High-pressure Grease Incident
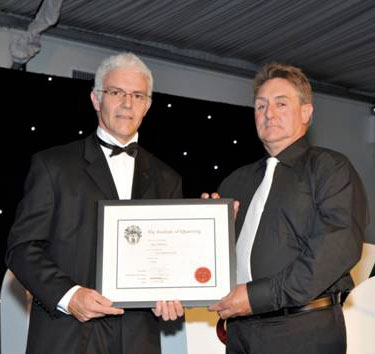
In this abridged article, Ken Andrews gives a graphic personal account of the life-changing injuries he suffered at work one night in 2004. Since the incident Ken has proactively sought to improve safety in the industry by sharing details of his traumatic experience and warning others of the dangers of fluids under pressure. He was recently presented with the Institute of Quarrying’s 2010 Caernarfon Award†.
I started my career in the maintenance, construction and mining industries as an apprentice fitter and turner some 40 years ago. Since then I have held a range of positions ranging from tradesman through to maintenance manager for a large mining company.
As a result of my front-line and management experiences, and my own involvement in a serious safety incident in 2004, I have developed a passion for promoting safety in the workplace in general, and specifically in the area of working with fluids under pressure.
My aim is to heighten awareness of the dangers that operators and trades persons face on a daily basis when working with modern machinery and fluids under pressure, to improve safety in the workplace and to reinforce the need for everybody’s involvement in making the way we all work, safe.
The 2004 incident
The incident occurred just after midnight on 31 July 2004. I had started work at 7.00pm and was handed over a job to change a dragline dump sheave (one of a pair of rope sheaves that allow the dragline bucket to empty when over the spoil heap).
Delivery of a rebuilt sheave had been arranged with the supplier and this arrived on site at around 8.00pm. I organized the cranes and equipment required to conduct the change, carried out and completed the required task risk assessments, then removed the old sheave and fitted the new one.
The sheave wheel is supported by a centre axle and taper roller bearings. I called our lube service truck to the dragline and explained to the operator that I needed him to pump grease into the bearing assembly until he could see the grease coming out between the wheel and both side frames. I left the lube operator to do this while I carried out some other work.
After a while the lube operator said he had been greasing for several minutes but was not seeing any grease coming out of the assembly, so I went to take a look. I proved that the grease system from the truck was working fine and explained to the operator that we would have to be careful in trying to find out why the grease was not coming out, as there could be up to 10,000 psi of pressure in the sheave bearing area.
I decided to loosen a second grease nipple that was visible on the top of the assembly by a flat (one-sixth of a turn) to see if any grease or air would leak past the thread, as I had noted that there was no sealant on the nipple.
I reached into the sheave frame, loosened the nipple as planned and then stepped back for a short time. As I moved back to the sheave and looked down on the nipple to see if any grease had become visible, there was a loud bang and the grease nipple was fired from the assembly.
The nipple struck my safety glasses separating the lens from the frame and tearing the glasses from my face. The lens cut me to the bone above the right eye and across my nose. At the same time a column of grease and highly compressed air was discharged from the bearing housing and struck me just below, and in, the right eye. This totally destroyed my eyeball and shattered all the bones around and behind the eye. The bone fragments and a quantity of grease ended up inside my skull; my cranial sack was ruptured and grease and bone entered my brain.
I was evacuated to a major hospital some 2h away by road for treatment. During the initial assessment of my condition the medics did not notice that I had suffered brain intrusion injuries. This was discovered some 10h later when a doctor spotted cranial fluid leaking from my eye socket. It then took a further 5h to get a team together to operate on me.
The operation to repair the damage and save my life took approximately 11h. This involved splitting the skin across the top of my skull, pulling my face forward and removing a section of my skull around the damaged area. Grease and bone were removed from my brain, my eye socket was repaired as far as possible and the remnants of my eye were removed. The doctors were amazed that I did not appear to have sustained any major brain damage from the incident or their repairs.
I was hospitalized for 14 days and returned to a limited office-work role after 16 days. After another two weeks I was back to full working days and moved into my current support role within the maintenance department. Due the loss of my right eye and damage to my hearing, I am not able to safely work on equipment in the workshop and so continue in a support role managing projects, technical support and failure analysis.
My recovery has involved a couple more operations, an eye prosthesis implant and some further recovery time. The end result is a total loss of sight in my right eye, about a 50% hearing loss in my right ear, together with some slight balance problems and some post-traumatic stress issues.
Incident investigation
The subsequent incident investigation was carried out by my employer and Australia’s Department of Primary Industries (DPI).
Following an in-depth examination of the safe systems of work that my employer had in place, and an exhaustive look at how I went about managing the safety of myself and others, and to see if I had complied with the requirements of my employers safe systems of work, no blame was apportioned to either my employer or myself.
The DPI found that I had extensive knowledge of the dangers of fluids under pressure (I have been working with draglines and high-pressure systems since 1969) and had explained the hazards to the person working with me. Even though I had assessed the risk of grease under pressure, I was caught out; my injury was simply a matter of being in the ‘line of fire’ when it all went wrong.
The reason the grease nipple and the grease were fired out at such high velocity was due to the fact there was a large quantity of air compressed and grease in the sheave under 4,200 psi of pressure.
The aftermath
When I returned to work I was challenged by my general manager to put together a toolbox talk that would inform others about the dangers of working with high-pressure fluids. This talk has now grown into a presentation that lasts more than an hour.
Not only do I talk about the hazards of hydraulics and hydraulic tooling, I also stress the dangers of high-pressure water blasters, compressed air and now the increased dangers to mechanics from high-pressure common-rail fuel systems.
We are currently running systems at up to 19,000 psi in our mining fleet, but perhaps even more frightening is the fact that most popular light-vehicle common-rail engines run at around 28,000 psi in the fuel rail. Most mechanics in service centres have no idea of the hazards or the potential for injury.
On 30 July 2004 I kissed my wife goodbye at 6.00pm. Seven hours later, at 1.00am on 31 July, my wife and two children had to rush to the local hospital where they saw me lying on a gurney, covered in blood and grease, not knowing if I was going to live or die. Seven years later, that moment still impacts on my now 17-year-old daughter.
†: The Institute of Quarrying’s Caernarfon Award is presented annually for the best paper given at an Institute event anywhere in the world and which is adjudged to have contributed the most to the advancement of some aspect of the industry.