Heavy Metal Maintenance
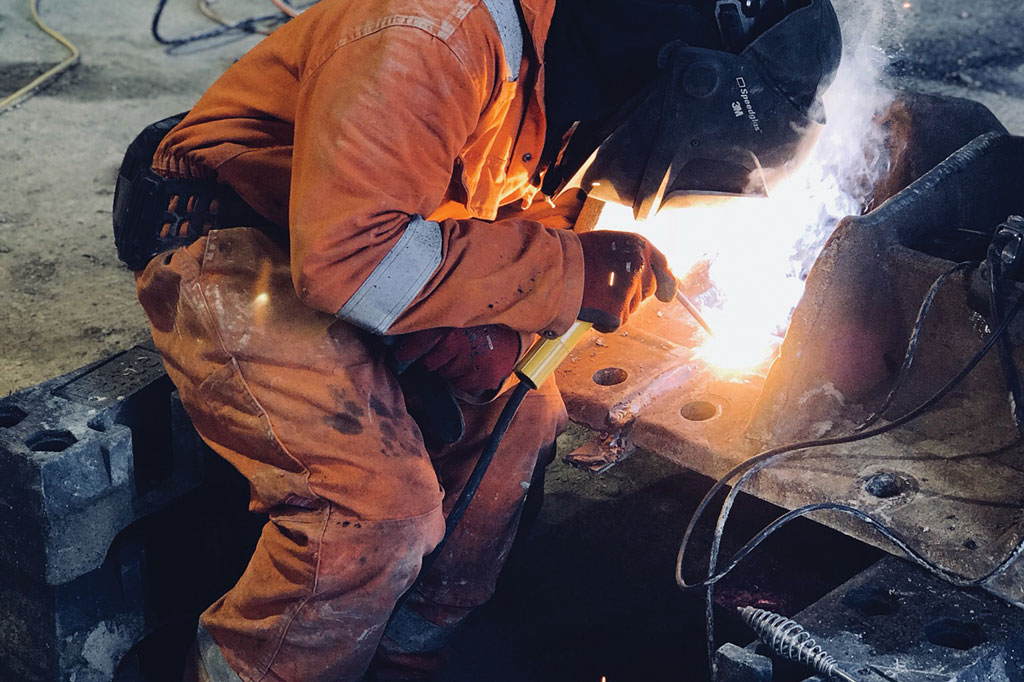
First published in the March 2019 issue of Quarry Management
WJW Engineering successfully complete welding repairs to Kleemann impact crusher apron at Huntsmans Quarry
WJW Engineering, specialists in welding, fabrication and mechanical repair services for aggregates/construction plant, commercial vehicles and structural steelwork throughout the UK, were recently tasked with repairing a Kleemann impact crusher apron at Breedon Southern’s Huntsmans Quarry.
After several years of hard work, the apron had been left with major cracks. Previous ‘quick-fix’ repairs had now failed and the steel had been left brittle after work-hardening through use. For maximum cost-efficiency, the apron needed to be repaired to a high standard in as short a time frame as possible.
Given the extent of the cracks, had the apron been intended for full-time use again, WJW Engineering’s advice would have been to replace rather than repair. However, in this instance, Breedon had already purchased a replacement apron for the machine and, once repaired, the broken apron was to be stored as spare part until needed.
WJW Engineering found that the middle section of the broken apron had taken the brunt of the damage and one major crack had re-opened across almost a third of its length, splitting in two as it moved towards the centre. In addition, all three of the central gussets had cracked and needed to be cut out and replaced.
In the first instance, all three wear plates had to be removed, and as most of the captive bolts had seized, these needed to be cut out. Once the plates had been removed it was possible to cut out the gussets. This revealed yet more cracks and exposed the true extent of the damage.
Next, the main crack was chased back and bevelled ready for welding. At the ‘Y’ (where the crack split in two), it became clear that the angle of the crack was on a horizontal plane through the apron. Consequently, the decision was made to remove the entire section, but before this could be done braces were welded on the front and back of the piece, to avoid distortion through heating and welding,
Once the cracked section had been cut out it was possible to replace it with new 35mm thick steel plate. The work piece and the new steel were both bevelled to a 37.5° angle (to give the best results) and backed. ‘Backing’ is where a sacrificial piece of steel is used underneath the piece to ensure the root weld pass penetrates the full depth. The steel is then cut and removed once welding is complete (see fig. 1). This is only possible, however, where both sides of the piece can be accessed with ease. Once bevelled and backed, the new steel was welded in and the main crack was completely welded up.
The welding alone took more than 4h to complete using the MMA (manual metal arc) welding process. As this job lent itself to the use of long welds, WJW Engineering opted to use low-hydrogen 7018 welding electrodes for the repair because, in such circumstances, they provide the best all-round strength and ease of use.
All that remained now was to weld in the three gussets. Prior to doing this, two holes for wear plate bolts had to be cut through the new plate insert using a mag drill. The piece was prepped and a new 25mm steel plate was cut to size. Both the piece and the steel plate were bevelled, ready to be welded in. To achieve an adequate weld size for the thickness of the material and to fill the bevel, more than six passes were made on every joint.
Once the gussets had been welded in there were then just a few minor cracks to chase and fill. Finally, new wear plates were fitted to complete the repair work and the apron was put into storage, ready for use as a spare part when required.
For more information visit: www.wjwengineering.com
- Subscribe to Quarry Management, the monthly journal for the mineral products industry, to read articles before they appear on Agg-Net.com