The Next Generation
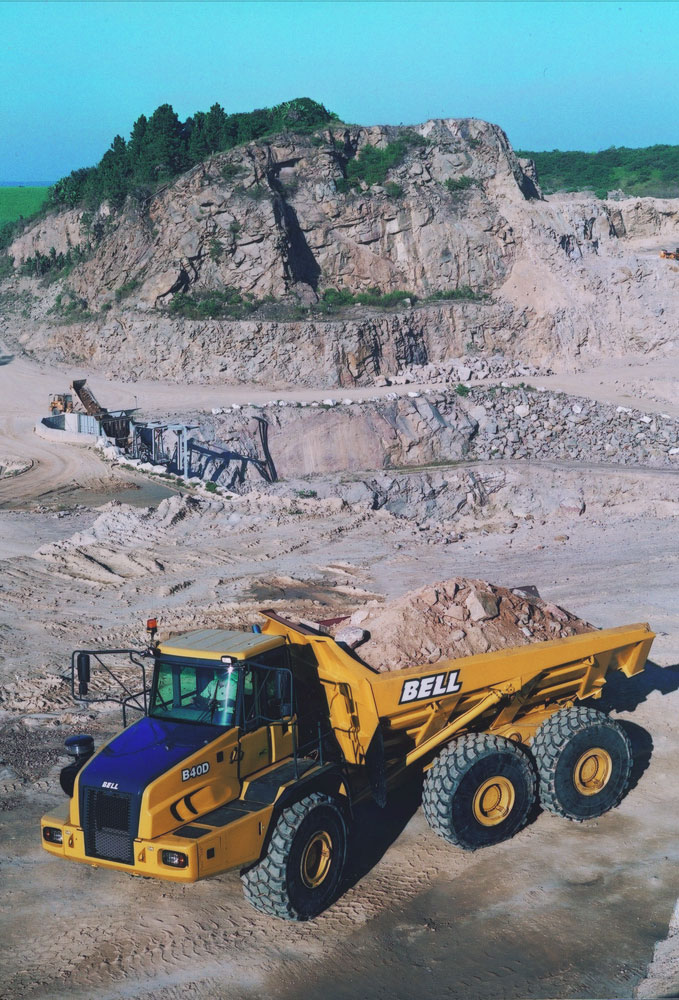
Bell unveil fourth-generation D-series ADTs
Three-and-a-half years after introducing their C-series articulated dumptrucks, Bell Equipment have launched their fourth-generation D-series range, which is said to represent the most radical upgrade in engineering design and incorporation of key componentry since the first Bell ADT rolled off the production line in 1985. With their innovative design and drivetrain technology, Bell confidently expect the new machines — the B40D, B35D, B30D and B25D — to accelerate the company towards its target of capturing 20% of the world’s ADT market by 2003.
According to Bell Equipment, the two larger units, the B40D and B35D, represent an 85% upgrade over their C-series predecessors, while the B30D and B25D are virtually ‘clean sheet’ designs. But although the entire engineering design and much of the manufacturing process has undergone a total change since production of the first Bell ADT 17 years ago, the company’s design philosophy remains the same: to produce a robust, reliable truck that is operator friendly, economical to use and simple to maintain, with the overriding emphasis on providing the lowest cost per tonne.
Bell Equipment’s group technical director, Peter Bell, commented: ‘After more than three-and-a-half years of research and development and 30,000h of rigorous prototype testing in some of the most demanding construction and mining sites in the world, we are confident that we have achieved our objectives.
‘However, the key benefits of the D-series machines were not achieved in isolation. Much of the research was conducted with input from, and in conjunction with, leading customers, including several in the UK and Ireland, as well as alliance partners John Deere Construction Equipment and Hitachi Construction Machinery.’
The B40D and B35D units are powered by the new ‘eco-friendly’ Mercedes Benz V6 OM501LA turbocharged and intercooled diesel engine, while the smaller B30D and B25D units are fitted with the Mercedes Benz OM906LA engine.
With its electronically managed unit injectors and ultra-high (8,000 bar) injection pressures, the D-series’ V6 power plant is said to combine very low fuel consumption with emissions that are compliant with future international legislation. In addition, the OM501LA delivers its power at low revs/min and weighs around 500kg less than its equivalent in-line six competitors, further maximizing fuel savings.
The two larger trucks in the D-series range retain the successful Allison world-series transmission which achieves six well spaced speeds with one less planetary gear set, thus providing more power to the ground. The B30D and B25D are both fitted with the proven Ecomat transmission.
Improved safety is a key feature of all the D-series machines, which benefit from uprated braking and retarding capacity. The B40D’s oil-cooled wet-disc brakes, which reduce stopping distances by around 20%, are immune to environmental conditions and operate for up to 10,000h between services. The B40D also features an output-type transmission retarder which is particularly effective at high speeds. When in the retarding mode, the transmission is programmed to downshift, maximizing engine revs/min and the engine valve brake (EVB) system to provide up to 800kW of retarding power.
Cost-effectiveness has been factored into the design of the new machines with the low-overhang front end, the ribbed body and the extensive use of high-strength steel and composite materials all combining to give the D-series less dead weight and more payload capacity; the payload-to-weight ratio advantage delivering more tonnes per unit of fuel used.
Further cost savings are also being passed on to the end-user through enhanced component protection and engineering advances which have reduced service and maintenance requirements. The D-series power plant is engineered with a service life some 50% greater than its predecessors (up to 20,000h to the first overhaul). In addition, maximum protection against malfunction is provided by the D-series’ electronic control systems. The engine and transmission electronic controllers are networked by CAN bus to the chassis control unit. Should an operating parameter look like going out of range, the controller reduces power or limits shifts, as appropriate, in order to prevent damage.
Operator safety and comfort are also well catered for on the D-series machines with a new ergonomically designed cab. Driver protection is accentuated by a six-pillar ROPS/FOPS frame with a steel roof, while the cab itself is fully sound insulated and equipped with a wrap-around dashboard featuring carefully located control instrumentation. Additional features of the cab include a climate-control system, an air-suspension seat and an unobstructed curved and tinted windscreen for good all-round visibility.
Bell Equipment UK Ltd, Unit 6C Graycar Business Park, Barton Turns, Barton-under-Needwood, Burton-on-Trent, Staffs DE13 8EN; tel: (01283) 712862; fax: (01283) 712687; email: general@bellequipment.co.uk; website: www.bell.co.za
Three-and-a-half years after introducing their C-series articulated dumptrucks, Bell Equipment have launched their fourth-generation D-series range, which is said to represent the most radical upgrade in engineering design and incorporation of key componentry since the first Bell ADT rolled off the production line in 1985. With their innovative design and drivetrain technology, Bell confidently expect the new machines — the B40D, B35D, B30D and B25D — to accelerate the company towards its target of capturing 20% of the world’s ADT market by 2003.
According to Bell Equipment, the two larger units, the B40D and B35D, represent an 85% upgrade over their C-series predecessors, while the B30D and B25D are virtually ‘clean sheet’ designs. But although the entire engineering design and much of the manufacturing process has undergone a total change since production of the first Bell ADT 17 years ago, the company’s design philosophy remains the same: to produce a robust, reliable truck that is operator friendly, economical to use and simple to maintain, with the overriding emphasis on providing the lowest cost per tonne.
Bell Equipment’s group technical director, Peter Bell, commented: ‘After more than three-and-a-half years of research and development and 30,000h of rigorous prototype testing in some of the most demanding construction and mining sites in the world, we are confident that we have achieved our objectives.
‘However, the key benefits of the D-series machines were not achieved in isolation. Much of the research was conducted with input from, and in conjunction with, leading customers, including several in the UK and Ireland, as well as alliance partners John Deere Construction Equipment and Hitachi Construction Machinery.’
The B40D and B35D units are powered by the new ‘eco-friendly’ Mercedes Benz V6 OM501LA turbocharged and intercooled diesel engine, while the smaller B30D and B25D units are fitted with the Mercedes Benz OM906LA engine.
With its electronically managed unit injectors and ultra-high (8,000 bar) injection pressures, the D-series’ V6 power plant is said to combine very low fuel consumption with emissions that are compliant with future international legislation. In addition, the OM501LA delivers its power at low revs/min and weighs around 500kg less than its equivalent in-line six competitors, further maximizing fuel savings.
The two larger trucks in the D-series range retain the successful Allison world-series transmission which achieves six well spaced speeds with one less planetary gear set, thus providing more power to the ground. The B30D and B25D are both fitted with the proven Ecomat transmission.
Improved safety is a key feature of all the D-series machines, which benefit from uprated braking and retarding capacity. The B40D’s oil-cooled wet-disc brakes, which reduce stopping distances by around 20%, are immune to environmental conditions and operate for up to 10,000h between services. The B40D also features an output-type transmission retarder which is particularly effective at high speeds. When in the retarding mode, the transmission is programmed to downshift, maximizing engine revs/min and the engine valve brake (EVB) system to provide up to 800kW of retarding power.
Cost-effectiveness has been factored into the design of the new machines with the low-overhang front end, the ribbed body and the extensive use of high-strength steel and composite materials all combining to give the D-series less dead weight and more payload capacity; the payload-to-weight ratio advantage delivering more tonnes per unit of fuel used.
Further cost savings are also being passed on to the end-user through enhanced component protection and engineering advances which have reduced service and maintenance requirements. The D-series power plant is engineered with a service life some 50% greater than its predecessors (up to 20,000h to the first overhaul). In addition, maximum protection against malfunction is provided by the D-series’ electronic control systems. The engine and transmission electronic controllers are networked by CAN bus to the chassis control unit. Should an operating parameter look like going out of range, the controller reduces power or limits shifts, as appropriate, in order to prevent damage.
Operator safety and comfort are also well catered for on the D-series machines with a new ergonomically designed cab. Driver protection is accentuated by a six-pillar ROPS/FOPS frame with a steel roof, while the cab itself is fully sound insulated and equipped with a wrap-around dashboard featuring carefully located control instrumentation. Additional features of the cab include a climate-control system, an air-suspension seat and an unobstructed curved and tinted windscreen for good all-round visibility.
Bell Equipment UK Ltd, Unit 6C Graycar Business Park, Barton Turns, Barton-under-Needwood, Burton-on-Trent, Staffs DE13 8EN; tel: (01283) 712862; fax: (01283) 712687; email: general@bellequipment.co.uk; website: www.bell.co.za