Back To The Future
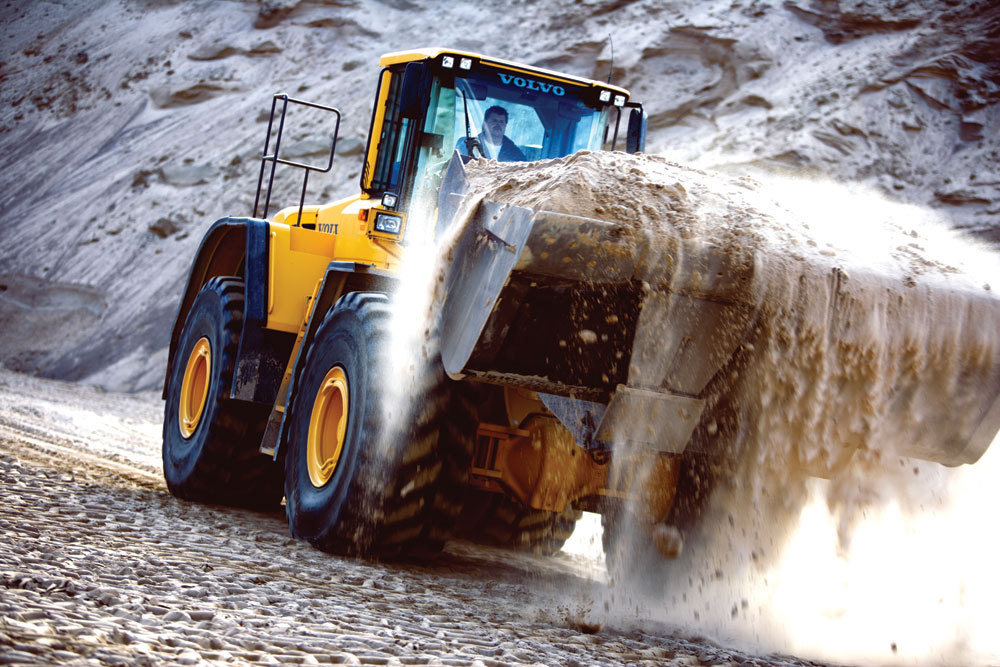
The diesel engine is not ready to give up its dominance of the construction equipment industry quite yet – but it does have to share the limelight. Brian O’Sullivan examines developments in hybrid engine technology
Hybrid engine technology is not new. Even though magazines are full of articles talking about multiple propulsion systems as if they were the latest invention, they most plainly are not: the idea is as old as the engine itself. But with potentially significant fuel savings and improved performance on offer, what hybrid technology plainly now is – is popular. Very popular.
The heat is on
For a combination of reasons the major nations of the world are now keen to develop new types of engines and work on adjustments to new fuels. The oil/combustion engine partnership has been dominant for over 100 years but its critics are getting louder. The fact that the supply of oil will eventually run out, that it is increasingly expensive and that demand for oil is projected to soon exceed supply are all helping to bring near the date when the world is no longer dependent on the ‘black stuff’. There are also concerns about burnt oil-based fuels’ CO2 emissions contributing to global warming and their impact on health. These diverse factors have now come into alignment; creating a situation whereby manufacturers are keen to develop vehicles – including construction equipment – that use less fuel, are more efficient and cleaner in their emissions.
On the fuel side, Volvo, the world’s largest producer of heavy-duty (9–18-litre) diesel engines, are conducting research into bio-diesels and biofuels generally which, if successful, will strongly reduce carbon dioxide emissions. It will take a while for the bio-diesel supply chain to creak into life, but it is growing fast: in the US alone bio-diesel sales tripled to 75 million gallons during 2004–05, according to The Economist. Admittedly, the US market for diesel is 60 billion gallons a year, but it is a start – and the political and economic will is moving in biofuel’s direction.
Meanwhile, diesel engine technology has improved enormously in recent years. Noxious emissions have been reduced by over 90% and, with the help of turbocharging, fuel injection, multiple valves per cylinder etc, today’s diesel engine performance is much greater than that of engines of just a few years ago.
With emissions regulations in the US and Europe getting tighter it is becoming harder to eke out the necessary improvements from traditional diesel engines. One method to reduce emissions is, of course, to reduce fuel consumption – and a good way to do that is to fit a smaller engine and share the power burden with another motive force. The initial results of Volvo’s research into this field are showing quite spectacular fuel savings – in certain construction equipment a hybrid approach is making 40–50% fuel savings a real possibility. And it is no bad compromise either – far from reduced usability, there is every indication that performance may be enhanced by adopting a hybrid policy.
Diesel deficiencies
Generally, diesel engines remain surprisingly inefficient. Despite the improvements in technology, more than 90% of the energy created is ‘wasted’ through combustion-related losses, leaving only a fraction for actual mechanical work.
Electricity-powered motors, however, lose hardly any energy in heat, noise etc, and are, therefore, a more efficient energy provider than diesel-powered combustion engines, even though the production of this electricity has obviously required some other source of energy. And although other types of compatible energy are being considered, electricity is currently by far the most popular hybrid partner for diesel engines. And it does not produce harmful emissions either, which helps diesel-electric hybrids easily meet emissions regulations.
Best of both worlds
On their own, both diesel and electricity have performance disadvantages. Diesel engine torque is minimal at low engine speeds, where much of the energy is used to merely keep itself going. In order to achieve acceptable acceleration, much bigger engines than are needed for their general work are fitted. These are heavy and use more fuel purely to operate themselves. Electricity’s failings, on the other hand, lie in the fact that the energy is stored in batteries – which are a less dense power source than diesel’s fuel tanks. This means the batteries must be larger and heavier than diesel tanks in order to achieve the same energy output – and refuelling/recharging takes a long time.
However, when these two power sources are put together both disadvantages fall away. Because an electrical motor produces maximum torque ‘at stall’ it more than makes up for diesel engine torque deficiency at standstill and low speeds. This means that a smaller, more fuel-efficient diesel engine can be used. In fact, the engine needs to be sized for just above average power – as opposed to the current situation where it is sized for peak power. And the electricity recharging/storing problem is overcome by recharging the batteries while the diesel engine is working and/or from capturing the energy from braking. Therefore, smaller batteries can be used. By working together, each power source operates at the most efficient part of its range. For diesel engines this also means operating at a point where the relative output of harmful emissions is minimized. According to Dan Benjamin, an analyst at ABI Research, hybrid systems can cut emissions by eliminating situations where NOx (nitrogen oxide) emissions are at their very worst
Although the car industry is embracing the concept of hybrid technology, it has been slow to take off in the construction equipment industry. However, with construction equipment the issue is not just about motive force but also about finding hybrid solutions to the hydraulic issues – and both these aspects need to be developed in parallel. Taken as a whole, roughly half of the fuel consumed in an excavator or wheel loader is taken up in simply moving the vehicle. The remaining 50% is spent on powering the hydraulics, moving the boom, stick, bucket etc.
Even some very large manufacturers still claim that there is no customer demand for hybrid-powered construction equipment or that it is too expensive. Others state that the required performance improvements can be achieved by fine-tuning the current diesel-only platform. However, a number of manufacturers are now embracing the concept and one of the most active of these is Volvo Construction Equipment (Volvo CE). Leveraging their position as part of the $32 billion Volvo Group, they are investing heavily in research on alternative power sources and alternative fuels, as well as in the constant refining of existing combustion technology.
Working as a team
The work Volvo is doing on its diesel-electric hybrid called for a decision on how the two ‘engines’ should work together. There are two main alternatives: series or parallel.
In a series design, the diesel engine is not directly connected to the driveline but instead powers an electrical generator. The electricity generated is fed to motors that physically drive the equipment, with any spare energy being used to recharge the batteries. When a surge of power is needed, electricity comes from both the generator and the batteries. One benefit of an electric-only power system is that electric motors work well over a wide range of speeds and, therefore, a complicated transmission is not needed. Also, because there is no mechanical link between the diesel engine and the transmission, the speed of the diesel engine generally does not change with the speed or power demands of the equipment: instead it can operate continuously at its optimum and most efficient speed. Diesel-electric trains have used this system for decades.
Parallel systems, on the other hand, connect both the electric motor and the diesel engine to the mechanical transmission, so that they work together to operate the vehicle. This is the option that Volvo have focused much of their research efforts on. The clever part of this system is the way it connects these two power sources together. A key component is the ‘I-SAM’ – or Integrated Starter, Alternator Motor. Basically, the I-SAM is a powerful starter motor with enough strength to propel even heavy construction vehicles from standstill up to a good speed for the diesel engine to take over. The I-SAM’s cleverness does not end there: when the vehicle wants to slow down, the I-SAM can be run backwards as a generator/alternator, washing off the vehicle’s speed and recovering ‘free’ energy in the process – which is then fed back to the batteries. This is called ‘regenerative braking’. The I-SAM also contains a power train management unit, which sits between the clutch and Volvo’s specially designed automatic gearbox, governing the gear-shifting strategy and the power split between diesel and electric power. Needless to say, electronics also play a significant part in governing the power-split system.
Because of the I-SAM’s ability to offer both high power and high torque at low speeds it can easily propel construction equipment from standstill, using electric-only power. And as already mentioned, because the diesel engine is not needed for this initial (peak) burst of energy, a smaller engine that is more suited to the average energy demand of the equipment can be fitted.
Moreover, having a more powerful electrical system on construction equipment has further fuel-saving benefits. Because the I-SAM is such a powerful starter motor, the diesel engine can be shut off completely when not required and rapidly spun up to its optimum speed before injecting any fuel and restarting the engine. This not only saves fuel but also reduces noise emissions, which are already lower as engine speeds do not need to rise to peak levels.
As with any new technology, there is the concern that the benefits of the system will be outweighed by new problems. But early indications from prototypes show that hybrids need no more maintenance than diesel-only construction equipment. In fact, brake wear is likely to be reduced as the I-SAM removes some of the braking duties from the service brakes.
Dawn of a new age?
The biggest fuel savings from diesel-electric hybrids in the construction industry are likely to come from those machines where there are frequent starts and stops. This is because the diesel engine will be dormant for much of the time. Machines such as wheel loaders will see big fuel savings, but all construction machinery should see benefits from this technology. There are, of course, many unanswered questions and a lot more research and testing is needed. Construction equipment is used in aggressive situations and any new technology will have to be robust enough to survive. But it is not inconceivable that in a few years’ time operators will have a graph on a monitor in their cabs informing them what power source is being used, whether the batteries are using power or consuming it and whether the diesel engine – if present – is running or off.
The big question is whether this is the right time for hybrids. Volvo CE’s president and CEO, Tony Helsham, thinks it is. He believes many contractors are actively reviewing how they can reduce their dependency on oil. ‘For a range of economic, political, environmental and health reasons, now is a good time to take hybrid technology seriously. At Volvo, we have a technology that has the realistic potential to popularize hybrid power systems for heavy vehicles,’ he said.
The Day After Tomorrow
There is no question that construction equipment is set to undergo radical changes in the coming decade. Hybrid engines are almost a certainty – but what about design? Volvo Construction Equipment have let their designers imagine the wheel loader of the future, and the Gryphin is the surprise result.
Gryphin is an extreme concept wheel loader representing the machines of the 2020s. Following the success of the SfinX excavator design study in 2004, Volvo’s designers have again turned their creative brains to imagining how wheel loaders will develop in the medium-term future.
Using an electric hybrid power source, Gryphin emits almost no emissions. Instead of heavy transmissions, drivelines and axles, Gryphin uses electrical motors inside each wheel, allowing much higher underbody ground clearance and a super-quiet machine.
Views from the driver’s seat are excellent in every direction; made possible by all-round glazing and see-through lattice pillars. The glass in the cab is intelligent: heating up in cold weather to prevent frost or condensation and becoming darker in bright sunlight.
Volvo wheel loaders have long been admired for their high breakout forces and excellent parallel lift. Gryphin brings these capabilities to a new level by introducing a solid, yet lightweight, centre boom. Not only does this improve lifting performance and reduce torsional stresses, the absence of traditional front boom linkages allows a much better view of the work area.
The lack of a traditional driveline and axles allows the adoption of intelligent independent suspension. This not only offers a more comfortable ride for the operator, with fewer vibrations in the cab, but also allows for variable ride height. The frame can be lowered for high-speed haul cycles, reducing the centre of gravity and allowing much higher speeds than are currently possible with no loss of comfort or stability. The frame can also be raised; increasing ground clearance over rough ground and offering greater dump heights while maintaining stability.
Much of the technology found on the Gryphin is already under development or even being tested, and Volvo CE say this is a very real interpretation of what will be seen at work at quarry and construction sites two decades from now.