Bomag Soil Stabilizers help deliver urban renewal
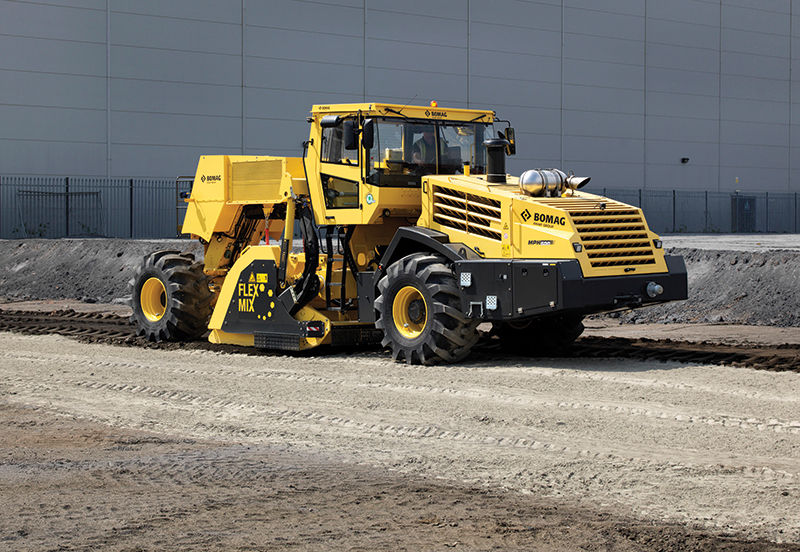
First published in the October 2015 issue of Quarry Management as Flexible Solution
Independent Stabilization Co. Ltd’s two new Bomag MPH 600 soil stabilizers help deliver urban renewal across the country
The Independent Stabilisation Co. Ltd have taken delivery of two new Bomag MPH 600 soil stabilizers – the first of which was delivered to a redevelopment site in Oxford in March this year. The second machine has recently been supplied and put straight to work at The Hub – a new business/industrial site in Birmingham where it provided the soil stabilization of a sub-base for a warehouse development.
Soil stabilization is the process of creating a controlled fill drying method which ensures soil is at the correct moisture content to achieve maximum compaction. And according to Bomag, stabilizing with lime, cement or other binders, is an extremely cost-effective method of converting weak soils into a usable and environmentally sound construction material.
The 28-tonne MPH 600 unit has been specially designed to tackle the toughest soil stabilization jobs with outputs of between 3,000 and 5,000m3 per day. Powered by a Stage IIIB-compliant, eight-cylinder Deutz engine (440kW), the machine features hydrostatic all-wheel drive for enhanced controllability and utilizes Flexmix technology for optimized performance.
The soil stabilizer is also equipped with Bomag’s BRS 05 quick-change holder system, offering reduced costs and rapid change times in difficult site conditions. It features a contamination-resistant design for easy handling and highly wear-resistant steel for long service life.
In milling mode, the rotor speed has 11 settings which means that tool and rotor wear are kept to a minimum. For improved reliability, a rotor drive automatic overload protection system provides high machine availability under severe conditions.
Specially designed with the operator in mind, Bomag have prioritized a workplace environment that provides the highest comfort in the toughest applications. For added safety, the height-adjustable ROPS cab offers greater visibility, thanks to a well-positioned seat and large glass frontage providing an optimum view of the site and operation.
The job at The Hub project started with a Bomag 12000 towed binder spreader being utilized to lay down a cement cover on the soil base. The MPH 600 soil stabilizer was then used to mix the cement with the soil in situ.
The stabilization of the available on-site materials, say Bomag, allows construction to be carried out cost-effectively, rapidly and with less environmental impact. Off-site disposal can be reduced to zero and the importation of expensive aggregate is greatly reduced. The on-site mixed material at The Hub development was compacted using a Bomag smooth drum self-propelled roller.
Commenting on the purchase of the MPH 600 soil stabilizers, John Bateman of The Independent Stabilisation Co., said: ‘The new-generation of Bomag machines are second to none in terms of performance and reliability. The first Bomag machine we bought was an MPH 100, but the industry and the company have come a long way since then. These new machines have significantly improved ergonomics and environmental features. Bomag have certainly listened to their customer needs and demands over the years.’
For more information visit: www.bomag.com
- Subscribe to Quarry Management, the monthly journal for the mineral products industry, to read articles before they appear on Agg-Net.com