Decarbonizing Heavy Construction Plant
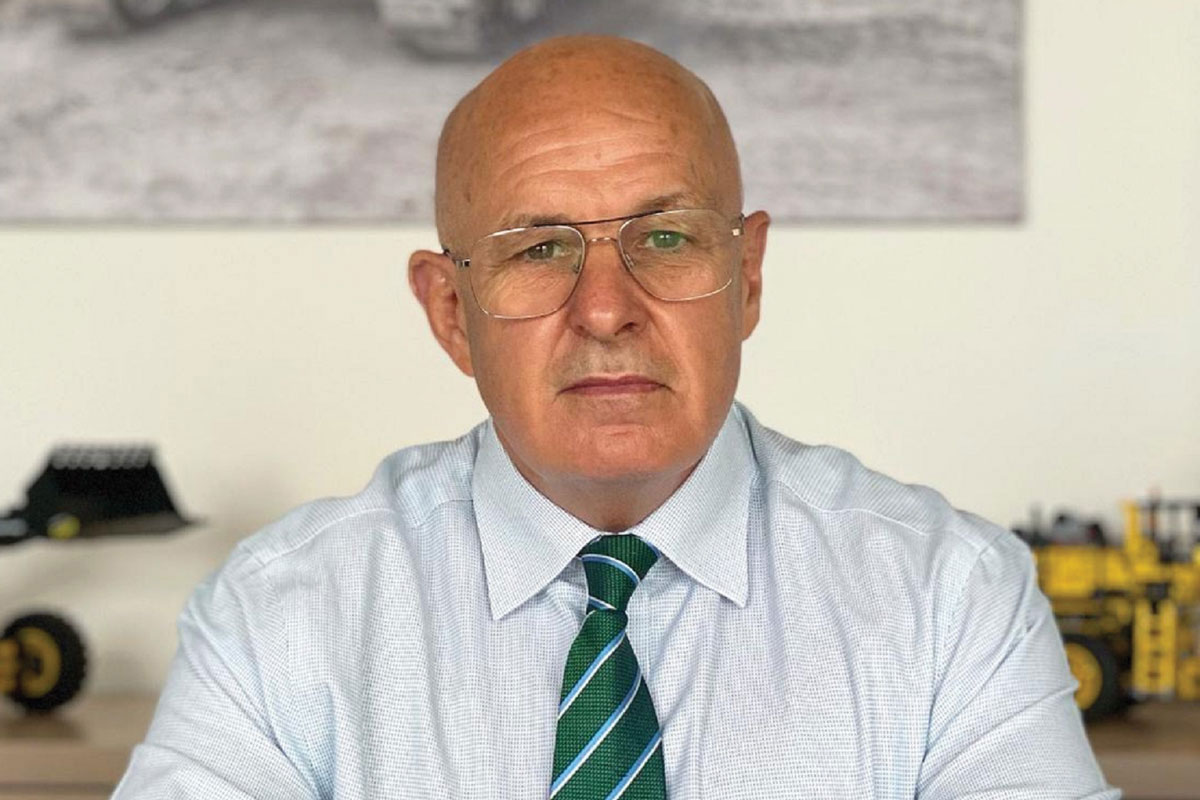
First published in the June 2021 issue of Quarry Management as Blueprint for a Green Future
As the Government seeks to deliver net-zero emissions by 2050, QM spoke to John Corcoran, managing director of Chepstow Plant International (CPI), about the importance of decarbonizing heavy construction plant through robust carbon footprint accounting, fleet-management services and an innovative mindset to help build a low-carbon future
Climate change has emerged as one of the biggest environmental challenges facing the planet. Whilst COVID-19 has changed the world and continues to dominate global headlines, no individual or organization is immune to the challenges that climate change presents, and everyone has a role to play in combatting it.
Businesses are increasingly aware of the need to address climate change and the move towards a zero-carbon future is not just about short-term expedience, but developing long-term solutions that are central to achieving a low-carbon economy.
The way new buildings and infrastructure are delivered will have a critical role in how the UK meets the Government’s ambitious carbon-reduction targets. According to the UK Green Building Council, around 10% of the country’s carbon emissions are directly associated with construction activities. And the number rises to 45% when taking into account the whole of the built environment sector.
The above figures clearly show an opportunity for the construction industry to help the Government reduce greenhouse gas emissions and achieve the goal of net-zero carbon by 2050. It also puts the industry in a position of great responsibility and influence, and the commitment to change has to be throughout the entire construction supply chain.
Parts of the construction sector are already taking a lead in addressing the challenge, with steps being taken to encourage sustainable behaviours and to put tangible goals and measures behind the commitments that have been made to tackling climate change.
The UK quarrying sector as a whole is aware of the need to decarbonize and has a pivotal role to play in helping the construction and infrastructure industry to improve its sustainable working practices and environmental performance.
Whether it is switching to full electric-powered construction machinery, recycling more building materials/components or reducing embodied carbon in construction projects by using more sustainable materials (eg low-carbon concrete), everyone in the mineral products supply chain – from designers and OEMs to contractors and investors – now has a responsibility to measure the embodied carbon footprint and consider the whole-life carbon performance of a product in its final application, such as a new building or resurfaced road.
Driving digital change
Innovations in digitalization and advanced data analytics are opening the door to improved efficiency, increased machinery uptime, safer working conditions and lower costs across the quarrying and aggregates sector.
‘In an industry focused on reducing running costs, enhancing operational efficiency, elevating health and safety standards, and cutting carbon emissions – lifecycle analysis and asset management are becoming ever more important,’ said John Corcoran, managing director of Chepstow Plant International (CPI), one of the UK’s leading mobile plant supplier firms and earthmoving contractors in the mineral products industry.
Headquartered in Caldicot, South Wales, the company has a long and successful track record of working closely with its clients and equipment partners to maintain the highest levels of health and safety on site, and leveraging data and innovation to deliver sustainable and practical solutions for resource extraction and materials transportation.
Digital and automation technologies have, undoubtedly, advanced in leaps and bounds over the last few years, giving quarry operatives and fleet managers immediate access to important operating parameters, condition and technical information.
As the pressure grows on aggregates producers to reduce operational costs and deliver long-term sustainability, having this kind of critical data at their fingertips speeds up decision-making, troubleshooting and performance efficiency.
‘As a forward-thinking and sustainable sector, we must embrace the opportunities and cutting-edge technologies that will help us build a low-carbon future,’ said Mr Corcoran, who leads CPI’s efforts to find innovative ways to help earthmoving customers move aggregates safely, efficiently and become more environmentally friendly in the process.
‘New digital technologies, such as telematics, IIoT (Industrial Internet of Things) and advanced analytics, have impacted almost every aspect of the industry operation, particularly in load and haul applications.
‘There is no doubt, the future of quarrying is digitalization because it provides the greatest potential for improving business and operational efficiency, with a more environmentally focused perspective.’
But of all the trends impacting the construction industry supply chain, none will be as critical as decarbonization. Quarries and mineral extraction sites must become more agile and future-proof in readiness for the new technologies, energy/carbon reporting tools and climate-related changes and legislation that will transform the sector for decades to come.
Reduced fuel usage, lower carbon emissions
Given the unstable financial climate brought on by the COVID-19 pandemic, a key challenge for many aggregate suppliers, earthmoving contractors and heavy plant suppliers, such as CPI, is delivering the lowest-cost-per-tonne productivity and maximizing returns on investment by improving fuel economy, cutting downtime and reducing overall running costs.
‘Fuel consumption is a huge overhead and accounts for a significant proportion of total machine operating costs in heavy plant and equipment,’ commented Mr Corcoran. ‘However, by taking a holistic view of expenditure and putting in place energy-management plans and cost-saving initiatives, quarry operators can cut operating costs by tens of thousands of pounds and demonstrate best practice in reducing carbon emissions and improving energy efficiency.
‘The recent sharp rise in fuel costs that we have seen in the UK, often partly due to high taxes, has made quarry and fleet managers more aware than ever of the implications of the vehicles and equipment they run and how they operate them.’
So, is this the end of the road for the diesel-powered combustion engine? There is no question that construction equipment is set to undergo radical changes over the next decade or so, as one of the major areas of emphasis going forward will be the continued drive towards electrification.
Whilst diesel-electric hybrids and full electric-powered machines can provide lower total cost of ownership and deliver a positive impact on climate change in response to the industry’s decarbonization challenge, there is still huge potential for improving the eco-friendliness of conventional engines, with the help of better fuels and lubricants.
It is also worth noting that diesel engine technology in non-road mobile machinery (eg articulated dumptrucks, excavators, wheel loaders, jaw crushers etc.) has progressed enormously in recent years, with construction equipment becoming more fuel-efficient and cleaner under EU Stage V emission standards.
It pays to analyse
It is no secret that heavy-duty mobile equipment on jobsites spend a large proportion of their time idling, with one leading OEM estimating that an average machine will spend 40% of its time idling whilst in operation.
There are a host of factors that impact fuel efficiency and equipment performance in quarrying applications. Fleet owners and managers can reduce costly fuel bills by maximizing operator training to ensure reduced carbon emission levels, checking earthmover tyres pressures regularly, utilizing telematics technology, etc.
One of the simplest yet most effective measures that can bring substantial savings to a fleet is idle reduction. Switching the engine off during periods in the haul cycle reduces unnecessary machine operation and presents a cumulative fuel saving opportunity for heavy plant operators.
Furthermore, fleet managers who reduce idle time are likely to see benefits such as improved processes, decreased engine maintenance costs and reduced emissions of harmful greenhouse gases into the atmosphere.
‘It is obvious idle time has a direct impact on fuel consumption and eats away business profits,’ explained Mr Corcoran. ‘However, engine idling is often overlooked in the aggregates sector.
‘To effectively protect against unplanned downtime and reap the benefits of increased efficiency and lower fuel costs, it is important quarry managers are aware of, and address, the hidden impact that prolonged machine idling can have. Cutting out engine idling across a fleet is a quick and relatively easy way to improve fuel efficiency, reduce your carbon footprint and, ultimately, increase profit margins.’
With decarbonization high on the construction agenda, it is more important than ever to prioritize and achieve long-term sustainable and verifiable reduction in energy consumption and carbon emissions.
And with these changes in mind, the UK earthmoving sector is looking to data and analysis as a way to keep costs down, production high, operators safe and carbon emissions within bounds.
Providing exceptional customer care and great value has been CPI’s focus since the business was founded in 1995 by Eddie Hayward, whom Mr Corcoran has praised for ‘his entrepreneurial approach to business and ethical approach to life’. Almost 26 years later, and Mr Corcoran is clearly excited by the future growth potential for the company and the opportunities in the heavy equipment rental market.
‘Despite the challenges posed by the current COVID-19 crisis, CPI have recently signed a multi-million-pound deal for more than 70 new Stage V-compliant Volvo machines,’ he stated.
‘Like any business, it’s imperative that we continue to meet customer demand and we can only achieve this by delivering the latest and most efficient and environmentally friendly assets currently available. Continued investment remains the most sensible option for companies during uncertain times and this approach has ultimately unlocked a number of economic and sustainability benefits for both CPI and their clients.’
In addition to this, CPI’s customer-centric business approach to delivering equipment-management solutions has helped the company become the preferred strategic partner and supplier to some of the biggest players across the quarrying industry and its wide supply chain.
Earlier this year, CPI strengthened their service offerings with the launch of EvoFleet, a new fleet-management service to help their clients become more efficient, productive and environmentally friendly.
‘The EvoFleet service programme is an example of our proactive approach to catering for the needs of our customers,’ said Mr Corcoran. ‘As we enter a post-pandemic recovery, not to mention the Brexit impact on trading conditions, many contractors and quarry operators are facing a challenging business landscape driven by hikes in energy costs, legislative measures to reduce noise and carbon emissions, and the need to be health-and-safety conscious and environmentally responsible.
‘In launching EvoFleet, we’re easing the burden and responsibility of asset management from our clients and, essentially, giving fleet managers complete peace of mind on a range of mobile equipment-related issues, from engine management and fuel cost savings to plant safety and operator training.’
Indeed, with everything from cycle time reporting to payload data, and machine performance to energy consumption, EvoFleet uses equipment telematics to ensure heavy plant machinery is being utilized effectively and efficiently.
It is expected that telematics and transportation technology will be widely adopted across the heavy earthmoving plant industry, particularly integrated AI data collection and predictive analytics. With telemetry technology comes a lot of data, and Mr Corcoran quickly pointed out that it is how the information is used that counts.
‘Adopting new technologies is just not enough – it’s the data that comes with it, understanding the benefits and harnessing that accurate data which will benefit your business at the end of the day,’ he stressed.
‘Data collection is critical across the board and when telematics data are used effectively they can take the guesswork out of mobile plant utilization by providing a full picture of the fleet operation and task ahead.
‘Being able to ‘see the future’ and make informed decisions based on operational data will drive business intelligence for fleet managers, especially as construction starts to pick up throughout 2021 and beyond.
‘Digitalization and plant automation have never been more important than in today’s climate, and the heavy plant hire sector needs to seize this opportunity to provide greater transparency across the supply chain and help fleet owners make the best decisions possible in mobile asset management, with real-time intel into what is happening from the field. This includes machine hours and location, information on available equipment, and fleet idle time, fuel consumption and condition.’
Perfect partner
All this attention to detail, coupled with the company’s strong investment in new plant, machinery and personnel, have all been key factors in the success of CPI. The mobile plant supplier has developed a strong national reputation for quality, service and innovation – operating an ongoing fleet-replenishment programme to ensure its customers have access to, and benefit from, one of the most modern contracting fleets in the UK with more than 400 machines.
And it is these CPI core values of always trying to improve and innovate that has seen the company develop longstanding partnerships with key clients and OEMs in the mineral extractives sector which, Mr Corcoran believes, allows Chepstow Plant to be at the forefront of game-changing industry improvements in asset utilization, safety and sustainable business practices.
CPI, for example, have strategic and collaborative partnerships with SMT GB and Volvo CE, which has seen the introduction of state-of-the-art inclinometers and advanced telematics systems, such as the Haul Assist application, fitted on all of the company’s Volvo articulated dumptrucks (ADTs) as part of their standard specification.
‘Operational productivity in the aggregates industry is being driven by the use of data and analysis, so it is important that we continue working alongside our customers and suppliers to help develop new machine enhancements and services like Volvo’s Haul Assist, which allows operators to monitor their articulated hauler fleets and optimize haul cycles using a real-time tracking map,’ said Mr Corcoran.
With many quarry operators fully committed to delivering further safety improvements as part of the industry’s ‘Zero Harm’ and the Mineral Products Association’s ‘Vision Zero’ initiatives, there is a growing need for OEMs, contractors, site owners and plant suppliers to share and spread best working practices across the construction supply chain.
‘Health and safety is our first and foremost priority,’ continued Mr Corcoran. ‘As one of the leading plant suppliers in the UK heavy equipment market, we have a duty of care to provide our clients with the highest levels of health and safety performance and to ensure a safe work environment is developed, maintained and monitored in meeting the industry’s Zero Harm objectives.
‘We have already seen a significant reduction in unsafe tipping, thanks to additional safety equipment measures such as the Volvo-designed inclinometers and Bell Equipment’s ‘Safe Tip’ management software on all our ADTs.’
Apart from safety, fuel burn and tonnes per litre moved are equally important subjects for CPI’s customers, and the company will continue to work in collaboration with its industry partners to help clients to accelerate their adoption of cleaner energy and mobility solutions, and to achieve their decarbonization goals.
At the same time, Mr Corcoran said CPI will focus on minimizing the environmental impact of their own operations and supply chain to reduce their overall carbon footprint.
‘Approximately 98% of our earthmoving contracting fleet is currently powered by EU Stage V/Tier 4 Final engines, so our machines are amongst the best in their class on current emissions standards,’ he commented.
‘However, as a proactive, forward-thinking business, we want to go the extra mile and further reduce idling time across our entire ADT fleet because Stage V presents a real scope for technological advancement and key opportunity to help us cut spending on fuel and reduce environmental pollution such as noise and exhaust gases.
‘We want to take more accountability for our carbon output and CPI have already set new carbon-reduction targets across their articulated dumptruck fleet, to not only mitigate greenhouse gas emissions, but also to positively demonstrate our environmental commitment to the construction and quarrying industries.
Mr Corcoran added: ‘We recently conducted a detailed study into idle reduction and found that a CPI-operated ADT (Stage V compliant) idling for 30 minutes daily and running 2,000 hours per year would consume 42,000 litres of fuel and produce 110 tonnes of CO2.
‘By reducing average idling times across our fleet and cutting a machine’s carbon footprint with lower CO2 emissions; we are, effectively, increasing our ecological handprint, which would allow us to run 16 new ADTs with net-zero carbon emissions in 2022 through carbon offsetting.
‘If we look at the wider industry and the impact this could have, indicative figures show that a high proportion of mobile plant in the sector spends 30-35% of its time idling. For assets working 2,000 hours a year, this can equate to almost 2-3 hours each day. Not only do businesses incur thousands of pounds in wasted fuel, but there are substantial environmental savings to realize.
‘Utilizing the CPI Carbon Neutral Model, companies with this excess idling could reduce their impact by approximately an additional 440 tonnes of CO2 and burn more than 120,000 litres less fuel per machine each year, all by tackling idling time on site. Across a fleet or network of sites, these figures can very quickly escalate and therefore provide a genuine opportunity for companies to reduce their impact on the environment.’
As technology continues to develop, from 5G remote-controlled machinery to cloud-based monitoring tools, there has never been a better time operating in the quarrying and aggregates industry.
The latest developments in vehicle telematics, GPS fleet-tracking systems and on-board technologies – along with the experience of fully trained drivers and new machine enhancements – can help fleet owners/operators drive efficiency and performance on their jobsites, whilst reducing their carbon footprint and keeping mobile equipment going for the long haul.
And this is where CPI have come to the fore. For a company always thinking about what the client will want as an end product, CPI recognize the key role technology and their all-encompassing approach to sustainability have played in their success. The heavy mobile plant supplier has taken active steps to explore and implement more sustainable practices to improve its safety and environmental performance, and help clients with theirs.
These include: raising awareness of environmental issues among operatives and customers; adopting additional emission-reduction measures; and helping to deliver innovative technologies that promote a safety-first mindset and eliminate all energy-related greenhouse gas emissions. Undoubtedly, a win-win for CPI, their clients, the industry, and the environment.
- Subscribe to Quarry Management, the monthly journal for the mineral products industry, to read articles before they appear on Agg-Net.com