Geotechnical Optimization of Excavation Designs in Rock
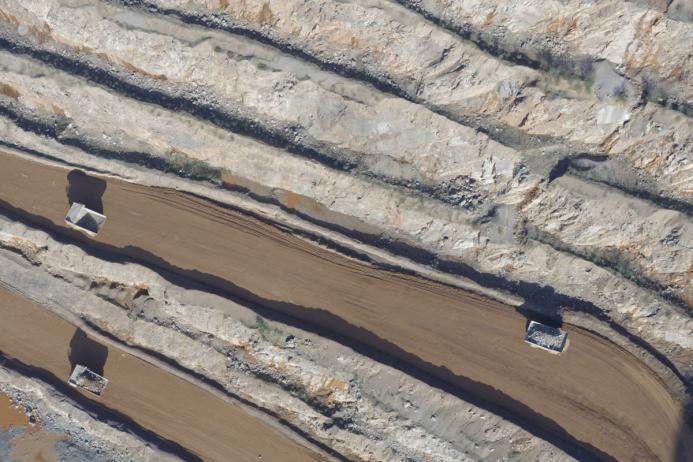
First published in the March 2025 issue of Quarry Management
How drone data can help reduce geotechnical uncertainty and maximize reserve recovery
By Ben Mason, associate partner and geotechnical engineer, GWP Consultants LLP
Quarries of the 21st century face a widening range of challenges under the umbrella of sustainability. There are increasing drivers towards minimization of any detrimental impact of quarry operations on the climate, landscape, ecology, and local communities, whilst remaining economically competitive and protecting the health and safety of workers and members of the public. At the same time, national reserves of aggregates are in decline and the planning system is often seen as obstructive to timely replenishment. More must be gained from any resource with reduced impacts.
One path to improving the sustainability of quarry operations is to maximize recovery of mineral within a defined footprint through the optimization of excavation designs whilst maintaining stable and secure slopes. However, given that geological strata are invariably heterogeneous, anisotropic, and discontinuous, this is often no simple feat. The behaviour of geological materials can be complex, and the validity of any predictions are subject to uncertainty due to both the intrinsic ‘randomness’ of geological phenomena and incomplete knowledge of ground conditions.
Geotechnically optimized excavation designs to maximize recovery of mineral reserves rely on reducing this uncertainty. Without a solid understanding of the underlying ground conditions and their spatial variability, and the likely failure mechanisms or representative geotechnical material parameters, geotechnical designs must account for uncertainty by making conservative (worst-case) assumptions about ground conditions, selecting conservative input parameters to slope stability analyses and/or adopting higher target factors of safety that a design must achieve to be acceptable. Invariably, this leads to sterilization of mineral as excavated slopes must be left slacker than optimal.
Geotechnical uncertainty can be reduced through effective and high-quality site investigations. The more boreholes are drilled the better we understand the distribution of strata. The more samples are tested the better our understanding of the mechanical behaviour and strength of a material. Conversely, inadequate site investigation may lead to implementation of geotechnical designs which have been prepared without knowledge of adverse ground conditions (eg the presence and distribution of weak bands, faults, high groundwater pressures etc).
The use of unmanned aerial vehicles (UAVs) for remote discontinuity surveys is well tested and, combined with on-site observations, provides an opportunity to reduce geotechnical uncertainties when designing safe and stable excavations in fractured rock masses, as well as providing data of sufficient quality and quantity to support optimization of excavation geometries.
One of the key factors influencing the stability of fractured rock masses is the orientation of the natural breaks or discontinuities with respect to the excavated faces. Robust geotechnical design of excavations in such materials relies on collecting accurate and representative data on discontinuity orientations and their spatial variability. Without the support of adequate geotechnical data to reduce uncertainty, an overly conservative slope design may have to be adopted with wider benches and slacker slopes to account for uncertainty around break back associated with plane, wedge or topping failures. This could lead to the unnecessary sterilization of mineral reserves which could have been worked safely for want of sufficient data.
Conversely, without access to adequate data to support the geotechnical design, the potential for some types of discontinuity-controlled failure mechanism to occur may not be identified. This could lead to the implementation of an excavation geometry which is overly steep and risks the unexpected occurrence of bench or multi-bench-scale failures.
Traditionally, the methodical collection of discontinuity orientation data required geologists to work directly below rock faces to obtain hand measurements with a compass clinometer. Clearly, this comprises a high-risk activity, one which is now rarely permitted except under well controlled circumstances. Remote discontinuity surveys completed using UAV-acquired data have largely replaced the need to undertake this high-risk activity.
The UAV imagery required to prepare high-quality three-dimensional models for detailed discontinuity mapping can (weather depending) be obtained within one or two working days for even a relatively large quarry excavation. Following placement and surveying of ground control and check points, vital for model corrections and quality assurance checks, the capture of overlapping overhead and oblique images can be safely completed by the UAV pilot from several safe vantage points. The risks to personnel from quarry operations, mobile plant movements or rockfall are much reduced compared with traditional methods.
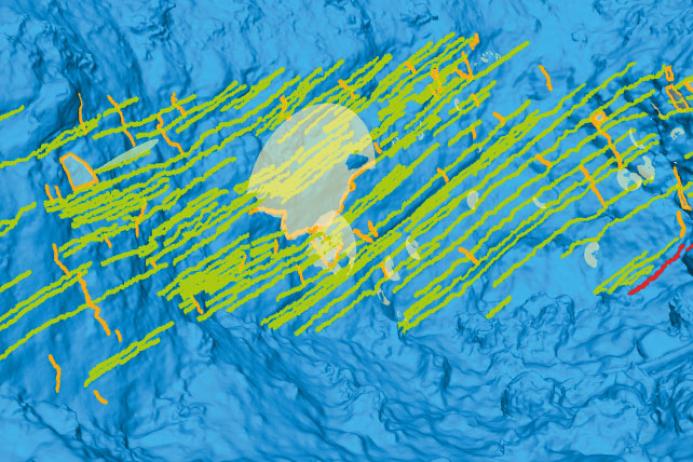
UAV-acquired face imagery is processed through specialist software, typically using a structure-from-motion (SfM) algorithm, to prepare a three-dimensional digital mesh model of the faces from which the orientations of discontinuities are measured. High-quality and statistically robust discontinuity orientation data sets can be obtained from the comfort of the office without exposure of personnel to the hazards of active quarry operations. Information can be obtained on discontinuity set or individual structure variability, positions, and changes across different geological or geotechnical domains. Measurements are not limited to those within the safe reach of traditional mapping techniques and can be easily queried, checked, and exported to other software for further geotechnical analysis.
In combination with an experienced geologist or geotechnical engineer, UAV-acquired face mapping data can allow for greater confidence in predictions of fractured rock mass behaviour on excavation. The data forms the basis of subsequent kinematic and limit equilibrium stability analyses which aim to predict the extent and likelihood of any break back that needs to be accommodated by the excavation design. With the support of high-quality orientation data sets reducing uncertainty, there is the potential for adopting steeper, geotechnically optimized excavation designs which minimize sterilization of mineral whilst maintaining secure and stable slopes.
Whilst UAV-acquired data has allowed for vastly improved characterization of some geometric properties of discontinuities, it has not, and cannot, replace the need for geotechnical engineers to spend time on site. Any remotely obtained data must be subject to ground-truthing. Robust data on other vital parameters which influence excavation stability (eg discontinuity surface roughness, aperture, wall coatings or infillings) cannot be characterized remotely and still require engineers to spend time with their noses to the rock.
Digital face-mapping methods can provide a record of discontinuities and their position (or projected positions) in three-dimensional space. This has the benefit of allowing for the prediction of intersections with current or future excavation developments and, where required, allows for design modifications or changes to working methods to be planned in advance to prevent instability. As the collection of discontinuity orientation data using UAVs can be undertaken relatively rapidly and without significant interruption to site operations, it can be repeated periodically for active excavation areas to identify or confirm the positions of adversely oriented and highly persistent weak planes, such as faults, pre-sheared horizons or clay wayboards, and allow for proactive updates to excavation designs to prevent the undercutting of such features.
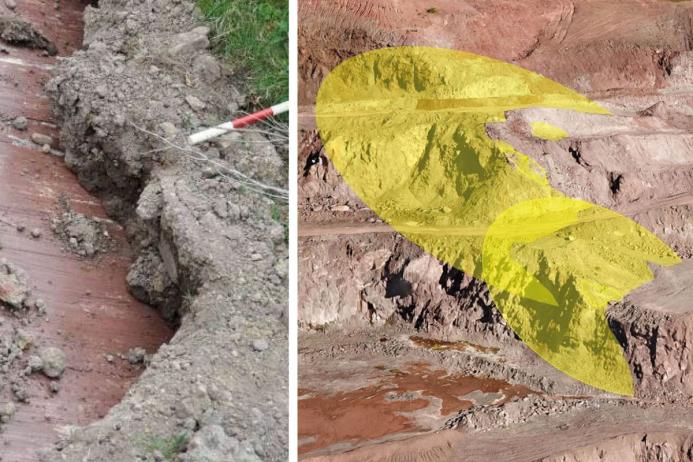
UAV face mapping is now a well-tested and effective tool for reducing uncertainty by providing safe access to high-quality, reliable, and statistically robust data sets on discontinuity orientations, persistence, spacing, and their spatial variability. Reduced uncertainties can lead to adoption of less-conservative geotechnical slope designs, maximizing the recovery of mineral within a defined footprint. Whilst UAVs can rapidly provide high-quality data over large areas, they remain but one tool in the geotechnical armoury and must be combined with other site-investigation techniques to fully characterize strata.
Geotechnics is often viewed principally as a risk to be mitigated in quarrying. Whilst risks do need to be properly mitigated, obtaining a better understanding of ground conditions and their variability can also give opportunities for geotechnical optimization of designs. With the adoption of well-tested technologies, such as UAVs, for improved data capture, even relatively small investments in site investigation can pay large dividends for the geotechnically optimized design and implementation of secure, stable, and sustainable quarries.
Subscribe to Quarry Management, the monthly journal for the mineral products industry, to read articles before they appear on Agg-Net.com