At the Cutting Edge of Steel Production
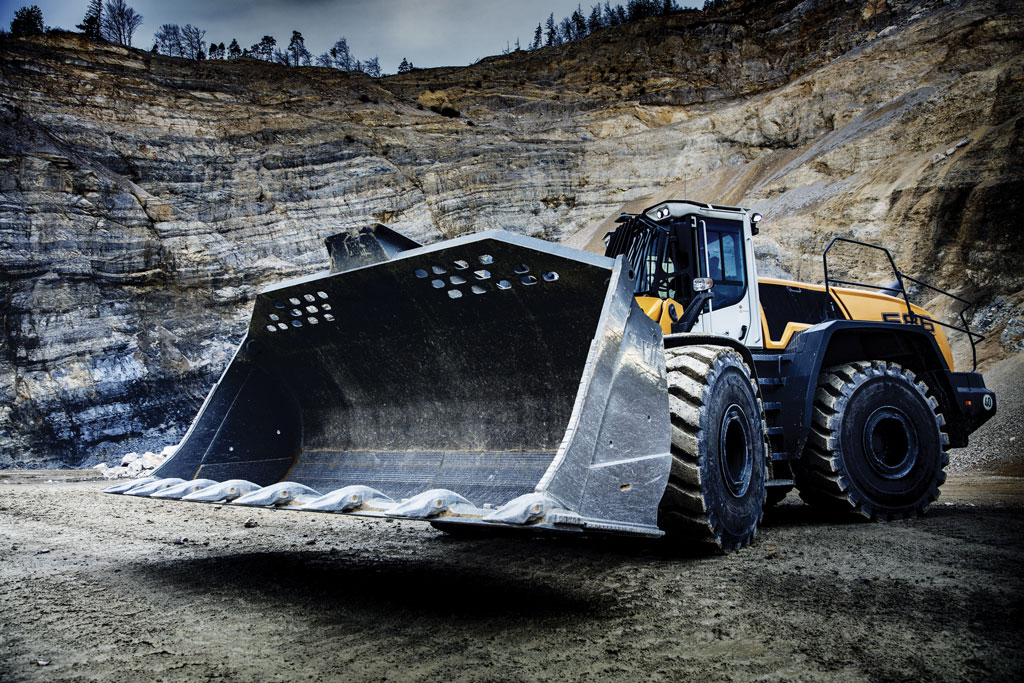
First published in the March 2019 issue of Quarry Management
QM reports on how Swedish Steel (SSAB) are cutting the carbon footprint of producing and using steel
People have been making fine steel for thousands of years. For most of that time it has been an art, passed down through the generations. The Little Mesters of Sheffield were (and in a few cases still are) past masters of making fine steel cutlery and tool and weapon blades by beating, tempering and quenching the metal. Japanese craftsmen also perfected these skills and also still make fine blades in this way.
It is an art because it is based on an appreciation of the colours of the metal while being heated, the sound of it as it is hammered, and how it is quenched.
The finest blades are made by beating and folding the metal to remove impurities and create a blade with a hard edge, so it can be sharpened and will remain sharp, with a softer backing to absorb impacts and protect the sharp edge.
Whilst in the past the results depended on the skills of the individuals making the steel, science plays a more significant role in steelmaking these days. As Jacob Sandberg, who is in charge of production and product development at Swedish Steel (SSAB) Special Steels, manufacturers of specialist steels such as Hardox, told QM: ‘Since the 1970s metals have become really deep and advanced. Most of the development in steelmaking takes place on computers.’
The holy grail of steelmaking is to achieve hardness and toughness, but the trouble is there is a trade-off between the two. Making steel harder normally means adding more carbon, which makes it more brittle and less flexible.
What the steelmakers of old were doing when they beat, heated and quenched the metal to different degrees on different parts of the blades, was creating ‘gradients’, even though they did not know it explicitly.
It is only in the past 20 years or so as our understanding of materials at the nanoscale has increased that gradients have been identified and their significance fully appreciated. The knowledge started with biology. How, for example, do a stag’s antlers manage to survive the collision force of two 200kg creatures coming together at some speed?
The answer is that the antlers consist of several layers of bone with gradients of constituent granular crystals, getting larger the further they are from the surface. A cow’s horns have a similar structure made from keratin (hair) backed by bone.
This same gradient arrangement is seen throughout the living world, making hard and resilient materials from not altogether promising materials. Human teeth have the same gradient between the dentin on the inside and the enamel on the outside.
Doing the same with much stronger materials – metals – produces correspondingly harder and far more resilient products.
But how to do it? At the University of California, Berkeley, Robert Ritchie, Professor of Engineering, achieved gradients by bombarding the surface of steel with small steel balls. This created a gradient of grain size in the metal from harder martensite to larger austenite in alternating stripes. The result: harder steel that is not brittle.
Scaling this sort of laboratory test up to industrial production is challenging. One way of doing it might be with 3D printing, and Jacob Sundberg says 3D printing is an area being explored by Swedish Steel, although he will not elaborate.
He says SSAB work closely with their customers to make life easier for them with products such as Hardox 500 Tuf, which was introduced last year (see QM November 2018). This has that desirable mixture of exceptional hardness while retaining its toughness. Combining the best properties of Hardox 450 and Hardox 500, SSAB say the result is a wear plate with no real comparison in the market.
Hardox 500 Tuf is the first 500 Brinell (HB) wear plate with properties on a par with structural steel. It delivers high strength, extreme hardness and toughness in a single wear plate. The material offers a 70–100% longer service life compared with conventional 400 HB AR steel, according to SSAB’s wear calculation software WearCalc, based on sliding wear with granite. And it has improved dent protection.
Hardox 500 Tuf can perform as a structural material in heavy-duty tipper bodies and buckets. And not only can it be used thinner, so there is less of it to move around, it is recommended for use without ribs on dumptrucks (further reducing weight) to allow it to flex rather than dent when the truck is loaded. Because it is hard and tough, it also has a low wear rate, so needs replacing less often.
In buckets, too, less steel is needed so more product can be lifted, and that means more finished product for each litre of fuel.
Savings can be significant – a dumptruck might typically carry an extra 10–20% of product, or even more in some applications. Or using Hardox 500 Tuf might mean you can use a smaller, more fuel-efficient truck.
And those savings mount up. Thomas Hörnfeldt, SSAB’s vice-president of sustainability, says 90% of the environmental impact of a dumptruck comes from its use rather than its manufacture. Likewise, replacing a Hardox 450 bucket with a Hardox 500 Tuf bucket of the same capacity would mean 700 tonnes less CO2 emissions over the lifetime of the bucket. In other words,
230,000 litres less fuel.
The performance of Hardox 500 Tuf is proven even in freezing conditions. Typical working conditions include the loading and unloading of heavy and sharp rocks in quarries and mines, and handling large and heavy recyclable materials, such as concrete with rebar dropped into tippers.
Another new SSAB product launched just last month is Duroxite 200 overlay plate for preventing severe sliding wear. With its high proportion of extremely hard multiple alloy complex carbides deposited on a mild steel backing plate, Duroxite 200 is designed to last much longer than common chromium carbide overlay (CCO) products.
It is particularly suitable for preventing sliding wear in industries such as quarrying, mining, cement and recycling where abrasive materials require extremely hard surfaces. Using Duroxite 200 instead of other CCO products in sliding wear applications results in much longer service life. Depending on the abrasive material, the relative service life can be increased three to four times and even more in some cases.
Development continues in these and other directions. In September 2018 the SmartSteel Innovation Challenge was launched as a mutual initiative from SSAB in conjunction with another Swedish steel company, Sandvik Materials Technology, and others. The idea is to use open innovation in order to find new ways to develop steel products.
The challenge attracted 26 applications. This was whittled down to seven finalists selected to pitch their ideas to an expert jury in the final round in Stockholm in December.
The jury decided on two winners: Fraunhofer Institute for Physical Measurement Techniques IPM from Germany; and Luleå University of Technology from Sweden. They came up with similar ideas, both very much in line with the SmartSteel vision. Their proposals are for using steel itself as a product identifier.
Niko Korte, head of SSAB digital business development, said: ‘These solutions are perfect examples of what we need to speed up development towards steel being part of the Internet of Things.’ In other words, the steel can report back on its own condition, increasing working life and improving working practices without the danger of a production-interrupting failure.
Another development from SSAB is an addition to the 1,100MPa range of Strenx performance steels. Strenx 1100 Plus is a new hot-rolled, high-strength strip steel that delivers outstanding welding and bending performance. And thanks to its improved weld seam strength, it contributes to lighter, stronger and more environmentally friendly lifting equipment, such as cranes, as well as lighter transportation solutions and advanced structures that require exceptional strength in the welds.
The ‘Plus’ in the product’s name refers to the practical elimination of weak weld seams, because the strength, elongation and impact toughness properties of the welded area meet the minimum guarantees of the parent material.
The optimal combination of strength and toughness of the welded and heat-affected area offers a major benefit to the design engineering process, allowing the design to be based on the same minimum static strength for the entire application, depending on the design rules.
This translates into cranes that reach higher, trailers that can carry more payload, and trucks that use less fuel and, therefore, emit less CO2. Strenx 1100 Plus is available in thicknesses of 4–8mm, widths up to 1.6m and lengths up to 13m.
Winkelbauer get tough on wear
Winkelbauer GmbH in Austria are one of the leading suppliers of heavy-duty buckets and other construction equipment for the European market. The company is an early adopter of SSAB’s new wear-resistant steel grade Hardox 500 Tuf. Upgrading to this material allows Winkelbauer’s customers to load more and extend the service life of their equipment.
Winkelbauer’s chief executive officer, Michael Winkelbauer, said: ‘We’re now telling our customers, you have two favourable options: Use Hardox 500 Tuf to make the bucket lighter, while the service life remains as long as you’re used to from a Winkelbauer bucket. Or use Hardox 500 Tuf in the same dimensions as before to get a considerably longer service life and reduced costs thanks to longer service intervals.’
By using Hardox 500 Tuf in a thinner dimension, the new generation of Winkelbauer heavy-duty bucket has 10–16% less tare weight with the same service life as the previous generation. This allows for an increase of loaded volume of 6–10% at the same total weight.
To meet one customer’s requirements, Winkelbauer designed a bucket that allows the operator to load a truck to its maximum capacity of 24 tonnes in only three passes. This saves 25% of the time required for a loading cycle.
Michael Winkelbauer is impressed not just by the quality of the new steel grade, but also by SSAB’s unwavering commitment to support and service life. ‘We would generally need a time frame of 1–2 years for a conventional test of a new material. We don’t have that time, which is why we need a partner we can trust and rely upon.
‘The depth of service that we have enjoyed from SSAB employees from the very outset is one-of-a-kind, and this level of quality cannot be found in any competing products on the market. When SSAB release a material, we know for sure it delivers as promised.’
The welding and machining of Hardox 500 Tuf can be performed with the same equipment used for other Hardox grades and bendability recommendations are similar to those for Hardox 450.
Mr Winkelbauer added: ‘Before going into production, we have naturally experimented with the material and tested it in welding. Since it’s important to reduce welding seams in order to minimize production costs and improve performance, we have analysed wear patterns and modified the design and construction of our buckets to make best possible use of the mechanical properties offered by Hardox 500 Tuf.’
Greener steel
During the triennial dealer conference at SSAB last year the steel company announced plans to replace their coke-burning blast furnaces with electrical arc furnaces, powered by renewable energy. This would cut out a number of CO2-creating processes, including the burning of fossil fuels to make coke, as well as allowing SSAB to use recycled steel alongside their newly mined ore.
The reason for the change is that the production of every tonne of steel adds 1.5 tonnes of CO2 to the atmosphere. ‘We thought we could do better,’ said Thomas Hörnfeldt, SSAB’s vice-president of sustainability.
SSAB’s production plants in Sweden, Finland and the US have an annual steel production capacity of 8.8 million tonnes. The company also has capacity to process and finish various steel products in China, Brazil and other countries. In Sweden and Finland, production is integrated into a blast furnace process. In the US, electric arc furnaces are used for a scrap-based production process.
As renewable electricity can be variable, SSAB plan to store it to ensure continuous production by using Sweden’s excess of electricity supply at certain times of the day to separate water into hydrogen and oxygen. When there is not enough renewable energy, the hydrogen and oxygen will be burnt, producing the heat to drive turbines and generate electricity. And the only residue is water.
SSAB are partnering with their electricity supplier (Vattenfall) and their iron ore supplier (LKAB) to develop this technology, which they hope eventually to be able to export to steel producers all over the world.
Thomas Hörnfeldt said transferring to renewable electricity now would increase the price of the steel, but sustainable electricity production is increasing so quickly, and the price of it falling so rapidly, that he believed the price of electricity generated from renewable energy would be comparable to current energy costs by the time the new plant is built.
SSAB, LKAB and Vattenfall have carried out a pre-feasibility study for the fossil-free steel initiative, which is being called Hybrit. Development could begin this spring. The planning and designing is expected to cost SEK20 million (£1.7 million). The Swedish Energy Agency will finance parts of the project.
The initiative could reduce Sweden’s carbon dioxide emissions by 10% and those in Finland by 7%. The reduction in Sweden has been described as being crucial if Sweden is to be able to meet the goals of the Paris Agreement.
- Subscribe to Quarry Management, the monthly journal for the mineral products industry, to read articles before they appear on Agg-Net.com