Reinforcing The Commitment To Health And Safety
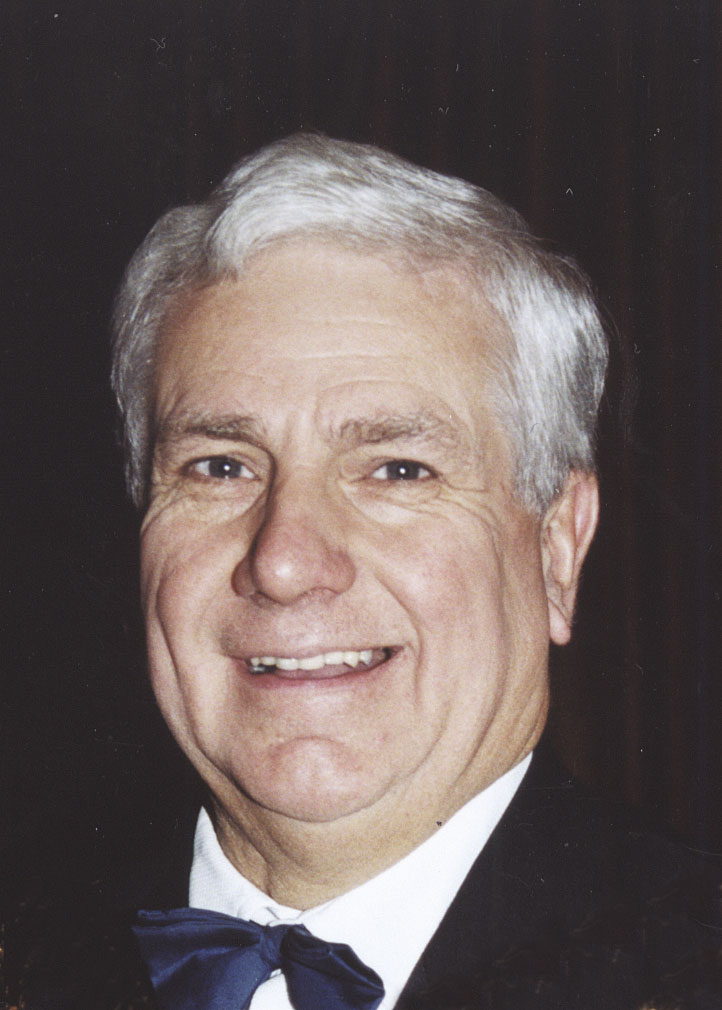
With more and more companies already considering health and safety at board level, Phil Shirley talks to Foster Yeoman’s newly appointed chairman, David Tidmarsh, about the importance of corporate responsibility as a key driver of positive change for the UK quarrying industry.
A number of factors are currently having a significant impact on the UK quarrying industry, including the Working Time Directive, the cost of plant fuel, the cost of road transport and the aggregates levy. In total, these problem issues represent arguably the worst kind of risk to the UK quarry products market — susceptibly to import substitution.
The growing risk posed by health and safety (or more to the point, the lack of it), however, is of equal if not greater concern, which is why the largest independent quarrying company in Europe has set an unprecedented target of reducing its reportable accidents by 50% year on year for the next five years. If successful, Foster Yeoman will reduce their reportable accidents to just one a year by 2010.
That however would still be one accident too many for David Tidmarsh, who as the newly appointed chairman of Foster Yeoman is determined to take health and safety performance into a new dimension. ‘I have had an increasing interest and focus on safety in the last eight or nine years of my life,’ says Mr Tidmarsh, ‘and now it’s time to reinforce that commitment by helping Foster Yeoman become a leader in health and safety performance.
‘Of course, I am being driven by changes in legislation, but also by a strong belief that, as an employer, I have to have a more responsible attitude to the inherent risks our people are exposed to. Our philosophy is simple –– if it’s not safe don’t do it, we don’t want you to do it and we don’t expect you to do it.’
Foster Yeoman recently reinforced their commitment to health and safety by implementing a new health and safety policy, which is driven by a behavioural approach to safety management. To develop the new policy the company enlisted the support of safety guru Peter McKee, a former DuPont man.
DuPont Safety Resources were founded over 30 years ago to build upon the top-class safety principles and best practices employed throughout DuPont, and to partner with client organizations to assist in their efforts to achieve similarly excellent safety performance.
The UK mining, quarrying and building products industry was notorious for its poor safety record. In June 2000 the Quarries National Joint Advisory Committee adopted the Hard Target of halving the number of accidents in the industry by 2005. The initiative has so far resulted in the injury rate being reduced by 46% (2000–2004). The next stage (2005–2010) will be to achieve a further 50% reduction in injuries, with the ultimate aim of zero incidents by 2015. Even so, further improvements have to be made above and beyond the classic safety approach (managing vehicle movement, slips, trips and falls, housekeeping, equipment safety etc).
According to Mr Tidmarsh, one aspect that has not been addressed fully is that of the behavioural approach to safety management –– establishing why people perceive, react and respond in the way they do. ‘Instead of having process health and safety we are focusing on people’s behaviour,’ he says. ‘Approximately 96% of accidents are caused by behaviour rather than an item of plant or equipment failing. If people focus on the process alone they are actually only focusing on 4% of the problem.’
Managing people to behave safely is a major challenge in this particular industrial sector. There may be policies and procedures in place, but often a subconscious mindset prevails of: ‘do whatever it takes to get the job done quickly and profitably’. This may lead to proper and effective safety considerations being pushed down the priority scale.
A cornerstone of the DuPont safety philosophy, and therefore the bedrock of any safety consultancy program, is that all injuries and accidents at work are preventable, particularly within a culture of behavioral change where absolute commitment from the top level is evident because the executives and managers lead by example.
David Tidmarsh calls it ‘visible felt leadership’. ‘Directors and managers must be visible and their enthusiasm for safety must be felt by everyone,’ he says. ‘How do you achieve this? First, you need a commitment from directors and senior managers that they are going to change and that they are going to focus on people and not on the process. This is now happening at Foster Yeoman.
‘We already have a very good bureaucratic process-orientated safety system, but it fails to deal with the 96% of accidents that are caused by people. This is why we must change. The quarrying industry’s record used to be poor but it has improved significantly over the past few years and I would expect this improvement to continue because I now believe that the industry is much more focused on the people issues rather than the process issues.’
Unfortunately, however, the quarrying industry, like its close relative the construction industry, is an inherently macho industry. ‘People want to break records, beat deadlines, build things more quickly and push the boundaries of possibility,’ explains Mr Tidmarsh. ‘The inevitable problem with this is that people take short cuts and it is when they take short cuts that they become unsafe.
‘And incidents can cause lost production. I once had a quarry where there was a serious injury and the HSE shut the site for 10 days. We were unable to supply our customers for 10 days all for the sake of somebody taking a short cut, so I am not convinced that there is an argument that says taking short cuts benefits either the company or the customer.’
Mr Tidmarsh obviously has a point, although if a company is working to tight deadlines, faced with the risk of penalties and saddled with low profit margins, then, sometimes, short cuts do pay off. There is no denying the fact that, at some point, whether processing aggregate or building a skyscraper, health and safety is compromised by financial needs.
Of course, a proactive health and safety strategy can improve overall performance
and reduce costs. There is absolutely no doubt about this and there is a direct link to housekeeping. ‘Part of the process of improving safety is to improve housekeeping,’ explains Mr Tidmarsh, ‘because untidy sites are virtually always less-safe sites.
‘Safety must be integrated as a core business and personal value, recognizing not only that good safety is good business, but that it is important for each member of the business to have a personal value for their own safety and the safety of the people they work with. It is our people who provide the solutions to our safety problems. They are the one essential ingredient in the recipe for a safe workplace.
‘They contribute to the overall success of Foster Yeoman. By demonstrating a real concern for each employee, however, leadership helps establish a mutual respect, and the foundation is laid for a solid safety effort.’