Peak Performance
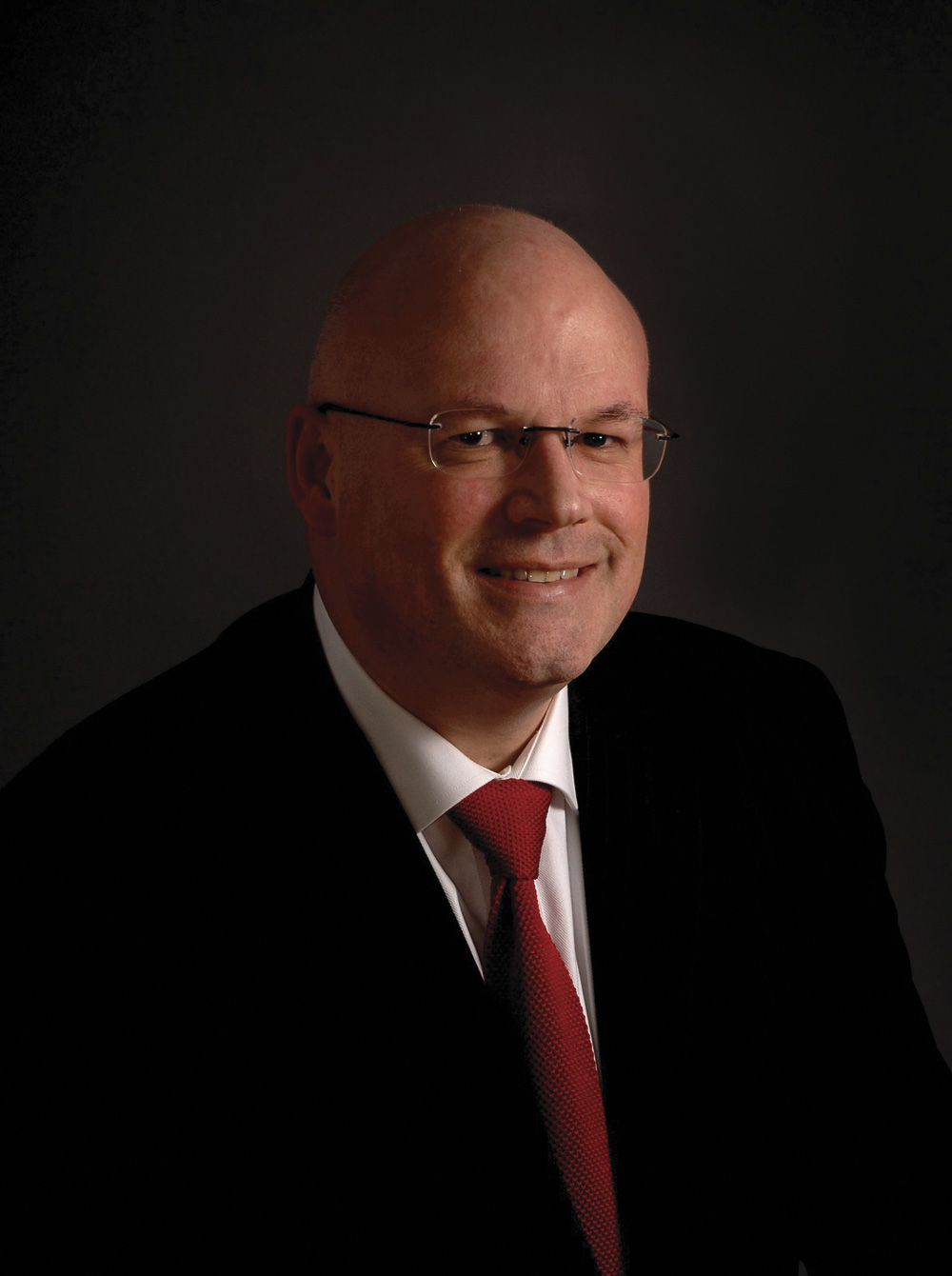
Ian Ritchie, managing director of Brammer UK, explains the role of maintenance and asset management in optimizing plant performance
As UK industry starts recovering, manufacturers are experiencing almost unprecedented performance improvement challenges with increasing raw material and commodity costs, extended lead times and continued tight budgetary, employment and capital investment controls.
However, the key drivers of manufacturing competitiveness and profitability remain the need to optimize output and efficiency while reducing operational costs. If efficient, reliable plant is key to success, the maintenance and asset management strategy is critical.
A best-in-class approach to optimizing plant performance will align the strategies, goals and metrics of production and maintenance teams, fostering collaboration to aid effective prioritization and decision-making.
Common objectives should be standardized around metrics including overall equipment effectiveness (OEE) and asset downtime – how long assets are offline against total availability.
To maximize OEE and minimize downtime, plant must be well operated and maintained, with vital spares available when needed.
This is brought firmly into focus by the fact that unplanned downtime can throw manufacturing schedule adherence into disarray. As well as costing thousands of pounds per hour, lost production time can mean missing an order deadline and consequential customer loss.
It can also be further complicated by issues of ageing plant and equipment. Since the recent recession, economic and financial pressures have influenced a general reduction in capital investment in new plant and equipment. Many companies are instead focused on driving existing assets over an extended lifespan, frequently while working within reduced operating budgets.
An effective maintenance and asset management strategy is absolutely critical to meeting these challenges while delivering on operational performance, service and overall profitability targets.
Developments in maintenance strategy
A best-in-class strategy focuses on proactive, condition-based maintenance management. This will go a long way in helping to avoid asset failure and fixing potential production asset problems before they create unscheduled downtime.
Making effective asset maintenance decisions requires the right data at the right time and in the right format. This may include adopting condition-monitoring techniques, such as vibration analysis, thermographics, oil sampling and acoustic analysis, to help monitor plant performance.
The impact of this approach is being widely proven in safeguarding production schedules, adding efficiencies, reducing maintenance costs, improving spares management and even lowering energy consumption.
For example, scheduled maintenance to a motor whose energy usage is exceeding the level expected can help identify contributing factors and allow corrective action. This illustrates how energy consumption data can inform operational decision-making and contribute to OEE.
Whatever approach is adopted, its goals and metrics should be closely aligned with those of the production and procurement teams to ensure a consistent, collaborative approach to spares purchasing and management.
Best practice in maintenance management
Maintenance spares management also contributes significantly to overall efficiency, maintaining production continuity and avoiding downtime.
A successful sourcing strategy focuses on total cost of ownership, with factors such as component lifespan, criticality, reliability, reduced maintenance and service intervals all informing the purchasing decision.
Ultimately, the strategy should ensure the most common and machine-specific spares are always available. Stock value and stock-keeping units held should be minimized, with supplier numbers minimized to reduce inventory and working capital tied up in spares as well as the transactional costs associated with maintaining duplicate suppliers.
The strategy should also focus on engineering spares standardization, which can significantly reduce inventory and cash tied up in stock, while ensuring a consistent component standard is used across the asset base.
The benefits of outsourcing
Purchasing spares for production equipment maintenance and repair is often complex and both time- and resource-consuming. Well managed, however, it can generate cost savings through demand reduction, reduced inventory and production and maintenance improvements.
Where the procurement and spares management process is large scale or complicated, there is much to be said for outsourcing part or all of it to a specialist maintenance, repair and overhaul (MRO) partner. This partner should offer procurement and supply chain management expertise, combined with value-adding services such as condition monitoring, energy audits, drive system design and lubrication programmes. This enhanced support can free valuable in-house procurement, production and maintenance capacity to focus on improvement projects, to increase production output and efficiency.
Outsourcing some, or all, MRO spares management functions is consistently proven to reduce total acquisition costs and working capital, while the right partner can also add value to the engineering team to support plant uptime and production output optimization. In the current economic climate, with capital investment restrained and plant asset life therefore extended, an effective maintenance strategy is key to improved manufacturing plant reliability and higher operational and financial performance.
For further information visit: www.brammer.co.uk