The Effective Suppression Of Dust
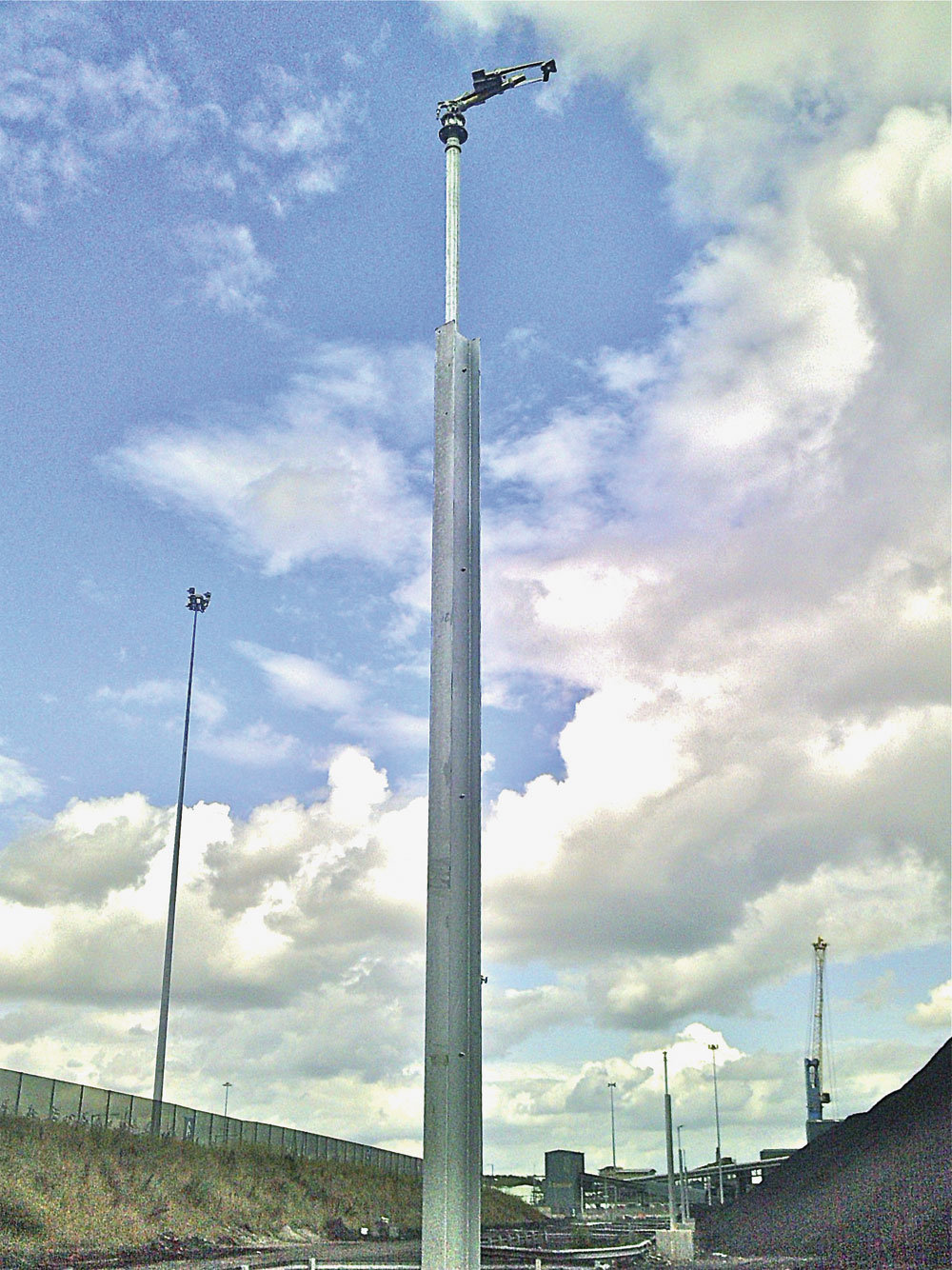
Examining the use of wet dust-control systems and their benefits
By Chris Hutchins, Wright Rain Environmental Ltd
When specifying a system for the control of dust, many issues need to be taken into account, including the following: the nature and size of the dust particle; the size of the spray drop, its angle of delivery and pattern; the placement of the nozzle; the quality and availability of water and its pressure; and the level of control required.
This article examines the use of ‘wet’ dust-control systems, ie systems which use water as their main medium of control. Wet systems increase humidity to prevent dust from becoming airborne or are used to bond with airborne dust in order to bring it down to the ground.
The water is applied using spray nozzles and water mixed with chemical agents that can both aid the binding process and reduce the amount of water used. The method of application and positioning of the nozzles depends on the nature of the problem. Stationery equipment often requires a different solution to systems that move.
The nature and size of the dust particle
The size of a dust particle can vary from 0.01μm (carbon black) to 500μm (pulverized coal). The size of the dust particle is important because it indicates the size of the spray droplet to be used – large droplets will not combine with smaller dust particles and the smallest droplets can evaporate and thus release the dust they have captured before it has been dealt with. Dust capture tends to be most effective when dust particles collide with water drops of a similar size. In simple terms, therefore, the smaller the dust particle, the smaller the droplet needed to deal with it.
The size of the spray droplet and its pattern
Critical to every installation is the size of the droplet and the pattern produced by the spray head, both of which depend on the nozzle used. When specifying a nozzle the droplet size must be considered first, ie the size of the droplets that leave the spray head. This can be affected by many factors including nozzle capacity, liquid pressure and liquid properties. The design of the head itself has a large influence on droplet size. A few basic rules apply:
- An air-atomizing nozzle produces the smallest droplet size and full-cone nozzles produce the largest.
- The higher the pressure the smaller the droplet size.
- Lower flow produces smaller droplets than higher flow.
- An increase in surface tension increases the droplet size.
- Smaller droplets have a higher velocity but lose that velocity quicker than larger droplets.
A droplet size of less than 200μm is usually ideal for airborne dust particles. Such sizes can be achieved by the use of atomizing heads. The atomization is achieved by the use of high pressure and small apertures or by the addition of compressed air to such a situation. This produces a very fine mist or fog as the head reduces the droplet size to a minimum. The smaller droplets are effective in this situation because their surface tension is reduced, allowing them to bond more easily with the dust particles, while the number of droplets is increased thus allowing a far higher bonding rate.
There is a cost penalty associated with this type of operation as the pressures required are usually produced by the use of expensive pumps – air compressors add to this cost. The addition of surfactants (which help to break down the surface tension even further) can offset some of these costs.
Once again, a few standard rules apply:
- To prevent dust, a hydraulic nozzle producing droplets between 200 and 1,200μm is generally used.
- For airborne dust with smaller particles, air-atomizing nozzles or hydraulic fine-spray nozzles that produce droplets between 20 and 200μm are generally used.
- The type of nozzle and spray pattern to be used will depend on the operating conditions.
- Operating conditions will determine which nozzle style and spray pattern will offer the best performance.
Types of spray nozzles include the following:
- atomizing spray – discussed above, used for dust suppression
- hollow-cone nozzle – reduces clogging, gives a small droplet size and is used where dust is widely dispersed; often used for dust prevention
- full-cone nozzle – provides a high speed and can reach long distances, produces a medium to large size droplet; often used for dust prevention
- flat-spray nozzle – gives a rectangular spray pattern and is useful in enclosed spaces, produces small to medium sized drops; often used in dust prevention.
The spray pattern selection will depend largely on the site conditions and the material which provides the dust.
The material giving rise to the dust needs to be considered, as different materials respond in different ways to moisture and its components. Too little moisture and it can dry quickly leaving the dust, while too much can result in the creation of a quagmire.
The integrity of the material may also be affected by the wetting agent. If water is used to excess, some materials being treated may become soaked and unusable. The use of surfactants may not be appropriate and foaming agents can create foam when it is not required.
Binding agents can be successful in containing long standing piles and their effectiveness can be renewed by the application of further water. Certain binding agents can, for example, turn aggregate dust into a solid roadway with a reasonably long life.
The placement of the nozzle
There are some obvious issues in relation to the positioning of nozzles – the availability of water and power being the two major ones. Assuming that these issues can be overcome, the major placement issue is the operation causing the dust.
Each situation has its own solution:
- Soil heaps tend to be in fixed positions and so fixed heads tend to be best.
- Conveyors can benefit from the application of binding or foaming agents applied directly to the belt.
- Shredders need suppression at both the intake and output, and mounting on to the shredder can be best.
- High winds tend to need larger droplet sizes diffused by high-pressure guns.
Overspray and water conservation are other issues which may need to be addressed.
The quality and availability of water and its pressure
The quality of the water to be used in a system is critical to its effectiveness. Rainwater, seawater, recycled water and run-off can all be used in addition to mains, but each presents its own level of difficulty. The use of different types of water can overcome supply problems and tanks can provide a top-up for otherwise inadequate supplies.
The usual source of water, and least difficult to use, is tap water. It is clean and, usually, abundant, but because of the processes it has undergone to arrive at its destination, it is inevitably the most expensive type of water used in any system. In a typical water main, the pressure is also usually insufficient to operate all but the smallest system, so the use of pumps is normal for virtually every dust-suppression system. However, tap water has an advantage in that, because it is so clean, it does not usually require the filters and cleaning systems required when using water from other sources.
Rainwater can be another good source of supply but as rainfall is unpredictable, it will always need a backup system to ensure continuous supply.
River and seawater will need to be thoroughly filtered before use, and with seawater there is also the corrosive effect of the salt to be taken into consideration. Similarly, recycled water may need to be treated before re-use.
To add to these methods of supply, boreholes can also be sunk to provide a continual supply of water to the site. This method, like the use of river and seawater, is normally subject to limits on the amount which can be taken each day. Such limits can be partially, and sometimes completely, overcome by the use of tanks.
The other major issue is pressure. As mentioned above, mains water pressure is not usually sufficient for any effective dust-suppression system. The only effective way to increase pressure is by the use of a pump. The type of pump used for each system is dictated by the requirements of that system; too powerful and even the biggest spray head will be converted into a misting unit; too weak and very little will happen.
The level of control required
The level of control can vary from no control at all at one end of the scale through to fully automated control at the other end of the scale.
The simplest systems are hand-operated and controlled by an operator turning a tap on and off. The operator may need to move the spray head by hand to the areas where water is required and will decide on the amount of water used. Such systems can be remarkably effective in certain situations, particularly on smaller sites where the cost of labour is not a critical issue.
At the other end of the spectrum, a meteorological station may be used to measure wind and humidity levels and adjust spray patterns and areas accordingly. Dust sensors can decide when and if an area needs to be watered, and wind sensors can specify the sprays to be used, eg in perimeter rain curtain systems where prevailing wind changes make certain curtains more effective than others. The timing, sequence, volume of water used and, indeed, all other aspects of the system can be automated to ensure maximum efficiency.
The deciding factor in all systems tends to be cost. As with most things, the more that is spent the greater the control that can be achieved.
For further information visit: www.wreltd.co.uk