Energy Savings At RMC Aggregates
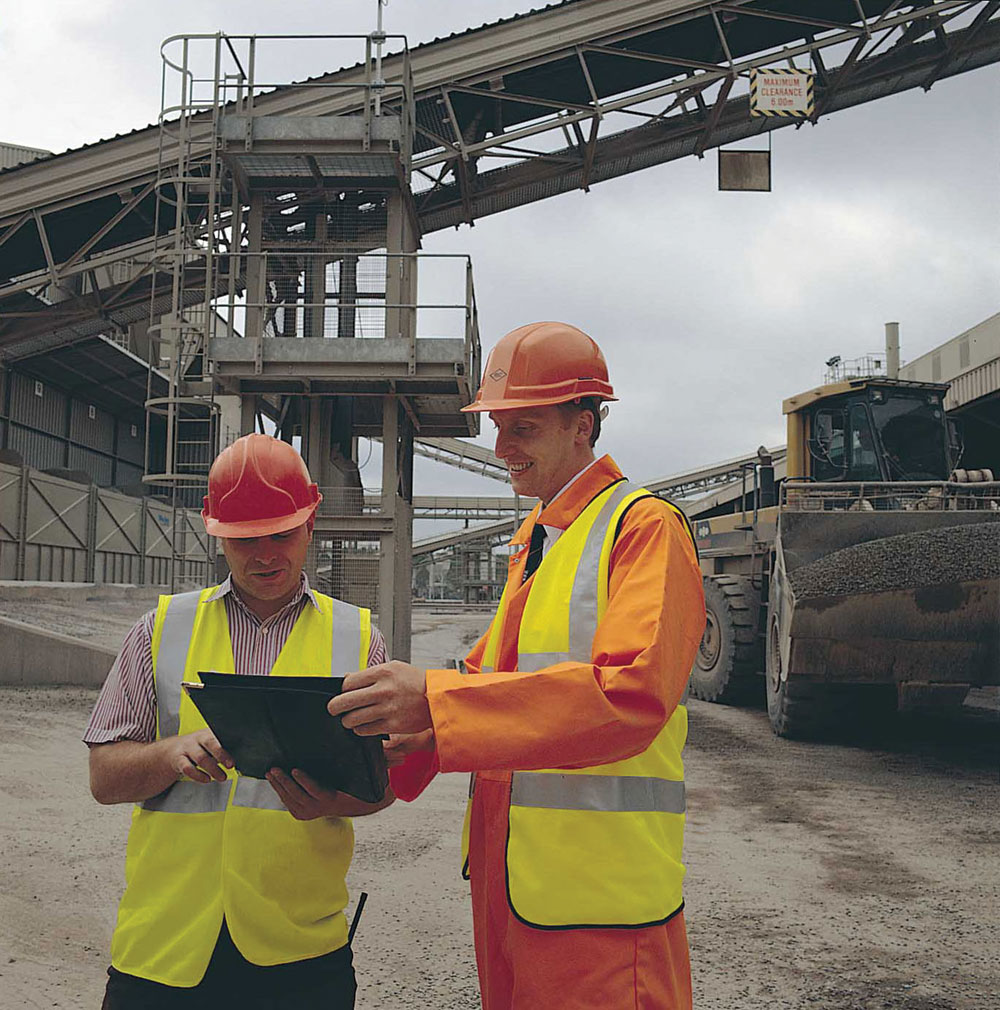
RMC’s international aggregates businesses are half-way through a 4–5-year energy efficiency campaign, which is now showing early positive results. In the next 2–3 years savings are expected to reach £5 million a year
Environmental issues have always been important for quarries, but usually in relation to the local environment. Now, global environmental concerns are becoming increasingly significant, as government initiatives designed to combat climate change begin to make an impact.
The RMC Group, one of the world’s largest building materials companies, with operations in over 27 countries, is responding positively to the challenges and opportunities presented by the Government’s climate change and sustainable development initiatives. Noel Morrin, international environment director for RMC, says: ‘Essentially, our aim is to become more efficient. Our work in improving energy management makes a direct impact on profitability. However, it also helps us to meet environmental targets. The business case for action is clear.’
Mr Morrin is responsible for initiating a far-reaching energy efficiency campaign which has the potential to save individual companies in the RMC Group an aggregated £5 million a year within the next 2–3 years. The scheme began two years ago when Mr Morrin brought in Future Energy Solutions to investigate the potential for saving energy within the Group’s aggregate businesses. The aggregates area of the business was selected for attention because it offered the most potential. Although the cement division is the highest energy-consuming division, the sites are large and energy is already very well managed. Second to the cement division, aggregates account for 20–25% of RMC’s energy bill, spread over 400 sites in 16 countries, many of which are fairly small. These offered the best opportunities for improving energy efficiency.
Future Energy Solutions, previously known as ETSU and part of AEA Technology Environment, were chosen for their unrivalled track record of advising government and industry on how to save energy for over 25 years. Mike Birks, senior consultant with the company, says: ‘For the last 25 years we have been helping companies such as RMC to save energy. Our role is to offer companies independent expert advice. We can identify and prioritize areas for making energy savings – often without the need for great investment. Our clients can then draw on our expertise in developing and implementing strategies to achieve these savings. Training is an important component of this process.’
The campaign started with 14 pilot schemes in seven countries, including sites in the UK, six in the USA and others in Spain, Portugal, Czech Republic, Hungary and Austria. Each pilot project began with a fast-track energy audit, conducted by Future Energy Solutions, to establish the biggest energy-saving opportunities.
Noel Morrin says: ‘Future Energy Solutions conducted classic energy audits for the selected sites, including looking at the management systems. It is worth remembering that the people who use most energy are generally not the ones who pay the bills! We wanted Future Energy Solutions to make the links and then help us with on-site training.’
Future Energy Solutions identified significant energy-saving opportunities. According to Mike Birks, the energy audits were able to identify a range of strategies which could be expected to save RMC in the region of 5–20%. Savings in this range are fairly typical and could be achieved by most companies, he says, so a company with an energy bill of £1 million could be saving up to £200,000 year.
Training
The next stage was to set up an appropriate energy-management structure within RMC. This meant appointing and training on-site energy managers and national co-ordinators to identify and manage energy efficiency. As engineers, they all had technical expertise, but they needed training to focus on energy management. This was initially conducted by Future Energy Solutions at RMC’s UK headquarters and on site internationally, and then followed through by Noel Morrin and his colleagues. Training began by understanding the reasoning behind tackling energy consumption, then focusing on practical measures for saving energy, based on the opportunities found during the energy audits of the sites.
Mike Birks explains: ‘We needed to start by illustrating what can be achieved and why. Often fairly straightforward alterations to common practices, such as shutting off equipment when it is not needed, can have a tangible impact.’ Mr Morrin adds: ‘Ultimately, the campaign is about improving the efficiency of our operations. Saving energy saves money and improves profitability. The majority of savings were associated with transport, with others mainly electrical.’
Mr Morrin also identified the importance of how the scheme was integrated. ‘We had to phase the work into normal operations, and be certain that we did not disrupt normal business,’ he says.
Monitoring and targeting software
The studies identified the need for monitoring and targeting software to be developed. Future Energy Solutions advised on the content of key areas of the software, such as meter management, compressors, drivers and CUSUM analysis, but the software itself was developed in-house by RMC.
‘The software development has been absolutely crucial to our success,’ says Mr Morrin. ‘It has not been expensive to develop, but it has taken time. A great deal of thought and care went into its design, and the input from Future Energy Solutions was invaluable in helping us to target the key issues, but the critical success factor was the specific knowledge of our own industry that was brought to bear by our colleagues. We now have a state-of-the-art monitoring and targeting system which we run on the RMC Group Intranet. Ultimately, every country has access to the system and local languages make it user friendly – this is essential for it to work.’
This last point is particularly important for RMC, which has sites in 27 countries. The software is already available in English, Spanish, German, Czech and Portuguese, and has been designed so that it can be adapted for other languages to be added when new sites are brought into the system. Obviously, workers on site need to be able to use the system in their own language for it to work efficiently.
It has taken the development of complex software to allow for the cumulative effects of small changes to be analysed. To achieve this, it was vital for all sites to agree to weekly reporting, explains Mr Morrin. ‘The frequency of reporting is often monthly, and we had to get all our sites to agree to weekly reporting. Some businesses had been used to daily, others monthly, but we all have to work on the same reporting period to allow for comparisons. We all need to feed in ‘like for like’ data. Each energy centre at each site can then track and check changes to determine their effects.’
‘This can be extremely useful,’ says Mr Morrin. ‘For example, analysis of two sites, that on the face of it look the same, may identify two very different energy profiles. Once these anomalies have been identified, the local management can investigate why they exist and then determine a strategy for tackling them. The key to success is in the software and local knowledge.’
It’s good to share
In June RMC launched a virtual library of good practice, available on the company’s Intranet. This gives energy managers access to good-practice information from other sites, as well as from external sources, including suppliers. Access to this library will prove invaluable to new site energy managers as they join the scheme. As Mr Morrin explains, the library will help energy managers to share their successes. ‘When a new site comes into the scheme, once the energy manager has established his baseline data, he can determine the best strategy for making savings, based on the experiences of other mangers at similar sites –– both within his own country and internationally. The value of the library will increase as new experiences and successes are added.’
Future expansion
RMC are two years into the scheme, with at least another two years to go. According to Mr Morrin, once metering is in place, it can take about six months to establish the baseline data. From this point, energy managers can plan their strategy. ‘Typically, it takes about 12 months to get the point where we can seriously monitor progress,’ he says.
He adds that site energy managers are embracing the scheme with enthusiasm. ‘We have a problem in establishing accurate baseline data at the beginning, but we find that once managers can see how quickly and easily some savings can be made, they start straight away. So some savings are already being made while the baseline data is being established. Of course, this is nothing to complain about but it can lead to an understatement of savings!’
The costs of implementation have not been great, and Mr Morrin is pleased to confirm paybacks in the region of only eight months. ‘We are now at the point of expanding operations within each country, he says. ‘We are just starting a big push in the UK, and in another two years we expect to have a complete uptake on priority aggregate sites.’ By the end of the next two years he expects the individual companies in the RMC Group to be collectively saving £5 million a year.
‘There is one final plus to the scheme,’ he adds. ‘I feel that we are definitely in a win–win situation. Not only are we reaping the rewards of improved efficiency, but we will also be well ahead in terms of our environmental reporting. We are able to track our energy use in a very accurate way and we can use the systems we have installed to help with tracking our carbon dioxide emissions as each type of fuel is logged individually.’
For further information contact Mike Birks at Future Energy Solutions on tel: (01235) 433468, email: Mike.Birks@aeat.co.uk; website: www.future-energy-solutions.com
Alternatively, contact Noel Morrin on tel: (01932) 583097; email: noel.morrin@
rmc-group.com; website: www.rmc-group.com/rmc/env/
Environmental issues have always been important for quarries, but usually in relation to the local environment. Now, global environmental concerns are becoming increasingly significant, as government initiatives designed to combat climate change begin to make an impact.
The RMC Group, one of the world’s largest building materials companies, with operations in over 27 countries, is responding positively to the challenges and opportunities presented by the Government’s climate change and sustainable development initiatives. Noel Morrin, international environment director for RMC, says: ‘Essentially, our aim is to become more efficient. Our work in improving energy management makes a direct impact on profitability. However, it also helps us to meet environmental targets. The business case for action is clear.’
Mr Morrin is responsible for initiating a far-reaching energy efficiency campaign which has the potential to save individual companies in the RMC Group an aggregated £5 million a year within the next 2–3 years. The scheme began two years ago when Mr Morrin brought in Future Energy Solutions to investigate the potential for saving energy within the Group’s aggregate businesses. The aggregates area of the business was selected for attention because it offered the most potential. Although the cement division is the highest energy-consuming division, the sites are large and energy is already very well managed. Second to the cement division, aggregates account for 20–25% of RMC’s energy bill, spread over 400 sites in 16 countries, many of which are fairly small. These offered the best opportunities for improving energy efficiency.
Future Energy Solutions, previously known as ETSU and part of AEA Technology Environment, were chosen for their unrivalled track record of advising government and industry on how to save energy for over 25 years. Mike Birks, senior consultant with the company, says: ‘For the last 25 years we have been helping companies such as RMC to save energy. Our role is to offer companies independent expert advice. We can identify and prioritize areas for making energy savings – often without the need for great investment. Our clients can then draw on our expertise in developing and implementing strategies to achieve these savings. Training is an important component of this process.’
The campaign started with 14 pilot schemes in seven countries, including sites in the UK, six in the USA and others in Spain, Portugal, Czech Republic, Hungary and Austria. Each pilot project began with a fast-track energy audit, conducted by Future Energy Solutions, to establish the biggest energy-saving opportunities.
Noel Morrin says: ‘Future Energy Solutions conducted classic energy audits for the selected sites, including looking at the management systems. It is worth remembering that the people who use most energy are generally not the ones who pay the bills! We wanted Future Energy Solutions to make the links and then help us with on-site training.’
Future Energy Solutions identified significant energy-saving opportunities. According to Mike Birks, the energy audits were able to identify a range of strategies which could be expected to save RMC in the region of 5–20%. Savings in this range are fairly typical and could be achieved by most companies, he says, so a company with an energy bill of £1 million could be saving up to £200,000 year.
Training
The next stage was to set up an appropriate energy-management structure within RMC. This meant appointing and training on-site energy managers and national co-ordinators to identify and manage energy efficiency. As engineers, they all had technical expertise, but they needed training to focus on energy management. This was initially conducted by Future Energy Solutions at RMC’s UK headquarters and on site internationally, and then followed through by Noel Morrin and his colleagues. Training began by understanding the reasoning behind tackling energy consumption, then focusing on practical measures for saving energy, based on the opportunities found during the energy audits of the sites.
Mike Birks explains: ‘We needed to start by illustrating what can be achieved and why. Often fairly straightforward alterations to common practices, such as shutting off equipment when it is not needed, can have a tangible impact.’ Mr Morrin adds: ‘Ultimately, the campaign is about improving the efficiency of our operations. Saving energy saves money and improves profitability. The majority of savings were associated with transport, with others mainly electrical.’
Mr Morrin also identified the importance of how the scheme was integrated. ‘We had to phase the work into normal operations, and be certain that we did not disrupt normal business,’ he says.
Monitoring and targeting software
The studies identified the need for monitoring and targeting software to be developed. Future Energy Solutions advised on the content of key areas of the software, such as meter management, compressors, drivers and CUSUM analysis, but the software itself was developed in-house by RMC.
‘The software development has been absolutely crucial to our success,’ says Mr Morrin. ‘It has not been expensive to develop, but it has taken time. A great deal of thought and care went into its design, and the input from Future Energy Solutions was invaluable in helping us to target the key issues, but the critical success factor was the specific knowledge of our own industry that was brought to bear by our colleagues. We now have a state-of-the-art monitoring and targeting system which we run on the RMC Group Intranet. Ultimately, every country has access to the system and local languages make it user friendly – this is essential for it to work.’
This last point is particularly important for RMC, which has sites in 27 countries. The software is already available in English, Spanish, German, Czech and Portuguese, and has been designed so that it can be adapted for other languages to be added when new sites are brought into the system. Obviously, workers on site need to be able to use the system in their own language for it to work efficiently.
It has taken the development of complex software to allow for the cumulative effects of small changes to be analysed. To achieve this, it was vital for all sites to agree to weekly reporting, explains Mr Morrin. ‘The frequency of reporting is often monthly, and we had to get all our sites to agree to weekly reporting. Some businesses had been used to daily, others monthly, but we all have to work on the same reporting period to allow for comparisons. We all need to feed in ‘like for like’ data. Each energy centre at each site can then track and check changes to determine their effects.’
‘This can be extremely useful,’ says Mr Morrin. ‘For example, analysis of two sites, that on the face of it look the same, may identify two very different energy profiles. Once these anomalies have been identified, the local management can investigate why they exist and then determine a strategy for tackling them. The key to success is in the software and local knowledge.’
It’s good to share
In June RMC launched a virtual library of good practice, available on the company’s Intranet. This gives energy managers access to good-practice information from other sites, as well as from external sources, including suppliers. Access to this library will prove invaluable to new site energy managers as they join the scheme. As Mr Morrin explains, the library will help energy managers to share their successes. ‘When a new site comes into the scheme, once the energy manager has established his baseline data, he can determine the best strategy for making savings, based on the experiences of other mangers at similar sites –– both within his own country and internationally. The value of the library will increase as new experiences and successes are added.’
Future expansion
RMC are two years into the scheme, with at least another two years to go. According to Mr Morrin, once metering is in place, it can take about six months to establish the baseline data. From this point, energy managers can plan their strategy. ‘Typically, it takes about 12 months to get the point where we can seriously monitor progress,’ he says.
He adds that site energy managers are embracing the scheme with enthusiasm. ‘We have a problem in establishing accurate baseline data at the beginning, but we find that once managers can see how quickly and easily some savings can be made, they start straight away. So some savings are already being made while the baseline data is being established. Of course, this is nothing to complain about but it can lead to an understatement of savings!’
The costs of implementation have not been great, and Mr Morrin is pleased to confirm paybacks in the region of only eight months. ‘We are now at the point of expanding operations within each country, he says. ‘We are just starting a big push in the UK, and in another two years we expect to have a complete uptake on priority aggregate sites.’ By the end of the next two years he expects the individual companies in the RMC Group to be collectively saving £5 million a year.
‘There is one final plus to the scheme,’ he adds. ‘I feel that we are definitely in a win–win situation. Not only are we reaping the rewards of improved efficiency, but we will also be well ahead in terms of our environmental reporting. We are able to track our energy use in a very accurate way and we can use the systems we have installed to help with tracking our carbon dioxide emissions as each type of fuel is logged individually.’
For further information contact Mike Birks at Future Energy Solutions on tel: (01235) 433468, email: Mike.Birks@aeat.co.uk; website: www.future-energy-solutions.com
Alternatively, contact Noel Morrin on tel: (01932) 583097; email: noel.morrin@
rmc-group.com; website: www.rmc-group.com/rmc/env/