The HAVS and the Have-Nots
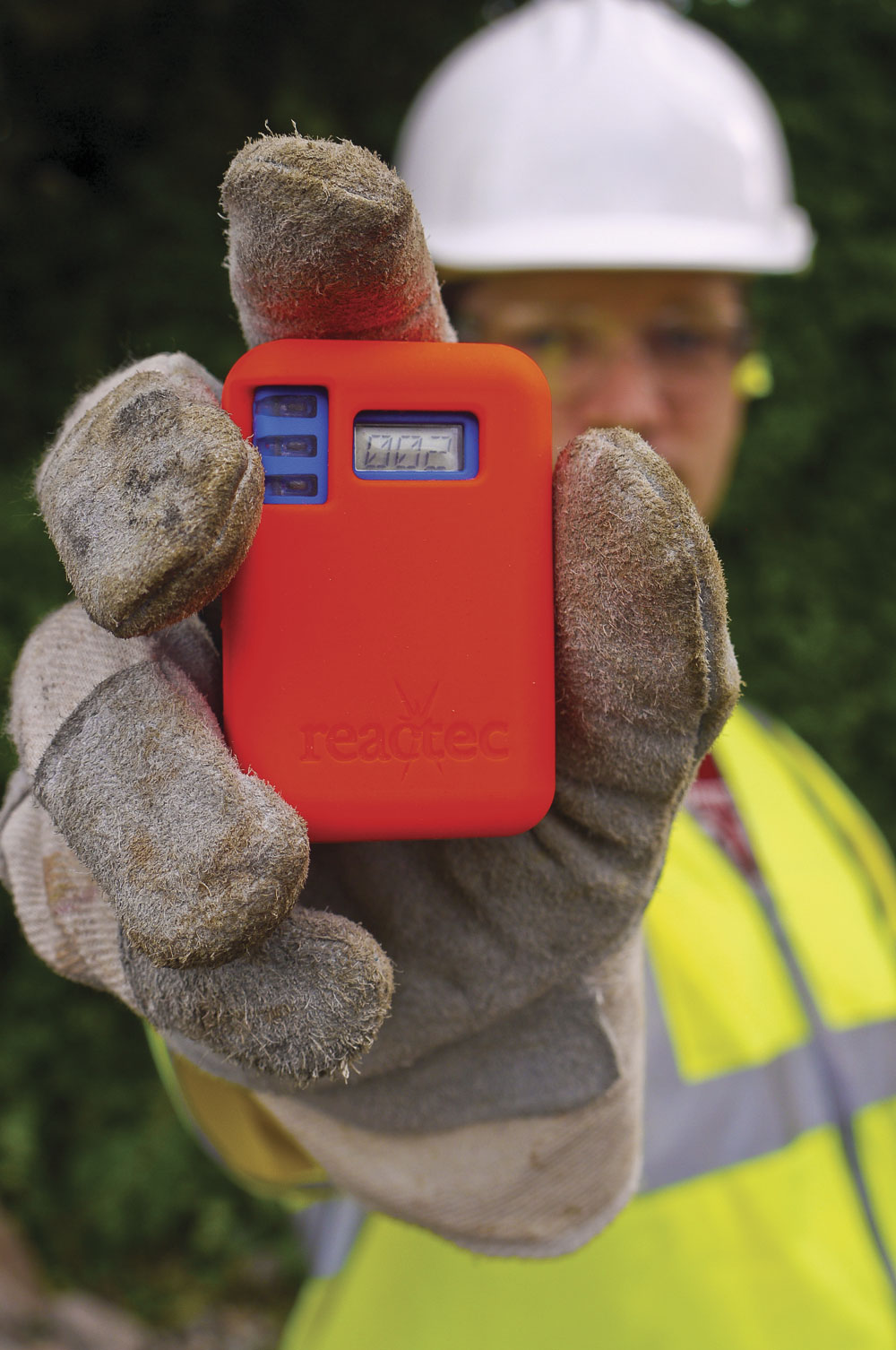
Vibration reduction experts Reactec Ltd call on companies to make a better commitment to vibration safety in the workplace
Companies should implement the most up-to-date safety measures to keep their workers safe from vibration injuries, rather than do the bare minimum to meet regulatory guidelines. This is the view of vibration reduction experts Reactec Ltd, who say many businesses throughout the UK are still choosing to simply tick boxes when it comes to meeting their safety responsibilities, rather than making a firm commitment to protect their staff from crippling injuries such as hand arm vibration syndrome (HAVS).
Under strict guidelines set out by the Health and Safety Executive (HSE), UK firms are required to keep their staff within acceptable vibration exposure limits when they use power tools or other vibrating equipment, or else face heavy fines for failing to comply with the legislation. But despite these limits, many companies simply do the minimum required to meet their targets, rather than keep their staff properly protected from harm.
The HSE’s Chief Inspector of Construction, Philip White, highlighted this issue at the recent ICE & Costain 2011 Health and Safety Lecture, where he said that companies had ‘taken their eye off the ball’ when it came to dealing with traditional health risks such as hand arm vibration.
Edinburgh-based Reactec Ltd, who produce the award-winning HAVmeter safety system, believe that using technology to continuously monitor an employee’s exposure to vibration is the only way to ensure they remain safe in the workplace – and they are urging employers to implement rigid safety systems in order to meet their corporate responsibility targets.
Jim O’Hagan, managing director of Reactec, said: ‘The HSE introduced legislation in 2005 in the form of the Control of Vibration at Work Regulations, which clearly stipulated how much vibration is acceptable in the form of Exposure Action Values (EAVs) − the daily amount of vibration exposure above which employers are required to take action. The regulations also set out acceptable Exposure Limit Values (ELVs) – the maximum amount of vibration anyone can safely be exposed to on a single day.
‘Thankfully, this legislation has already prompted some firms to take vibration management seriously, and these companies have implemented effective monitoring systems designed to measure workers’ exposure to vibration in order keep them within the safe limits.
‘However, while companies face heavy penalties for not keeping to these restrictions, many of them chose to do the basics required to keep them within the limits, rather than actually act as responsible employers.
‘The HSE’s Chief Inspector of Construction believes that companies are taking their eye off the ball when it comes to vibration safety, and he is absolutely right. HAVS is a huge risk for anyone who regularly uses vibrating tools and it can devastate lives, but far too many firms are failing to adequately protect their employees.
‘The simple fact is that continuous monitoring is far and away the best way to guarantee that your workforce is protected from injury, while also adhering to the HSE restrictions. Doing the bare minimum and ticking the boxes should not be an option; your staff should be confident that you are always putting their safety first rather than just protecting yourself from liability.’
According to Mr O’Hagan, using a continuous monitoring system such as Reactec’s HAVmeter will not only prevent the inaccuracies that arise from using a manual timesheet system, but will also save businesses time and money in the long run, as well as protecting them from costly compensation claims.
‘Manual methods of calculating vibration exposure levels have been shown to be far less reliable or accurate than an automatic system. You rely on untrustworthy timesheets and, even if your staff use a stopwatch to time their exposure, this involves a lot of wasted time and effort to do correctly,’ explained Mr O’Hagan.
‘An automatic system like the HAVmeter not only provides additional safeguards for employees’ occupational health, it also gives companies a robust and foolproof way to protect themselves against liability for injuries and avoid compensation claims.
‘With such a system, it is possible to accurately collect detailed data on who has used which tool, when it was used and for how long. The level of reporting is so comprehensive that employers are able to determine detailed data on trigger time for the actual number of tools that are being used. This data can assist in monitoring tool servicing intervals and optimizing correct tool usage in the workplace.
‘The benefits and potential costs savings in tool inventory and service costs make the business case for continuous monitoring a compelling proposition. It really is the best way to improve workplace safety, save money and ensure that a business is being as responsible as possible for its staff.’
According to Mr O’Hagan, the HAVmeter is the UK’s leading system for monitoring vibration exposure and is used by many of the country’s major quarrying and construction firms, including Aggregate Industries, Tarmac and Balfour Beatty.
Safety first for Aggregate Industries
In 1985 vibration white finger was officially listed as a prescribed condition in the UK. Now, with more than £100 million of government compensation having been paid out to victims, many firms in the quarrying and mining sector are introducing preventative solutions.
Medically known as hand arm vibration syndrome (HAVS), vibration white finger (VWF) affects tens of thousands of British workers employed across the private and public sectors. However, with some two million people exposed to the risk of VWF daily, that number is expected to rise.
HAVS is the result of over exposure to vibrating equipment and can mean painful and disabling injuries of the blood vessels, nerves, joints and muscles in the hands and arms. In extreme cases it can even lead to the loss of fingers.
In 1997, some 12 years after HAVS was recognized as a serious medical problem, the High Court awarded £127,000 to a number of coal miners in recompense for developing VWF from working with vibrating equipment.
By 2004 that sum had risen significantly with the Government reporting that it had paid out £100 million to people suffering from the VWF across Britain. As startling as these figures may be, many large private sector organizations are still not investing in VWF prevention.
However, with companies throughout the UK and Ireland wanting, and needing, to be seen as considerate employers, some are now investing in new preventative technology to safeguard their employees, including Aggregate Industries, who have started using HAVmeters at some of their key UK sites.
For example, for the last 18 months HAVmeter safety devices have been used by employees at the Aggregate Industries’ Waddington Fell Quarry, near Clitheroe, Lancashire, a dimensional stone and sand quarry where production and maintenance staff use multiple power tools on a day-to-day basis. Use of the HAVmeter system is helping to ensure that the workers are able to monitor vibration levels to keep themselves protected from injury.
Gordon Dick, manager of Waddington Fell Quarry, said it had been an all-round positive experience since the introduction of the HAVmeter system. ‘We have become increasingly aware of the issues of HAVS on site over the last few years and are aware of the risks to both our maintenance and production staff,’ he commented. ‘Most quarries across the UK will be using exactly the same power tools and exposing their operators to the same level of hand arm vibration risk.
‘After starting a paper-based system to monitor vibration levels a few years ago, it was clear that this system wasn’t going to work, with time being wasted and results not always being accurate. We have been using the HAVmeter for more than 18 months now and already we have seen big changes. Not only are we ensuring the safety of our valued workers, but we have seen up to a 25% reduction in vibration point values.
‘The introduction of HAVmeters into our workforce has meant that we have taken a massive step forward in terms of the time savings we have made. There has been nothing but positive feedback from our employees; the HAVmeters are extremely easy to use and many of them feel the device has made their working life easier.’
The HAVmeter system allows workers using vibrating tools to easily and accurately monitor their exposure levels to hand arm vibration. At the beginning of each shift, the worker signs out a HAVmeter from a base station using his or her own personalized card, which is programmed with the levels of exposure they should work within. They then attach the device to every tool that they use during their shift. The HAVmeter provides a constant readout of exposure level and flashes a warning to the worker when his or her exposure limits are reached.
While HSE regulations require employers to take responsibility to monitor time spent using vibrating machinery, until the arrival of this device there was no reliable solution to ensure workers’ time spent exposed to vibration levels was 100% accurate. The HAVmeter allows both employee and employer to know exactly who has been doing what and when, building up a complete and detailed record of tool usage and HSE exposure points for each employee every day.
Once these data have been uploaded into Toolminder software, a comprehensive set of standard and custom reports can be created to show workers a full breakdown of their exposure to vibration levels and which management and occupational healthcare staff can use to manage each employee’s healthcare plan. The reports are complete, accurate and unambiguous – providing the most comprehensive information about exposure to hand arm vibration levels in the workplace.
For further information about the HAVmeter visit: www.reactec.com/havmeter