories of West Yorkshire, who offer advanced analysis, testing and heat treatment of metals on a single site, provide a range of case hardening, induction hardening, Tufftride ferritic nitrocarburising and other processes for high-performance gears.
‘Ideally, we like to be involved as early as possible in the gear design process, because our metallurgical experts can advise on the optimum material, our heat treatment professionals can identify how to achieve the correct hardness profile at the right price, and our practical experience of heat treating hundreds of thousands of gears and gear teeth means we can often foresee technical issues down the line and avoid them,’ explained Michael Emmott, heat treatment commercial manager for Keighley Laboratories.
‘We pride ourselves on keeping gear wheel distortion to a minimum and processing materials according to their metallurgy and technical requirements, giving the correct strength characteristics for the identified torque transmission.’
Keighley Labs can offer different types of jigging to cope with different gear geometries and assist with distortion control, as well as various quenching techniques such as press quenching for cooling thin or complex parts, and molten salt baths for processes, including austempering and martempering, which keep distortion to a minimum.
‘A variety of gear shapes and sizes demands not only flexibility in the heat treatment process, but also in the quenching, and that’s what we can offer,’ continued Mr Emmott.
Case hardening, and carburising and carbonitriding in particular, are the most commonly used techniques for high-performance gears, producing a softer, tougher core to avoid tooth breakage, while achieving a hard, wear-resistant case to prevent pitting. It lends itself to both high and low volume requirements and a wide variety of gear shapes and sizes, up to around 1m in diameter and 2 tonnes in weight at the Keighley Labs facility.
Case depths between 0.1mm and 5mm are achievable, with PLCs and oxygen probes allowing temperatures and cycle times to be accurately controlled. Test pieces are also highly representative of processed batches, thanks to excellent repeatability.
For larger gears up to 3.5m in diameter and 4 tonnes in weight, or where deeper hardening to 10mm is required, Keighley Labs offer induction hardening which uses high-, medium- or low-frequency alternating current to heat the surface of a gear tooth.
Both spin hardening and tooth-by-tooth or contour induction hardening methods are available, with the tooth-by-tooth techniques particularly suitable for larger gear wheels. Spin hardening is usually a rapid process, often completed in a matter of minutes, whereas tooth-by-tooth (also known as progressive or zone hardening) is more time consuming, although both methods ensure low distortion.
For relatively fragile gear geometries, Tufftride ferritic nitrocarburising is a further option. As a comparatively low temperature, low-distortion salt bath process, it produces a thin, iron nitride compound layer that is particularly resistant to wear and prized for its superior sliding and running properties – suitable for gear wheels. Other specialist heat treatment techniques are available, as well as pre- and post-hardening processes such as annealing, normalising, stress relieving and tempering.
Keighley Labs have experience of processing gears of all types and sizes from several millimetres to several metres, although most fall in the mid-range sizes for mainstream power transmission applications. The company also undertakes volume contracts and special jobs for single-gear sets, although there is generally a premium for smaller projects.
Mr Emmott said: ‘We endeavour to supply a gear wheel that’s fit for purpose, which means heat treating a left-hand and a right-hand helical gear, for example, demands as much individual attention as a batch of massive gear wheels destined for crushing plant on the other side of the world. In either case, if the teeth start dropping off, that would be a catastrophe and that is exactly what we’re paid to avoid.’
Keighley Laboratories Ltd, Croft House, South Street, Keighley, W. Yorks BD21 1EG; tel: (01535) 664211; fax: (01535) 680604; email: info@keighleylabs.co.uk; website: www.keighleylabs.co.uk