Haul Road Maintenance
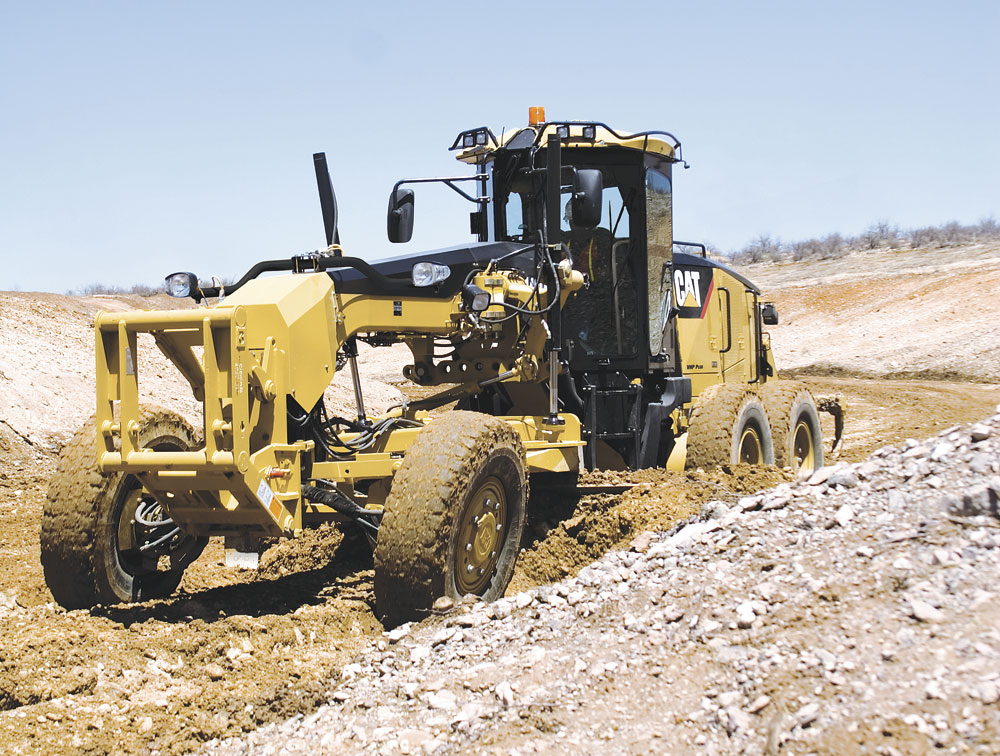
A vital factor in the value chain
By Mark Senyard, product manager of Barloworld Equipment, South Africa
As a general rule, the ability to travel comfortably along a quarry haul road in a light commercial vehicle at a safe and acceptable speed is a good indication of a well-maintained surface. However, this is just one indication, and a host of other factors need to be considered to ensure a safe and cost-effective haulage route. These factors include gradients, drainage and road width design.
As a starting point, it is important to emphasize that haul road maintenance requires a dedicated focus and must be addressed on a continual basis as part of the operational cycle since good roads improve production, extend tyre life and reduce overall operating costs. The reverse scenario is equally true.
Tyres are a key expenditure item to be preserved for as long as possible. However, despite this, approximately 80% of all large tyres fail before wear due to poor maintenance and operating practices. This statistic is underscored by a recent study at a major metal mine, which indicated tyre cuts (45%) and impact damage (20%) as the largest contributing factors towards premature tyre failure.
The chief culprit is spillage from off-highway haulage trucks. It is, therefore, critical that a motor-grader is deployed on site to continually maintain haulage routes and remove loose debris.
Poor road maintenance practices also result in an increase in rolling resistance, defined as the pressure exerted on the tyres by a road’s riding surface. Typically, for off-highway trucks running radial-ply tyres, a minimum rolling resistance of around 1.2% would be expected for a hard and well-maintained permanent haul road. However, if this figure increases by just 5%, the impact becomes disproportionately greater and could result in up to a 10% decrease in production, and a 35% increase in production costs.
Essentially, there are three key factors that determine optimum haul road condition: material quality; design; and maintenance. It is equally important to note that haul roads begin at the loading face and end at the dumping point, and maintaining good floor conditions in both of these areas will definitely reduced tyre wear and fuel burn costs.
Once a road deteriorates, assuming it was well constructed in the first place, it takes five times as long to repair it again to an acceptable condition. In this respect, it is important, in terms of maintenance, to match the right grader and water tanker units to the quarry’s haulage route.
Grader size
The size of the grader will depend primarily on the width of the haul road, but will also be influenced by the road’s construction, and the quarry’s ongoing maintenance programme. A neglected road will require more intensive remedial action and a larger grader to cut and grade final levels.
Caterpillar’s H-Series motor-graders have set the industry standard across the quarrying, mining and construction sectors for many years, and have now been complemented by the introduction of the M-Series, which is gaining ground in southern Africa following its global introduction. Available in seven different models, the M-Series starts with the 120M (14,093kg operating weight) and extends to the 24 M (62,456kg operating weight).
What distinguishes the M-Series from the H-Series is the introduction of joystick controls, replacing the conventional steering wheel and operating levers. The two electro-hydraulic joysticks reduce hand and wrist movement by as much as 78% compared with conventional lever controls, greatly enhancing operating efficiency, while the high level of visibility (view forward to the blade, working surface and front tyres) makes the M-Series easier to operate without sacrificing control.
For reshaping haul roads, the typical blade loads are about one-third to half of full capacity. However, where large hauling units travel on softer materials, heavy blade loads may be required to reshape the road surface. Many quarries are also located in areas requiring haul roads with steep gradients or where very precise roadway elevations and slopes are desired. These considerations will determine which grader model best suits the application.
The 120M through 16M (26,060kg operating weight) models provide a broad range of extended blade positions that are particularly beneficial in mid-range bank sloping, ditch cutting and ditch cleaning. A long wheelbase permits an aggressive blade angle, allowing material to flow more freely and reducing power requirements.
Servicing time and cost on the M-Series has also been reduced. For example, top accessible drawbar wear inserts and the shimless mouldboard retention system make DCM (drawbar, circle and mouldboard) adjustments fast and simple, delivering precise material control while further reducing operating costs.
Dust suppression
Of equal importance to having a well-constructed and graded haul road is the need for dust suppression. Dust thrown up by continuous haulage can reduce visibility and mobility, posing a safety hazard. Additionally, regular watering helps to maintain compaction.
As a guideline, the size of the water tanker should match the size of the haul trucks. For example, if the quarry is using Cat 777 units, these should be supported by Cat 777 water trucks. Tanker size will also depend on factors such as the length of the haul road and the location of fill points. ‘Spot’ watering also works well for areas with limited water supply, and for safe travel, a ‘checkerboard’ or intermittent ‘spot’ pattern is recommended to reduce the slippage risk during retardation on gradients.
The downside of over-watering should also be considered, as washing out the fines will lower the cohesive properties of the road, accelerating deterioration and causing potholes to form. These will grow rapidly if ignored, and soft and wet spots need to be completely refilled and compacted with good, dry material. Optimally, the slope of the road should adequately carry away storm water run-off, with minimal evidence of water entry into the road sub-base.
In addition to designing haul roads to save on costs, safety is of paramount importance. To avoid the risk of collisions on two-way sections, the design should cater for worst-case scenarios with approaching corners and crests clearly visible at standard travel speeds. The short distance for horizontal and vertical curves must be sufficient for a machine to stop before reaching a hazard or obstacle, and the distance from the operator’s eye must equal or exceed the required stopping distances.
Gradients should be kept smooth and constant as this minimizes transmission shifts, permits a higher average speed to be maintained, and allows more constant braking effort on returns. Gradients of less than 10% are recommended for maximum tyre life.
Computing the haul road width on horizontal curves is a specialist area. For example, a wider road is required on curves to account for the overhang occurring at the front and rear of the machine, as well as the lateral clearance between passing trucks.
On one-way straights and corners, a minimum of two to 2.5 truck widths is recommended, but for two-way traffic, this would increase to a minimum of 3 to 3.5 truck widths on the straights, and a minimum of 3.5 to 4 truck widths on the corners. However, each quarry is different and extra width allowance should be made where needed, to accommodate difficult driving conditions.
This article first appeared in Modern Quarrying, the official magazine of the Institute of Quarrying Southern Africa.