The Necessary Accessory
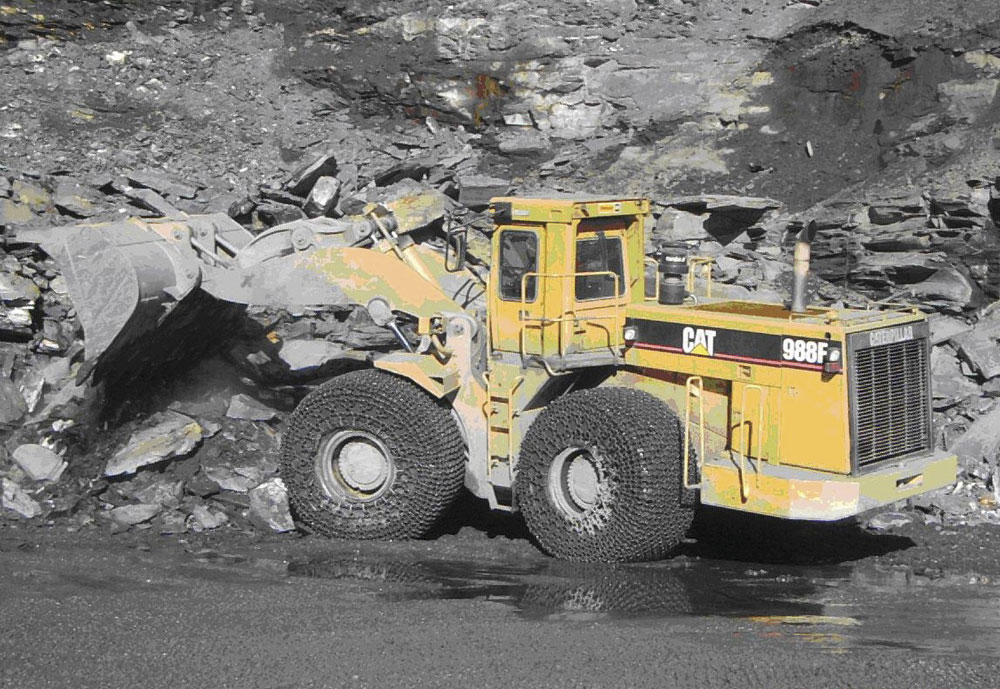
A brief guide to choosing the correct tyre-protection chains
Despite the economic slowdown, demand remains high for those companies that can demonstrate competitiveness in quality, price and delivery. This maxim applies as much to heavy industries, such as minerals, aggregates, fossil fuels, demolition, recycling, forestry etc, as it does to the service sector.
Where loading and hauling is a central component of an operation, optimizing plant availability is the key to success, and this success depends on skilled staff and a rigorous maintenance schedule with particular attention being paid to the tyres.
A good plant manager will make certain that both staff and machines are well protected, for without a full set of sound tyres, just as without a skilled operator, a loader or truck is simply an expensive, idle lump of metal.
No two sites are exactly the same, however, so it is essential to invest in tyres that promise optimum serviceability. Big-name manufacturers such as Bridgestone, Goodyear and Michelin, as well as established independent suppliers with knowledge of many brands, will be able to advise on most appropriate tyre for the job in hand.
The considerations that apply to automotive tyres are amplified many times over when it comes to selecting earthmover tyres. Each condition or combination of conditions must be matched by the appropriate tyre construction and tread.
For example: Is the site wet, clayey or icy? Is the running surface abrasive powder, shingle or flint? How long and how steep are the haul roads? What payload weights are being shifted? Are machines working in extreme temperatures? What about wear and tear?
Manufacturers do their best to make their tyres abrasion resistant and ‘bullet-proof’, but the very flexibility that makes a tyre function as it should is precisely what makes it vulnerable to sidewall piercing. If a tyre wall is damaged, quick action may save the day, but however good the repair, the tyre will have lost some of its original integrity.
While T&C Site Services prefer to sell tyres, their technical director, Derek Adams, agrees that there are instances where tyre-protection chains (TPC) are essential. ‘Dealing with a blown tyre or repairing a machine that has skidded off road is no one’s idea of a happy day, so it’s hardly surprising that where tyres are subject to excessive abrasion or are vulnerable to sudden-death piercing, tyre-protection chains are considered essential,’ he said.
TPC suppliers
Nowadays, the consideration is no longer whether or not to fit tyre chains, but rather whose brand and which type. There are approximately 10 tyre chain manufacturers worldwide. In the Far East, a number of relative newcomers are offering a limited range of cheap chains, which can be attractive to operators whose tyre specifications match what is available and who, given the unknown standards of metallurgy and welding, are ready and able to carry out their own installation, tensioning and repairs.
After a series of acquisitions and consolidations, Europe now boasts very few tyre chain manufacturers – perhaps most notable among those that remain being Pewag and RUD-Erlau.
Following the introduction of versatile pneumatic-tyred loaders in the early 1950s, RUD-Erlau built upon their snow chain technology to develop and evolve earthmover TPCs into the sophisticated products seen in action today. From that early innovation, over the last 60 years RUD-Erlau have grown to command some 65% of the world market, making the RUD-Erlau range a useful benchmark when selecting an appropriate tyre-protection chain.
TPC types
No matter how well made and maintained, tyres can suffer from unacceptably heavy abrasion to the extent that they can almost be seen to shrink day by day as the tread (and the operator’s investment) wears away. Quartz, dolomite and basalt are just some of the materials that can cause tyre abrasion. In these instances, a quality abrasion-resistant chain, such as RUD-Erlau’s Ring-Link system, is designed to create a barrier between the tyres and the ground.
The density of the mesh required will depend on the exact nature of the work site, but in every case the mesh should be self-cleaning and the links specially hardened to resist wear at the points where they interact with the connecting rings. RUD-Erlau say operators should expect a well-fitted, quality abrasion-resistant chain to more than double the life of a tyre. In many cases, operators can also save money by using part-worn tyres.
For operators working flint, slate and shale-like rocks, or loading scrap metal or demolition debris, no matter how well constructed the tyres may be, sudden-death sidewall piercing is always a risk. In a small operation this could put the entire production shift on costly standby while a temporary fix or a replacement tyre is sought.
At best, tyre repairs are a stopgap; once the tyre sidewall has been penetrated the steel cords may be damaged and no amount of fillers, patches or vulcanizing will restore the tyre’s original integrity. In such situations, the only guarantee of long-term plant availability is to protect the tyre from the outset. In these environments, RUD-Erlau recommend a close-meshed chain such as their Ring-Ring system, which embraces the entire tyre surface and deflects sharp-edged rock.
At some sites, where the terrain is slippery or at altitudes where trucks have to contend with icy haul roads, poor traction can be a major problem and operators could risk ‘losing’ the truck with all the collateral damage that may involve. Where the tyre tread cannot provide sufficient displacement to ensure adequate grip, the solution may be provided by a simple, open-ring link chain, such as the RUD-Erlau Garant series. Where additional grip is required, RUD-Erlau recommend Terraplus with its studded links for extra ‘bite’.
In the narrow galleries of underground mines, low-profile loaders and haulers can face a combination of abrasion, sidewall damage and poor handling. However, advanced alloys and a proprietary hardening method have led to the production of a lightweight energy-saving chain known as the X19 FELS Toro. This chain is said to resist abrasion so effectively that RUD-Erlau are able to claim, with confidence, a 30% longer tyre service life.
Steel making pushes machines and tyres to limits not experienced in most other industries. Pot handlers carry ladles full of molten metal and wheel loaders shift fiery slag for reprocessing. Here, where tyre-protection chains have to absorb abrasive limestone ash and contend with extreme heat around the clock, unknown and unproven products are not an option. These conditions require a robust chain such as the RUD-Erlau Ring Locking system.
As technical advances have made them lighter, stronger and more durable, TPCs are no longer just an add-on. When the experience, expertise and support that come with a quality TPC are factored in, not to mention the benefits of assured plant availability, the little extra that a quality chain may cost is easily justified.
Case study
Studies have shown that TPCs are an investment that can actually save money, and while commercial confidentiality makes it hard to get hold of reliable figures, those shown below from an independent study at a European quarry, although now a little dated, still clearly illustrate the benefits that TPCs can provide.
A Caterpillar 988B loader running on 36/65-33 DT tyres in a German limestone quarry was getting through a set of tyres every 1,200h at a cost to the company of US$37,615 per set (US$31.35 per hour). The quarry invested US$56,200 in a set of RUD-Erlau FELS Royal X16 TPCs, which extended tyre life to 12,000h and reduced tyre costs to US$3.13 per hour. Factoring in a conservative chain life of 10,000h (US$5.62 per hour), the total hourly cost then amounted to US$8.75, representing an overall saving of US$22.60 per hour (72%).
Productivity also showed significant improvements; load-out increased by 16% from 550 tonnes/h to 630 tonnes/h, and downtime dropped from 160 hours per year for tyre repairs to 36 hours per year for chain servicing (ie loader availability increased by 124h and downtime reduced by 78%). Following installation of the TPCs, the Cat 988B’s annual output grew from 1,012,000 tonnes to 1,253,032 tonnes, an increase of just under 24%.
Conclusion
A set of tyre-protection chains can extend tyre life (whether new or part-worn) indefinitely, but the cost advantages do not stop there. Apart from scheduling an occasional couple of hours for inspection and chain tensioning, wheel loaders and dumptrucks should be constantly available and delivering materials to order, giving operators a competitive edge and ensuring fully satisfied customers.
However, in the same way that operators need to be careful about their choice of tyres and the type of protection chains used, they should also be discriminating in their choice of TPC supplier. Key considerations include:
- Availability – Does the supplier have the manufacturing capability to deliver on time?
- Quality – Is the metallurgy, welding and hardening verifiable to the highest standards?
- Range – Can the supplier offer chains to fit specific tyres and match specific site conditions?
- Reputation – Is the manufacturer well regarded in the industry?
- Experience – How long has the supplier been manufacturing TPCs?
- Personnel – Do the metallurgists, designers and engineers have in-depth experience of TPCs?
- Support – Is there a network to provide timely after-sales service and support ?
- Value – Will the investment in TPCs pay for itself in terms of cost savings and productivity?
For further information visit: www.erlau.com