Silo Dust Control
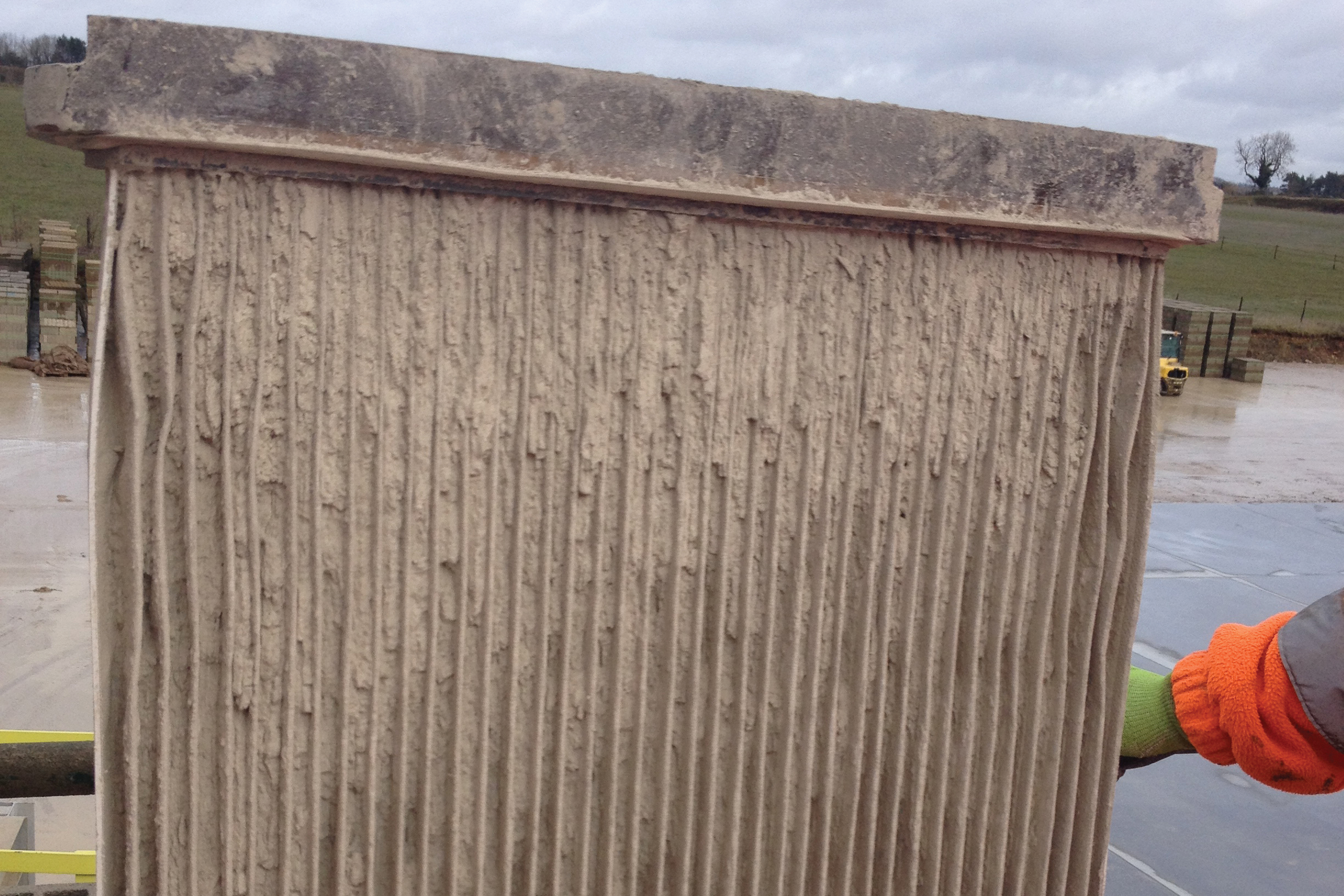
First published in the December 2017 issue of Quarry Management
Maximizing dust filtration efficiency with new technology
Particle filters are an essential component in any powder storage silo, providing safe ventilation of air without expelling product into the atmosphere. However, this process inevitably leads to product being engrained in the filters, leading to loss of efficiency and potentially more serious consequences. Here, Hycontrol look at the problems associated with filter degradation and outline how the latest advances in filter technology allow for increased efficiency.
The storage of powdered product in silos is commonplace in a wide range of processes in diverse industries. However, there are important safety considerations associated with the operation of storage silos, particularly during the pneumatic filling process when excess pressure can become trapped within the silo. The dangers posed by the over-pressurization of silos can include serious injury or even death, and should not be taken lightly. Damage to equipment will also result in financial loss and production downtime.
The purpose of a silo-protection system is to negate the risks of over-filling or over-pressurization when powdered material is transferred from a road tanker to a silo. Guidance on minimum requirements for acceptable silo safety equipment is available from organizations such as Defra and the Mineral Product Association (MPA). The MPA guidance lists essential components for safety systems, including:
- A sufficiently sized pressure-relief valve (PRV)
- A pressure sensor and alarm system
- Level-monitoring equipment
- An efficient air-filtration system.
Filter units
Filter housings mounted at the top of silos are designed to vent air blown in during filling, whilst preventing dust particles from escaping into the atmosphere. Designs vary, but modern systems are usually based on filtration using either bag filters or cartridge filters that utilize porous media to trap the dust particles. As the replaceable filter media becomes engrained with dust and filtration efficiency drops, users should be able to easily remove them to insert fresh filters.
Normally, filter housings are fitted with some form of self-cleaning system, typically mechanical shakers or reverse-jet systems that blow dust back out of the filters and into the silo with a burst of compressed air. Of the two, air-jet systems are generally regarded as more modern and efficient. Filter units without self-cleaning systems (referred to as static units) are still seen occasionally, but current guidance advises against their use.
Filter problems on the silo top
Faulty operation of filter units can stem from a range of issues, including blockages, failure of the cleaning system and the fitting of unsuitable or wrongly sized filters.
It is to be expected that, over time and with the regular filling and emptying of contents from the silo, the filter media will become engrained with more and more powdered product, which, eventually, the cleaning system will be unable to remove. Although filter manufacturers give recommended check routines and filter replacement schedules, evidence from the field indicates that these guidelines are often ignored. In some instances cartridges in larger or taller filter units are very difficult to access without the use of scaffolding and personal safety gear. As a result, these cartridges are left to operate long after they lose filtration efficiency. However, it is often not just inaccessible filters that are given scant regard when it comes to maintenance, as filters at more readily accessible heights regularly suffer similar levels of neglect.
As mentioned, most modern filtration cleaning systems rely on reverse-pulse air-jet systems to clean dust from cartridges using short, powerful blasts of air. This requires a reliable supply of compressed air to the silo top. Loss of airflow will drastically reduce the effectiveness of the cleaning system, leading to rapid product build-up.
Insufficiently sized filter units (frequently found on older silos) are problematic because even if the filter media is well maintained, the filter may not be able to vent sufficient volumes of air quickly enough to adequately relieve increasing pressure in the vessel during filling, which can be extremely dangerous.
Blocked filters are a common contributor to silo-protection problems. If dusty air cannot be cleaned and escape through the filters, it will blow out through the pressure-relief valve. This poses a significant risk as powders carried in the airflow will form hard compounds when mixed with atmospheric moisture, leading to the PRV becoming blocked with hardened product over time. This problem becomes acute during the filling process if increasing air pressure inside the silo cannot be safely vented. In the past, this has led to silos rupturing or the filter unit being ejected from the silo roof. The consequences of such an incident could include serious or even fatal injury to workers or the public, catastrophic silo damage, loss of material and production, and harmful environmental pollution, plus damage to the company’s reputation and significant health and safety fines.
Can velocity
It can be seen, therefore, that efficient, well-maintained filtration units are an important factor in ensuring silo safety. Key to ensuring reliable filtration is the velocity of airflow within the filter unit casing between the cartridges. This is referred to as the ‘can velocity’.
Can velocity is a fine balance; it must be consistent along the full length of the filter at a sufficient strength to allow the dust dislodged during pulse cleaning to escape from the cartridge surface and fall away into the vessel below. If the velocity is too low, the loss of pressure towards the bottom of the filter cartridges (furthest from the air jet nozzles) will not be enough to dislodge the dust particles resting in the filter. If the velocity is too high, dislodged dust will be re-entrained in the airflow and re-deposited on the cartridges – or will simply be blasted from one filter cartridge into its neighbour. Congested filters mean reduced performance, ultimately risking complete blockage.
Improving the design
The latest advances in filter technology, utilized in Hycontrol’s Hyvent unit, allow for greatly increased airflow within the vent unit while simultaneously reducing air velocity from below. This has been achieved by changing to a conical filter shape, as opposed to the old-style cylindrical cartridges.
The advantages of this new design are three-fold. First, by greatly increasing the space for free air flow from below, the can velocities are reduced. Lower velocities of circulating air make it easier for dust particles to drop out of suspension back into the vessel below, thereby reducing re-entrainment in the airflow to the cartridges. Figure 1 illustrates the increased space above the filter inlet point as a result of the tapered filter design. This means that 82% of the area at the inlet chamber of the filter unit is free (as shown in the bottom half of the illustration) as opposed to typically 59% when using cylindrical elements. The result is lower upward air velocities at this point, increasing dust separation.
Secondly, the increased space between the filters reduces the likelihood of dust being passed to neighbouring cartridges, particularly when the airborne dust is moving at a lower velocity. This will help quicken the rate at which the dust drops out of the filter. The less dust that is retained circulating in the filter unit, the less dust that will become re-engrained in the filter media, resulting in better performance and a longer lifespan for the filter cartridges.
Finally, the design results in greater cleaning efficiency by the compressed-air jet. Figure 2 shows the flow of compressed air into the cartridge and the reduction in dust expulsion resulting from decreasing air pressure. Traditional cartridge filters (shown on the left) suffer from reduced airflow towards the bottom as pressure is lost.
Conical filters (shown on the right) offer an improvement by evenly distributing pressure down through the cartridge, thereby maximizing product removal. The tapering of the inner core of the filter elements enhances the effectiveness of the compressed-air jet, giving a more even clean over the length of the cartridge. Collectively, these features mean the new-style filters have a longer functional life and offer a greater consistency of performance.
Conclusion
A modern, high-efficiency filter unit should fulfil several criteria:
- Easy access to filter cartridges for maintenance and replacement
- Correctly calculated size to deal with the maximum volume of airflow
- Efficient self-cleaning system (ideally reverse-pulse air jets firing down into the filters)
- Latest enhanced filter cartridge design to ensure optimum performance.
Advances in filter technology are greatly improving both the lifespan and the performance of silo filtration systems. However, even the most efficient self-cleaning unit will require regular, scheduled maintenance to ensure continued optimum performance. As mentioned in the introduction, filters should also be considered as an essential part of an integrated system to monitor for and prevent over-pressurization in silos. Indeed, a testable protection system that monitors and records high-pressure events during filling operations will also assist preventative maintenance for the filters, as regular occurrences may indicate issues with airflow through the unit. The complete silo-protection system, including the filter, should be inspected and the functionality of the components physically checked on a regular basis – it is not sufficient to merely visually inspect and dust-down equipment. Hycontrol recommend thorough service assessments every 6–12 months, depending on the frequency of filling. For more information visit: www.hycontrol.com
- Subscribe to Quarry Management, the monthly journal for the mineral products industry, to read articles before they appear on Agg-Net.com