Maintaining Silo Safety Equipment
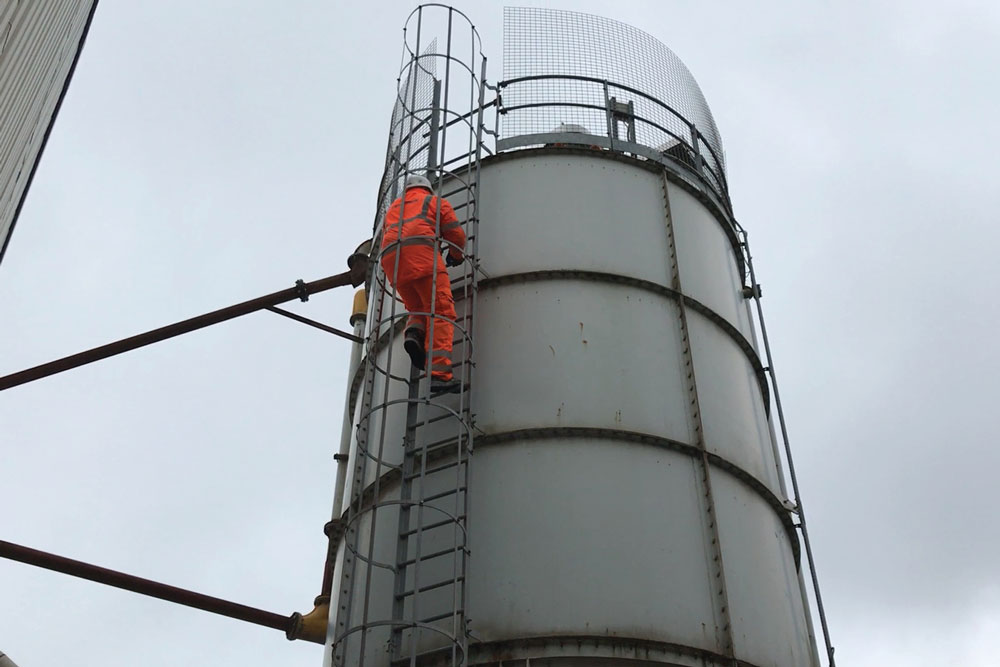
First published in the May 2018 issue of Quarry Management as Ground Control
David Wadsworth, UK sales manager at Hycontrol, discusses the health and safety issues in maintaining silo safety equipment at height and puts the case for ground-level testing
The maintenance of safety equipment mounted at the top of silos presents a Catch-22 situation for site managers: it is dangerous to send staff up there to check things are in good working order, putting them at risk of falling, and it is unquestionably dangerous to not send them up and, as a result, neglect vital safety equipment. With increasingly stringent health and safety legislation to consider with regard to working at height, and stiff penalties levied in the case of accidents caused by negligence, it is essential that management and staff are aware of the risks as well as the best-practice solutions when it comes to maintaining silo safety equipment at height.
Silo-top equipment means working-at-height risks
Silos for the storage of powdered products are commonplace in a wide range of industries, including cement and quarrying. These vessels can be up to 50m (164ft) or more in height and require a number of essential safety devices to be mounted on top, such as the pressure-relief valve (PRV), pressure sensor, high-level alarm and the air-venting dust-filtration unit. Together, these pieces of safety equipment form the basis of a silo-protection system.
These systems may vary somewhat in design, but as highlighted in best-practice guidance from the Mineral Products Association (MPA), all the above-listed items are essential for maintaining site safety due to the risks posed by over-pressurizing or overfilling silos. Indeed, recent incidents at sites around the world have highlighted just how important this is.
Whilst this equipment is essential for site safety, mounting it at height creates a whole new set of problems. Safety equipment is only ever as good as the last time it was tested, and best-practice guidelines state that silo pressure safety equipment must be tested prior to every pneumatic filling operation, which has often required a member of staff to climb the silo to manually test the equipment, regardless of weather conditions or visibility. It is plain to see how this creates additional risk.
Slips, trips and falls continue to pose significant workplace safety issues. Should they take place at height, the danger is even more significant. Statistics from the Health and Safety Executive (HSE) show that, in the UK, falls from height accounted for 29% of all fatal injuries in the workplace, with 39 fatalities and 6,521 injuries in the year 2013–2014 alone. Silos are a classic example of the dangers of working at height: besides the sheer height and difficulties of accessing the silo top, they are usually outdoors, which puts workers at risk from slippery surfaces, high winds, harsh weather and a range of other dangers.
Additionally, the ageing workforce further complicates matters – according to a 2015 report from the Chartered Institute of Personnel and Development, approximately 35% of workers in the UK’s mining/quarrying sector and 33% of workers in the construction industry are aged 50 or older.
Rescue plans and risk assessments
Whilst older workers are likely to be more at risk of health complications arising while on site, the fact is that workers of any age are at risk when required to work in difficult-to-access locations such silo tops. Managers are required to consider any potential hazards that may arise when workers are climbing up, on top of, or down a silo. Thorough risk assessments are essential and must consider the condition of ladders, guardrails and cages, as well as the integrity of the silo roof. But there are many other risks that should also be looked at.
For example: what will happen if a worker falls and is injured while working at height? Or, what will happen if a worker suffers a heart attack, heat stroke or a sprained ankle while on top of a silo? These potential problems must be considered. There is clear guidance stating that all sites must have a rescue plan in place for safely bringing stricken personnel down, which must be carried out by personnel on site. Employers should not rely on calling for external assistance, as injured or sick staff members will require immediate help. Any delay may prove critical to their health.
The HSE states that all sites should have appropriate rescue equipment readily available and that staff should be competently trained to use it. Assessments should be made to ascertain the most appropriate form of high-level rescue equipment. As with all safety equipment, this will need to be checked and tested on a regular basis, as appropriate. The site rescue plan should also be regularly assessed and updated as necessary. This plan must consider a wide range of factors, not least the safety of the workers carrying out the rescue procedure.
HSE guidance also strongly advises against allowing anyone lacking the necessary skills to carry out work at height. This is an important servicing consideration – do the people being sent to the silo top actually know what they are doing when they get there? Will they be able to fully test the silo-top equipment and verify its functionality, or will they only be able to visually inspect the equipment and clean it? It is also unlikely that supervisory staff will want to climb the silo to check the quality of maintenance.
It is no surprise, therefore, that site staff are often averse to the idea of climbing silos for a great variety of reasons. The fact that working-at-height risks are so commonplace underscores the notion that it is preferable to minimize the need to climb silos in the first place.
Eliminating climbing risk with ground-level testing
Historically, the impracticability of testing equipment at height – or, in the case of the pressure sensor and PRV, of having to physically remove them from the silo for a workbench test – has meant that maintenance has been neglected. This, of course, generates further risk: eg from sensors developing faults, or PRVs and filters becoming blocked.
So, how can the risks posed by climbing silos be reduced whilst maintaining a safe equipment-testing regime? The answer is to utilize equipment that features a ground-level test (GLT) facility, such as Hycontrol’s new SHIELD silo-protection system.
The idea behind GLT is simple and self-explanatory: it gives the user the ability to test the functionality of equipment mounted on the silo-top with both feet safely on the ground. With the Hycontrol system there is a single push-button or key test on the control panel, which is usually located at the fill point. With a single action, all key components are checked, with a light and siren indicating the outcome of the test. Whilst wiring and power tests (lamp tests) have been commonplace for many years, the ability to remotely test the functionality of an entire level safety system was only firmly established in the early 2000s, when Hycontrol’s close collaboration with the Refined Bitumen Association, to improve safety standards in the bitumen industry, highlighted the need for testability from the fill point before each tanker discharge. The utilization of dependably testable equipment, along with improvements in procedures and panel display equipment, helped to drastically reduce spillage rates. This concept was then applied to pressure safety systems for powder silos.
A wide variety of pressure safety systems offering varying degrees of testability are available on the market, and Hycontrol advise users to consider the importance of being able to reliably test all key components regularly when considering their silo-protection options.
As part of Hycontrol’s new integrated SHIELD silo-protection system, the GLT function allows site operators to fully test vital safety equipment and guarantee that all components of are working properly before each and every delivery takes place. The system is linked to a normally closed valve that will not permit a fill to take place until a test has been performed.
The Hycontrol GLT system is said to be unique in that it tests the operation of the pressure sensor, level sensor and PRV, as well as checking that the compressed-air supply to the filter self-cleaning mechanism is on. Because this is an integrated test, the cycle is initiated by a single push of the button on the fill-point panel and is completed in a six-second time frame – much faster than the two or more hours it would take to remove silo-top equipment for a bench test.
Conclusion
A system that can test all of the key safety components on top of the silo will reduce maintenance levels significantly and provide a safer working environment for site operators. As well as eliminating the need to regularly climb the silo, site staff can be confident that filters are not at risk from blinding and pressure build-up, product is safe from overfilling wastage, and pollution risks are being negated. Ground-level testing should not be the limit of a silo-protection system’s activity; monitoring and reacting to pressure during the filling procedure is essential, as well as controlling alarm functions and recording pressure and level events for maintenance purposes. Above all, site operators must remember that in order to ensure their safety system is fully operational, it must be regularly tested.
- Subscribe to Quarry Management, the monthly journal for the mineral products industry, to read articles before they appear on Agg-Net.com