Worker Protection
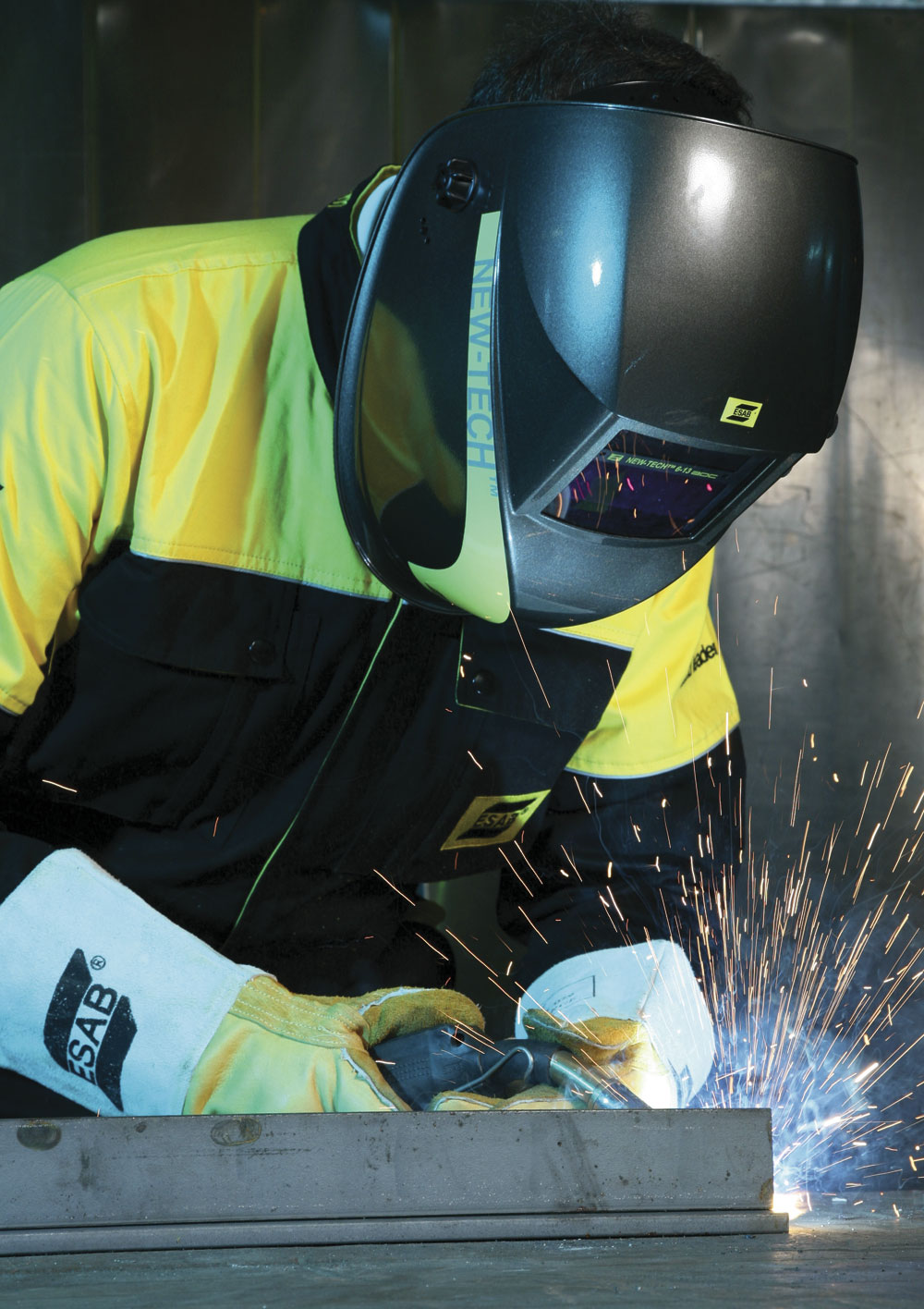
PPE – a critical element in risk management and hazard control
By Mark Homan, global PPE/welding accessories business manager, ESAB
In some industries there are hazards that simply cannot be designed out. Dust, noise and vehicle movements are inevitable in most quarries, concrete plants and asphalt production facilities. Thus, in these highly litigious days when every procedure seems to require a risk assessment, personal protective equipment (PPE) is vital when it comes to maintaining the health of the workforce and ensuring against the possibility of substantial damage to the bottom line.
But the problem does not just end there. Ear plugs are useless if they are not worn and the same goes for safety glasses and other PPE. Indeed, ear plugs may offer little or no protection even if they are worn. They have to be used correctly if they are to attenuate noise sufficiently enough to reduce hazard.
Businesses have a moral requirement to look after the health and safety of their workforce as well as the strictly legal duty. But looking after the workers can have important financial advantages too: accidents often cost more than prevention and litigation is never cheap.
It all starts with the risk assessment, a document designed to identify hazards and risks. Some of these potential pitfalls can be designed out of the process (that is the idea of doing the risk assessment in the first place), but in some cases it will come down to control of risk rather than elimination.
It may only be possible to reduce the likelihood that an accident will occur by putting in place structures or safety features that will lessen the chance that something will go wrong, or at least make the consequences less dire. If that is the case then PPE is an absolutely critical element in terms of risk assessment and hazard control.
The exact form of protection will vary from industry to industry. Most industries, if not all, have standards published by UK and international bodies. It may take time to check, but the information is there for the health and safety manager to find. These sources can play an important part in the risk assessment, which will be rendered more authoritative by reference to standards and the right type or grade of PPE with regard to site-specific circumstances, ie the actual hazards faced.
Britain and many other western countries require the provision of PPE for workers in some circumstances, but the quid pro quo and benefit from the company’s point of view is that workers are also legally required to use PPE if it has been supplied.
Some entire industries have a culture where it is clear that walking into a manufacturing plant or on to a site without appropriate PPE is a matter that will have disciplinary implications. But long-serving staff can prove to be a problem if they have been doing the same work for decades without the benefit of PPE. They may decide that they know best, an accident will never happen to them and their future health is assured.
One way to deal with this problem, and a technique that sometimes allows companies to make remarkable strides in improving health and safety, is to engage the workforce itself. Peer pressure can prove a lot more powerful than management diktat when it comes to encouraging workers to use PPE properly.
Convince a cadre of health-and-safety-aware workers that PPE will prevent unnecessary risk and a company can shift the factory floor or site perception so that the mindset of the whole workforce shifts. If it is possible to engage belief and enthusiasm, self-policing will work better than signs, strict rules and enforcement. Workers may easily be able to spot a manager in time to fit the appropriate PPE for a few seconds, but they will find it less easy to get round the spirit of the rules if other workers are watching out for non-compliance.
So-called world-class companies and those aspiring to achieve this status will have notice boards with information about the health and safety record of the site or plant. Key indicators will be shown in easy to understand formats, such as diagrams or graphs of accidents. Striving to achieve improvements in health and safety is a goal everyone can unite around.
However, companies have to supply the right type of PPE. Sometimes simply complying with the regulations is not enough. A wide range of PPE is available on the market and much of it complies with the relevant standards, although price and quality may vary.
But companies usually get what they pay for. Cheap PPE, for example ear defenders that are uncomfortable, is useless if workers decide they are not going to wear it. The same goes for eye protection, gloves, helmets and the complete array of personal protective equipment. But if there is a problem in justifying the specification of premium-price PPE, remember that there is no point in buying cheap PPE if workers are not going to use it.
Helmets are probably the most important items of safety equipment for welders. Today, most welding helmets have visors that darken automatically. Different technologies or techniques are used to achieve this effect and not everyone realizes that temperature can be a highly critical element.
The way these filters are activated means that the ambient temperature is critical when determining how quickly they work. Increase the temperature and the speed of darkening will increase. So, if a brochure or website simply quotes a switching time, that information is almost useless – a switching time at what temperature?
Some manufacturers may quote a switching time at 55°C, but fortunately most real environments rarely encounter such extremes. Cheap helmets will probably meet the requirements of EN 379, but anyone who spends all day tack or spot welding will notice the extra light that spills through the visor as a result of the longer than required switching time.
Tired workers with eye strain are much more likely to make errors and these can cost a lot more than the additional cost of specifying the right type of helmet in the first place.
Heavy helmets and those that are unequally balanced can prove to be just as big a mistake. Five minutes of lost production a day due to neck strain, headaches or discomfort adds up to 19h in a year. Cost this out at a very moderate £10 an hour and the company could be losing £190 for each worker forced to wear uncomfortable headgear.
But it is not just output that suffers. Quality can also be adversely impacted if workers have to put up with uncomfortable conditions. Skimping on PPE can be a false economy that will have a negative impact on the bottom line.
Moreover, it is not enough simply to specify the right gear, it also has to be inspected regularly and maintained properly. There is always the risk that damaged PPE will function badly and undermine an entire health and safety programme.
In the last 50 years or so there has been a dramatic improvement in health and safety in the workplace. PPE has played a vital role in making this happen.
For further information, contact ESAB on tel: (0800) 3893152; email: info@esab.co.uk; or visit: www.esab.co.uk