Taking Technology to the Next Level
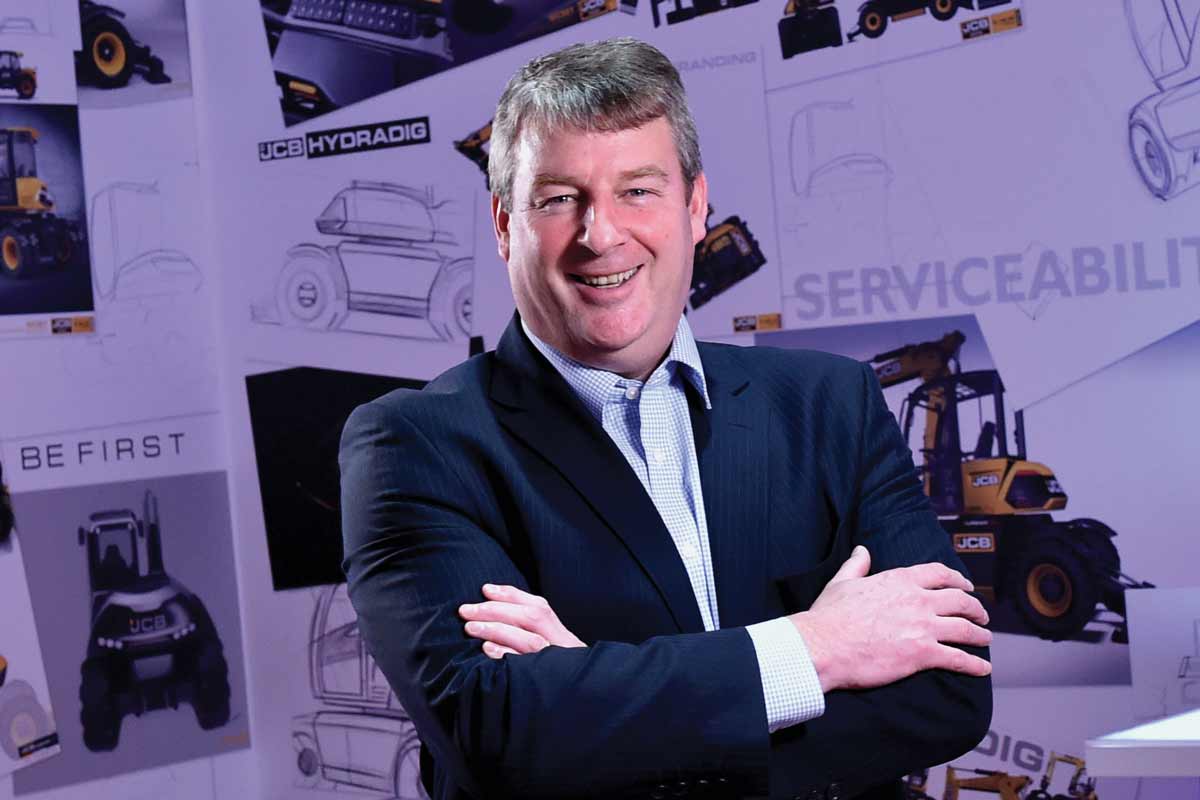
First published in the November 2019 issue of Quarry Management
JCB’s chief innovation and growth officer, Tim Burnhope, talks to Quarry Management about electrification, connectivity and continued global expansion
JCB, the UK’s most successful construction equipment manufacturer and one of the largest machinery companies in the world, will celebrate their 75th anniversary next year. With sales of more than 96,000 units in 2018 and record turnover of £4.1 billion, JCB are in very good health and few would bet against further expansion.
To enable that continued growth, the company has recently invested £65 million in a new factory in Gujarat, India, spent £50 million on new head office premises for subsidiary company JCB Germany and is about to open a £50 million, purpose-built, cab-manufacturing plant near its global headquarters in Staffordshire. That will bring the company’s UK factory count to 11 separate facilities, from a global total of 22 manufacturing sites.
While JCB might not be the biggest equipment supplier to the quarrying industry when it comes to face digging, the company’s machinery is well represented within the extractive business, particularly in the rehandling sector. JCB are also one of the leading suppliers to the fast-growing recycling and materials-handling markets.
One of the reasons for this success has been JCB’s commitment to a vertically integrated design and engineering philosophy. The company produces a surprising amount of its componentry in house, including the JCB Dieselmax diesel engine, JCB transmissions and axles, hydraulic cylinders and many other smaller components.
‘The opening of the new cab facility will make JCB one of the largest cab providers in Europe, allowing us the opportunity to design and engineer the cab, not just for machine operators, but for manufacturing and assembly,’ said chief innovation and growth officer Tim Burnhope.
JCB will further develop their Command Plus cab, already seen on many of the company’s wheel loaders and Loadall telescopic handlers, to suit a wider range of machinery. The Command Plus design can also be seen on the firm’s latest X-Series crawler excavators. By integrating their own engines, transmissions and axles into dedicated drivelines, JCB have also been able to focus more on industry-specific performance and productivity.
‘Now looking at our wheeled loading shovel offering, the JCB 457 model offers great productivity, with fabulous fuel economy and an excellent cab environment,’ said Mr Burnhope. ‘We’ve had a lot of success with these loaders, across Europe and in Scandinavia.’
Though the 457 is currently the firm’s largest wheeled machine in emissions-regulated countries, JCB also offer a larger 467 loader in less-regulated territories. Likewise, the firm has a heavier crawler excavator for quarry customers outside Europe and the North American market.
Of course, the family-owned company is better known for its wide range of compact machinery and it is here that JCB are again taking a lead on many of their competitors. The company has launched its first full electric, battery-powered machines, including an electric mini-excavator which is already proving popular with rental companies, contractors and demolition businesses.
While electric drive has been a popular option in specialist markets, such as powered access, for some time, indeed JCB offer a range of battery-powered work platforms, powering digging and loading equipment has traditionally been a job for the diesel engine. However, with the launch of the 19C-1E electric mini-excavator and the 30-19E Teletruk, the company is pioneering zero-emission running to a broader customer base.
Though both are part of a growing E-TEC range of JCB machines, the mini-excavator and the Teletruk industrial forklift take a slightly different approach to battery power. The 19C-1E mini uses automotive lithium-ion batteries, while the Teletruk operates on lead-acid batteries. Each power source has been chosen to suit the individual application, with lithium-ion better for to all-day independent use on site with an overnight charge, whereas the lead-acid batteries in the Teletruk can easily be removed and replaced for charging, providing round-the clock working, if required, in industrial applications. The heavier lead-acid batteries are also used to provide part of the counterweight for the Teletruk’s innovative telescopic loader arm.
The 19C-1E is perhaps the more important step forward, providing cable-free operation on construction and demolition projects, with low noise and zero emissions at the point of use. Early success will no doubt lead to the introduction of additional full electric models across the JCB range.
‘We’d always thought the focus of electric would be on smaller products,’ said Mr Burnhope.
‘The machine has to be commercially viable as a working tool and the electric mini has already been a real success for us. The scalable challenge is the cost and the return on investment. You’ve got to work out the right job site and the applications that suit an electric machine.’
That said, while JCB had expected some urban contractors and utilities to take to the electric mini, the growth has come from a much wider customer base. The electric machine is proving popular in demolition, where it can work inside buildings. Similarly, the excavator lends itself to underground and tunnelling work, where zero emissions are an essential requirement. The high cost of exhaust extraction equipment for use in underground and tunnel work, in particular, has made the initially higher purchase cost of the electric machine less of a concern for contractors.
More of a surprise is that the machine is experiencing growing international demand, with customers around the world showing interest.
‘We’ve got people in Africa and India asking for the electric mini,’ said Mr Burnhope. ‘One of the challenges with pioneering is that you think it’s going to be a niche machine, but there are the same emissions issues for customers worldwide. It’s important that we approach the future with a really open mind.’
Of course, while electric drive is a rapidly emerging technology, JCB continue to develop their more traditional power sources. The company is investing heavily in its diesel engine ranges, to meet ever more stringent emissions regulations.
‘We’ve got such a large product portfolio and we want to get everything through EU Stage V. The 55kW engines and higher-powered models are starting to ship now. Stage V is ultra-clean diesel,’ said Mr Burnhope.
‘We’ve reduced the fuel used by our customers by 50% in recent years and the engines are now so incredibly clean. This is very exciting and can help have a very positive impact on climate change. We are working to minimize CO2 and to come up with solutions that provide close to zero NOx. However, we need to see clear steps to carbon neutrality.’
JCB believe that a machine’s driveline is not the only way to improve efficiency and boost productivity. A move towards automation and connectivity will bring equally valuable improvements. Here too, JCB are at the forefront, having equipped many of their machines with the LiveLink telematic system for many years now, whilst offering all of their heavier excavators pre-wired for machine guidance and control systems from the factory.
‘We are hungry to develop automation for the benefit of the industry. We want to build on our success with telematics and I think we’ve got to produce the very best pieces of construction, waste and quarry equipment, that have the perfect solution for the customer,’ said Mr Burnhope.
‘We’ve got to have the most intuitive machines for both novice and skilled operatives. We’ve got to embrace new technologies – batteries, gas, fuel cells – while embracing our clean technologies which Stage V takes to a whole new level. There are going to be big breakthroughs in technology and the use of that technology could be a great opportunity for equipment providers.’