On Higher Ground
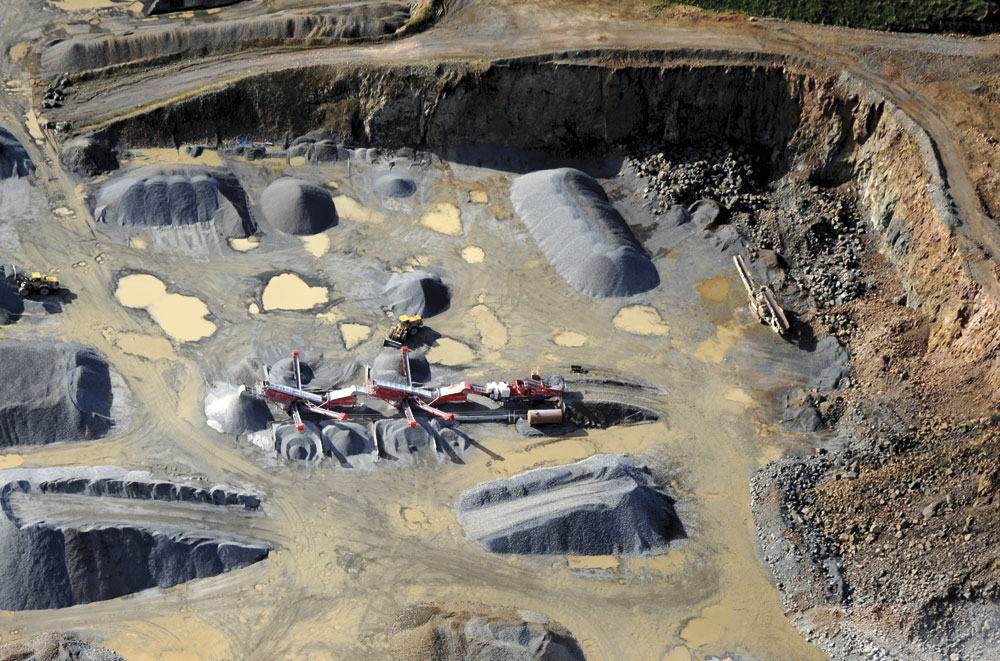
An efficient low-cost solution from Barr Quarries helps deliver improved health, safety and environmental performance at Tincornhill
Improving workplace health and safety is without question the highest priority for any quarry operator. Since the launch of the Hard Target Initiative in 2000, the mineral products industry has successfully achieved a 55% reduction in accidents (up to the year 2006/07) and is now looking forward to Target Zero, which aims to achieve zero reportable accidents by 2015.
Indeed, these are challenging times for the wider quarrying industry, as companies not only have to find ways of driving down accident and injury rates across their sites, but also equally importantly, have to tackle key issues such as sustainability, carbon reduction and training and recruitment. With the quarrying sector becoming an increasingly competitive marketplace, businesses have to be able to compete effectively and efficiently, and for many being eco-conscious has now become an integral part of everyday working practice.
Barr Quarries, for example, have demonstrated that good sustainable practice can help a company reduce production costs, improve its overall performance and, more significantly, ensure the quarrying workplace is a much safer environment for its employees.
As part of a major investment programme to improve operations across its sites, the company has designed, constructed and commissioned a raised crushing and screening platform for use at Tincornhill Quarry, at Sorn, in East Ayrshire.
With an operational lifetime of around 25 years remaining, the quarry is one of Barr’s flagship sites, producing in excess of 200,000 tonnes of high-quality aggregates for a number of local concrete and coating plants they operate. The business fully understands the importance of offering its customers quality products and over the last few years has invested greatly in the improvement of its mobile crushing and screening operations at Tincornhill Quarry.
Recent additions to the fleet include: a Sandvik UJ440i mobile jaw crusher; a Sandvik UH440i mobile cone crusher; a Terex Pegson 1300 Maxtrak mobile cone crusher; and Terex Finlay 694 and 683 mobile screens.
‘Since the corporate investment programme began, we have seen a significant improvement in the quality of materials being processed at Tincornhill,’ said Gordon Hynd, production manager for Barr Quarries. ‘However, we still managed to identify further areas of concern and safety issues that needed to be addressed.’
Andrew Gillon, engineering manager for Barr Quarries, added: ‘The idea of having the raised island at Tincornhill actually stemmed from our regular site safety meetings. We had discussed a number of potential problems associated with the use of mobile crushers and screens. For example, loading out the aggregates caused excess stockpile material to develop around the plant, which created access difficulties to certain areas during routine maintenance procedures. This also increased plant downtime time for staff cleaning around the plant area, impacting on the general productivity of the equipment. Additionally, there was the risk of cross contamination of stockpiles, which has now been removed with central dividers being added to the plan.’
Another common safety hazard during routine maintenance operations was the demarcation between wheeled plant and pedestrians, thus increasing the risk of vehicle-pedestrian collision.
‘Having carefully identified the ongoing issues at the site through consultation with quarry manager Brian McClelland and his team, we needed to develop a system that offered improved production and operational flexibility, while strengthening our site environmental and health and safety commitment,’ explained Mr Gillon. ‘We came up with the solution to raise the mobile processing plant on to a drier and much cleaner environment, which would segregate equipment, personnel and aggregates on site.’
The installation of the raised platform was approved by the Barr senior management team, as the development was seen as the most economical and effective solution to counter the operational issues and health and safety problems at Tincornhill. The timescale for the project was also a critical factor; the whole installation process took three days to complete, allowing the quarry to operate as normal with no expensive shutdown costs or major loss in production.
The plan involved recycling old excess precast units at a stockyard operated by sister company Solway Precast. The island design was to use old L-shaped seating sections as precast concrete panels to construct the support walls for the 48m long raised platform and to provide individual stocking area dividers under each conveyor.
Once the concrete pedestals were erected and backfilled with scalpings, handrails and steps were fitted to mark the controlled access points to the plant working area, as well as to segregate both the operational staff and maintenance team from the earthmoving plant.
It was imperative for Barr to employ a system that could be moved and repositioned nearer the working area of the quarry. With the precast panels being freestanding, the platform can be moved as the quarry develops, eliminating any mobility issues in the long-term development plan. Quarry manager Brian McClelland commented: ‘We foresee this operation on a bi-annual basis as the quarry expands.’
Since installation, crushing and screening operations at Tincornhill have improved markedly and Mr Gillon and Mr Hynd are delighted with the benefits of the low-cost bespoke solution.
‘The raised platform has ticked every box on our agenda,’ said Mr Hynd. ‘It has improved productivity efficiency by around 10%, thanks to reduced maintenance and cleaning activities, which, in turn, is saving us time and money. We have also addressed the issue of dust control, with an improved dust-suppression system that is more suited for use in a semi-permanent working position.’
Echoing Mr Hynd’s sentiments, Mr Gillon commented: ‘The most visible benefits are how clean, safe and organized the working environment is at Tincornhill. As the island is raised, the potential to be affected by adverse weather is reduced, lowering the risk of slips, trips and falls associated with water and freezing. If required, the Sandvik UH440i cone crusher and two Finlay 694 mobile screens can be tracked off the platform to allow mechanical cleaning of spillage, eliminating the risk of manual removal.’
Barr’s success story has not gone unnoticed in the quarrying industry. At last year’s MPA Health & Safety Best Practice Awards, the company was awarded a ‘highly commended’ certificate by the judging panel for its raised crushing and screening platform at Tincornhill Quarry.
While this innovative sustainable solution may not be suitable for use in every quarry, it does offer operators, who find themselves in dealing with safety and environmental problems, a cost-effective option to mitigate the impact on their normal business operations.
According to Mr Gillon, several quarry firms have already enquired about the raised platform. ‘Recently, I was asked by a health and safety conscious operator to calculate the overall cost and time of the project,’ he explained. ‘With such interest shown, we’re more than happy to share and spread this best working practice as far and wide as possible across the industry. At the end of the day, we have a duty to make the quarrying workplace safer and to encourage other businesses to follow suit.’
Acknowledgement
The editor wishes to thank Barr Quarries for permission to visit Tincornhill Quarry and, in particular, Gordon Hynd, production manager, and Andrew Gillon, engineering manager, for their help in preparing this article.