Volvo CE Unveil Loading and Hauling Innovations
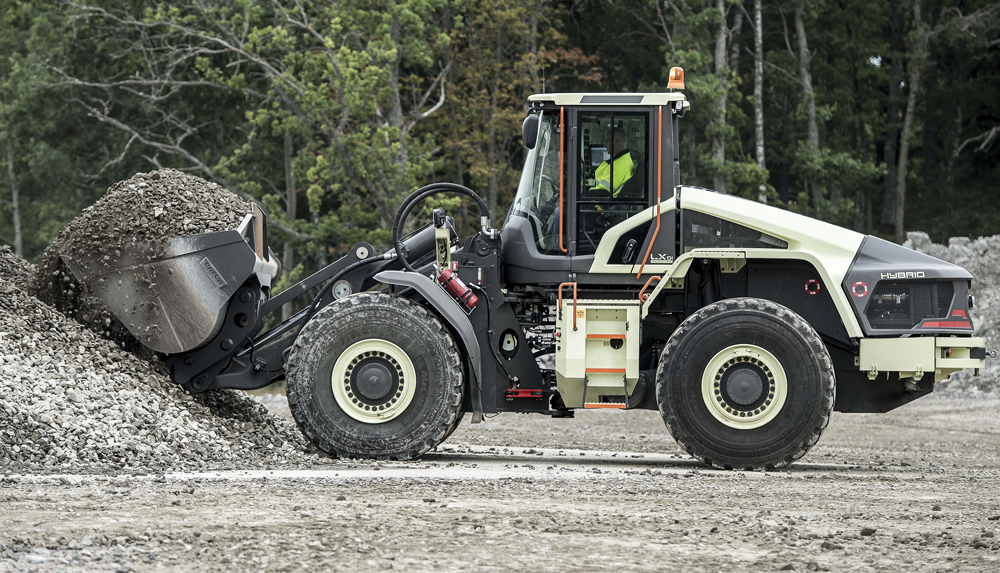
First published in the November 2016 issue of Quarry Management as Looking to the Future
Volvo CE use Xploration Forum to unveil prototype hybrid wheel loader, outline work on an electric site research project and demonstrate prototype autonomous wheel loader and articulated hauler combination
Volvo Construction Equipment (Volvo CE) reinforced the fact that energy efficiency is at the top of their agenda when they unveiled their prototype hybrid wheel loader – known as the LX1 – at the Xploration Forum in Eskilstuna, Sweden, earlier this year. The company gave customers, the international press, government representatives and academics an exclusive look at the electric hybrid machine, which is said to deliver up to a 50% improvement in fuel efficiency. On top of this, the LX1 also offers a significant reduction in emissions and noise pollution compared with its conventional counterparts.
The LX1 is a series hybrid incorporating a driveline that consists of electric drive motors mounted at the wheels, electric hydraulics, an energy storage system, a significantly smaller diesel engine and new machine architecture. It is this combination that allows the substantial gain in fuel efficiency. According to Volvo CE, the prototype – which has 98% new parts and a fundamentally new machine design – is capable of doing the work of a wheel loader that is one size larger. At this stage, the LX1 is part of a research project and is not commercially available.
Short- and long-term outlook
The Volvo Group defines electromobility as ‘commercial vehicles and machines that can utilize an electrical motor to propel or to perform the main purpose of the machine’. A hybrid is classified as a machine that uses more than one power source and captures and reuses energy that would otherwise be wasted. It is a prerequisite that the machine has the capability for energy storage to count as a true hybrid.
Volvo CE started their journey with electromobility and hybrid technology in 1998. The company has long-term plans to develop products and services for electromobility, including electric hybrids and electric sites.
‘Although we believe that there will be a major shift towards electric hybrid technology in the future, our customers, quite rightly, want improved efficiency now. We are delivering this through more conventional technologies and soft offers,’ said Scott Young, electromobility programme manager at Volvo CE.
‘This is because we need to meet customers’ immediate expectations in terms of total cost of ownership (TCO). A large part of TCO is energy cost, but other significant expenses include purchase price and maintenance. These aspects help drive our hybrid development plans. Therefore, before we launch a machine like the LX1, you can expect to see elements of this design incorporated into our products. This supports short- and mid-term developments and requirements while the market continues to accept the technology, technology improves and the cost of new technologies decreases.’
Volvo CE have teamed up with their customer Waste Management – the largest environmental services and recycling company in North America – to field-test the LX1. Waste Management, who own one of the largest fleets of Volvo CE equipment in the world, have been running a conventional machine to gather baseline data at two of their facilities in California. After the Xploration Forum in September, the LX1 was shipped to the company so that it could carry out fuel efficiency and emission reduction tests at these sites.
‘We see Volvo CE as a strategic partner,’ said John Meese, senior director of heavy equipment at Waste Management. ‘We have one of the largest fleets of construction equipment in North America and want to use the best available technology to improve our operations and the service we deliver to customers. From the minute we were introduced to the LX1 we knew we wanted to work with Volvo CE to prove the concept in the real-world environments we operate in. We are anticipating excellent results when it comes to reducing the use of fossil fuels and lowering exhaust emissions. An additional benefit is the dramatic reduction in noise pollution.’
‘Although it may be possible to realize fairly high levels of fuel savings and productivity gains in prototype form, when it comes to serial production you have to consider cost and return on investment,’ said Scott Young. ‘Hybrid technologies are still a relatively expensive solution and adoption has been slow. This is because the benefit of current hybrid machines on the market isn’t significantly higher than conventional technologies, so it takes longer to achieve payback on your investment.
‘However, the cost of energy storage systems such as lithium ion batteries is steadily decreasing, along with other technology, so that’s starting to make hybrids more attractive financially. There are still opportunities to further optimize conventional technology – and these developments will compete with hybrid technology for some years. That said, however, we are currently in a period of exponential technology growth and I believe this industry shift will move at a faster pace than others have in the past.’
Autonomous load carrier
As well as prototype hybrid technology, Volvo CE used their recent Xploration Forum to reveal more about their electric site solution and unveil the new-concept HX1 autonomous battery electric load carrier. This prototype machine is one element of an electric site research project that predicts up to a 95% reduction in carbon emissions and up to a 25% reduction in total cost of ownership. The project aims to electrify a transport stage in a quarry – from excavation to primary crushing and transport to secondary crushing. It involves developing new machines, work methods and site-management systems. As well as a fleet of HX1s, other prototype machines that make-up the electric site system include the LX1 hybrid wheel loader and a grid-connected excavator. Significantly, new technology encompasses machine and fleet control systems and logistic solutions for electric machines in quarries.
‘This research project is a step towards transforming the quarry and aggregates industry,’ said Johan Sjöberg, technical specialist in site automation at Volvo CE. ‘By using electricity instead of diesel to power construction equipment in a quarry, we have the potential to deliver significant reductions in fuel consumption, CO2 emissions, environmental impact and cost per tonne. The electrification of construction equipment will produce cleaner, quieter and more efficient machines – this represents the future of our industry.’
Electrifying innovation
Volvo CE have teamed up with their customer Skanska Sweden, the Swedish Energy Agency and two Swedish universities – Linköping University and Mälardalen University – to collaborate on the jointly funded SEK203 million (£18.7 million) project. All of the partners were at the recent Xploration Forum to present the concept to the delegates. Volvo CE are co-ordinating the project and are in charge of developing the machines and systems. Skanska Sweden are providing logistical solutions, application relevance and job-site knowledge. The Swedish Energy Agency – a government agency for national energy policy issues – is helping to fund the project and the universities are carrying out research. Three PhD students are looking at energy management for electric vehicles, safe and robust software controls and energy-optimized work cycle control.
Volvo CE have invested SEK129 million in the project, the Swedish Energy Agency has provided SEK65 million (it awarded SEK59 million to Volvo CE, SEK5 million to Linköping University and SEK1 million to Mälardalen University) and Skanska Sweden have contributed SEK9 million.
The project started in October 2015 and is due to be completed in late 2018. Volvo CE are currently developing and testing the technologies, concept and prototypes in house. Skanska Sweden will then incorporate the demonstration machines into their operations and test the electric site concept at a quarry in western Sweden for 10 weeks at the end of 2018. After this, Volvo CE will examine the project results to see if the concept is viable for the industry. Currently this work is just a research project, with no plans for industrialization at this stage.
‘This type of co-operation between Volvo CE, their customers, governments and academia allows us to invest in new technologies and explore solutions that are both relevant for our customer base and address future challenges,’ said Erik Uhlin, advanced engineering technical project leader at Volvo CE. ‘Each year Volvo invest a substantial amount of money in emerging technologies, advanced engineering and product development, but without vital public funding and support from partners it would not be possible for research projects like this to go ahead.’
Intelligent machines
Delegates at the Xploration Forum also witnessed an exclusive demonstration of a prototype autonomous wheel loader and articulated hauler working in tandem. The loader filled the hauler, before dumping its load and repeating the cycle. In a one-hour comparison it was found that the autonomous wheel loader could reach the equivalent of 70% of that of a skilled operator’s productivity levels when loading and unloading. And this is not just theoretical, the machine has also done ‘real work’ for a Volvo CE customer at an asphalt plant in Sweden.
‘The demonstration machines were programmed to work together and carry out a specific set of actions on a pre-defined route,’ explained Jenny Elfsberg, director of emerging technologies at Volvo CE. ‘The machines can perform the same task over and over again, along a fixed route, for a relatively long period of time. But it’s still early days for this technology; we are working on developing solutions that have the required safety and performance levels that the market will accept.
‘There is still a long way to go so there are no plans for industrialization at this stage,’ she continued. ‘Currently these prototype machines don’t communicate with each other and machine-to-machine communication technology – where machines ‘talk’ to one another and to a central control point – is crucial when it comes to avoiding collisions and facilitating an efficient flow of equipment.’
The machines used in the Xploration Forum demonstration were standard Volvo products – an L120E wheel loader and an A25F articulated hauler – which had been upgraded with autonomous technology. Once a solution is finalized, this technology could be applied to other products in Volvo CE’s range.
‘Autonomous machines will increase safety in hazardous working environments and eliminate the possibility of accidents caused by human error,’ explained Jenny Elfsberg. ‘They will also perform repetitive tasks more efficiently and precisely than a human operator and, because machines will be operated in the most efficient way, customers will benefit from improved performance, productivity, fuel efficiency and durability.
‘In the future, you could also potentially have one operator for three or four machines, increasing productivity and further decreasing costs. Looking ahead, I imagine that autonomous machines will be smaller and more robust. There will be no need for a cab or suspension – much like the HX1 autonomous load-carrier concept.’
Looking to the future
Volvo CE have been working on autonomous machine research for more than a decade and their focus on futuristic technology is fuelling the development of mid-term innovations at the company. However, technology such as semi-automated or automated functions will support more immediate developments years before it is possible to realize the ultimate goal. There are already cases of automated and assist functionalities on the market today. For example, earlier this year Volvo CE launched Volvo Co-Pilot, a system that offers a range of intelligent machine services – Load Assist, Dig Assist, Compact Assist and Pave Assist – to help operators deliver higher-quality outcomes, in less time and with less effort.
‘We are starting to see systems that are less dependent on operator skills, ones that support operators with guidance or control primary functions,’ said Jenny Elfsberg. ‘In the future we will see increased machine autonomy and the operator will act more in a supervisory capacity. This will provide less stressful, more interesting work for operators, with perhaps several machines being controlled remotely by one operator. Of course, some tasks are so complicated that you really need to feel what you’re doing, and in those cases we will still need operators controlling the machines from inside the cab.’
• Subscribe to Quarry Management, the monthly journal for the mineral products industry, to read articles before they appear on Agg-Net.com