Combined Power
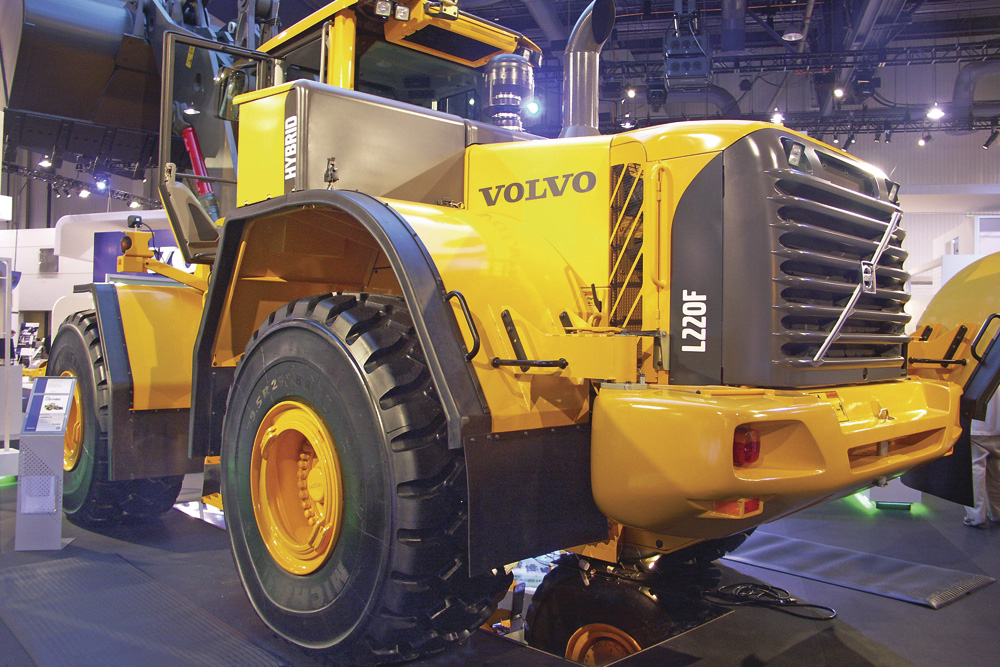
Hybrid systems will add cost and complication to machines but quarry owners who embrace the technology could cut their fuel bills. Colin Sowman investigates
After more than 110 years of development, the diesel engine is about as good a power source for mobile plant as it is possible to get – it is small for the amount of power it produces, quiet, reliable, long lasting, needs only a daily supply of fuel and is now very clean. However, it has two big drawbacks: the cost of diesel and the CO2 emissions that result from burning fossil fuels.
Miles Watkins, director of sustainable construction with Aggregate Industries, says the fuel consumption of mobile plant is by far the biggest contributor to the carbon footprint of the company’s quarrying business. He would be extremely interested in evaluating systems that can reduce carbon emissions but feels the plant manufacturers have been ‘slow off the blocks’. ‘We’ve seen telematics and driver training but very little in the way of machine developments,’ he says.
Now, however, systems to reduce fuel consumption are starting to make their way through into production machines. Many plant manufacturers are exploring hybrids – machines with more than a single source of power – as a way to cut fuel consumption and thereby reduce CO2 emissions and fuel bills.
Most hybrids work on the basis of harvesting and storing energy when it is not needed and feeding it back into the drivetrain when additional or maximum power is required. Traditionally, this energy has been wasted. For instance, applying the brakes turns the kinetic energy embodied in a moving machine into heat which is then dissipated to the atmosphere. But now systems are being developed to capture and store that energy, and in many cases this involves an electrical system and batteries as a storage medium.
Unlike the one-solution-fits-all diesel engine, hybrid systems are good in some conditions and bad in others. For instance, the Toyota’s Prius, the world’s most popular hybrid car, is at its best around town where repeated braking recharges the batteries which power the electric motor to drive the vehicle along or add to the petrol engine’s power when accelerating. However, on a long motorway run the batteries and electric motor simply add to the vehicle’s weight, which actually impairs fuel economy.
Hybrids, therefore, need to be tailored to the machine’s operation: harvesting spare energy when it will not impair the duty cycle and delivering it back when it can enhance performance. With that in mind it is not surprising that wheel loaders, with their stop and start, backwards and forwards operation, are the first targets for many manufacturers’ hybrid systems.
Volvo started the charge – albeit their wheel loader has not yet come to market – and others have followed with their own variations on the technology.
Having analysed a typical wheel loader duty cycle, Volvo’s engineers sandwiched a motor/generator unit between the engine and transmission. As the name suggests, the unit acts as a generator to charge the batteries and then switches instantly to a motor when additional power is required. In operation the unit would harvest excess energy from the engine, such as when the shovel comes free of the stockpile or when braking, in order to charge batteries mounted on the side of the machine. On the next cycle, when accelerating or penetrating the stockpile, the energy stored in the batteries is fed to the generator which instantly switches to motor mode and boosts the power available to the operator.
Having installed a large amount of battery power, other functions such as the air-conditioning can be run from them instead of from the engine, which means the operator does not need to sit with the engine running to keep cool.
While Volvo said the system could dramatically reduce fuel consumption, they now say battery and other technologies have moved on and the machine, as initially exhibited, will not go into production. However, Volvo’s crusade to reduce fuel consumption continues and hybrids will play their part, but so will other innovations such as the Optishift transmission which is cutting fuel bills by 15% while retaining the traditional driveline.
At this year’s Conexpo exhibition, Kawasaki exhibited a prototype wheel loader with a hybrid torque converter and a motor/generator. In place of a normal torque converter, Kawasaki are using a ring gear and set of planetary gears. The engine’s crankshaft is connected to the centre shaft of the torque converter while the drive to the transmission is from the centre of the planetary gears. A motor/generator is then used to control the rotation of the ring gear.
When the ring gear is free to rotate there is no drive through the system but as the ring gear is braked, drive starts to be transmitted to the transmission, and at the point where the ring gear is stationary, the power is passing straight through with only minimal losses. However, instead of a simple brake on the ring gear, Kawasaki’s system uses a motor/generator which can take energy from the system when the machine is braking or stationary and lifting its bucket clear of the stockpile, and feeds the additional power into the driveline when accelerating. In stockpile applications, Kawasaki say up to 35% fuel savings are possible and it plans to market the machine by 2013.
Taking a leaf out of Caterpillar’s book (see Cat D7E box), John Deere have developed a diesel-powered electric drive system for wheel loaders. The machine retains its diesel engine but this is coupled to an alternator (and a hydraulic pump) rather than a mechanical transmission. Each wheel is fitted with a brushless oil-cooled electric motor powered from the alternator. This system allows the engine to run at a constant speed and can, therefore, be optimized to be at its most fuel efficient at the set speed. In addition, electric motors provide maximum torque from zero revs. This allows the manufacturer to reduce the power and capacity of the installed engine without losing any performance in terms of driving into stockpiles. According to John Deere, their electric-drive wheel loaders can be up to 25% more fuel efficient in the right operation.
There are further savings too in terms of service items as the wheel motors are identical, so at around 20,000h the heavily used front motors can be swapped diagonally with the lesser-worked rears. John Deere expect to price the machine so that the fuel savings will pay back the on-cost within two years.
While wheel loaders are an obvious choice for hybridization, other plant items can benefit too, and Komatsu have had a hybrid excavator on the market for a couple of years. During that time more than one million operating hours have been clocked up – but only in Japan and China. However, at Conexpo 2011, Komatsu showed a refined Mk2 version which will be available in Europe and the UK.
The hybrid HB215LC-1 has a 104kW engine compared with 116kW in the standard 210 machine – and uses a motor/generator in place of the standard hydraulic slew motor. When the operator pushes the joystick the electric motor slews the upper structure. As the joystick is released the motor instantly switches to generator mode, which has the effect of braking the slewing turret. The energy created during this process is stored not in batteries, but in capacitors, which Komatsu say provide fast energy storage and instantaneous power transmission the next time the operator wants to slew.
Komatsu say the HB215LC-1 saves an average of 25% fuel compared with its standard excavator, and they back the hybrid powertrain with a five-year/7,000h warranty.
There could be even bigger fuel savings to be had with excavators, according to Tana Utley, Caterpillar’s chief technical officer and vice-president of product development. At Conexpo she said: ‘More than 50% of the energy you put into the fuel tank is lost through losses in the hydraulic system. So our engineers are going right back and looking at the architecture of the hydraulic system to see if there are different ways to put those components together to reduce metering and parasitic losses.’
One potential way to save energy would be to use individual electric pumps to power each hydraulic circuit. Not only would the pipe runs be shorter (with consequentially less energy loss), but electrically controlled pumps could offer improved controllability and responsiveness as well as lower fuel bills.
At JCB’s recent Waste Day event, group managing director Tim Burnhope hinted very strongly that the company was exploring hybrid technology, although he did not identify any particular machine type.
Researchers at Aalto University in Finland are using hybrid systems based on motor/generators with storage capacitors that can halve the fuel consumption of non-road mobile machinery. The project has already developed hybrid gantry container cranes, although production versions of more mobile machines may be five years away.
In the road transport sector, other forms hybrids are being evaluated including KERS (Kinetic Energy Recovery System), which is best known for its use on Formula 1 racing cars. According to Tobias Knichel of Flybrid Systems, storing the energy mechanically is more efficient than converting it into electricity and back again.
In commercial installations, instead of using foundation brakes to slow and stop the vehicle, the first application of the brake or retarder engages a constantly variable transmission (CVT) system which uses the excess energy to speed a flywheel up to 65,000 rev/min. When additional power is required, the input/output ratio of the CVT is adjusted so that the energy stored in the flywheel is fed back into the driveline.
A KERS unit is currently under evaluation in a city-centre bus and is equally applicable to other stop/start operations, and could be beneficial to machines such as articulated dumptrucks. However, the backwards/forwards operation of wheel loaders would make any KERS installations more complex, and it is still too early to know what fuel benefits the system could achieve.
Although hybrid technology is becoming available, many UK buyers may be reluctant to adopt such innovations as some 80% of the plant in the UK is purchased by plant hire companies. This poses a problem because the plant hire company may not know what its machine will be doing from one month to the next, so the ‘right operation’ cannot be guaranteed.
Furthermore, the additional purchase cost would be borne by the plant hire company while the user would accrue the savings in the form of lower fuel bills. The general feeling among hire companies is that the customer wants to pay as little as possible and a jump in the rental fee is out of the question. That said, at the smaller end of the market, Speedy have used the fuel savings available from several items to justify an increase in hire rates.
While these reservations do not hold true for quarries that own their machines, unless UK sales reaches a critical volume the manufacturers will not import hybrids. If they do, but the numbers remain very low, owners may be concerned about the service back-up available for their more complicated machinery.
For instance, if the only criterion was reducing fuel consumption, then UK buyers would be queuing up for Caterpillar D7E electric-drive bulldozer (see box). During extensive trials in the waste market, the D7E used between 10% and 30% less fuel than a D8 – but so far no UK company has placed an order.
‘It’s too early to say yet,’ says Matthew Hanlon from loader hire specialists John Hanlon and Co. He believes it is up to the manufacturers to produce a viable machine that provides fuel savings over the complete mix of jobs, rather than just one specific task.
Assuming the machine fits its operation, Miles Watkins says Aggregate Industries would then consider its reliability and whole-life costing. ‘If the initial price is higher that doesn’t matter too much providing the whole-life cost is equal or favourable,’ he said.
It will take time for hybrid technology to build up a track record and the manufacturers will have to make the machine more flexible if they are to gain wider acceptance. After all, you do not overtake a century of diesel engine development in a few years.