Lafarge Aggregates’ Journey To Zero Harm
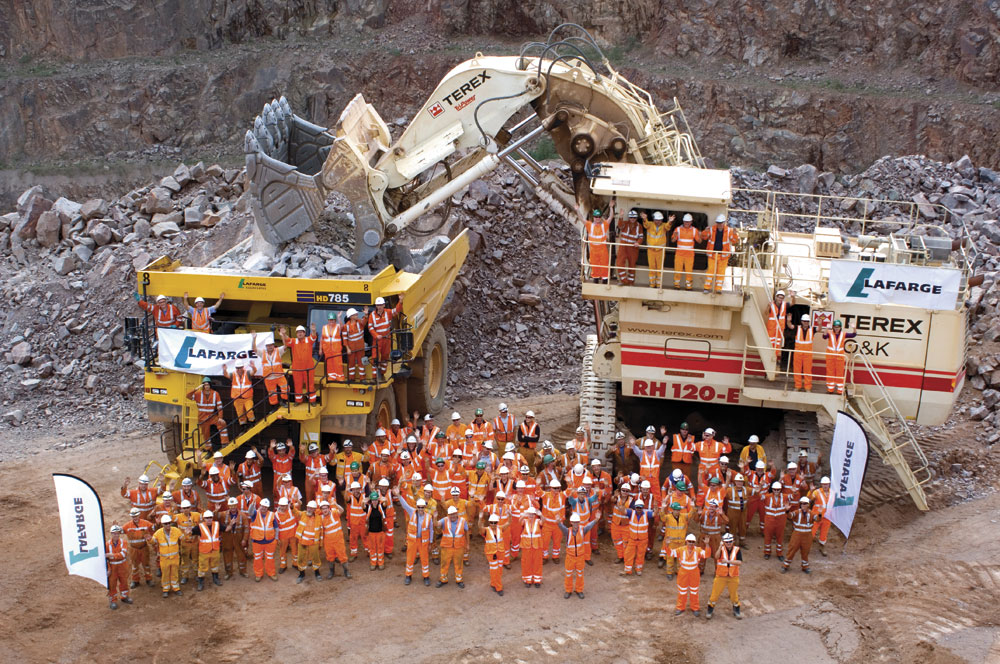
Working to achieve a significant reduction in lost-time incidents
By Ian Brown, national production manager, Lafarge Aggregates Ltd
This paper has been written on behalf of all the employees at Lafarge Aggregates Ltd who have worked together to achieve a 97% reduction in lost-time incidents (LTIs). This is an achievement that most people thought could not be done, but from 2003 to 2011 Lafarge in the UK have reduced their rate of LTIs from more than one a week to around one or two a year.
The author has been employed in the quarrying industry with Redland and Lafarge since 1982 working as a production manager at various levels and in different parts of the world. In the early 1980s quarrying was potentially very dangerous and accidents occurred far too often. Managers were trained in incident investigation and told that ‘people getting hurt or killed in quarries were common, it’s a tough place to work and incidents just happen’. In a typical quarry at that time the working face was often more than 30m high, edge protection was almost non-existent, fly-rock was not unusual, and crusher drives sometimes had no guards. Thankfully, these and many more horrors have largely been eliminated from modern operations.
When the HSE set the ‘Hard Target’ of cutting reportable incidents in quarries by 50% between 2000 and 2005, the majority of managers in the industry thought this was unachievable. All the combined experience showed that despite numerous pieces of legislation, huge safety manuals and substantial workforce training, incidents would still happen in quarries.
Quarrying was one of the first industries to have specific legislation. The Quarries Act 1894 was in response to an appalling rate of injuries and deaths. This was followed by another law in 1938, and a major upgrade to the Mines and Quarries Act 1954 – the ‘Orange Book’ that many readers will be familiar with. The well known Health and Safety at Work Act 1974 led to a number of specific regulations, including electricity, vehicles, explosives, COSHH, noise and tips. This long list was updated with the current Quarries Regulations in 1999.
Did all of this legislation make any difference? The statistics show that there were 1,150 fatalities and 12,000 serious injuries at around 8,000 operations during the first 10 years after the Quarries Act 1894. One hundred years later these numbers had reduced to 40 deaths and 1,100 injuries in a much smaller workforce at around 1,500 operations. Readers will be able to judge for themselves whether or not this performance is good enough.
On 11 August 2003, a shotfirer with many years’ experience was killed at Dowlow Quarry in Derbyshire. He was using a backhoe excavator fitted with a breaker and was in the process of removing some stubborn toes at the bottom of a high face when a large column of rock fell directly on to the machine. Recent heavy rain had weakened a clay-filled fault near the working location.
This turned out to be a pivotal moment in the history of Lafarge Aggregates Ltd. Dyfrig James had recently been appointed managing director of the company when this tragic event occurred. Dyfrig decided that Lafarge were going to eliminate incidents in the workplace, setting a very clear target of zero harm. The number one priority of the business was clearly established when Dyfrig announced to every employee and contractor the phrase that the company still uses today, ‘No job is so important that it is worth getting hurt doing it’.
Everybody agreed with Dyfrig, but at first most people found it quite difficult to work out what they were going to do in order to achieve the objective of zero harm. Nearly every employee had undergone training dedicated to reducing incidents, but reluctantly accepted that around 60 LTIs a year for the size of the workforce (then around 2,200 people) was the best that could be achieved.
One of the first steps forward was that everybody started to put safety at the top of their agenda; Dyfrig’s statement had struck a chord. Another early success was to require anybody involved in a lost-time incident to attend a return-to-work interview with the divisional director at head office. This was one of the ‘sticks’; later, one of the ‘carrots’ was the offer of an extra day’s holiday for every employee if the whole company (employees and contractors) achieved zero lost-time incidents for three months. This had never been done before; the previous record was less than a month. A daily countdown was communicated across the organization through a pop-up message whenever a computer was turned on. Suddenly, people in the normally safer office-based functions took an interest in the welfare of the front-line quarry operatives who were usually at greatest risk. The LTI-free period increased steadily and it took about a year for staff to achieve their first extra day’s holiday.
The workforce tried to make progress using a simple philosophy which showed that most organizations were dependent on supervision to control the number of LTIs. This does not work well enough. Lafarge’s objective was to become an interdependent organization where the whole team is committed and dedicated to looking after themselves and each other. Achieving this position will result in the least number of incidents.
In 2004, many people at Lafarge first met Peter McKie, the former DuPont managing director. He introduced staff to the concept of visible felt leadership (VFL). If employees see managers talking about safety and ‘feel’ its importance they will react positively. The leaders of an organization can make a difference by giving the most important resource they have – ‘Time’.
We are told that about 5% of incidents are due to the failure of equipment and systems. The other 95% are due to the actions of people. Leadership is critical; people will act unsafely if managers allow them to. Most people will do what they think management want them to do.
The top 200 managers were trained in the process of VFL through interactive task audits, many of them by Peter McKie; there was an opportunity to hear it from the man himself. Peter helped managers to start to believe that zero harm was possible. Many readers will be familiar with this process; if not, it is thoroughly recommended. Senior managers and many others were seen visiting Lafarge sites across the country. The people actually carrying out the work in the quarry were engaged in conversations about their work and how it could be done in the safest way possible, many for the first time.
The objective was to find out what people were doing, if they understood the risks involved in the tasks they were undertaking and what they were doing to eliminate the risk of an injury. If unsafe actions were observed or admitted to (which became more common when it was realized that they would not be disciplined) corrective actions were discussed and implemented. Many situations were solved by simply doing things differently; others required some expenditure for extra training, a safer means of access or a special piece of equipment. A short report was left on site to act as a reminder of the issues discussed, both positive actions and where remedial work was required. This information was also stored on a central database for future analysis.
All of those trained in VFL were asked to commit to a certain number of hours per month, usually at least four. This was tracked with a league table to make sure that it remained a top priority. After a couple of years a graph of the number of VFL hours against the LTI frequency rate (fig. 1) showed a clear link. With more than 350h of VFL every month, the number of LTIs reduced to less than one a quarter.
In addition to VFL, Lafarge also recorded approximately 600 unsafe acts and near misses every month, including incomplete PPE, using a mobile phone while walking, or taking short cuts. The unsafe acts/near misses are recorded by people in a broad range of positions within the company. The intention is for the unsafe act to be resolved at the time by the person identifying it. Some operatives will be enthusiastic about catching a manager out with a near-miss report, while others will report the event for the manager to resolve. It is also sometimes easier to pick on lorry drivers or contractors rather than workmates, but there is significant progress.
During the last few years Lafarge have implemented a huge number of safety improvements and initiatives. Some have cost relatively small amounts of money, while others have cost no more than re-prioritizing staff time. A few examples are presented below, but there are many more.
- All vehicles and mobile plant are drive-through or reverse-parked at all times. The driver’s visibility is significantly improved when pulling away. This includes every employee and visitor to every Lafarge site in the UK. Seeing around 300 cars reverse parked at the company’s head office is quite impressive, but believe it or not, some visitors still do not notice that something is different in the car park, until they are requested to reverse park at reception.
- All employees, contractors and visitors receive a safety induction on site. This varies in detail according to the nature of the visit. For example, fitters dismantling a crusher will be more rigorously inducted than the local mayor on an accompanied site tour.
- Thorough incident investigation and root-cause analysis is carried out. This includes minor events that probably would not have been reported a few years ago. A director will conduct a review of the more serious incidents.
- Drugs and alcohol testing is carried out for all drivers involved in vehicle or plant collisions, regardless of severity. Random testing has also now been implemented. Unfortunately, there have been a small number of positive results, however the number of occurrences is reducing.
- The disciplinary process is used where appropriate and some people have received written warnings or lost their jobs for behaving unsafely. This includes management as well as site operatives.
- Thousands of hours of targeted training have been carried out; from the Mobile Plant Training Academy for new starters (fig. 2) to Safety Leadership for the company directors.
- Establishing a competent management team for all of the company’s quarries has been a high priority. Every site has at least two managers who have been trained in Managing Safely by IOSH and have achieved a SHE NVQ at Level 3 or 4.
- Continuing Professional Development (CPD) has been implemented. Lafarge also developed the Corporate Professional Competence Scheme (CPC) with the Institute of Quarrying and were the first company to sign up.
- Managers have worked closely with mobile plant manufacturers to design and install innovative safe-access systems (fig. 3). This has reduced the need to climb vertical ladders or on excavator tracks and minimizes the risk of operatives falling from height.
- National Safety Week is held each year in June. Every site is visited by a manager from another area. The visitor aims to talk to all employees and carry out some improvement tasks while on site. A different topic is chosen each time; such as good housekeeping or improved health.
- On several occasions when there was an LTI at a site, all operations were suspended. This allowed time for the workforce to think about what had happened and to discuss ways to ensure that the operation achieved the goal of zero harm.
- Safety Focus Groups have been set up and chaired by the directors. The topics include working at height, transport, energy isolation and mobile plant safety. The groups are made up of people from different sites and with different job roles. Numerous initiatives have been developed and implemented across the aggregates, ready-mixed concrete and asphalt businesses.
- ‘Take time out’ is a commonly used phrase that encourages all employees to stop and think about the task they are going to do next. This could be reading the site traffic plan or a carrying out detailed risk assessment for a major repair. ‘Take time out’ to plan the job safely, before starting work.
- All employees now attend health monitoring every three years. A number of previously undiagnosed ailments have been identified and treated. In addition, many employees have been taking more exercise and there is now a long list of participants in sponsored events involving running, cycling and climbing mountains (fig. 4).
Small incidents and injuries are now considered unacceptable and investigations often result in changes to the way things are done. People are not afraid to speak up and they know what to do when risks are present. There is now an increasing number of new employees at Lafarge who have not had any experience of a company that incurred an LTI every few days (fig. 5). There is a very visible link between each employee’s contribution to a safer workplace and the tangible result of being very close to zero incidents.
The safety culture at Lafarge Aggregates has changed beyond all recognition during the last seven years and is a very long way from the potentially dangerous workplaces that existed in the early 1980s. Lafarge employees and contractors now take greater care in looking after themselves and each other, and all are committed to everybody going home safely every day.
Remember, ‘Take time out for safety’ and ‘No job is so important that anybody should be hurt doing it’.
This paper won the 2010 Marston Award – an annual prize for the best paper presented to an Institute of Quarrying branch meeting by a UK member, of any grade, employed within the quarrying industry.