A Ceramic Solution
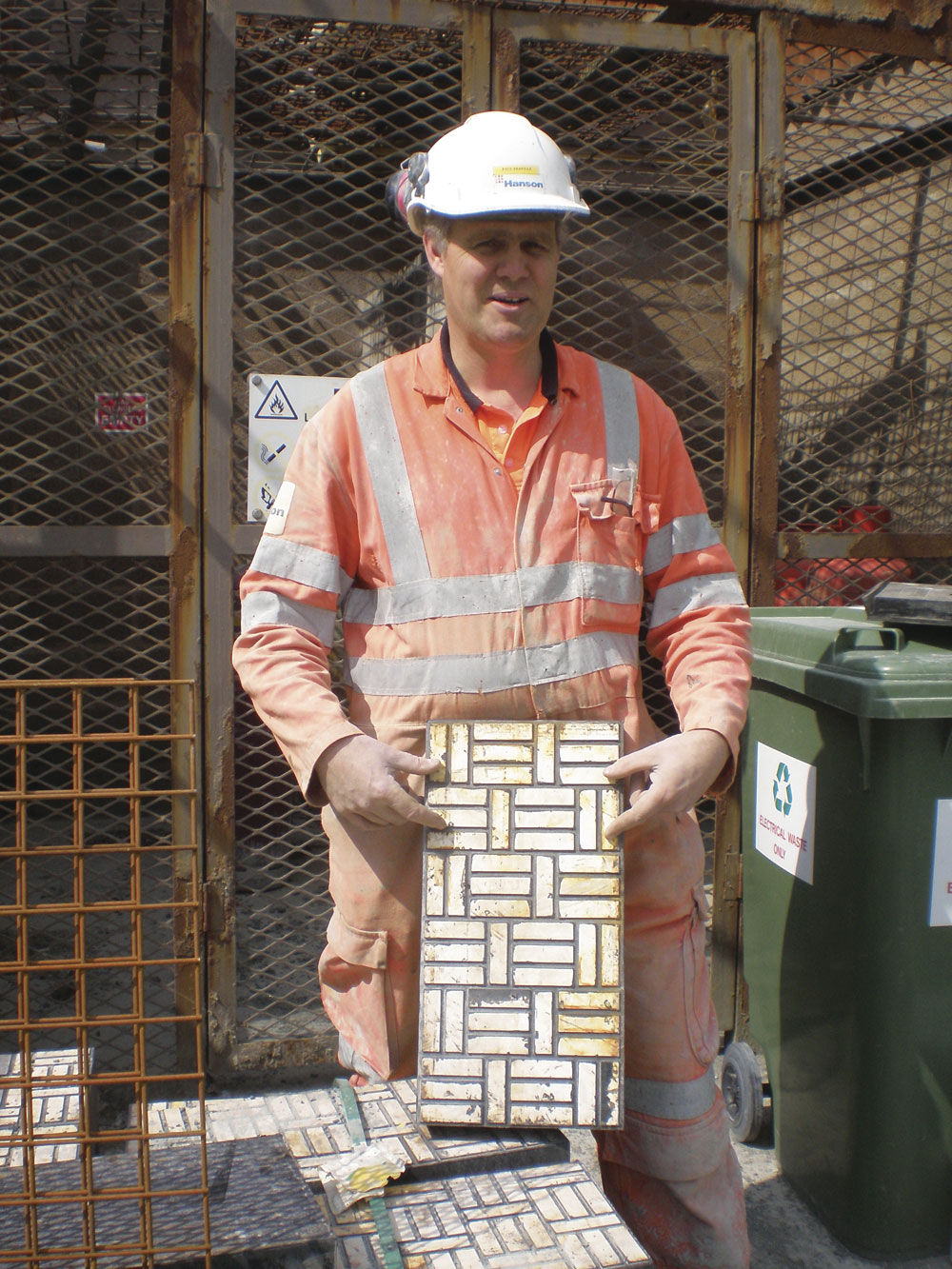
Hanson UK’s Ingleton Quarry improves screening efficiency with ceramic lining technology
Hanson UK’s Ingleton Quarry in the Yorkshire Dales National Park has taken advantage of the latest developments from Sandvik to improve its screening efficiency through the replacement of quenched steel liners with ceramic inserts. The existing steel wear protection plates used in the screening process had to be changed frequently, thereby reducing operational efficiency, and were noisy. In order to address these problems, the company took advice from Sandvik on how they could improve their efficiency and reduce noise. Although Hanson’s management was initially sceptical about the claims made by Sandvik, they are now said to be ‘delighted’ by the performance of the ceramic liners, which have significantly improved the efficiency of Ingleton’s screening operation.
The first aspect that Sandvik looked at was the feedbox leading to the primary screen. The initial set-up was based around 30mm steel-backed rubber elements which, due to the heavy-duty nature of the screening operation, had to be changed every four months. Sandvik’s solution was to replace the rubber elements with 27mm thick Sandvik WT9200 ceramic liners. Even though the application is particularly arduous (250 tonnes/h of greywacke material with a feed size up to 200mm), the ceramic liners have given 18 months of trouble-free service. The liners are due to be rotated in the next few months, giving Hanson another six month’s life from the installation.
According to Sandvik, WT9200 ceramic wear protection plates are intended for the harshest applications with very high material flows containing coarse material. They are particularly suitable when a combination of extreme wear resistance, impact resistance and long wear life is required. The ceramic wear plates have large and extremely hard ceramic bricks vulcanized into a matrix of wear-resistant rubber. Owing to its elastic properties, the rubber acts as a noise and impact dampener, thereby making it possible to use the product in applications involving high levels of impact without the risk of crushing the ceramic bricks. Moreover, flexibility of installation is ensured as the wear plates can be easily cut crosswise with a band saw, while a staggered pattern prevents longitudinal wash out.
As a result of the extended life of the liners used on Ingleton Quarry’s primary screen feedbox, Hanson asked Sandvik to look at other applications at the site that would benefit from the use of ceramic. One particular part of the operation that was immediately noted as having the potential for improvement was the discharge chute at the end of the screening operation.
The discharge chute in question is a wet application dealing with very fine material on a final 6ft x 16ft screen that was previously lined with quenched steel plate. This had, on average, lasted three months before having to be replaced, so Sandvik substituted the steel liners with WT9200 cut to size. Although the discharge chute was irregular in shape, the ceramic liners were easily cut and shaped to fit, further demonstrating the flexibility of installation. The ceramic liners have now been in operation for more than a year and are showing no signs of wear. The extended wear life has freed up many man hours that would otherwise have been spent re-lining the chute.
Sandvik’s light-duty ceramic sheeting and ceramic wear plates offer extremely long wear life in applications involving sliding wear. Their thickness and light weight make them well suited to applications where weight and space are limiting factors, while their smooth, low-friction surface helps prevent material build-up in low-inclination installations. The square ceramic tiles make it possible to bend the sheeting, which makes it a suitable protection method for both concave and convex surfaces. Additionally, the size of the ceramic sheeting can be easily adjusted by bending the sheeting and cutting it between the ceramic tiles. The sheeting is supplied with a bonding/contact layer on the back to simplify the gluing process and reduce installation time. High bond strength ensures that the product remains securely attached throughout its wear life.
Through the replacement of existing steel liners with the WT9200 ceramic versions from Sandvik, Hanson have reduced the sound emissions emanating from their operation due to the dampening effect of the liners, and reduced the number of replacements required during the production process, thereby improving productivity. Thus, the efficiency of the operation has been improved and, at the same time, an environmental impact (noise level) has been reduced.