Training For Competence
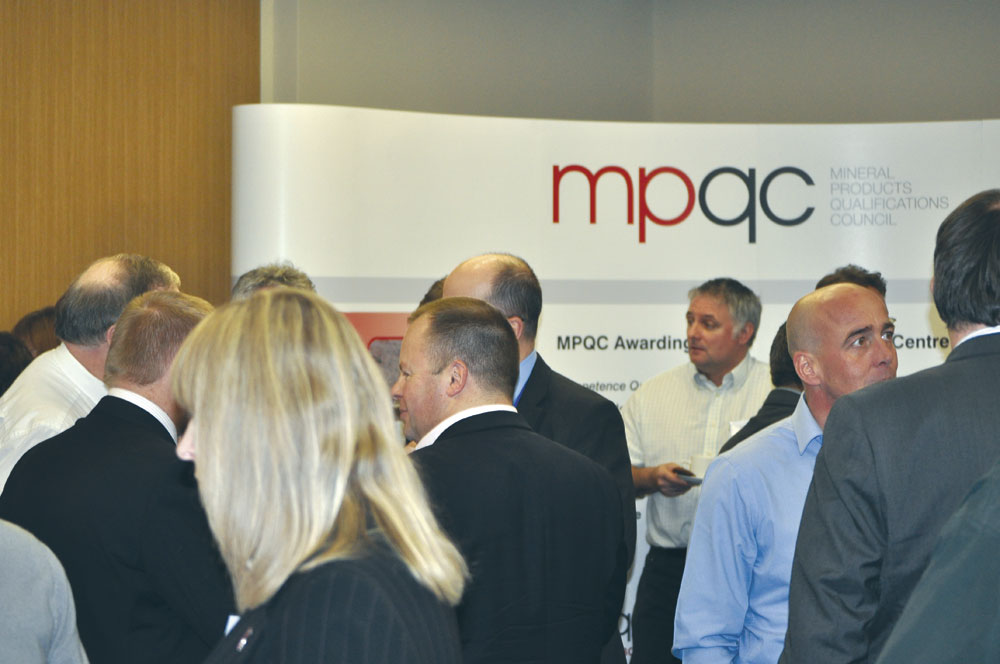
Delivering a fully competence-assured industry within the new Qualification and Credit Framework (QCF)
The Mineral Products Qualifications Council’s recent ‘Training for Competence’ workshop, which was originally scheduled for December 2010 (but had to be postponed due to the adverse weather conditions), finally took place at the Link Hotel, Loughborough, in January.
Having held a series of similar workshops at venues across the UK in conjunction with the Institute of Quarrying (IQ), MPQC recorded its best ever turnout for such an event with nearly 100 delegates attending the half-day seminar.
The Training for Competence workshop proved to be a highly stimulating and informative event, with key speakers including: Roy Bush, HM Inspector of Quarries; Graham Crawshaw, standards and development manager for MPQC; Julian Smallshaw, education manager for IQ; Mike Phillips, general manager of IQ; and Jonathan Ledger, contract manager for Proskills.
With industry NVQs being replaced by qualifications within the new QCF, it is important to raise awareness of these changes and their benefits in order to help employers and individuals understand how the system works and how they differ from the current NVQs.
One of the major challenges facing the industry is the need to have a fully competent workforce. The Health and Safety Executive (HSE) is actively looking for quarry operators to be able to demonstrate the competence of their staff through industry-designed training/qualifications and to develop and maintain employees’ skills through CPD.
Following an introduction by event chair Viv Russell (regional operations director for Tarmac), Roy Bush of the HSE started the seminar proceedings with a presentation on the need for continued competence in the quarrying sector.
With competence playing such a key role in improving the health and safety standards of the industry, Roy urged everyone to build on the competence and operational best practice that has already been achieved. Although the industry has made significant progress towards the Target Zero initiative, he warned that quarrying firms cannot afford to rest on their laurels but must show ongoing commitment to competence, which, in turn, would lead to a sustainable safe working environment for the benefit of all.
Roy also stressed the importance of training and the need for individuals to keep their CPD records up to date as industry legislation changes. He said that the aggregates sector, as a whole, must continue its current training initiatives, but more importantly companies need to further invest in future programmes if they are to move forward.
Roy said that he believed this would help raise health, safety and environmental standards even higher, and demonstrating this unprecedented level of success (ie meeting Zero Harm) would set an example for other manufacturing sectors to follow.
Next to take the stage was Graham Crawshaw of MPQC, who gave a rundown on the new Qualifications and Credit Framework. With the imminent move from NVQs to the QCF, many employers are asking what this change will mean for them and their staff.
Before explaining exactly how the QCF works and the impact it will have on companies, Graham discussed why the change had come about. He pointed out that the new qualifications have been brought on by the new EU framework and are very similar in content and standard to the existing NVQs, although the QCF modular format will offer much greater flexibility.
‘Learners’ will have a wider choice in the units they can take, together with flexibility on how they study and the time taken to complete each module. Furthermore, the new framework, argued Graham, will reduce bureaucracy in accrediting and assessing qualifications.
He also discussed in detail the QCF changes that are likely to affect employers and those in training within the industry. For example, all recognized vocational qualifications will be approved by the Sector Skills Councils and readily available to learners in small, credit-based units of learning. These credits will be the building blocks of qualifications within the QCF, with 13 credits representing a certificate-level qualification.
To help delegates gain a better understanding of the changes and credit values (based on learning time) under the new framework, Graham gave an example of how the current NVQ Level Blasting Operation module will be delivered and the transitioning from NVQ to QCF.
Continuing the theme of the Qualification and Credit Framework, IQ education manager Julian Smallshaw took the stage to highlight the key benefits of QCF, including the development of a ‘structural learning path’ in which individuals are given a Unique Learner Number (ULN).
This 10-digit number is allocated to every person over the age of 14 who is involved in nationally accredited education or training as a part of lifelong learning. It will remain with them throughout their careers so that all education/training can be linked together and easily identified by employers. NVQs currently held will still be recognized at their existing value.
Importantly for the delegates, Julian gave several examples of how courses under the old NVQ framework will fit in within the new QCF structure. He also urged employers, trainers and learners to be aware of the revised types of qualification under the new framework: Award; Certificate; and Diploma.
Mike Phillips, the penultimate speaker, spoke about the IQ’s role within the industry, most notably the importance of ongoing professional development and how this dovetails with the existing NVQs and new QCF.
Echoing Roy’s sentiments, Mike explained the need for businesses to maintain and demonstrate an individual’s competence at work, which was followed by a short video clip defining the meaning of competency. He also pointed out that it is employees who are responsible for their own CPD records and all persons appointed should know, understand, record and operate within the limits of their own individual competence.
With competence now an integral part of health and safety, Mike highlighted the benefits of the IQ Corporate Professional Competence Scheme, which was introduced in 2009 with the endorsement of the HSE. Many of the major UK quarry operators have already signed up to the CPC scheme and IQ is now encouraging SMEs and contractors to join the programme as a way of demonstrating competence in a standardized format.
The final speaker of the day, Jonathan Ledger, discussed in detail the funding streams available for training and staff development within the extractives sector. Despite the well-publicized Government cutbacks, Jonathan said that there is still time left for employers to apply for public funding in relation to skills and training.
He focused on how companies can obtain funding for training for various schemes, including: Joint Investment Programme; Apprenticeships; Train To Gain; and Leadership & Management.
Viv Russell concluded the proceedings by thanking all the speakers for their outstanding presentations. The general consensus at the Training for Competence workshop was that the implementation of QCF represented a significant step in reforming the industry qualifications landscape for the 21st century and was being widely welcomed by employers, learners, training bodies and awarding bodies alike.