Bespoke Health And Safety
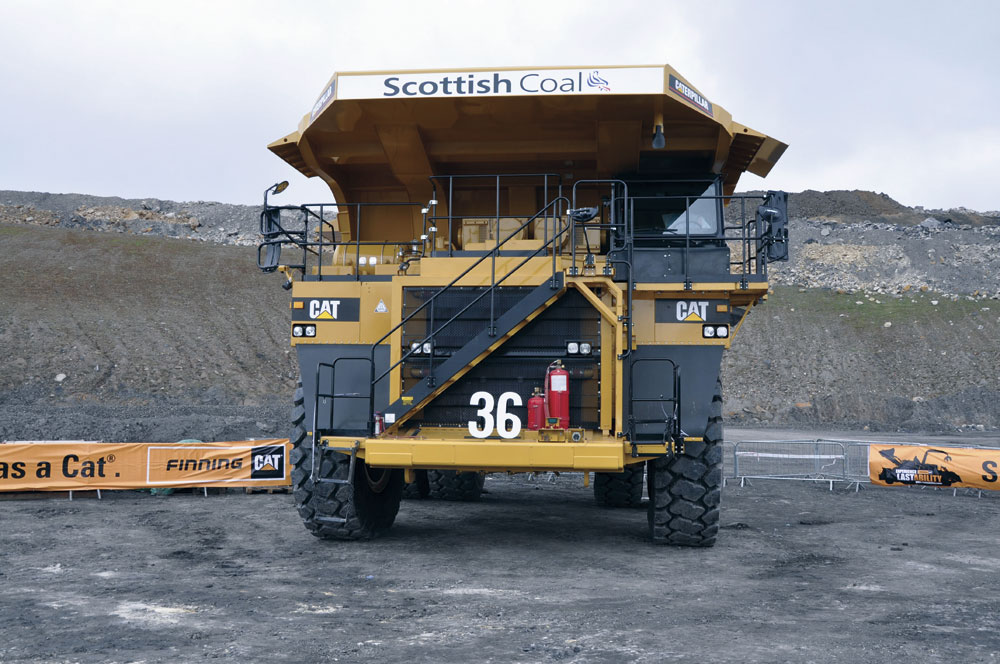
Andy Thomas of Finning Custom Solutions examines the Finning approach to mobile plant health and safety and says operators should not be afraid to enhance further
Health and safety, and in particular the protection of staff, is one of those subjects that everyone is agreed upon, which is why it is so important that the industry as a whole keeps challenging manufacturers of mobile plant and equipment to deliver safer products.
The challenge for manufacturers, however, is to comply with regulations. Compliant, regulated designs are a great start to improving health and safety, but should be no more than that – a starting point. Because the challenges faced by every plant operator demand a totally different approach, Finning (UK) Ltd now have a dedicated custom engineering team with the sole aim of providing solutions that are specific to machine, application, environment, process and climate.
There are two strands to this approach. The first relates to new equipment and product development, where the Finning custom engineering team work with Caterpillar colleagues and dealerships across the globe to feedback the needs of the UK quarry sector. Here, Finning are able to influence the design and manufacturing process of new and existing models as they are updated, a process which benefits customers on a global basis.
The second and probably most important strand relates to the retrofitting and design of bespoke systems for new and increasingly older equipment. Here, the Finning custom engineering team work hand in hand with their rebuild colleagues.
The answer to the question ‘Can we improve health and safety as part of the purchase or rebuild process?’ is most certainly yes, and it is here that quarry companies should do two things. First, talk to the operators who will be using the equipment, as they are at the quarry face and will often have very practical issues and even suggested solutions. Secondly, challenge the equipment supplier(s) to provide relevant options and ensure they understand the company’s site-specific problems and operating needs.
From a practical delivery perspective, in the author’s experience it is always important to share ideas with everyone involved in the process, making designs as visual as possible so that all can input into the final decision-making process. An excellent recent example of this collaborative working process was a bespoke access and egress system that Finning fitted to a new Cat 365C excavator for one of their quarry customers.
The challenge laid down by the customer was to develop what could best be described as a total access, egress and platform safety solution, never before attempted on the Cat 365C. This involved the creation of a complete set of straight stair-like steps that could be hydraulically raised and lowered. At the top of the stairs a total machine-surround platform was created with barriers enclosing the whole of the top of the machine. In addition, the existing walkways were enclosed and widened for safer movement around the machine at height.
This example demonstrates how customer-led health and safety concerns allowed Finning’s custom engineering solutions team to completely rethink and transform the way an operator could access a machine and be protected when servicing it. Now in operation, the system has proven to be so popular with the customer Finning are confident that, in the future, this option will be adopted by numerous other customers.
A common task when rebuilding a machine relates to the all-important issue of access and egress. As the industry knows, from a legal point of view, updating access and egress on older models is not mandatory. Increasingly, however, Finning customers are recognizing the potential hazards of sticking with legacy systems, particularly those customers with mixed fleets of new and older machines, operated by various staff members.
Improvements do not have to be particularly complicated or expensive. For example, when the first 785D dumptrucks were delivered into the UK recently, Finning’s custom solutions team helped their colleagues in the company’s Glasgow branch perform a number of practical alterations. These were based on both customer knowledge and site knowledge. Changes were made to access and egress with new steps designed to be lifted up and secured to prevent damage when operating on site. Other more simple changes included remounting the fire extinguisher for improved access and fitting bespoke mirror and camera systems to improve visibility.
Another very simple change highlighting site-specific thinking involved the movement of the 785D headlights. Due to the type of general site transport vehicles being used on site, had the headlights been kept in their original position, they would have shone directly into the eyes of oncoming staff – potentially dazzling them.
It can be seen from the above that the issue of health and safety and mobile plant use is a topic that should be constantly challenged at every point from specifying new equipment, right the way through to maintaining existing fleets and rebuilding.
For further information on Caterpillar products and services from Finning UK and Ireland, visit: www.finning.co.uk