Less Downtime, More Uptime for Repair and Maintenance
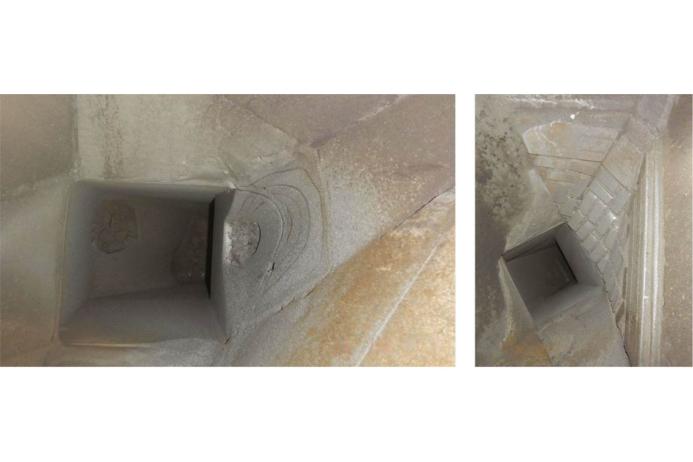
First published in the September 2023 issue of Quarry Management as Less Downtime, More Uptime
UK distributors WJW Engineering outline the benefits of using Ferobide weldable tungsten carbide wear plates
Ferobide is a relatively new tungsten carbide composite material. Field trials began in 2015 and since then the material has proven its performance in a multitude of applications. Until now, sales have been focused on overseas markets due to the greater volume of production outside the UK.
As on-site welders and fitters across the quarrying industry are constantly maintaining plant with wear issues, so much time is spent on re-lining hoppers, fabricating new aprons, removing and rebuilding feed-out assemblies, and the list goes on as wear issues arise from processing abrasive material. What can be done to prevent this wear? How can one limit the downtime for maintenance?
As with most solutions, the initial consideration is within the design of the original equipment. For those who are looking at new equipment, special attention should be given to the type of material to be processed, the speed of the system, the distance and attack angle of material drops, and the rates of transfer of material through hoppers and bins.
It is important to ensure that your manufacturer has experience with the given aggregate. Size, shape, and sharpness of material have a great bearing on the rate of wear. Be sure to discuss options for hardened steel in high-wear areas – often the additional cost of hardened plate does not outweigh the benefits.
Be sure that the new plant is ‘maintenance friendly’. So many repairs that are carried out could be expedited significantly if there had just been some thought given to maintenance. Access is probably the most valuable time-saving asset that can be achieved by design.
Some of the simplest modifications or options can make a real difference when it comes to maintenance. Design of feeding and chute drop angles can make a big difference to wear as well. Be sure to discuss this with your manufacturer.
If you are running your existing plant and are looking for solutions to improve the ease of maintenance and cut downtime, then there are several areas to focus on.
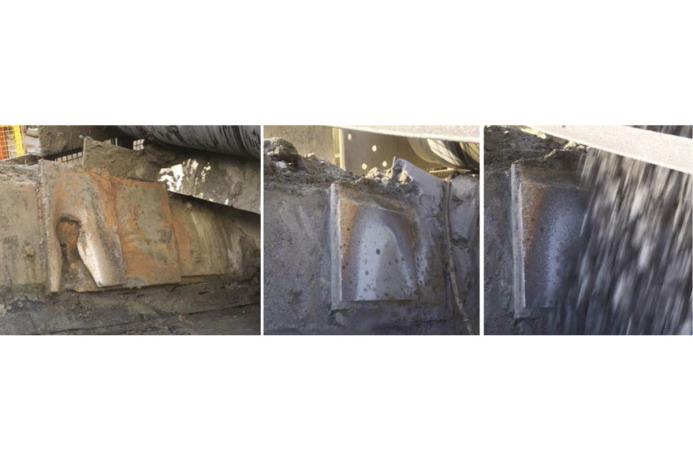
For smooth operation of conveyor rollers and scrapers, there are quick fixes that can increase the service life of conveyors. So often conveyor systems are found to have at least one or two failed roller bearings, and carrying out a very small and simple maintenance task can have a huge impact on the efficiency and longevity of system components. It is recommended that checks should be carried out at least weekly.
We find conveyor scrapers to be a contentious issue among site maintenance staff. They do not need to be, with the options available such as Flexco cleaners and others, it is another straightforward item to rectify to increase the life and efficiency of your plant.
From conveyors to feeds to storage, the transfer is usually where the wear makes an impact. If access prevents easy maintenance, key improvements are required. Once hoppers and feeds are easy to get to, maintenance can be much safer and more efficient. If you have great access but lack replaceable wear parts, this is another significant area to improve on.
Take the time during plant shutdowns to create a folder of cardboard wear plate profiles. If you can take measurements of chutes and hoppers or even make templates, you will have a much easier time when cutting new liners for installation. If you can supply your maintenance engineers with templates, they can have plates cut and drilled in advance to lessen downtime when fitting.
Consider improving the material used for liners, so whatever you are using – is it the most efficient? There are more wear-resistant materials on the market now than ever before. Take the time to consider your requirements, as this could significantly save on maintenance costs and time.
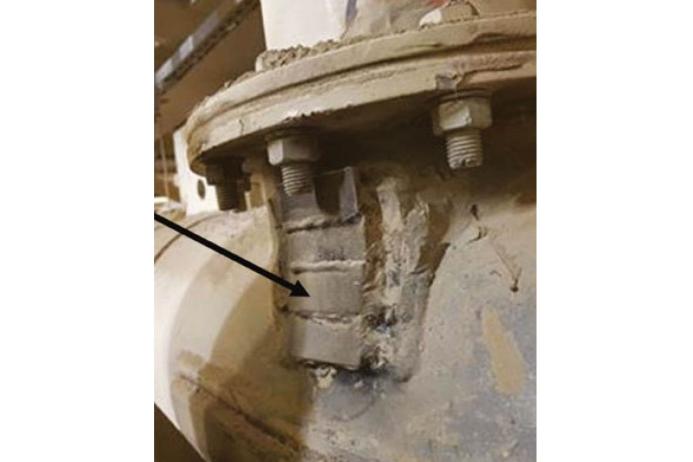
For large areas, hardened steel plate such as Hardox or a chromium carbide plate could be beneficial, but for condensed, smaller areas of wear, Ferobide could be a solution? Ferobide has been used in place of hardened material in extreme wear areas with impressive results, generally outlasting chromium carbide plate by as much as 13 times.
Although Ferobide costs more than the other materials mentioned, the expense can be easily justified when looking at the downtime saving. One customer, for example, had downtime costs amounting to £3,000 per hour. To replace a lining in a chute on their plant, the time it took to weld in a patch varied between a couple of hours and a half-a-day’s work.
Regardless of the time, the area of extreme wear affecting the customer’s chute was approximately 100mm x100mm on each side. Two 6mm Ferobide plates (200mm x200mm) were recommended as a solution, which cost in excess of £800. They will outlast an HB500 plate by 10 times in this application – reducing downtime, installation, and welding costs (repairing 10 patches) totalling over £60,000 for the customer.
Often, weak points reveal themselves when it is too late to do anything about them. A plant is running and production for the week cannot be halted. This type of maintenance is known as ‘firefighting’ and businesses have to use all their available resources to get the problem rectified as quickly as possible.
Experienced operators have a well-stocked store of spare parts, including bearings, rollers, scrapers nuts, and bolts. They will also have steel for patching and scrap for overcoming unique problems.
WJW Engineering argue that quick repairs do not have to mean temporary repairs. If you have a hole in a chute for example, fit a liner to the repair patch so that a future fix is only a couple of bolts away. Again, small changes to methods used can make good long-term gains. Of course, for those moments when you do just need a quick patch – Ferobide can be used as an external patch to ward off the worst of the wear.
For more information visit: www.wjwengineering.com/ferobide
Subscribe to Quarry Management, the monthly journal for the mineral products industry, to read articles before they appear on Agg-Net.com