Dust Control
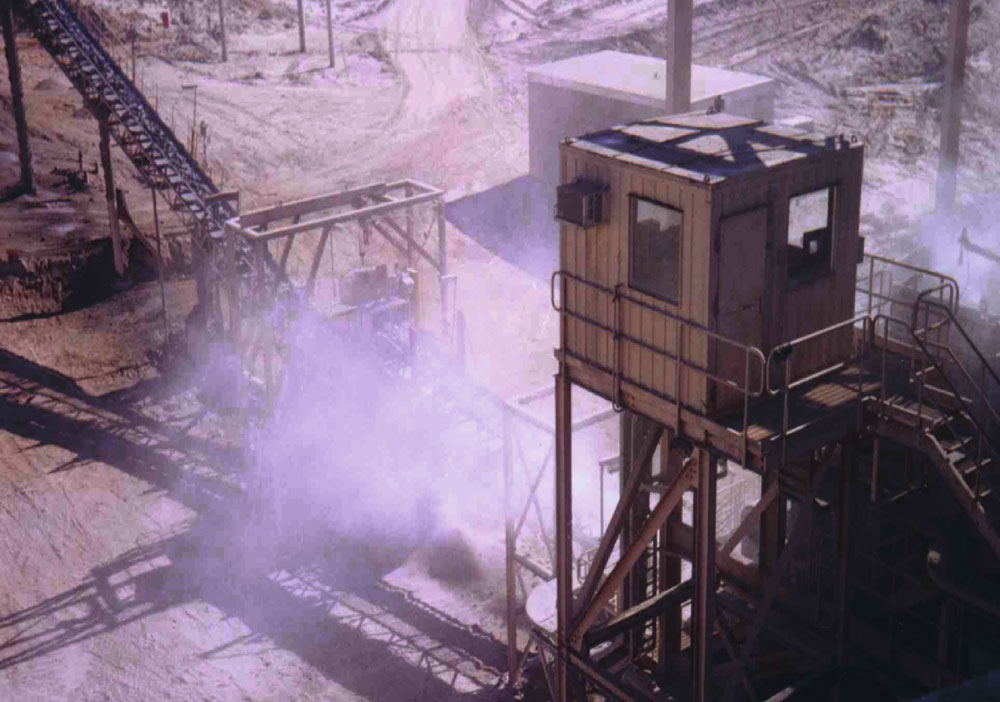
DustFoam — a solution to the problems associated with fugitive dust
When a mineral product is extracted, crushed, screened or handled small particles, generally below 75 microns in size, are released into the surrounding environment.?The heavier particles, generally above 20 microns, settle out in the vicinity of the emission source.?Wind and air disturbance can influence settlement.?Particles less than 20 microns in size can move around with the air currents and may remain suspended for long periods of time, while in still air conditions they will eventually settle out. Fine particles below 10 microns are normally not visible individually and it is this fraction that is referred to as airborne dust.
Airborne dust is a nuisance and/or hazardous to health depending on its chemical composition.?In the minerals extraction industry products containing silica or lead normally represent the main health hazard.?Particles below 5 microns are normally not collected in the nose or in the mucous of the mouth but pass directly to the lungs.?This can build up in the lungs causing chronic diseases such as silicosis and pneumoconiosis.
Legislation in most parts of the world sets limits for the control of dust to atmosphere from plant and exhaust stacks, and the control of dust inhaled by operators.?For silica oxide (free silica), this can be as low as 0.1mg/Nm3 in the respirable range. The effects of respirable dust can be mitigated to some extent by wearing the correct PPE equipment appropriate to the health hazard.
The handling of materials containing harmful elements and dusts that give rise to high atmospheric emission levels therefore requires special consideration in relation to plant design, including the need to remove operators away from the working process wherever possible. Experience shows that, if allowed, a number of process designers ignore dust control in their plant philosophy so as to keep the capital cost below a perceived budget.?In such cases, when the plant starts operating it is often the case that dust emissions become unacceptable and expensive modifications, such as sealing and/or retrofitting of dust-control methods, become necessary.?This scenario is often the most expensive solution and can result in confrontation with local government authorities and/or damaged relationships with neighbours. Moreover, this initial impression may be difficult to eradicate.
As part of any dust-control solution, sealing and containment are usually essential requirements, together with either dust suppression or dust extraction, or a combination of both.
SEALING AND CONTAINMENT
Fines generated by bulk products generally do not present a problem until they become airborne and/or settle in large amounts around the process plant.?The plant design should be examined carefully to minimize the release of dust to atmosphere and to prevent spillages. Where practical, it is important that:
- Product is not allowed to fall freely from the head of a stocking-out conveyor, particularly when this process is outside and involves a fall from a considerable height.
- Product is not allowed to transfer down open chutes, particularly where there is more than 1m of elevation involved.
- Product is not allowed to become too dry;?this increases dust release.
- Product is screened in a logical manner so that the fines are taken out first rather than last.
- Product is not allowed to free-fall into trucks or rail wagons, particularly where this is carried out in the open and subject to windage.
When considering sealing and containment, the following points should be borne in mind:
- Conveyors should normally be enclosed if they are outside and subject to windage.
- Feed chutes should be sealed into the skirted area of the receiving conveyor (with at least 3m of skirting).
- Where practical, the entire process plant should be installed inside buildings to reduce windage effect and to contain as much of the dust as possible – this reduces neighbour complaints but can cause higher dust emissions within the buildings.
- Install the most effective belt scrapers if there is a tendency for fine product to return on the understrand of the conveyor or where the product has a high moisture content.?Conveyor belts can be responsible for shedding considerable amounts of dust into the atmosphere adjacent to each return idler and also contribute to spillage.?If possible, the scraper manufacturer should service the belt scrapers on a regular basis.
- Where possible, stocking-out conveyors should be of the ‘luffing’ type so as to reduce product free fall.?Alternatively, the stockpile should be maintained as high as possible, again to reduce free fall particularly when exposed to high-wind conditions.?Various dust-control chutes are also available, eg the Didcot chute, which hangs vertically from the conveyor head to the ground and has a number of staggered apertures sealed by self-opening neoprene sheeting. Product falls down the chute and exits through the appropriate opening depending on the height of the stockpile, thereby reducing the open fall of materials in free air (not suitable for use where the product is not free-flowing).
- Screens should be encapsulated and sealed into the underpan where possible.
- Flooring in screen houses should normally be solid and sealed into the screen underpans to prevent the release of dust from the bins into the main screening area.??
Although sealing and containment will reduce the release of dust to atmosphere and may be regarded as good design practice, there are many cases where this is not adequate and further dust-attenuation measures have to be considered. Such measures are often demanded by the environmental agencies as a condition of planning consent.
Dust attenuation comes in various forms, including:
- Dust-extraction and collection systems.
- Dust suppression using water only.
- Dust suppression using water and surfactant.
- Foam suppression using a foaming product and a small amount of water.
- Fog systems, whereby compressed-air nozzles produce a fine mist that agglomerates fine dust already released and allows it to fall back into the product.
DUST SUPPRESSION
This remainder of this paper explores dust-suppression techniques. Quite often in the past such systems were:
- badly designed and applied
- the cause of screen blinding due to excess moisture addition
- poorly maintained and controlled
- subject to frost damage
- removed to gain access to plant and not recommissioned
- not able to achieve adequate dust reduction.
Such problems have led to a general ‘loss of faith’ in standard water-only or water plus surfactant systems. Such systems continue to be used, however, as they represent a cheap cosmetic solution to the problem of dust control. The result is poor neighbour relationships (with implications for future planning extensions), poor operator working conditions, excess maintenance expenditure, and high water demand.
Properly designed and maintained foam systems, however, represent a considerable leap forward from the ‘normal’ wet suppression system and, in general, will outperform water/surfactant systems.
Overview of ‘wet’ dust suppression
When minerals such as aggregates, coal, iron ore etc are handled through conveyors, crushers, screens and various other dry processes, dust is released — the amount generally depending on the level of moisture present in the product, the product grading and the degree of disturbance the material is subjected to. If the process is carried out within buildings the dust released can cause serious contamination and produce a hostile environment for other engineering equipment to operate in, ie electric motors, gear boxes, compressors etc. Such buildings need to be cleaned out on a frequent basis. In addition to the labour this involves, some materials can be hazardous to health as defined by the COSHH regulations. Dust spillage of this kind has to be removed by operators wearing protective clothing, masks, breathing apparatus etc. Enclosing the process reduces the release of dust to the atmosphere but does not eliminate it, and personnel generally cannot work within the buildings during processing.
If the process is not ‘contained’ and the plant is situated on an open site the dust will be released to atmosphere. This may be deposited locally around the process plant but will also blow in the wind and contaminate the surrounding areas. It may well infringe the environmental rules for fugitive dust both within and outside the site boundary.
The addition of moisture to minerals being processed has been carried out for many years and can considerably reduce dust nuisance during handling. Water is added to the process mainly through the use of atomizing sprays. On some better-engineered systems, the water can be automatically shut off to parts of the plant that are not operating by using process signals and solenoid valves. Sometimes the mineral being handled repels water, making it difficult, using a water-only system, for the water to be absorbed by the finer fraction of the product, which is the main contributor to dust release. This is sometimes overcome by adding more water up to 3–5%, but this amount often cannot be tolerated. To help overcome this difficulty surfactants are used to reduce the surface tension of the water, making it easier to coat the mineral and reducing the amount of water used. Surfactants can reduce water consumption to 0.5–2%.
In instances where there is a shortage of water or where there is a limit to the amount of moisture that can be added, eg if the product is to be fine screened where the minimum mesh size is below 4mm, moisture contents above 1–2% can cause ‘blinding’ of the screens, seriously impairing screening efficiency. There are other mineral products where it is important to keep the added moisture content down, eg coal being fed to boilers or aggregate feed to asphalt plants, where ‘free flow’ characteristics are important, as are the costs related to driving off moisture. This again limits the amount of water that can be added as a dust-suppression agent.
It should be noted that the moisture percentage is calculated on the maximum flow rate of the product. If the feed rate varies then the percentage of moisture varies, ie 1% moisture at maximum demand equals 2% moisture at 50% design rate.
DUSTFOAM TECHNIQUE
To help overcome most of the above problems and also to improve the degree of dust control achieved, special foaming agents have been developed. Dust foam is produced at source by the controlled introduction of water and compressed air into a foaming chamber. This chamber creates micro-bubbles that can be applied to strategic parts of the process where the majority of dust is generated. The micro-bubbles need to have a high degree of stability, ie they should not break up when sprayed into the aggregate material being handled and they should maintain their shape until they enter the crusher, transfer point etc, whereupon they ‘burst’ causing the moisture they contain to be integrated within the product. Many foams are available today but it is the author’s opinion that DustFoam - a patented product manufactured by US firm Nalco – is the best product currently available by virtue of its micro-bubble stability. HW Enviroflo Engineering Ltd have the sole rights to use this foam in the UK and Ireland and other designated areas of the world. Cheaper foams are available but these normally require more foaming agent to produce a similar effect, which can be more costly overall. If DustFoam is applied to one application point it can have a considerable ‘carryover’ effect to other parts of the process.
As a general rule, one litre of DustFoam mixed with 99 litres of water will produce some 5,000 litres of foam that can be added directly to the process. This equates to 0.1% of moisture. On low-tonnage applications this can increase to 0.15%. Moisture with foam solution ranging from 0.6–0.75% water to foam ratio is the norm. A system may also run below these values but this can only be decided on site during commissioning, depending on the mineral being handled, the locations of application points, degree of sealing etc.
It can be seen, therefore, that the use of ‘foam’ dust-suppression systems requires considerably less water than conventional water or water and surfactant systems. Nalco DustFoam is a totally inert organic material and has no detrimental effects on watercourses, cement manufacturing processes, bitumen coating process etc, and a material safety data sheet is available in line with COSHH requirements.
DustFoam equipment
A typical Enviroflo/Nalco foam system comprises four major assemblies:
- Proportional feeder (cabinet mounted).
- Control module (cabinet mounted).
- Foam expansion chamber, which can be located adjacent to the above items or mounted remotely on the process plant adjacent to the point(s) of application.
- Electrical control panel.
Proportional module
The proportional module controls a specialized metering pump that maintains a constant ratio of DustFoam product to water throughput; this ratio stays constant even if the rate of water flow changes. The proportional feeder does not need a power supply to function as the pump is driven by the inflow of water. An in-line pressure regulator is installed ahead of the proportional feeder and the complete assembly is housed inside a metal enclosure, which is normally wall mounted and features a hinged door. A plastic tube from the bottom of the module passes through a hole in the base of the enclosure and into the DustFoam container below. The DustFoam product is induced up the pipe and into the feeder. A level switch can be fitted to send an alarm signal to the PLC when the container of foam reaches a low level.
Control module
The control module regulates and controls the following: compressed air pressure – approximately 60psi (4.13 bar) is normal; and compressed air flow rate – approximately 60–100cfm is required (1.7–2.8m3/min).
The module is configured and interfaced with a remote sensor for switching the system on and off corresponding to whether material is flowing through the particular part of the process that it serves, eg if a crusher is being treated then an electrical signal can be provided by a current-sensing relay linked to the motor current indicating if it is ‘on’ or ‘off’ load. Signals can also be taken from belt weighers, feeders, conveyors and other parts of the process to ensure that the foam is not applied to parts of the plant that are not in operation (PLC’s can be programmed to provide the switching signals necessary).
This module also contains a flow indicator for the water and DustFoam solution and a flow indicator for the compressed air. The compressed-air line incorporates an airflow regulator and an automatic shut-off valve complete with a pneumatic actuator ‘spring return’ controlled by a 110V single-acting solenoid. The water and DustFoam solution line has a globe valve to control the flow. A flow meter, an automatic valve complete with pneumatic actuator and solenoid, as per the above, and a non-return valve are also present. These valves and meters are used to commission the system and should normally be left in this position, assuming there is no change in the process.
An additional feature is normally added to the control module whereby compressed air is introduced into the outlet side of the water and DustFoam circuit in order to clear the lines downstream to the points of application. Known as the purge system, this prevents the lines from freezing and also removes the recently manufactured foam from the lines, as this will turn into a liquid after a number of hours. At process start-up new foam is introduced into the application lines (the process will not restart until the purge system has completed its task).
The above equipment is mounted in a suitably sized cabinet complete with a hinged door and arranged for wall mounting.
Foam expansion chamber
The foam expansion chamber is where the air, DustFoam product and water mixture interacts and expands to create the foam. From this chamber the foam is distributed via a number of identical-length hoses. Fitted with special spray nozzles, the hoses are located in strategic positions associated with the particular application point in question. On a crusher, for example, the nozzles will be directed towards the incoming material at the crusher inlet. Nozzles will also be located at strategic points associated with the crusher outlet. If possible, the top and underside of the material should be sprayed; this is best achieved when the material is in free fall on the outlet side of the crusher or at a conveyor transfer point etc. The expansion chamber can be mounted adjacent to the application point. A remote compressed-air line and a separate remote water and DustFoam solution line pass from the control module to the expansion chamber mounted on the plant. A typical foam chamber has two inlet connections and typically five outlet connections. The foam chamber is variable in size depending on the size of the application, ie the amount of water/DustFoam solution to be imparted to the process.
A proportional module and an expansion chamber are required for each application point. If there are two application points relatively close together, the proportional feeder can be used to serve two control modules, assuming they run together and maintain the same material flow rate.
DustFoam equipment, specifically the DustFoam product, proportional module, control module and inlet water supply, must be protected from freezing (DustFoam product is normally stored in 1,000-litre IBC containers and freezes at about 0°C). Equipment must be mounted within a building that always remains above zero degrees. If no suitable?building is available, the best solution is to fit all the equipment into a shipping container – this often houses the air compressor. The container is insulated, lined and heated (if necessary) and fitted with lighting. Equipment arrives on site prepared, wired and ready to receive site services of water and electrical (or sometimes hydraulic) power.
DustFoam system advantages/disadvantages
The DustFoam system offers a number of advantages including:
- Minimum water usage (0.1–0.15%).
- Does not blind fine screens or block chutes.
- Highly effective.
- Low maintenance.
- Improves wetting ability of water.
- Relatively low capital cost.
- Improves relationship with neighbours.
- Better working conditions for operators.
- Can replace bag-filter equipment.
DustFoam systems are, however, more expensive to run than standard water systems (though not when compared with dust-extraction methods) and require more energy to operate, mainly due to compressed-air requirements.
DUSTFOAM PERFORMANCE
Various tests have been carried out (mainly in the US) on the attenuation of dust when DustFoam is applied. One of these tests is summarized in the accompanying graph and is typical of findings by HW Enviroflo Engineering Ltd.
The author, Harold Wylie, is chairman and managing director of HW Enviroflo Engineering Ltd