No Wear To Be Seen
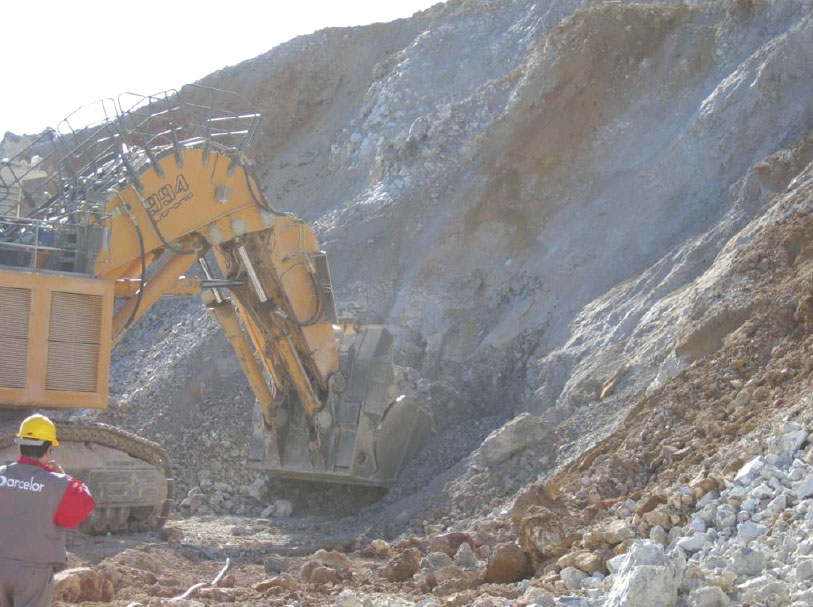
Creusabro 8000 exceeds expectations in Liebherr abrasion test programme
By Gilles Gros, product manager, IMS Group, and Nick Taylor, business development manager, IMS UK
Following the results of a comparative abrasion test programme run over 12 months in extreme mining conditions, Liebherr Group are now offering customers the opportunity to purchase crawler excavators and other earthmoving equipment with buckets equipped with Creusabro 8000 wear parts. The test programme, run in conjunction with IMS Group, proved that the use of Creusabro 8000 steel increased the wear life of the mining buckets by more than 46%.
Background
A world leader in the development and manufacture of mining and construction machinery, Liebherr are also acknowledged as suppliers of technically innovative and user-oriented products. An important area of development for the company was the ability to offer an improved alternative solution to the standard material fittings on excavator buckets, to provide a longer wear life option for the work-front facing components in very severe mining and quarrying applications.
Mining buckets used with crawler excavators are conventionally manufactured using high-yield-strength steel for the body with 400 and 500 HB water-quenched steel wear plates welded into position. This provides sufficient strength and an acceptable level of abrasion resistance.
Testing process
The test programme was carried out at the Assarel copper mine, in Bulgaria, which is renowned for its extremely abrasive conditions combined with fluctuating temperatures and variable weather, providing very harsh conditions under which the comparative test programme was run.
Two identical mining buckets were used for the test, both mounted on a Liebherr ER 994B – 771/14755 excavator. Both buckets were produced by Liebherr at their plant in Colmar, France, and were manufactured as two-part front shovel buckets with a mobile rear door for unloading the excavated material. The individual parts of both buckets were manufactured as shown in table 1.
To assess the overall difference in performance between mining bucket no.1, equipped with Creusabro 8000 wear parts, and mining bucket no.2, equipped with standard 400/500 HB steel wear parts, the testing schedule monitored:
- the thickness of the wear parts over a period of time
- the thickness of the cross-sectional beam on the static rear of the bucket (manufactured from the standard high-yield-strength steel)
- the tonnages of material moved over the same period of time.
Working conditions and parameters
Both buckets were tested by digging directly at the mine’s working face, in areas where the face had been blasted and also in areas where the face was in its natural state. The working face comprised of a range of different minerals, including sulphur, bornite, malachite, azurite, and cuprite, as well as a wide range of grain sizes.
The front shovels were operated for 23h a day, seven days a week, extracting and unloading the heterogeneous mineral into dumptrucks.
Mining bucket no.1, the IMS Group test bucket equipped with wear parts manufactured from Creusabro 8000 steel, was operated for a period of six months from October to March, through the ‘wet season’.
Mining bucket no.2, the original Liebherr unit equipped with wear parts manufactured from 400/500 HB steel, was operated for six months from April to October, through the ‘dry season’.
The test conditions for mining bucket no.1 were more severe than for bucket no. 2, as it was operated through the winter months, thus enduring extreme cold and moisture, which can cause additional stress and corrosion to the steel.
Results
The results obtained in the comparative abrasion test are summarised below:
Bucket no.2
Mining bucket no.2 – the original Liebherr unit used throughout the dry season from April to October – was utilized for a total of 2,540h before requiring maintenance. Severe wear was seen in accordance with the extremely abrasive conditions resulting from the sliding and impact of the material.
Specific observations:
- The level of wear found in the shovel bucket was very serious due to the abrasion effect from the continual throughput of the excavated material from the working face.
- Owing to the concentrated wear at the back of the shovel bucket, due to the weight and momentum of the high tonnages of material being extracted and dumped, the wear-protection strip extremities were totally worn away on the back of the bucket and could not be measured.
- Measurements taken showed the thickness of the beam (originally 120mm) had been reduced to 22mm as a result of the abrasive effect of the extracted mineral on the steel.
- Other consequences observed as a result of the continual wear on the inside faces of the bucket were loss of mechanical resistance and distortion leading to risk of rupture and the need for critical maintenance. However, no repairs were required on the outside surfaces.
Bucket no.1
Mining bucket no.1 – the IMS Group Creusabro 8000 wear parts-equipped test bucket – was utilized from October to March throughout the more severe wet season, which included rain, snow and extremely low temperatures. The bucket was used for 2,600h and, on inspection, required no maintenance or refurbishment at that time. It went on to operate for a total of 3,700h at which point minor refurbishment was required, which was primarily cleaning.
Specific observations:
- Despite the longer working hours and more extreme conditions, the Creusabro 8000 significantly reduced the level of abrasion and wear, thus preserving the integrity of the shovel bucket and allowing it to operate to its full potential.
- Some grooving in the structural base of the bucket was observed, due to the weight and momentum of the high tonnages of material being extracted and dumped, but the level of maintenance required was minimal.
- The wear protection strips on the static back of the shovel bucket were all in good condition.
- There was no visible dimensional difference between the initial alignment on the back of the shovel bucket and the post-test alignment.
- The wear-protection strip measurements that could not be taken on bucket no.2, because they had been totally worn away, were easily measured on the Creusabro-equipped bucket and showed the abrasion-resistant steel had performed extremely well compared with the standard water-quenched 400/500 HB resistant part, with minimal wear being recorded.
Conclusion
Table 2 provides a summary of the overall conclusions of the 12-month comparative abrasion test trial, showing the Creusabro 8000-equipped hardware provided more than a 46% increase in the working life of the shovel bucket. The ability of this grade to work-harden offers significant increases in service life compared to conventional 400/500 HB water-quenched steels.
The trial, which was conducted under the most extreme circumstances, showed that the Creusabro 8000 wear parts greatly exceeded all expectations in the comparative abrasion test programme. As a result, Liebherr have now decided to offer customers the opportunity to purchase crawler excavators and other mining equipment with buckets equipped with Creusabro 8000 wear parts. Indeed, based on these results, the Assarel copper mine has already placed an order with Liebherr Mining Division for five new buckets, all of which will be lined with Creusabro 8000.
For further information call IMS UK Ltd on tel: (0121) 326 3100; fax: (0121) 326 3105; email: imsuk.abro@ims-group.com; or visit: www.ims-uk.com