New Techniques For Dust Suppression And Control
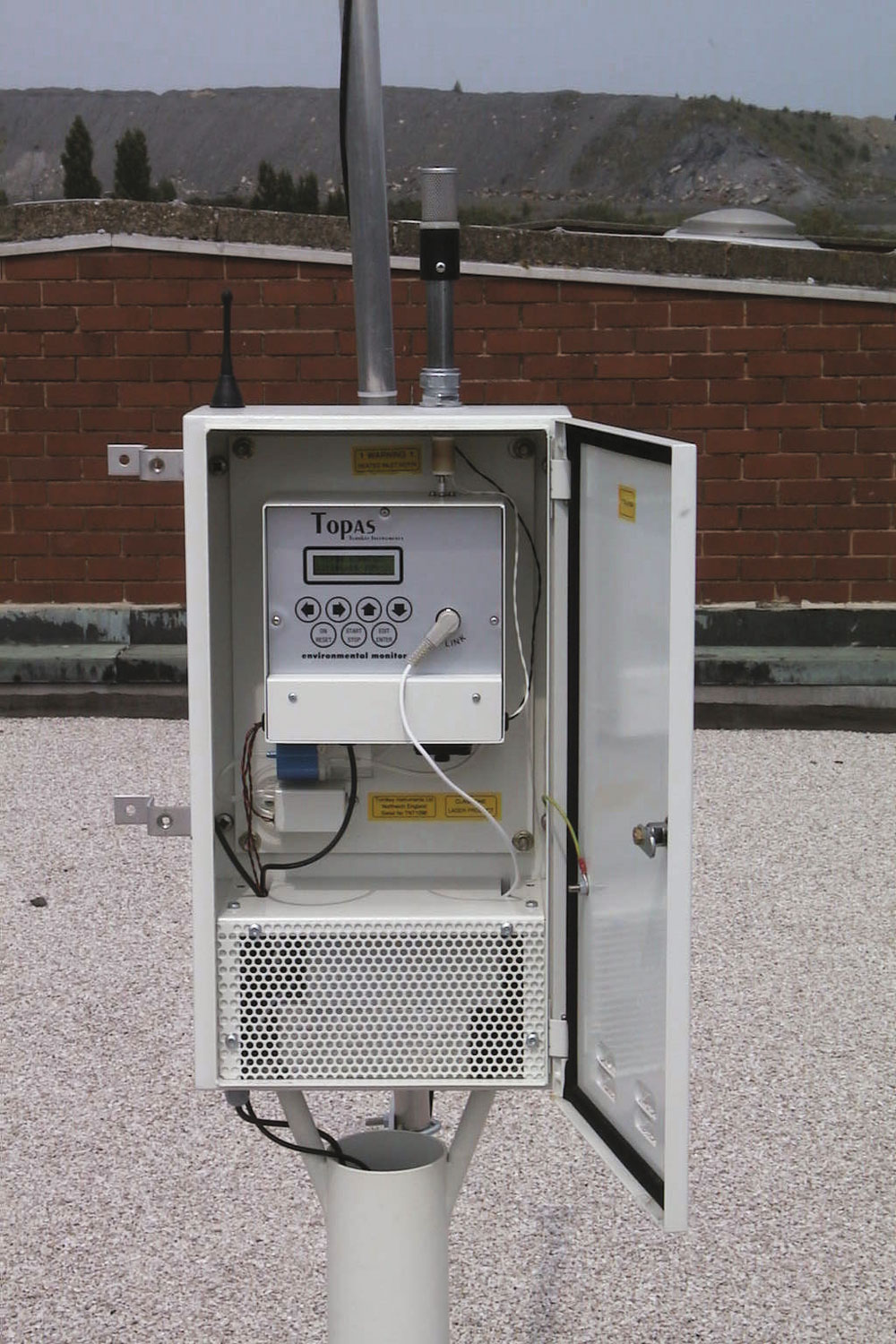
Turnkey Instruments discuss the use of continual dust monitors
A variety of dust-control technologies have been developed to help mineral extraction and processing operations meet planning conditions and environmental compliance for fugitive dust emissions.
The three basic types of dust-control system currently used in minerals extraction and processing operations are:
- dust collection
- wet dust suppression
- airborne dust capture.
Dust-collection systems use ventilation principles to capture the dust-filled airstream and carry it away through ductwork to the collector. Wet dust-suppression techniques use water sprays to wet the fugitive material so that it generates less dust. Airborne-capture systems also use water sprays but in this case the airborne dust particles are sprayed with atomized water. When the dust particles collide with the water droplets they agglomerate and rapidly settle out due to their increased size.
Chemical surfactants may be added to the water to reduce surface tension, thereby reducing droplet size. These additives also improve the ability of water to wet and to agglomerate finer particles.
Although water sprays have been the preferred treatment to suppress dust for many years, too much water can cause operational problems, while too little water means ineffective dust control. The fine particles in dust also contribute to holding unpaved road surfaces together. Good dust-suppression techniques, therefore, may result in lower maintenance as well as preventing complaints about off-site air-quality problems caused by operations.
One way to optimize the performance of a dust-control and suppression system is to operate it in conjunction with a continuous dust monitor. In its simplest form, this could report back to operators when high dust concentrations occur so that manual remedial action can be taken. However, it is possible to automate such a system so that the water sprays operate when the dust concentration rises above a pre-determined threshold. This will minimize the use of water and chemicals, thereby reducing costs and keeping the site drier than if water sprays are running continuously.
In the past, one problem has been in distinguishing locally generated dust, which needs to be suppressed, from dust blowing on to the site from elsewhere. A number of continuous dust monitors located around the site periphery can determine the quantity of dust entering and leaving the site. This information can be combined with wind speed and direction to determine the likely dust source. While such a network of monitors is useful for assessing the overall dust generated at the site and confirmation of overall compliance, it may not be much help in controlling dust blow-off from individual stockpiles or roadways.
Fugitive dust particles are predominantly larger than PM2.5 (ie greater than 2.5µm in diameter), whereas dust particles from distant off-site sources are predominately smaller than PM2.5. The reason is that the large particles settle out increasingly quickly with increasing particle size — the reason why agglomeration with water droplets suppresses dust. Indeed, the settling rate increases with the square of the diameter. Thus, a long way from a dust source the particles are predominantly PM2.5, near to the source they will be characterized by the PM10 (10µm diameter) or bigger fractions.
Until recently it has not been possible to determine the PM10 and PM2.5 mass fractions in real time using a single low-cost instrument. Turnkey Instruments, however, have developed a range of continuous dust monitors that do so and can provide outputs to control dust-suppression equipment. These instruments are easy to install and maintain. They have a low demand on the receptor site, can be fastened to almost any structure and require a low power supply.
Osiris and Topas instruments operate on the principle of light diffraction and have a virtually constant response irrespective of the colour of the dust particles. They give a continuous and simultaneous indication of the PM1, PM2.5, PM10 and TSP mass fractions. Due to its relatively low flow rate, the sampling efficiency of the TSP mass fraction will be affected by wind speed — at high wind speed it becomes increasingly difficult to get the largest particles into the instrument’s inlet. However, PM10 and smaller fractions are sampled efficiently and the relative PM10 and PM2.5 fractions taken together give a good measure of the local dust concentration and the proximity of the dust source.
It has been found that a PM10/PM2.5 ratio close to unity indicates a distant dust source, whereas a ratio much greater than unity indicates an increasingly local dust source.
Since the settling out of the PM10 particles depends on time, the PM10/PM2.5 ratio depends to an extent on wind speed, which determines how quickly the particles travel from their source. Since the instruments also have a built-in interface for wind-speed and direction sensors, these parameters can be factored into the calculations. The instruments also have a heated inlet system to ensure that the water droplets originating from the suppression equipment evaporate before being sensed and do not, therefore, add to the apparent dust concentration!
Turnkey’s dust-monitoring equipment can be operated in a number of different modes depending on the site and application:
- As independent monitors programmed with a hierarchy of SMS text messages to be sent out to chosen people when the dust concentration has been sustained above one or more preset concentrations for a given period of time. Site protocols can then determine what action should be taken and by whom.
- As part of a network of monitors controlled by a PC or site computer. These could include site boundary monitors as well as those located near critical stockpiles, crushers and roadways. The PC can be programmed to send out SMS text messages (as above) and, with appropriate interfacing, directly control the dust-suppression equipment. The PC-based systems allow more complex alarm criteria to be used with various conditional statements, including a consideration of wind speed and direction and other parameters such as time of day etc.
- As a web-enabled monitor so that anyone with the correct password (or none if open gain access is permitted) can access via the Internet to determine the current dust concentration, wind speed and direction etc. Turnkey instruments also have optional inputs for sound-level meters so that mean and peak noise Leq’s can be made available.
- As a simple on-off controller, whereby the monitor is directly connected to the dust-suppression equipment and automatically turns it on when the dust concentration rises above a preset level and off again once it falls. The control point could be stabilized using a PID control algorithm if required.
The use of Osiris and Topas instruments for dust control and suppression is not limited to mineral extraction sites and applies equally well to storage and handling facilities. For example, fugitive dust emissions from coal and iron ore storage and handling sites in the Port of Rotterdam in the Netherlands cause nuisance in residential areas, due to dust deposition, and add to the PM10 dust concentration. After extensive research, a new dust-control system, based on Turnkey Osiris, has been installed that monitors conditions at three receptor sites1.
This system provides plant operators with the necessary information to intervene when dust emissions are rising and nuisance is likely to occur in neighbouring villages. The system is expected to reduce peak emissions and thereby reduce the terminal’s contribution to ambient dust concentrations. It is also thought that off-line analysis of the data might yield additional information to improve the existing environmental management guidelines in use at the bulk terminal.
The BHP Billiton iron ore handling facility at Port Hedland, Western Australia, operates a large network of Osiris monitors for dust control purposes. Here a recent development has been the use of mobile Turnkey dust monitors fitted into vehicles together with GPS locators. The vehicles are driven over the site roads and monitor the concentration of dust generated against exact location. For this application the instruments are set to operate at their fastest response time of just one second, all four mass fractions being updated at one-second intervals. Suppression sprays are then applied automatically as required, thus minimizing the use of water and chemicals while keeping the roadways in good condition.
Integrating continuous and instantaneous dust monitors increases the performance and flexibility of dust-suppression equipment and should lead to overall cost-savings and better site conditions.
Reference
- Vrins et al, Clean Air Congress, London 2004.