Loading Made Simple With Aggregate Autodig
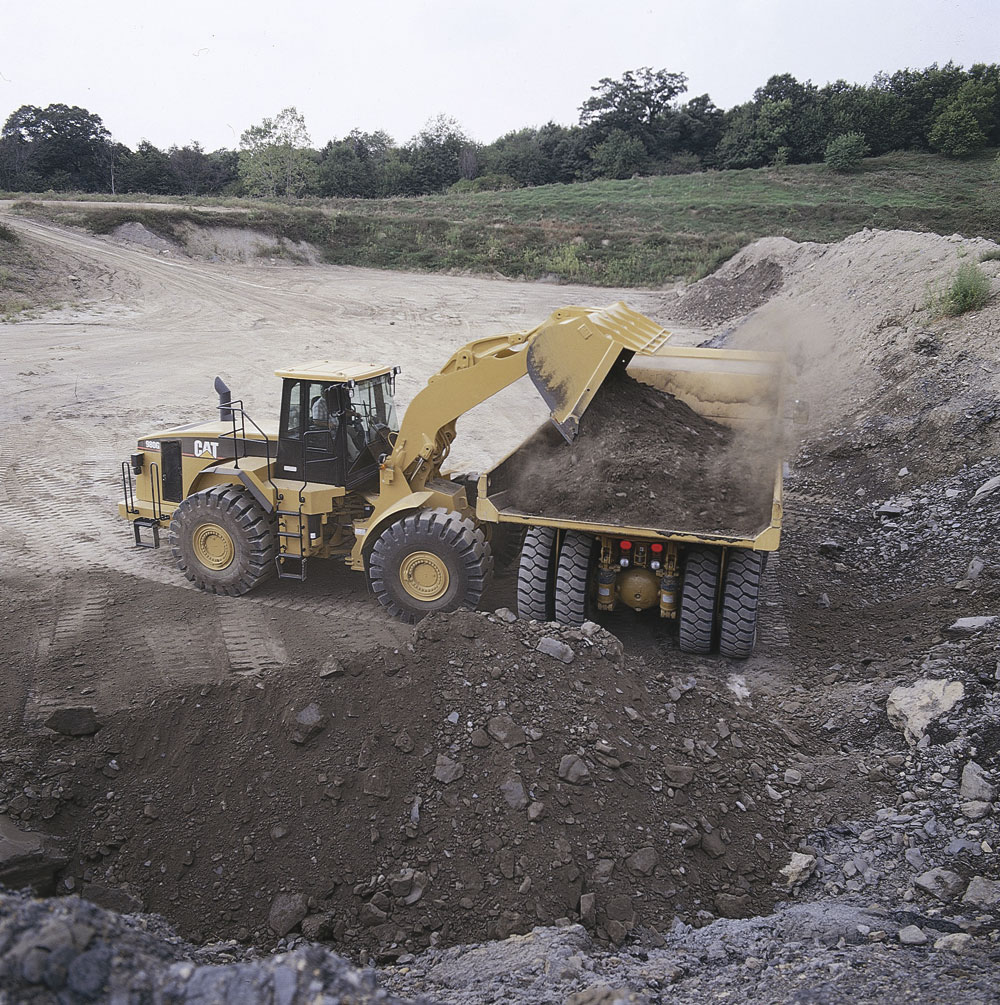
Caterpillar’s automated bucket-loading system helps improve bucket fill and cycle times
With ever tightening margins and a shortage of skilled mobile plant operators, the challenge of increasing productivity to maintain profitability has never been tougher for the aggregates industry. However, Caterpillar believe they have come up with the solution that many businesses are looking for — an automated bucket-loading system that not only guarantees consistently full bucket loads and reduced cycle times, but also helps to minimize wear and tear on the loading machines.
Called Aggregate Autodig, the automated loading system is available on Caterpillar’s
G-series II mid-size wheel loader range and is aimed at both experienced operators and those who are new to the profession.
The decision to develop Autodig followed numerous requests from companies in the aggregates industry for help in increasing productivity and reducing wear and tear. In addition to offering training and advice to mobile plant operators, Caterpillar believed that an automated loading system could help to resolve many of the common productivity issues faced by the industry, and following a six-year research and development programme Aggregate Autodig was unveiled.
The system, which uses Caterpillar’s advanced electro-hydraulics to control the lift arms and bucket and automatically load loose aggregate material, is very simple to set up and use. With a series of easy-to-navigate controls located in the overhead console and on the lever pod, the operator simply has to follow four straightforward steps.
First, switch the Autodig function on; second, select the operating mode; third, set the dig mode selector to suit the density of the material being loaded; and finally, set the linkage height stop if needed (a default position exists). Once the controls are set, the operator places the bucket near the ground and drives towards the pile in first, second or third gear. As soon as the bucket engages the pile Autodig takes over, controlling the lift and tilt, and automatically downshifting to the correct gear. Once the bucket is full Autodig tilts it fully to minimize spillage, lifts the linkage to the preset height and sounds a horn to indicate the end of the loading cycle.
Because the system is so easy to use, when it was first introduced to operators many viewed it with scepticism, particularly the more experienced ones who either questioned its effectiveness or were worried that it would contribute to further de-skilling or even make the profession redundant.
However, as Caterpillar product engineer Shaun Harpley explained, the system is not designed to replace operators, but to help them to achieve maximum levels of productivity.
‘The beauty of the Autodig system is that it removes from the operators the stress and tedium of repeatedly filling the bucket, allowing them to concentrate on driving the machine and interacting with third parties,’ he said. ‘Steering, throttle and directional shifts are all still controlled by the operator.’
Moreover, operators have the option to challenge the factory settings to see if they can achieve faster cycle times and can even record their own cycle times/ methods and set these as the standard parameters for Autodig.
Independent performance study
During an independent audit performance study carried out by Caterpillar, both experienced and inexperienced operators saw improvements in bucket fill and average cycle times when using a mid-size wheel loader with the Autodig function.
While the average cycle times were very similar for the experienced operator with and without Autodig (26s and 27s respectively), the average bucket loads were consistently higher when the Autodig function was switched on. With the inexperienced operator the differences were even more significant, with Autodig taking six seconds less to complete a cycle than the operator (30s rather than 36s). Once again, the average bucket loads were also consistently higher — an increase in productivity of over 100 tonnes/h.
Commenting on the findings, Mr Harpley said: ‘These tests showed that the Autodig system offers different benefits for different operators, depending on their experience. For the inexperienced operator Autodig can act as a useful training tool, helping to build confidence and experience, while for the experienced operator it helps to reduce fatigue and maintain optimum productivity levels throughout an entire shift.’
Reduced machine wear
As well as increasing productivity, the addition of Autodig helps to reduce mechanical wear and tear because the machine is driven to the manufacturer’s standards rather than having to cope with the idiosyncrasies of different operators. This, say Caterpillar, could potentially contribute to better fuel consumption, as operators tend not to drive the machines as harshly when Autodig is switched on.
Another costly issue for machine owners is wear and tear on the tyres and ground-engaging tools. One of the most common causes of premature wear on tyres is wheel spin, which is caused by drivers entering the pile too fast or in too high a gear. However, Autodig also controls the transmission during the loading cycle and automatically shifts the machine into the correct gear, thereby minimizing both wheel spin and tyre slippage. In terms of the ground-engaging tools, bucket positioning during both the loading cycle and while the machine is travelling is critical to the wear rates. Once again, the Autodig function dramatically reduces this problem by controlling both the dump height and return-to-dig positions, ensuring that the bucket teeth are not dragged along the ground. Also, by positioning the linkage at the correct height at the end of the loading cycle, spillage from the bucket is minimized while the machine is reversing or travelling.
These findings have been reinforced by the experiences of Bardon Aggregates. They recently signed a deal with Caterpillar dealers Finning (UK) Ltd for three Cat 972G series-II mid-size wheel loaders fitted with the Aggregate Autodig function for use at their Warmwell Quarry near Weymouth, in Dorset, which produces 500,000 tonnes of aggregate a year.
According to quarry manager Dave Searle, the Autodig system was selected for its ability to allow automated loading, but even he was surprised at how quickly his experienced operators adapted to the new function: ‘The drivers love it and the new system has reduced our costs right across the board,’ he said.
Finning (UK) Ltd, Watling Street, Cannock, Staffs WS11 3LL; tel: (01543) 461461.