Training with a Return on Investment
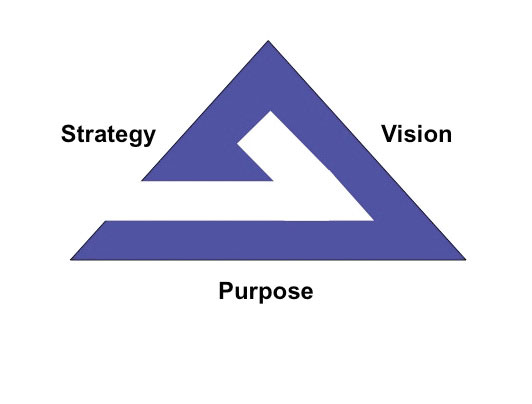
By Hefin Jones, operational training & competency manager, Aggregate Industries
Considering the difficult trading conditions that all construction materials suppliers find themselves in, a considerable amount of training is still being undertaken. Aggregate Industries are no different in this respect, in that one of their primary objectives is ‘preparing for the mid-term’, ie a focus on ensuring that the company has the right calibre of people in place to react to a recovery while prolonging growth through sustainability.
This paper outlines, primarily, one approach within Aggregate Industries which demonstrates that training can bring about not only the desired improvements in workforce knowledge and performance, but also a financial return on investment (RoI) if the training is approached appropriately.
In taking this approach, there are three questions that need to be addressed:
- What is Aggregate Industries’ training vision?
- What is the real purpose of training?
- What is the company’s strategy?
These are represented on the company’s Training Triangle (fig 1):
Aggregate Industries’ ‘vision’ is to achieve social and financial improvements, together with compliance, while focusing on the mid-term.
The company’s ‘purpose’ is to achieve Zero Harm, upskill its workforce, and achieve compliance by having a competent workforce.
The ‘strategy’ for achieving this involved identifying the company’s resources, budgeting finances and/or funding support, and securing buy-in from the business through the support of a director to ‘champion’ the training initiative.
Industry training focus
The extractive and mineral processing industry has, quite rightly, focused on legislative compliance training, this being supported by industry groups such as the Mineral Products Association (MPA), the Institute of Quarrying (IoQ), the British Aggregates Association (BAA), Proskills and the Mineral Products Qualification Council (MPQC). This has contributed to recognition, by the Health and Safety Executive, of the industry’s improved health and safety standards and performance. While everyone agrees that there is further work to be done to achieve the goal of ‘zero harm’, and to maintain that standard, training should not be focused solely on compliance.
Economic climate
There are challenging times ahead with constraints on expenditure. As with all business functions, training will need to be justified in terms of quantifiable RoI. Aggregate Industries recognized that there were opportunities for integrated training initiatives that were not exclusive to health, safety and environmental issues. These initiatives would align with the company’s Training Triangle model while encompassing both knowledge training and performance assessment within an emerging accredited qualification framework.
Qualification and Credit Framework (QCF)
QCF is the new format of assessment qualifications in England, Wales and Northern Ireland. The QCF replaces the National Qualification Framework (NQF), the framework on which NVQs were accredited, as the new standard of vocational qualifications. Scotland has its own new framework, the SCQF – Scottish Credit and Qualifications Framework.
It should be emphasized that currently held NVQs will still be valid as a way of confirming competence to the standards required in an occupational role, and that there will be no need to upgrade to a QCF provided that the holder continues to be engaged in a similar role where the relevant standards’ requirements remain unchanged.
QCF structure
- Unlike NVQs, QCFs are structured as building blocks known as ‘units’
- Units can be combined together through ‘Rules of Combination’ (RoC) to form a qualification
- A qualification can be structured to have mandatory units, optional units and additional units
- Pathways can be created to accommodate varying activities
- Qualifications have levels, size and credit values.
Training to meet the challenge
The Strategy for Sustainable Construction (SSC) brought to the fore the future intentions of government and set challenging targets. Aggregate Industries recognized the need to upskill their operational staff to meet these challenges. This need appeared greater within the company’s added-value businesses, which have high-impact manufacturing processes.
Interpreting the strategy for SSC
Interpretation of the SSC into its various categories identified the need not only to train and assess higher health and safety standards, but also:
- site efficiencies which improve plant operation
- production plant understanding
- relevance of plant maintenance to reduce breakdowns
- product quality and technical appreciation
- environmental impact and issues
- energy and carbon management
- customer expectation and satisfaction.
Qualification development
The following example demonstrates Aggregate Industries’ approach to training with a return on investment. The company decided to develop its own employer-led qualifications within the QCF. Following extensive consultation with operational and commercial staff, the Operational Training & Competency team structured three QCF qualifications under the ‘Asphalt Business Improvement’ banner.
- MPQC Level 1 Diploma in Asphalt Production in the Extractive & Mineral Processing Industry (QCF) – valued at 60 credits. This qualification was intended for new starters in the asphalt production business or for use within an apprenticeship framework.
- MPQC Level 2 Diploma in Asphalt Production in the Extractive & Mineral Processing Industry (QCF) – valued at 96 credits. A qualification structured around an asphalt plant operative who has a reasonable amount of production experience.
- MPQC Level 4 Diploma in Asphalt Production in the Extractive & Mineral Processing Industry (QCF) – valued at 151 credits. A high-level qualification suitable for supervisory staff and developing managerial staff with many years of asphalt production experience.
There are around 50 or more mandatory units plus optional units within each of the qualifications. Two pathways have been created to accommodate batch plants and continuous drum-mix plants. The individual units are structured to reflect the requirements within the Strategy for Sustainable Construction (SSC).
Accreditation
Having written the qualification units and their Rules of Combination, and consulted with the awarding organization and extractive and minerals processing industry (E&MPI) stakeholders, the task of accrediting the qualification consisted of a number of stages:
- Approval by Proskills, the Sector Skills Council for the E&MPI, through its Qualification Reform Group
- Endorsement by the E&MPI board
- Accreditation by the E&MPI’s awarding organization, the Mineral Products Qualification Council (MPQC)
- Acceptance by Ofqual, the Office of Qualifications and Examinations Regulation, and uploading on to their database.
These Aggregate Industries-developed QCF qualifications are of an ‘open’ status and are available to all employers and training providers for delivery.
Customer expectation
The way in which the industry’s customers measure product quality and performance has changed considerably in recent years. One example is the way the Highways Agency stipulates pavement quality not at the point of delivery and laying, but in the durability of the finished product in situ against contracted parameters (figs 3 & 4).
In order to demonstrate the association between customer expectations and the qualifications that have been developed, the following example looks at a specific unit that evaluates the operative’s (the learner) appreciation of the significance of producing the material to the correct quality standard.
The example considers a 20-tonne load of delivered asphalt which has been produced incorrectly. Binder separation has occurred (fig. 5), which may have been caused by a number of factors ranging from the moisture content of the aggregate to excess binder. Whatever the cause, it can be classified as a process failure by a member of the plant workforce who failed to appreciate the significance of overheating aggregates during the drying process or through the addition of excess binder.
In general terms, the cost implications of this failure can be quantified as follows:
- Return haulage - £3.50/tonne
- Original haulage - £7.00/tonne
- Stone - £15.00/tonne
- Bitumen - £30.00/tonne
- Electricity - £0.40/tonne
- Process fuel - £4.00/tonne
- Fuel taxation - £0.37/tonne
- R&M/labour costs - £3.00/tonne
- Total - £63.27/tonne
For a 20-tonne load this equates to £1,265, but there can also be costly remedial work, such as the cost of lifting and removing faulty material, delays, financial penalties, loss of reputation, legal action, loss of future business, not to mention additional costs relating to the lifting of sports arena and tennis court surfaces that may have been treated or painted.
QCF assessment process
The following are other examples of how the assessment process evaluates the standard achieved by the plant operator (the learner) and identifies gaps in knowledge or performance that need to be addressed.
All QCF units have been written in such a way that they define:
a. Learning outcomes – what the learner will be able to demonstrate in terms of knowledge or performance within the requirement standard.
b. Assessment criteria – what the learner can demonstrate through his/her acquired knowledge or through performance demonstration.
Example 1
Extract from ‘Housekeeping & Spillages Unit’
Learning outcome:
- Understand the need to control spillage
Assessment criteria:
- Explain the causes of spillage
- Describe the adopted practices that limit the occurrence of spillage
Expected learner response:
The learning outcome can be both knowledge and performance based where the learner can demonstrate his/her knowledge by verbally outlining the causes and practices or, alternatively, by demonstrating practices and examples around the plant area. An example of this is highlighted in fig. 6.
Example 2
Extract from ‘Asphalt Plant Operation Unit’
Learning outcome:
- Be able to carry out a plant shutdown using the plant PC
Assessment criteria:
- Perform a normal shutdown operation
Expected learner response:
In addition to demonstrating how a systematic shutdown of the plant is performed, the learner would be expected to highlight that lack of attention during shutdown can lead to costly downtime, as failure to complete certain key tasks will lead to start-up problems the following day. Examples could include periodic greasing, spillage clearance so overnight freezing does not prevent conveyor start-up, clearing bitumen lines and applying skip-release agent (figs 7, 8 & 9).
Example 3
Assessment of operatives will inevitably highlight shortfalls and so remedial training will need to be undertaken. An example of the effectiveness of this approach can be linked to the unit entitled: ‘Operation of the Burner in Asphalt Production’ (fig. 10).
As can be seen from the standard of the assessment criterion, there are some demanding requirements that need to be demonstrated. Delivery of this unit at one of Aggregate Industries’ sites highlighted training requirements for the staff and these were duly undertaken. Evaluation of overall equipment effectiveness (OEE) data over the following months revealed the following potential savings:
- Average fuel cost of £0.50/litre
- Consumption reduced from 14 to 12 litres per tonne over preceding three months following assessment and training
- A saving of 2 litres/tonne = £1.00/tonne
- Over the plant’s budgeted output of 50,000 tonnes/annum, this represents a saving/ cost reduction of £50,000.
Example 4
Another vital item of plant with considerable operating cost implications is the filtration system. The unit entitled ‘Operation of the Filtration System in Asphalt Production’ covers this equipment (fig. 13).
The unit assessment criteria requires the learner to:
- Describe the features of an efficient filtration system
The learner will need to have a thorough understanding of the working of this item of plant and be able to appreciate that the effects of abnormal or high filtration system pressure can lead to:
- reduced production rate
- electricity consumption increase
- fuel usage increase
- impact on material quality
- damaged filter bags
- remedial downtime
- environmental discharge issues
- confined space access issues.
Operational staff who fail to appreciate these effects could be adding thousands of pounds to the running costs of a site, reducing throughput, increasing operative health and safety risk factors, and jeopardising environmental conditions.
Qualification delivery
To aid the delivery of the qualifications, a modular training workbook was written for each of the levels. The workbooks were designed not only to impart knowledge to the learners, but also to serve as a means of capturing knowledge evidence through a question section at the end of each unit.
The assessments are undertaken in house by ex-asphalt plant managers who are able to demonstrate ‘occupational competence’ in the qualification subjects to MPQC – the awarding organization and external verifier for the qualifications. The qualifications are run through Aggregate Industries’ NVQ/QCF Centre with an in-company internal verifier.
Expanding the principle
Aggregate Industries have also developed similar QCF qualifications for their ready-mixed concrete operations – a Level 2 for plant operatives/batchers and a Level 4 for supervisory and operational managers.
- MPQC Level 2 Diploma in Ready Mixed Concrete Production (QCF) – 91 credits
- MPQC Level 4 Diploma in Ready Mixed Concrete Production (QCF) – 137 credits
These qualifications are also of an ‘open’ status and are available to all employers and training providers for delivery.
Further ROI initiatives
In conjunction with Ashorne Hill Management College, a management-development programme (MDP) has been established to deliver management excellence for Aggregate Industries’ first-line managers in all business sectors. Participating employees gain a CMI Level 3 Certificate in First Line Management (QCF) from the Chartered Management Institute on this year-long course, which combines residential training with site-based assignments.
Three programmes were delivered in 2011 with cohorts of 16, and a further five programmes with cohorts of 18 are planned for this year. Participants cover three main business modules:
- Leadership in Health and Safety
- Performance Management
- Business Improvement
As part of the Business Improvement module, each candidate has to undertake a site-based project that returns an investment. Based on the performance of the 2011 candidates, RoI in excess of £430,000 is anticipated from this initiative.
Measure the improvements
It is very easy to claim a return on investment or an improvement, but what is needed is statistical information to be able to demonstrate this. Although many would claim that they do not hold historical data, a host of information has in fact been collated by the industry over the years. For example, the following is a list of key performance indicators (KPIs) and evaluation and monitoring procedures that most companies have been undertaking for many years.
- Heath and safety LTIFR/incident reports/notices
- Environmental complaints/notices
- Return-loads analysis
- Tipped-loads record
- Laboratory testing results
- Plant stoppage time
- OEE (overall equipment effectiveness)
- Fuel usage per tonne
- Electricity consumption per tonne
- Plant repair and maintenance costs
- Customer feedback (complaints/ satisfaction)
Potential industry saving
If the asphalt business in the UK is considered as whole, an estimate of the potential savings that could accrue from a programme of training and assessment, as outlined above, is as follows:
Cost of Production (industry average at 2011 prices)
- Stone - £15.00/tonne
- Bitumen - £30.00/tonne
- Electricity - £0.40/tonne
- Process fuel - £4.00/tonne
- Fuel taxation - £0.37/tonne
- R&M/labour costs - £3.00/tonne
- Average CoP - £52.77/tonne
Potential Savings
Based on the average cost of production of £52.77 per tonne and assuming that the training and assessment programme brings about a modest saving of just 0.5% (it could be much more), this would represent a saving of £0.26/tonne.
The major producers in the UK have an average annual output of around 5 million tonnes, thus generating a potential annual saving of £1.3million (5 million x £0.26) per major producer. UK asphalt production in 2010 was 21.5 million tonnes, representing a potential total saving of £5.6 million on the estimated 0.5% improvement.
Returning to Aggregate Industries’ Training Triangle (fig. 16), the company’s ‘strategy’ is to deliver materials and services within customers’ expectations centred on the development and delivery of a QCF qualification.
The ‘purpose’ of having this ‘Asphalt Business Improvement’ QCF qualification is to upskill and develop Aggregate Industries’ staff into a competent workforce.
Achieving the company’s ‘vision’ is being complemented by a social and financial return on investment in its key asset, which is its workforce.
Acknowledgement
The author would like to thank colleague Dave Howourth for his invaluable assistance in the development of the QCF qualifications and the writing of units and workbooks. Thanks are also due to fellow staff members within Aggregate Industries’ asphalt and ready-mixed concrete businesses for their expertise during the development work.
This paper was presented at The Institute of Quarrying’s 2011 Annual Conference.