Effective Maintenance
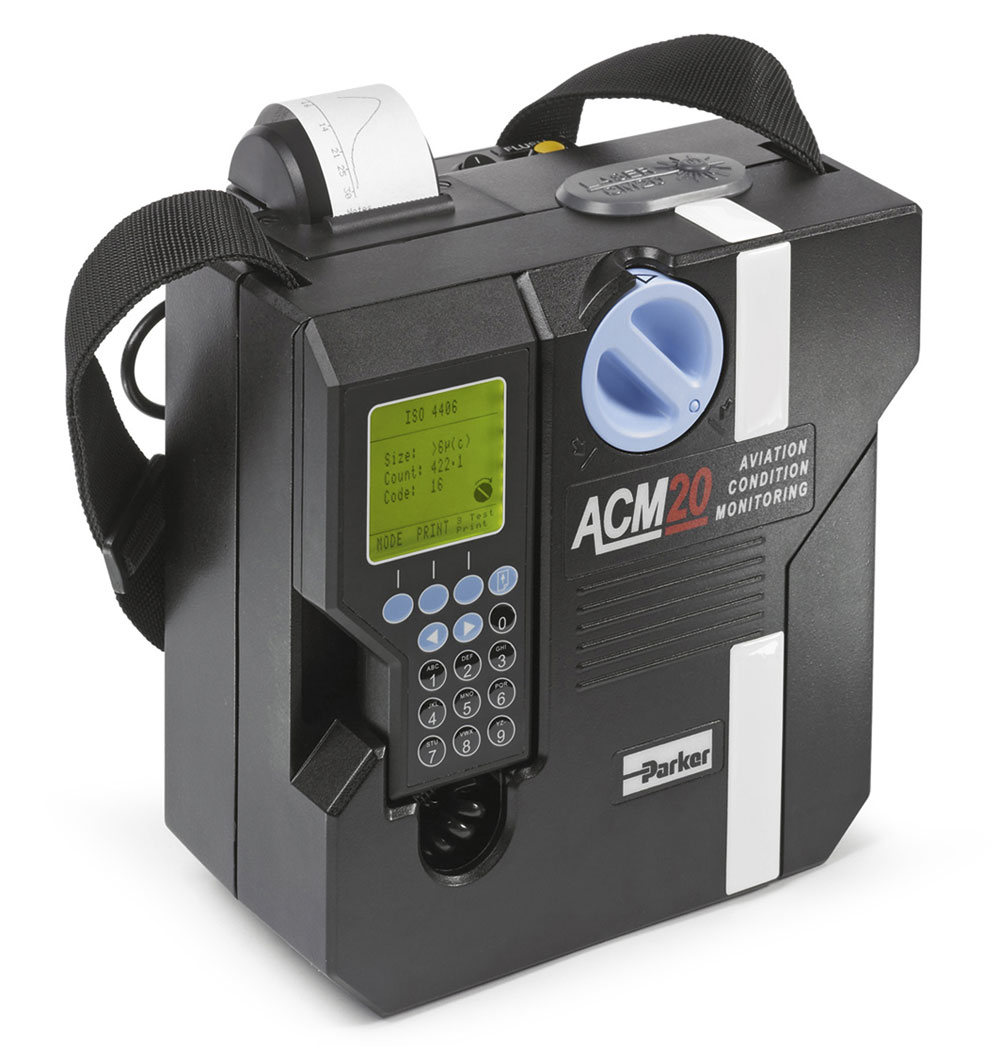
Marco van Boven, marketing manager for the European hydraulic filter division of Parker Hannifin, highlights the importance of effective hydraulic oil and diesel filtration for extremely demanding quarrying applications
There are signs of minor positive economic growth returning to the manufacturing sectors, with the mining and quarrying industries experiencing a 0.6% production output increase between June and July 2010.
However, this growth in production needs to be set against the figures for the same period last year, where output was 7.7% higher. So, although the general belief is that there is light at the end of the tunnel, companies are still under considerable pressure to protect their operating margins as they try to shake off the effects of the global economic downturn.
As such, many businesses are increasingly looking for ways in which to cut costs and often manpower, while boosting performance and productivity. In particular, maintenance and downtime represent a significant predicament for many companies. In some cases, maintenance continues to be perceived as an unavoidable expense, yet in others, it is accepted that planned maintenance is a key factor in enhancing output.
For example, maintaining the optimum quality of hydraulic oils and lubricants can optimize the efficiency of plant and equipment, thus increasing productivity, and ultimately, profitability.
For most quarrying and mining companies, the maintenance of hydraulic systems is vital, particularly when it has been estimated that 85% of hydraulic system failures can be attributed to hydraulic fluid contamination. The need for maintenance becomes even more critical when companies look at the harsh and demanding environments in which machinery is expected to operate within the quarrying and mining sectors.
Indeed, the challenging operating conditions alone are a key contributing factor in oil contamination, with the problems of moisture and dirt ingress via faulty seals and gaskets, and generated contamination containing metallic particles from rotating surfaces and bearing wear, having been common issues in these industries for a considerable number of years.
Although hydraulic oil systems are used in most production processes, they are often set in fixed locations and may not always deliver the optimum performance. Additionally, some static stand-alone systems are poorly protected from contamination, while mobile equipment, such as forklifts and off-highway equipment, can be difficult to service in situ.
To address these issues, leading manufacturers such as Parker Hannifin have developed a new generation of high-pressure filtration and analysis technologies that make it quick and simple for engineers to protect and maintain equipment wherever it is in operation. Ultimately, the use of such systems can cut maintenance costs and eliminate downtime, while increasing productivity and improving the bottom line.
For example, the latest generation of sensors can be connected dynamically as inline devices to systems such as oil condition monitoring instruments. Parker’s new icountPD OCI (Oil Cleanliness Indicator) and H2Oil water in oil monitor are essentially portable instruments complete with hand-held data-capture and LCD display units. In addition, they have been developed to offer higher levels of measurement performance, in particular greater accuracy and repeatability.
The icountLCM20 portable particle analyser, for instance, uses the latest laser technology in which a beam of light is passed through the oil to detect contamination quickly and accurately. As particles pass the photo diode sampling point, the reduction in light intensity transmitted, which is proportional to the particle size, is measured and recorded.
Data can then be downloaded into trend analysis software that allows even subtle deteriorating changes in a fluid’s condition to be identified and acted upon before any abnormal wear and potential damage to components.
With test cycles taking as little as 2min, these types of devices lend themselves to predictive maintenance programmes across large-scale sites, allowing engineers to identify particle contamination or moisture in oil before it can become a significant problem, thus eliminating complete oil changes and damage to critical equipment.
While implementing this latest generation of condition-monitoring technology helps engineers to optimize the performance, efficiency and service life of machinery, it should be noted that for these sensors to be very effective they need to be combined with high-efficiency filtration systems. This prevents problems from arising in the first place by ensuring that contaminants are removed before they can cause potential damage.
Furthermore, the latest filtration technology has been developed to remove water and particulate contamination efficiently and automatically, further improving the performance and service life of fluid-power equipment. The design and specification of such systems does, however, require considerable care.
If they are not properly designed or sized, pressure loss across filters can significantly reduce the efficiency of hydraulic systems, at worst, in some cases impeding overall system performance, reducing operating speed and affecting product quality.
Correct filter selection must also allow for overall operating conditions in order to minimize the cost and disruption associated with filter care. The first issue to consider is the filter material itself, as overall pressure drop is determined by the type and efficiency grade of material used and the area of material available.
In mobile quarrying and mining equipment, the size and location of the filter can be particularly critical, since space on the vehicle can be extremely limited, and designers must balance protection of the filter equipment from damage in service with ease of access for maintenance.
Additionally, applying a specific filter material has a significant impact on the dirt-holding capacity, which can help extend service life. To extend the life of a filtration system, Parker use multiple layers of different filter materials to ensure that larger particles do not prematurely overwhelm the finest filter materials in the system. Other recent advances in filter material modify the composition and construction of standard glassfibre materials to improve their strength and dirt-holding capacity while reducing resistance to flow.
Parker’s Microglass III media, for example, can reduce dynamic pressure across the filter by 10% and, simultaneously, significantly improve element life compared with a conventional filter. The company’s new EPF iprotect Series (Environmental High Pressure Filters) also provide effective solutions for system designers and maintenance engineers alike.
With the filter element staying in the filter bowl, more compact solutions are possible, reducing the time required for servicing typically by over 40%. A new, innovative, bypass valve reduces pressure loss across the filter and shortens the bypass opening period by minimizing the valve’s hysteresis. High-pressure filters fulfil an important function to protect sensitive system components from contamination and represent a significant contribution in achieving a safer functioning of the system.
Although once perceived as a particularly expensive procedure, oil condition monitoring and maintenance are crucial in optimizing the performance of plant and equipment. Thanks to the introduction of ever more innovative analysis and filtration technologies, this view is now widely accepted throughout industry as companies realize the benefits of effective maintenance through reduced costs, extended service life, minimized downtime, improved productivity and better profitability.
Parker Hannifin (UK) Ltd, Shaw Cross Business Park, Churwell Vale, Dewsbury,
W. Yorks WF12 7RD; tel: (01924) 487000