Volvo reveal results of Electric Site research project
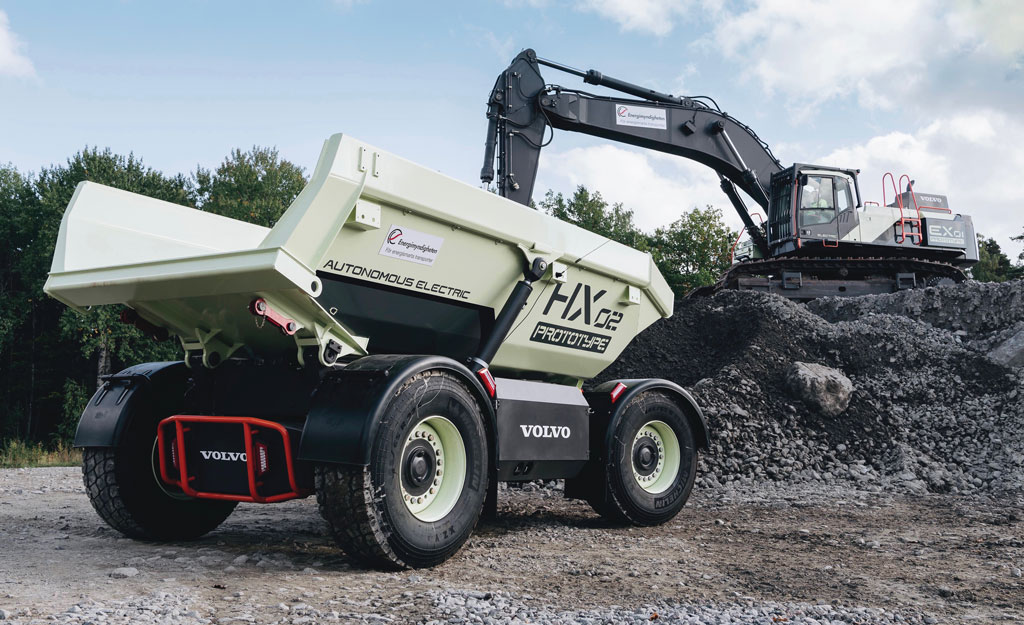
First published in the January 2019 issue of Quarry Management as Breaking New Ground
On 21 November 2018, Volvo CE hosted a special event at Skanska’s Vikan Cross Quarry, in Sweden, to reveal the ‘groundbreaking’ results from their 10-week Electric Site research project. QM sent Dan Gilkes along to find out more
Volvo Construction Equipment and Swedish construction and mining company Skanska have recorded a 98% cut in carbon emissions, from an electric quarry research project within the Vikan Cross Quarry, near Gothenburg, Sweden. The two companies, working in partnership with the Swedish Energy Agency and two local universities, have run the Electric Site project for 10 weeks, but now aim to continue with the prototype machinery until the end of the year.
‘Over the last 10 weeks we’ve made incredible progress, learnt a lot and seen huge potential in the Electric Site solution’s environmental, efficiency, safety and cost benefits,’ said Uwe Muller, chief project manager at Volvo CE, speaking last November.
‘In fact, we have decided that we want to learn more, so we will extend our test period with Skanska until the end of the year. The results we have seen so far confirm that this research project is a step towards transforming the quarry and aggregates industry and creating emission-free quarries.’
In normal operation, the site uses a 70-tonne crawler excavator, a diesel-driven mobile crusher, a 50-tonne wheel loader and three 50-tonne capacity rigid dumptrucks to move around 700 tonnes of blasted rock per hour. Between them, these machines consume around 3,000 litres of diesel in a working day.
The concept site replaces those machines with a diesel-electric hybrid wheel loader, a cable-electric crawler excavator and crushing equipment, along with eight battery-powered, autonomous haulers. Though yet to quite match the production rate of 700 tonnes/hour, the test fleet did reduce fuel consumption to just 64 litres/day, along with 9,320kWh of electricity. That is a reduction in carbon emissions of 98%, from 8,700kg/day to just 166kg/day.
This cut in diesel use also results in a 70% cut in energy costs, as electricity was supplied from sustainable, non-fossil fuel sources, as part of the test. With the hauling fleet using autonomous machines, there has also been a 40% reduction in operator costs. While production versions of these concept machines would no doubt carry a hefty premium versus conventional machinery, Volvo are confident that they could achieve an overall cost saving of 25% for a customer such as Skanska over a year of operation.
Each of the concept machines has been seen before, but this is the first time that they have been combined to run a complete job site. The EX1 crawler excavator is a dual-powered machine based on the company’s own 70-tonne EC750. The machine has been modified to incorporate an electric motor alongside the standard diesel engine, though the machine’s diesel engine is used for longer travel across the site.
‘To fit the new components in the machine without increasing its size required a significant amount of repackaging work,’ said Mr Muller.
‘However, in terms of the operator interface and controls, nothing has changed; it’s operated in exactly the same way as a conventional Volvo excavator. If the cable is connected the machine will automatically start in electric mode. If not, it will start in diesel mode.’
Once at the working location, the excavator is plugged into the grid, using a cable that is connected from above the main superstructure, behind the operator’s cab. The electricity is also delivered to the electric crusher, that is positioned below the blasted rock pile. The crusher has a gantry and boom that positions the power cable above the excavator, where it connects through a rotating coupling. When the crusher has to be moved within the quarry, the gantry legs are hydraulically lifted and the structure is carried by the crusher to the new position, where it reconnects with the excavator.
‘Because the machine will be relatively static, only moving a few metres once or twice a day as the excavator works its way through the blasted rock, it’s ideally suited as a fully electric machine on a cable,’ said Mr Muller. ‘This has allowed us to make a zero-emission excavator when it’s plugged into the grid.’
The crushed rock is loaded by the wheel loader into haulers and carried to a secondary crusher and conveyor system at the top of the quarry. Rock can also be stockpiled within the quarry using the loader, or the material can be loaded directly into the haulers from the conveyor feed.
Volvo’s LX1 prototype wheel loader is a series hybrid with electric drive motors at the wheels and electrically driven hydraulics. Using electric drive allows for a much smaller diesel engine, resulting in a 50% fuel saving over a traditional diesel-powered loader. As the haulers are much smaller than the rigid dumptrucks that are traditionally used, the site can also operate a much smaller loader, the LX1 tipping the scales at 20 tonnes, rather than the 50-tonne loader that is used with the rigid trucks. Despite this smaller size, Volvo insist that the LX1 can do the job of a conventional machine one size larger.
The second-generation HX2 haulers are totally autonomous machines and they have advanced significantly since the initial HX1 prototype of some years ago. They are powered by lithium-ion batteries, driving two electric traction motors and an electrically powered hydraulic system. The haulers have bi-directional drive, so there is no need to manoeuvre and reverse under the loader, the HX2 simply drives in, gets loaded and then drives out again, boosting productivity.
‘The HX1 was our proof of concept. Once we knew it was feasible, we updated the design requirements for the HX2 to incorporate shared technologies and components from the Volvo Group,’ said Mr Muller. ‘This includes electric motors, batteries and power electronics. Integrating a completely new drivetrain was crucial to take full advantage of the groundbreaking electromobility developments that are happening within the Volvo Group.’
The HX2 haulers have a 15-tonne capacity, rather than the 50-tonne payload of the three rigid dumptrucks, so there are eight HX2s on the site, to reach the desired production target.
During every haul cycle, each HX2 stops for one minute above an autonomous charging point, where a high-powered charging connection is inserted into the battery from below. This is similar to the catenary charging that Volvo use on their city buses, which drops from above to part-charge the batteries during stops. This continual boost to the batteries, allows Volvo to run the haulers with a smaller electrical storage system than would be required for a full day’s operation.
A central control room within the quarry monitors and controls the haulers, which run to a programmed GPS route on the haul road. They also have a vision system that prevents collisions within the site. The wheel loader operator controls the desired loading position by flicking a button in the cab when the machine is in the loading position. This load point is transmitted to the HX2 haulers, which then park in the required position to be loaded.
The haulers have an extended skip at one end that allows them to overlap their bodies. When loading from a conveyor or the crusher, they can be overlapped with the rearmost machine ‘pushing’ the truck in front. This allows the conveyor to run without stopping, as the haulers move smoothly below the flow of rock as they are filled up.
‘At Volvo CE we believe in a sustainable future and we are doing our best to build the world we want to live in,’ said Melker Jernberg, president of Volvo CE. ‘With this research we are combining intelligent machines, automation and electromobility to challenge traditional ways of working in the quarrying industry and explore new alternatives. We will now further mature the technologies involved and the reliability of the concept.’
‘With climate change reshaping our industry, we need to find new, sustainable solutions and build partnerships with organizations that have different competencies,’ added Anders Danielsson, president and chief executive officer of Skanska. ‘Our ambition is that this collaboration with Volvo CE will help us and our customers to reduce our carbon footprint.’
With more than an estimated 500,000 working quarries around the world, employing more than 4 million people, there are certainly potential carbon reduction and efficiency gains to be made.
- Subscribe to Quarry Management, the monthly journal for the mineral products industry, to read articles before they appear on Agg-Net.com