Breaking the Gearbox Repair Cycle
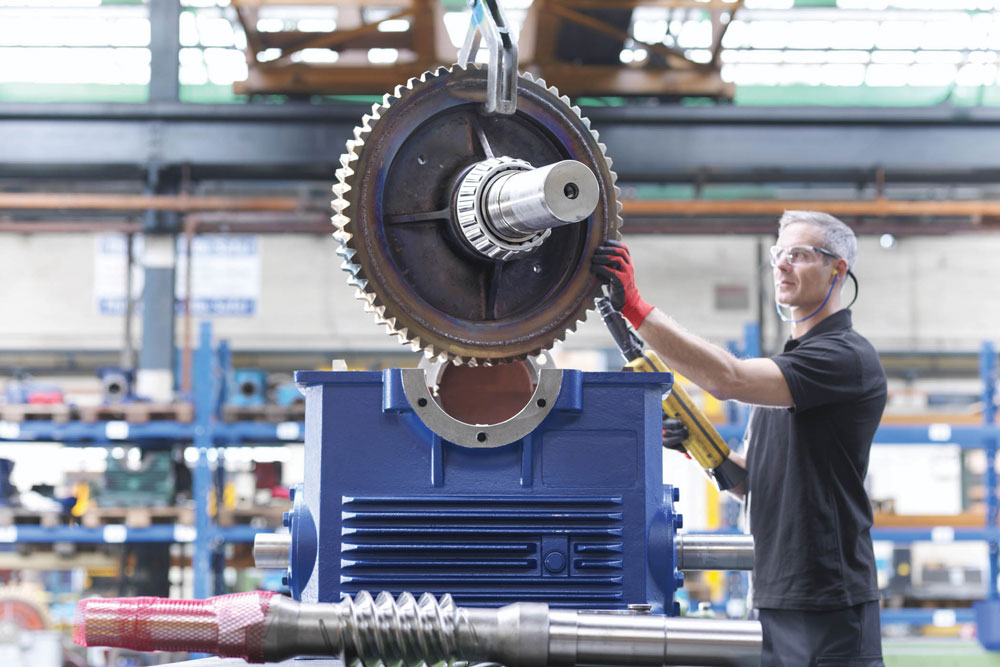
First published in the April 2018 issue of Quarry Management
Momentum for change is coming from the philosophies of modern manufacturing and new thinking on the part of plant operators, say Renold Gears
Failing industrial gearboxes can be a real problem in any industry, but particularly so wherever there is ageing plant, older equipment, arduous applications or harsh environments. One plant manager at a company producing construction materials described the job of keeping production going as ‘a real scramble’ every time a gearbox failure occurred.
The site in question operated numerous large conveyors, some steeply inclined, moving heavy aggregates around the plant. Gearbox failures had the potential to bring production to a complete standstill, because if any of the huge conveyors stopped working, a bottleneck would be created that could potentially halt other parts of the manufacturing process.
Although many of the critical gearboxes on the conveyors were the same model and the site had a spare, it was still a scramble to get the old gearbox repaired, while the spare was in use. The repair had to be conducted as quickly as possible so the spare was available again in case another gearbox failed on another conveyor.
Moreover, as the gear units were getting older the pressure was mounting. The maintenance team were working with a good gearbox repairer and had managed to avoid a complete shutdown, but it was looking like it was only a matter of time before they lost the battle, and this was not an option. A shutdown of even part of the plant, and the cost involved, was unthinkable.
This is a story that is unfolding every day in factories and plants all round the world, and the reason is simple. An emergency gearbox repair requires the repairer to finish the job as quickly as possible. Speed is of the essence because downtime has to be kept to an absolute minimum. So the gearbox repairer will do the minimum that is necessary to get the gearbox working again and reinstall it on the application so that production can resume.
This will typically involve changing the bearings and seals, cleaning the internal components and changing the oil. Although this will get the gearbox working again it is little more than a sticking plaster over the real problem. It fails to address the cause of the failure in the first place – wear to the internal gears and shafts.
The repaired gearbox will still be suffering from the same problems that the repair has only temporarily masked, and another failure is a virtual certainty further down the line. The only question is how long the repair will last before the gearbox fails again. This is a repetitive and hugely costly cycle that will repeat itself over and over again until the root cause is addressed.
Only a new gear unit or a refurbishment, rather than a quick repair, would solve the problem, but when a repair has been completed and the gearbox is working again, plant managers are likely to turn their attention elsewhere. Just recently a water company had four gearboxes repaired at a cost of around £50,000, which is about 10% more than the cost of completely new units, and around 30% more than it would have cost to have them refurbished.
The real problem when a gearbox fails is the time it would take to manufacture a new one or refurbish the old one, and so plant managers tend to opt for the quick repair. In the case of the water company, new gearboxes were eventually ordered to replace the ageing ones, bringing the total cost close to £100,000 – more than double what it would have cost if action had been taken in the first place before the units failed.
Although this problem is far from new, the momentum for change is coming from the philosophies of modern manufacturing and new thinking on the part of plant operators. The push to increase profits, cut costs and eliminate waste is almost becoming an engineering discipline in its own right. In the most forward-thinking organizations the pressure for a new strategy on gearbox failure is now coming right from the top – and it is easy to see why.
Take the water company as an example. If the aim is to cut operating costs, there is potentially a lot of money to be saved on gearbox repairs and the lost production that goes with it. This example involved just four gearboxes, but imagine the potential savings in operations that have hundreds of gearboxes, without even thinking about the cost of the downtime itself.
To address the issue some plant operators are implementing philosophies such as Total Productive Maintenance (TPM), where maintenance and production staff work together to cut downtime. This is based on teamwork and making gearbox maintenance an issue that is actively managed rather than simply reacted to when a gearbox fails. It includes a variety of approaches, such as predictive maintenance, implementing maintenance management systems, and training and management planning groups (these might include a combination of management, production and maintenance people).
For its part, the gear industry has developed a range of solutions that meet the needs of maintenance teams with gear units on a wide range of different industrial applications and environments. They include gearbox monitoring, smart gearboxes that signal alerts when problems arise, oil analysis and regular inspections undertaken by gear specialists. Taking it further, some plant operators have put gearbox maintenance on the table as an issue for suppliers to address, working in partnership, and it has spawned some innovative thinking.
For instance, in addition to a range of technical solutions and a dedicated team of engineers whose focus is solely on gearbox servicing, Renold Gears have introduced what they call their Service Exchange programme. Working closely with plant operators, critical gearboxes are identified on key plant and new replacement units are manufactured, initially free of charge. These new units are held in stock until required.
In the event of a failure the replacement unit is dispatched immediately and can often arrive on site within a matter of hours. The old unit is replaced with the new one and the failed unit is returned to Renold’s factory where it is properly refurbished to an as-good-as-new condition. It is then kept in stock until it too is required and the service cycle repeats. With the Service Exchange programme there is no need to scramble for an emergency repair.
The programme works particularly well for operations with numerous sites and with the same gearboxes deployed on multiple applications. The spare units can be held in stock and dispatched to whichever plant they are required at. It has the potential to deliver considerable savings in a relatively short period of time, as well as slashing downtime and bringing gearbox maintenance in line with other advanced manufacturing philosophies.
- Subscribe to Quarry Management, the monthly journal for the mineral products industry, to read articles before they appear on Agg-Net.com