Manager’s Guide To Energy Efficiency
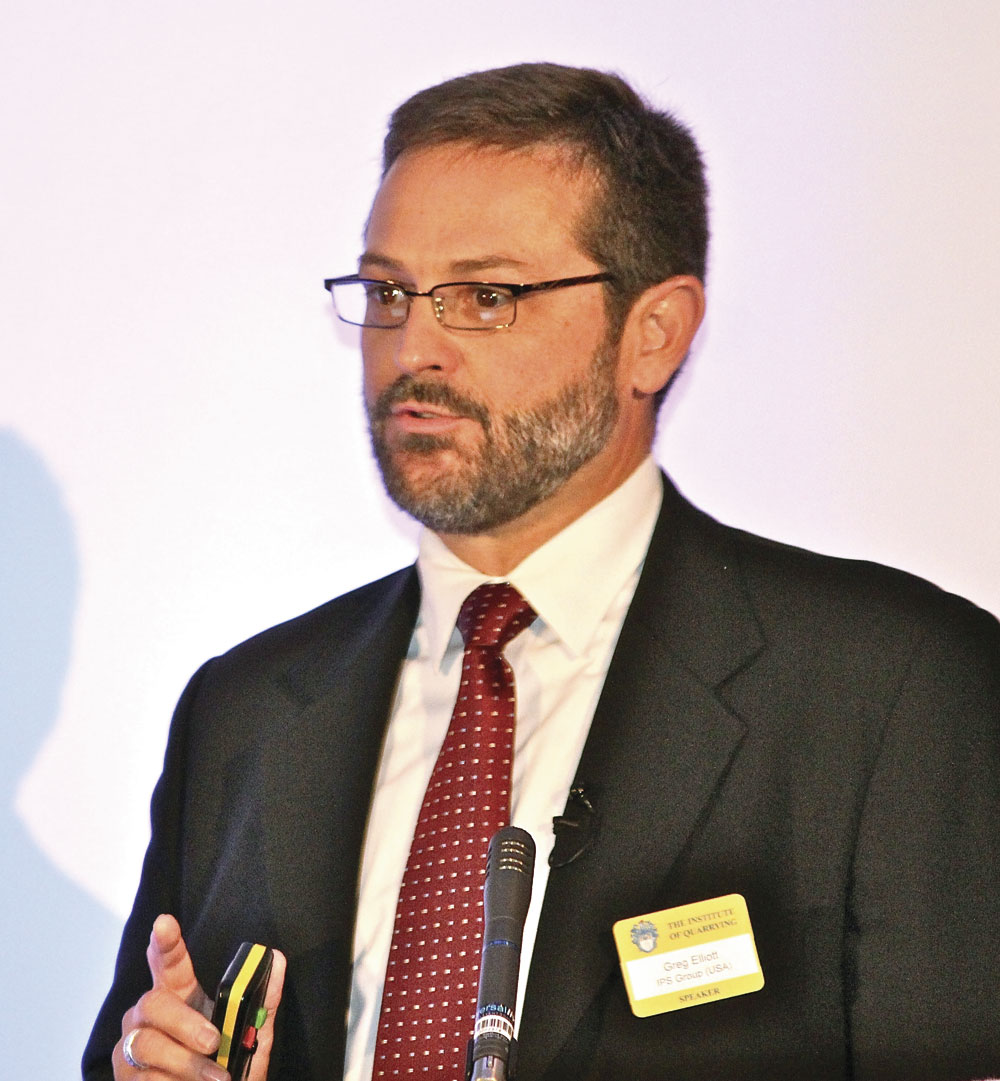
Measurement is the key to going ‘green’, as Greg K. Elliott, president of Innovative Plant Solutions Group Inc, explains
It is no secret that business leaders across various industries are facing the issue of ‘being green’ on top of dire financial and market declines. This has created a new paradigm that most leaders are less than prepared for. Many struggle to define what ‘being green’ means specifically within their industry and, more importantly, within their company. To most, being green means reducing their consumption of non-renewable resources and emissions. But this can be difficult to nail down.
It may be helpful to consider what important world organizations consider to be the definition of ‘green’. The most common broad-reaching term is ‘environmental sustainability’. The following are what a few organizations offer as a working definition.
The World Bank defines it as: ‘Ensuring that the overall productivity of accumulated human and physical capital resulting from development actions more than compensates for the direct or indirect loss or degradation of the environment.’
The Ministry of Economic Development of New Zealand suggests it means ‘movement towards redesigning the way society’s needs and wants are met so that they can be accommodated within the long-term carrying capacity of the environment’.
The FAO/Netherlands International Conference in 2005 defined it as: ‘Meeting the needs of the present without compromising the ability of future generations to meet their needs, eg keeping population densities below the carrying capacity of a region, facilitating the renewal of renewable resources, conserving and establishing priorities for the use of non-renewable resources, and keeping environmental impact below the level required to allow affected systems to recover and continue to evolve.’
From the above examples, the definition of ‘green’ can be simplified to: ‘reducing energy consumption and emissions per unit of production’ (per unit of production is of crucial importance within the definition and how it is put into practice). To grasp this meaning it is necessary to understand that the globally excepted definition of ‘energy’ equates to water, air, gas (fuels), electricity and steam. Thus, a definition such as ‘reducing the consumption of water, air, gas, electricity and steam, and the corresponding emissions per unit of production’ is a reasonable starting point.
Equally important to understanding what environmental sustainability is, is understanding what environmental sustainability is not. It is not a programme in a binder on the shelf, a label, a tag or a logo. Painting buildings or equipment green does not make a company green. Environmental sustainability cannot be restricted to a single silo in an organization.
As everyone now understands, environmental sustainability is not a fad or a trend that will soon go away. Nor it is the product of the marketing department. The author was amused to read a report of a cement producer who claimed a 30% reduction in carbon footprint, but failed to include in the report that production was down 47%. Environmental sustainability is not an outcome or a result; it is, first and foremost, a culture.
Environmental sustainability is and must continue to be a permanent change in the way companies do business. It is a new corporate culture with new operational practices and new fiscal approaches – a totally new vision. Being green, energy efficient or environmentally sustainable is a frame of mind that permeates every crevice of an organization.
Sustainability is no longer just an environmental issue but an issue of survival. In the very near future, and to some degree already, there will be two kinds of companies; those who have adopted a corporate culture of energy efficiency and the extinct.
An article in the Harvard Business Review (May 2010 edition) entitled: ‘The Sustainability Imperative’, by David A. Lubin and Daniel C. Esty, states the following: ‘Most executives know that how they respond to the challenge of sustainability will profoundly affect the competitiveness – and perhaps even the survival – of their organizations. Yet most are flailing around, launching a hodgepodge of initiatives without any overarching vision or plan. That is not because they do not see sustainability as a strategic issue. Rather, it is because they think they are facing an unprecedented journey for which there is no road map’.
The article continues: ‘Gaining advantage in a megatrend is not just about vision – it is also about execution in five critical areas: leadership, methods, strategy, management and reporting. In each area, companies must transition from tactical, ad hoc and siloed approaches, to strategic, systematic and integrated ones’.
‘…(executive leadership) must visualize goals and professionalize the process of aligning vision with business strategy. That means redefining performance expectations, specifying accountability, tracking results and rewarding success’.
The authors go on to say: ‘Recognizing that if they cannot measure it, they cannot manage it, companies are developing better means of gauging corporate sustainability-related costs and benefits and benchmarking performance’.
‘…like the IT and quality megatrends, sustainability will touch every function, every business line, every employee’. The truths of this article are undeniable.
The question at hand is how to achieve long-term sustainable and verifiable reductions in energy consumption and CO2 emissions. The emphasis of this article is the importance of the ability to measure and verify process efficiency, energy consumption and emissions through continuous monitoring. Without these elements in place any efforts to towards environmental sustainability will likely be thwarted.
No matter what the goal, the industry or the size of organization, striving to set and achieve objectives in the area of energy requires a clear methodology. It takes leadership in change management. Change management is a corporate culture issue and must take place from the top down with accountability at every level. The plan must include:
- Adaptation of a corporate-wide policy to support and fund energy efficiency
- Communication throughout all ranks, divisions and management levels is critical
- Application of plans and policies across all organizational silo structures for consistency
- Accountability based on clearly defined baselines and key performance indicators.
If each of these elements is not in place, goals will tend to be vague, universal and immeasurable.
It is likely that most readers will be saying to themselves ‘we’re already doing that’. But these economic and politic times call for a ‘next step’ in energy management. Many readers will be familiar with the Plan–Do–Check–Act model and are likely to be deploying something similar in a many areas of their companies. However, there is a flaw in this model and it can be seen in the way many companies are going about attempting to achieve ‘green’ goals.
How do you know where to begin your energy-efficiency plan if you do not know how much energy you are using relative to production units? Think of it this way; you would not drive a car without a working and accurate fuel gauge. You trust and rely on that gauge to give you accurate real-time information about how much fuel you have and how much you have consumed. It is time to address energy in the same way.
It is for this reason that IPS Group recommend that before you ‘plan’ you should ‘measure’. Measure consumption, measure output or productivity and measure time. Without this information it is not possible to develop a reasonable plan. By way of example, an aggregate producer in the UK who was committed to reducing energy consumption realized that the firm had enormous leaks in its compressed-air system both in the plant and in the garage, so it spent thousands of pounds and fixed all the leaks and replaced the regulators and lubricators. The owner expected to see tangible results in the electric utility bill, as he knew the compressor was now running significantly less. After 90 days, however, there was no visible reduction in the bill.
The reason: at the same time that the compressed air changes were made, upgrades to the administration office and dispatch computer were completed (new computers, new monitors, new phone system etc), so instead of seeing a reduction in the bill the owner actually saw an increase. Since there was no demand point metering to determine the correct measures of the compressed air system, he could not verify the savings. Worse still, the administrative building, the plant and the garage were all on one meter, allowing any improvements made in one area to be masked by inefficiencies in other areas.
Most companies that IPS Group talk to say they have already addressed or are addressing the ‘low-hanging fruit’. This means different things to different people, but the one thing they all have in common is the absence of a point of reference or a measurement. In another example, a company has exerted great effort and resources addressing the ‘low-hanging fruit’ issue of motor efficiency in more than 50 asphalt plants. They had a so-called expert come in and convince them that they needed to upgrade from direct-start motor starters to soft-start and variable-speed starters. They subsequently spent hundreds of thousands of pounds on new starters. The author recently spoke with both the producer and the supplier and asked a few questions, such as:
- How much energy was each motor using at any one given time?
- What did that equate to in kWh per tonne?
- What is the associated cost of operating those motors, before and after changes?
- How did you optimize the process to reduce demand on the motor?
The answers received can be summed up in two words – blank stare.
If your company is putting activity before preparation and targeting ‘low-hanging fruit’ without a plan and method of measuring in place first – stop! Activities, especially ad-hoc repairs, modifications and upgrades that are not based on accurate, real-time measurement, are likely to be ineffective, unnecessary and, thereby, money spent with no verification of savings. This deters future investment in the right activities due to a lack of results from past experience.
An ‘Environmental Sustainability Plan’, ‘Continuing Improvement Plan’ or ‘Energy Efficiency Plan’, or whatever you wish to call it, must encompass the following:
- Measure – in any planned change, it is first necessary to understand where you are before you can establish reasonable and attainable goals.
- Plan – once you have accurate and relevant measurements you can develop a clear and actionable plan.
- Implement – have a clearly defined action plan with milestones, accountabilities and flexibility.
- Assess – know how you are going to define measures of success and be prepared to adjust and realign activities, timetables and budgets.
- Repeat/Adjust – continue to apply the same methodology to all defined areas of your operation and until you achieve your stated goals.
There are many companies today that offer a technical solution to process and energy monitoring. This can be as simple as installing instruments to measure activities, whether process or energy related, and reporting back to a computer in the plant. But it may not be quite that simple.
There are right ways and wrong ways to measure process and energy consumption. It is usually not as simple as calculating kWh per tonne or per unit. Other issues, such as demand, power factor and total harmonic distortion, can play a huge part in determining your energy bill. Knowing how you are being charged by your electricity provider and how you use energy are crucial for developing the proper monitoring scheme.
Faced with a decision between temporary or audit measuring and continuous monitoring, do not opt for the cheap option. While there is certainly a place for temporary monitoring, it is not the correct data source for developing baselines and action plans. Think of it as a snapshot of a split second of your operation. Accurate baselines must be the result of the accumulation of data taken over time.
Moreover, bad information or anomalies should be weeded out. Another benefit of continuous monitoring is that it provides the data necessary to identify irregular or anomalous data. It is also possible to develop trends and exceptions from long streams of data that cannot be obtained from temporary monitoring. The more data that are available, the better the ability to identify these things and arrive at sound conclusions. Continuous monitoring is the only reliable and verifiable source for determining the impact of weather, production levels, time of day, operator performance and other variables on energy costs per production unit.
The bottom line is that failure to measure or failure to collect adequate and accurate information will result in flawed planning. There is an old saying ‘fail to plan and plan to fail’. The same can be said about failure in measuring to create accurate baselines. Bad data will result in bad goals.
Once you have good baselines you can proceed with planning your action steps. Another benefit of continuous monitoring is that it makes it possible see the immediate effects of corrective action. Perhaps even more importantly, once a performance goal has been achieved, continuous monitoring will provide immediate notification if efficiency begins to decline. This eliminates the assumption of making savings. There is little better insurance than to know that every pound invested in corrective action is working for you continually.
This may all sound expensive and it can be. But, it is possible to take small, proactive steps to build successes and justify further expenditures if you do it correctly from the beginning. This is why it is so important to select the right vendor/partner companies to assist in developing an energy-management plan and the installation of continuous monitoring.
Remember, the cost of being green is not a new cost. Waste costs more than the cost of being green. So, before throwing more money away – measure, measure, measure.
This article is based on the author’s presentation at the Institute of Quarrying’s 2011 Annual Conference Symposium on the theme of Energy Management & Cost Saving Initiatives.