Reducing The Cost Of Bearing Failure
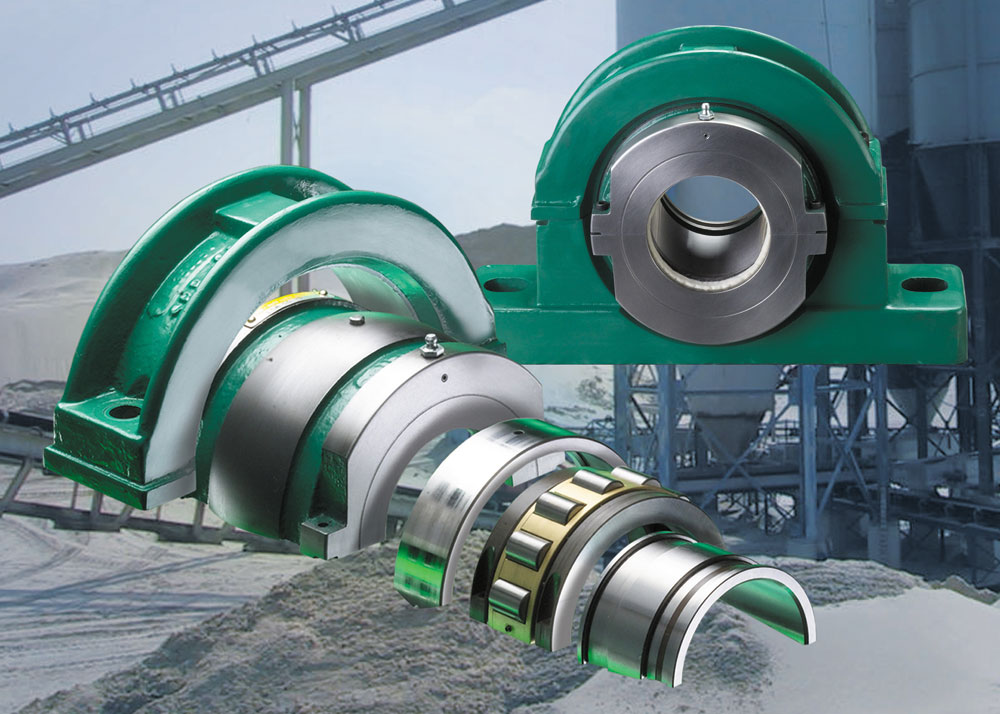
Adrian Menzies, sales and marketing director of Revolvo Ltd, explains why the lowest-cost bearing solution for the OEM is usually the most expensive for the end-user
Despite all the recent discussions regarding whole-life costs, the conflict remains between the requirement of OEMs to achieve the lowest installed cost for new equipment and that of the end-user for improved reliability and longer operating life.
The OEM is all too aware that quoting a high price can cost an order; yet as, for example, the US space programme revealed on many occasions, things tend to go wrong sooner or later with equipment that is built down to a cost. Unfortunately, despite many painful lessons, the cost-down philosophy still appears to permeate all levels of industrial supply from bearings and hydraulic/pneumatic components to drives and gearboxes. What this means for the eventual end-user of these products – probably a manufacturer with deadlines to meet – is a potential timebomb in the production system. In the modern world, with downtime a key production indicator (KPI), this is clearly not acceptable.
Increasingly, manufacturing companies are waking up to the fact that to achieve performance gains and optimize the full potential of their existing assets, they must achieve improved production efficiencies. However, to realize these efficiencies downtime must be minimized, which in turn means a whole new approach to the specifying of components and equipment that might cost a little more initially, but are fitter for purpose and more economic over the longer term.
One product area that aptly highlights this philosophy is rolling bearings. Overwhelmingly, solid bearings comprise the major segment of rolling bearings in use today, yet they are difficult to fit, impossible to inspect while in place, and even more difficult to replace when they fail. However, because solid bearings are inexpensive, hardly anyone questions the fact that they may not provide the most cost-effective long-term solution in all applications. They do not, of course, although the alternative of split roller bearings can be initially considerably more expensive, which is why they are generally used only in continuous process industries where bearing failures cannot be tolerated.
[img_assist|nid=12293|title=Split roller bearing|desc=|link=none|align=left|width=280|height=200] But the same is true in manufacturing industries; so why do process industries bear the additional cost? The answer is threefold: much easier bearing fitting – typically a split roller bearing (SRB) takes only 15% of the time taken to fit a solid bearing of the same size; the ability to inspect the bearing in situ; and the ease and speed with which split roller bearings and their cartridges can be replaced if there is a problem, without requiring extensive machine dismantling.
From the technical, economic and design points of view, split roller bearings offer a host of advantages and cut downtime significantly. Basically, the simplicity of fitting a split roller bearing, compared to a solid bearing, is a major factor in its longevity. Unlike solid bearings, SRB bearings are totally split to the shaft, a design that both simplifies and expedites installation, and cuts downtime to approximately one-eighth of that required to replace solid bearings of the same size. In addition, SRB bearings can have a longer life span because they cannot be cross-located. They also provide superior sealing arrangements, which means a longer bearing life with greatly reduced levels of maintenance.
A further advantage is that the design of SRB bearings allows for complete bearing removal and replacement by simply supporting the shaft. There is no need to lift the shaft, or to obtain access to the shaft ends, therefore expensive and awkward-to-handle lifting equipment is not required. This intrinsic feature is extremely valuable, generally, but especially regarding large machines where sheer weight and size can be a barrier to fast and effective servicing. It allows for much faster bearing replacement, which can save continuous-type businesses, such as the quarrying industry, a lot of money in costly downtime.
The example shown in table 1 illustrates the savings in downtime that can be accrued using SRB bearings. The data is taken from an actual example where solid bearings were replaced by SRB split bearings due to the costs that were being incurred as a result of extended times for bearing installation and replacement.
As the table shows, the initial purchase costs for the SRB split bearing far outweigh those of the solid bearing. However, this is the only area where solid bearings have the advantage. Once the costs of labour to replace failed bearings and production losses are considered, the positions are reversed with the total overall costs for the SRB split bearing being approximately one-fifth of those of the solid bearing.
Supporting the illustration is the recent application of Revolvo SRB split bearings at a number of mines owned by Anglo Platinum in South Africa. The bearings were employed to replace solid bearings on vent fans. These fans are crucial to production, and with downtime costs that could reach R500,000 (£72,000) per hour, the ability of the SRB split roller bearing to be installed in just 15% of the time taken to fit a comparable solid bearing, meant that their downtime costs were kept to an absolute minimum. As evidence of the success of Anglo Platinum’s conversion to Revolvo SRB split roller bearing units, to-date orders in excess of R900,000 (£130,000) have been received, providing similar bearings for fans at a further seven mines.
Revolvo Ltd, Queens Cross, Dudley, W. Mids DY1 1QW; tel: (01384) 844000; fax: (01384) 844255