Centralized Lubrication for Mobile Plant
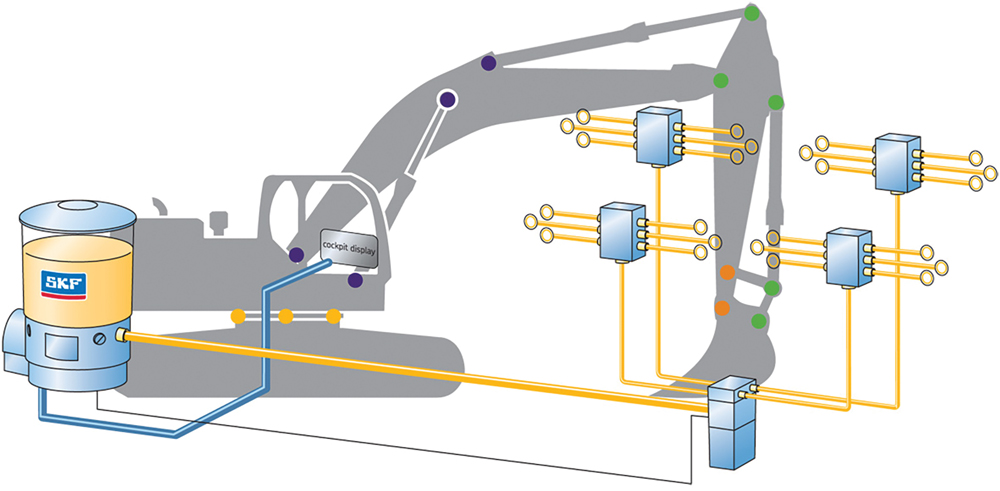
First published in the August 2016 issue of Quarry Management as Central Lines
For operators looking to extend component life and reduce failures in mobile equipment, centralized lubrication could be the answer, according to Matt Preston, lubrication applications engineer at SKF
Equipment reliability is always a priority for quarry and mine operators. The main drivers may change with commodity price swings, from maximizing output to keep up with high demand, to controlling operating costs in order to protect margins. But in every case, companies want their machines to spend more time out at work and less in the workshop for planned or unplanned maintenance.
The fact that effective lubrication promotes reliability is unlikely to surprise many operators, as lubrication problems are the underlying cause of around half of all bearing failures in service. What may come as a surprise, however, is that an excess of lubricant can cause just as much damage as an insufficiency. Forcing too much lubricant into a bearing increases friction, raises operating temperatures and distorts seals.
Lubrication can cause other problems too. Lubricants can become contaminated with water, dust or grit, promoting corrosion or wear. If the wrong lubricant is selected for a particular component, it may fail under the loads, temperatures and operating environment to which it is exposed.
Then there is the cost of lubrication activities. Lubricants themselves may be relatively inexpensive, but regular re-lubrication is labour intensive. Simply accessing the components that require lubrication can call for time-consuming disassembly. Getting into hard-to-reach areas on large machines can present risks to maintenance staff. And all the time machines are stopped for preventative maintenance, they are not making money for their owners.
With the inevitable pressure to complete routine tasks rapidly, it can be hard for maintenance teams to maintain quality. A couple of extra seconds on the trigger of a grease gun can be the difference between insufficient and excessive lubrication. It can be all too easy to miss components, to mistakenly select the wrong lubricant or to introduce contamination or other problems during disassembly or reassembly operations.
It is no wonder, therefore, that operators are increasingly looking at automated lubrication systems as a way to reduce costs and improve equipment reliability. The principle of automated, centralized lubrication systems is simple. Lubricant is stored in a container on the machine and pumped through pipelines to bearings and other components. A system of control valves manages the volume and frequency of lubricant delivery to suit the specific needs of each component.
In use, automated lubrication systems have been shown to reduce the labour associated with lubrication by 90% or more. Operators or maintenance staff still have to ensure there is sufficient lubricant in the supply tank, and conduct periodic checks to ensure pipes and feeders remain undamaged, but the daily labour savings can translate into half an hour or more of increased production time per machine. In most cases, automation also allows significant reductions in lubricant consumption, which has cost, environmental and health and safety benefits.
The industry has developed a number of different types of lubrication system to suit different categories of machine and different user needs. For small and medium-sized equipment, the SKF ProFlex progressive lubrication system, for example, uses a piston pump, with either integrated or on-board controls, to deliver lubricant to progressive feeders.
For larger equipment, where bearings require a greater lubricant volume or the distance to the pump is increased, higher pressures may be required. In these cases, a single-line lubrication system such as the Lincoln Centro-Matic is preferred. It can be scaled, depending on the size of the equipment, and is suitable for most lubricants. With a reservoir capacity of up to 20 litres, it can deliver lubricant at up to 15cm3 per minute.
The latest centralized lubrication systems can be controlled using industry-standard CAN-bus technology. This provides further benefits for operators, simplifying the installation and wiring of the system controls, and allowing the lubrication system to be tightly integrated with other components on the machine. In quarrying, for instance, this technology allows each section of a hydraulic excavator – such as slewing ring, boom, arm and bucket – to be lubricated independently, according to specific operating conditions. It also allows separate control and monitoring of each section, alerting operators to errors before major problems develop.
One German construction company has used CAN-bus technology to integrate centralized lubrication into a fleet of 50 off-highway machines. For example, it has equipped one type of Atlas wheel loader with a single pump unit to serve a zoned progressive lubrication system. Electronic valves control each zone and functional monitoring is performed using cycle switches, which are engineered to detect problems such as a lack of lubricant. Lubrication is fully integrated with the on-board computer via electronic control. It can be configured through the on-board display where the operator can view lubrication errors by zone across the machine.
For this particular operator, centralized lubrication has reduced grease consumption by around 28% across the entire fleet, equivalent to 668kg of lubricant. The company estimates that these savings could be boosted by a further 20% as its increasing understanding of real-world lubrication requirements help it to optimize the way the system is configured and used.
To work well, systems have to be designed and installed carefully, with proper consideration given to the lubrication requirements of the application, the types of lubricant used and the re-lubrication strategy adopted. Not all lubricants are suitable for all automatic lubrication systems, and different lubrication systems have different effects on the structure of the lubricant they dispense. Similarly, re-lubrication intervals must be defined in a way that prevents the lubricant from being stationary inside the lubrication ducts, especially when exposed to extreme temperatures that could promote premature degradation.
When properly designed, installed and maintained, however, automated lubrication systems ensure bearings and components get the right lubricant, at the right time, in the right amount. They make it possible to extend service intervals and reduce scheduled maintenance. As a further benefit, eliminating routine manual lubrication lets busy maintenance technicians spend more of their time on more valuable tasks, like finding the root cause of equipment problems or implementing improvement programmes to further improve productivity and reliability.
- Subscribe to Quarry Management, the monthly journal for the mineral products industry, to read articles before they appear on Agg-Net.com