Structural Integrity
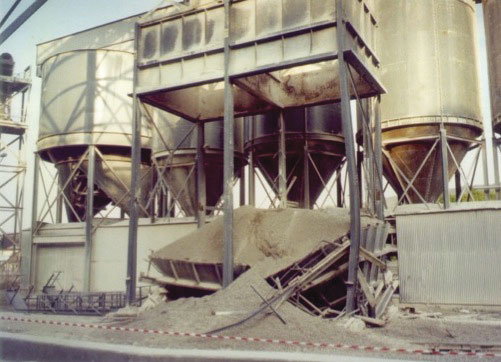
Inspections over the last 10 years highlight significant improvement in the condition of quarry structures
By Ken Irish, principal consultant, Irish & Walker Structural Investigations Ltd
The majority of quarry structures exist in a hostile environment; they are constructed mainly of steel and are exposed both to the elements and to a combination of water and abrasive materials. Coarse-grained sand, graded sandstone, limestone and, even worse, dredged marine deposits, when combined with water, have an unrelenting impact on structures which contain and/or transport such materials within the confines of a quarry.
In the author’s experience, condition monitoring of quarry structures prior to the year 2000 was, at best, carried out on an ‘ad hoc’ basis. This was illustrated in his March 2000 paper, entitled ‘Bunkers and Bins’, which was published in Quarry Management and highlighted the poor condition of some quarry structures at that time.
Background
In the late 1990s and early 2000s, a number of major structural failures occurred at quarry sites (eg fig.1.). By good fortune, no one was seriously injured or killed but the considerable interest shown by the Health and Safety Executive and ensuing pressure from insurance companies played a significant role in encouraging those responsible for the safety of quarry structures to put in place a regime of structural inspections.
Quarry structures
Numerous types of structures are found at quarry sites, some of steel construction, some with concrete frameworks and some conventional brick buildings. Examples of commonly found structures include:
Conventional structures
Both open and steel-clad structures, including open, shed-like structures and structures supporting silos and bunkers as well as crusher units, shakers and hoppers, are commonplace (figs 2a, 2b, 2c & 2d).
Buildings of concrete portal frame construction are less common but are regularly found at sites which produce concrete blocks.
As might be expected, buildings of brick construction and Portakabin-type buildings are found at almost all quarries. They include office blocks, gatehouses, laboratories and canteen facilities.
Steel bunkers, bins and hoppers
Almost always of steel construction, bunkers and silos take many forms, however most have conical or truncated bases and the latter are generally considered as ‘high-risk’ structures (figs 3a, 3b,3c, 3d, 3e & 3f).
Conveyor structures with integral walkways together with supporting trestles and towers
Conveyor supporting structures are invariably of steel construction; they can be of galvanized or non-galvanized construction and either bolted or welded. The bolted types are classified as ‘high-risk’ structures, since these have in the past been the most at risk of collapse (figs 4a, 4b & 4c).
The structures are almost always of lattice girder construction and always incorporate a walkway which is either cantilevered from one side or located centrally between twin conveyors.
Other structures
Many other items also are classified as structures by the quarry industry, such as weighbridges, various types of retaining walls, oil and water tanks, bund walls, stairs, ladders and handrails (figs 5a & 5b).
Other major structures such as jetties, piers, bridges and chimneys are less common but are, nevertheless, present at some quarry sites.
Objective of inspections
The prime objective of structural inspections is, of course, to identify both actual defects and potential defects. Defects might include faults such as minor impact damage or the occasional missing bolt, fractured weld or foundation defect, where no action is required other than to monitor the situation. Alternatively, they might include major problems which could result in the failure of structural elements, structural collapse or spillage of product, or even, in a worst-case scenario, injury or death. Having identified any major defects, the objective is to recommend remedial action indicating a suitable timescale for implementation.
What to look for
The following photographs, mostly taken in the early 2000s, show the somewhat neglected state of many quarry structures at that time but illustrate the types of problems which inspections are intended to identify.
The prime defects fit into three main categories:
Loss of section or ‘holing’ due to corrosion and/or abrasion
Corrosion affects, to a greater or lesser extent, just about every steel structure in quarries. The worst effects of corrosion tend to be on external and internal stiffeners and on the truncated sections of bunkers. The bottom sections of main support columns for most elevated open structures can also be affected, as can structural elements forming lattice girders. Chequer-plate flooring, safety barriers, handrails, stairs and ladders are also affected by corrosion (figs 6a, 6b, 6c & 6d).
Abrasion mainly tends to affect the internal elements of bunkers and, to a lesser extent, certain elements of conveyors. Corrosion and abrasion often combine and the most serious effects of such a combination occur inside bunkers and bins.
Impact damage
Vehicular impact affects external structural elements at or near ground level, often including the main support columns of what are extremely heavily loaded structures (figs 7a, 7b, 7c, & 7d).
Removal and/or repositioning of structural members
Structural members are sometimes removed and/or repositioned for the convenience of vehicular access or for the installation of conveyors, and this is often done without any kind of check on structural integrity (figs 8a, 8b & 8c).
Other typical problems
- Crushing of steel connections, where heavy impact occurs from crusher units (fig. 9a)
- Handrail defects caused by either corrosion or impact (fig. 9b)
- Foundations being undermined if to too close workings (fig. 9c)
- Missing bolts
- Fractured welds
- Spalling or cracking of concrete on both foundations and above-ground structural members
- Excessive vibration.
Typical inspection regime
During the past decade many quarry operators have adopted a system of regular structural inspections.
Inspection procedures vary somewhat throughout the industry but a typical approach is for non-engineering staff to be trained and authorized to carry out visual inspections on an annual basis, with trained engineering personnel inspecting structures every three years.
The annual inspection tends to cover items ranging from the safety of barriers to the condition and safety of major items such as bunkers and silos, their supporting structures and the lattice structures supporting the conveyors and walkways, together with their tower and trestle supports. The results of these inspections are recorded in a simple report format.
Triennial inspections cover the same ground but with the addition of non-destructive testing, which can include the physical measurement of plate thicknesses and the withdrawal of bolts for inspection.
The reporting process for both annual and triennial inspections includes recommendations for remedial work or work of a preventative nature and/or, in specific cases, the need to call on the services of a chartered structural engineer. The report usually sets down the timescale for the implementation of each recommendation.
Follow-up work
In the author’s experience, follow-up worksrecommended in the reports prepared by engineering personnel, ie the triennial reports, tends to be carried out diligently and within the timescales set down; however, recommendations made in annual reports are not always given the same priority with the result that recommended work is either not carried out within the set timescales or, in some cases, not carried out at all. Fortunately, the works which tend to be ignored are often items of lesser importance.
In the author’s experience, these systems have led to significant improvements in the condition of structures over the past decade, a fact illustrated by a recent survey carried out by him at a privately owned quarry.
The three-day survey of more than 50 silos and hoppers, together with approximately 30 conveyors, as well as numerous items of plant, retaining walls and other structures, revealed no significant defects. Only minor impact damage, a few missing bracings and some issues regarding excessive spillage on walkways were recorded. One significant observation was that the vast majority of the structures were made of galvanized steel; clearly, lessons have been learnt.
Possibilities for further improvement
Consideration could be given to introducing a formal Code of Practice for the inspection of structures throughout the quarrying industry. This could have significant health and safety benefits, particularly in respect of small quarry operators.
The industry’s reluctance to use paint, recognized by the author more than 10 years ago, continues and is one area where improvement could be made, particularly on non-galvanised structures. More regular painting could assist greatly by decelerating the rate of corrosion on external surfaces and thus prolonging their working life.
About the author: Ken Irish has been deeply involved with quarry structures for the past 15 years, having worked closely with a number of quarry operators. He lectures regularly on ‘The Inspection of Structures’.