Tarmac's Approach to Development Employees' Long-Term Skills and Career Paths
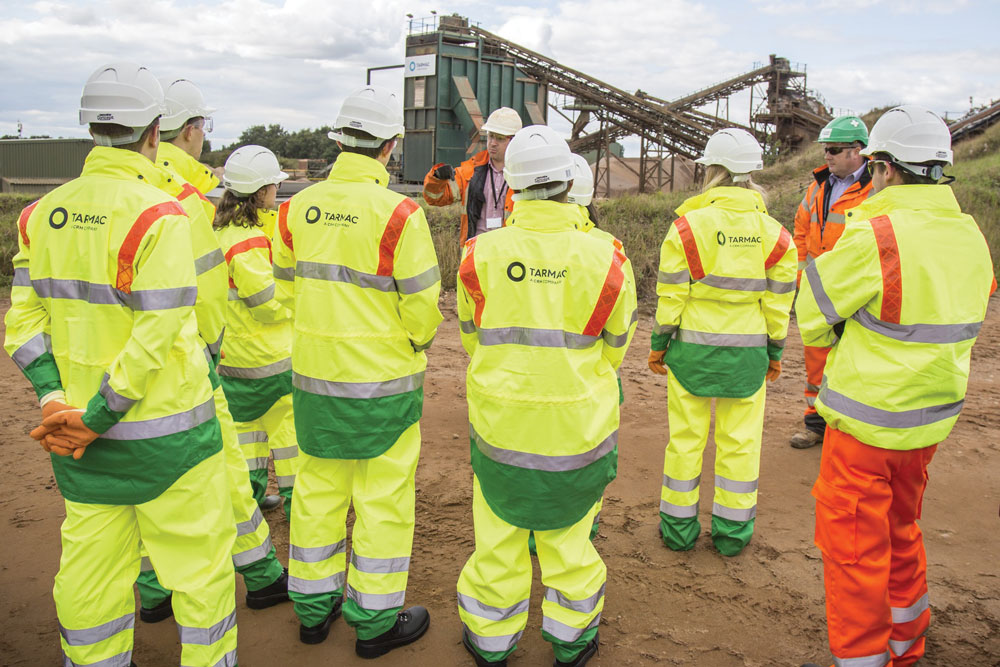
First published in the April 2017 issue of Quarry Management as We’ve got skills – and they’re multiplying
Headlines about the construction industry’s national skills shortage are increasingly common but they often overlook the work already being done by businesses in the quarrying sector to nurture talent and develop employees’ long-term skills and careers paths. Tarmac are driving professional development with a wide-ranging skills strategy that includes apprenticeships, mentoring and a partnership with a leading university.
Undoubtedly, the quarrying industry’s best asset is the strength in depth, skill and expertise of its workforce. Although not the ultimate silver bullet to solving the skills shortage, bringing in new blood and nurturing and investing in existing talent is critical to delivering the UK’s infrastructure targets.
Tarmac are one of a number of companies to have grown a skills programme that allows their current workforce to benefit and develop professionally. The company has put in place numerous initiatives across its operations, designed to help people add to their existing skill sets, develop their expertise and, ultimately, fulfil their potential.
To demonstrate this commitment, the company has recently applied to become a member of the 5% Club, a group of leading businesses that are striving to ensure that five percent of their workforce is made up of apprentices or graduates within five years. Currently 3.7% of Tarmac’s employees come from this population, testament to the company’s long-standing recruitment and skills programmes.
From apprenticeships, graduates and professional qualifications through to a bespoke mentoring scheme, the company provides a number of avenues for people to come into the business, identify development areas, gain additional experience and make the most of their transferable skills.
One such example, which is also benefitting the wider quarrying industry, is the company’s partnership with the University of Derby, where more than 75 of Tarmac’s employees are currently enrolled on industry-related diplomas and degree programmes. Staff study for professional qualifications part-time alongside their day-to-day roles and the courses are run from the university’s Centre for Mineral Products Professional Development.
The centre offers 18 separate qualifications across five main specialist areas – mineral extraction, asphalt and pavements, concrete, cement, and heavy clay. All courses are internationally recognized and developed in partnership with industry bodies, including the Institute of Quarrying and the Institute of Asphalt Technology.
The types of qualification on offer vary – from a Bachelor of Science in Minerals Management and a Foundation Degree in Mineral Extractives Technology to University Diplomas in Road Surface Treatments and Higher Apprenticeships in Mineral Products Technology – but all are designed specifically to provide students with a platform for career development.
To celebrate the continuing professional development opportunities offered by these courses, Tarmac’s senior vice-president, Martin Riley, recently attended a special Student Awards event at the university. In his capacity as Deputy Chairman of the Institute of Quarrying, he handed out awards to students who achieved top marks in their respective years.
He commented: ‘In the centenary year of the Institute of Quarrying, it’s fitting that the industry is looking ahead and supporting future talent and future leaders by working with organizations such as the University of Derby to create opportunities to learn and develop long-term, fulfilling careers. On a personal note, I was very proud that three of the top students were Tarmac employees; it really shows the immense energy, enthusiasm and passion of our people.’
Lee Preater, health and safety advisor at Tarmac, is in the second year of his Foundation Degree in Mineral Extractives Technology and was presented with the Longcliffe Calcium Carbonates Award (1st Year Student) by Martin for gaining top marks in his course assessments. Six months ago he was promoted and he credits his degree course for helping him make the step up.
‘There’s no question that my involvement in the course helped me to advance through the company, as it has allowed me to demonstrate initiative and broadened my understanding of the industry. The teaching has provided an immense amount of support in my day-to-day job and given me a far greater depth of knowledge to draw on, as well as bringing me up to speed on how other parts of the business function.’
Part-time study and blended learning mean that time spent away from the workplace is reduced, while course content is frequently evaluated to guarantee it will remain relevant. The projects undertaken are also directly related to the students’ day jobs, to ensure that learnings can be continuously applied in the workplace.
Lee continued: ‘The material we study is never pigeonholed and covers all aspects of the industry, from the use of technology all the way to financial management. Not everything is done via distance learning – we have regular group study days, which are great for building team spirit, and there are plenty of opportunities to network with people across the wider industry.’
Dannika Bannon, manager of Tarmac’s quarries at Bestwood and Calverton, in Nottinghamshire, is another to have benefited from the degree programme, having completed the same degree as Lee since joining the company. Her route into the industry was somewhat unconventional compared with some of her colleagues.
‘I came into the industry pretty much by chance,’ she explained. ‘When I left school I wasn’t sure what I wanted to do, but all my friends were off to university so I applied too. I studied law and criminology, but by the time I reached my third year I’d realized it wasn’t what I wanted to do for a living.
‘Through university I worked part-time for an out-of-hours logistics team and really enjoyed it, so when I saw a similar full-time transport logistics role at Tarmac’s head office advertised, I applied and was fortunate enough to get it.
Since she took on her first role with the company, Dannika’s career has seen her go from strength to strength, moving from logistics over to the operational side of the business in the role of weighbridge supervisor, before taking on the challenge of managing two quarry sites in Nottinghamshire.
She commented: ‘The first time I sat down with my manager, he asked me what my goals were and what he could do to support me. I told him that I wanted to be a quarry manager, and before I knew it I was enrolled on the University of Derby’s part-time foundation degree programme. I graduated last year and am already being encouraged to carry on my studies and do a Masters.
‘There are so many preconceptions about the quarrying industry. I think a lot of people assume it’s a physically demanding job in a dirty environment, but the reality is that it’s highly skilled and technical, with lots of opportunities for training and continuing professional development throughout your career.
‘The support I’ve had has been amazing,’ she continued. ‘Anything I’ve asked for, I’ve been given – from going back to university to qualifying as an explosives supervisor. There really are so many opportunities out there for people who are determined, enthusiastic and willing to work hard.’
In addition to encouraging its employees to develop their skills through formal qualifications, the company has also recently set up a pilot mentoring programme. This was established last year to help to connect people across the business, share knowledge and provide support where it is needed.
Learning and development specialist Deanne Bott explained: ‘In 2015 we conducted some research which included exploring gender diversity and inclusion, to develop a framework for a mentoring scheme across the whole business aimed at improving retention and engagement, with a view to opening up more potential career pathways.’
Key to making the pilot a success was ensuring that the participants were matched with the right mentors, in terms of their skills, experience, geography and professional objectives. Once this had been achieved, the participants attended an induction day and then regular meetings were scheduled between the mentor and mentee.
‘We found that the best approach was for both mentors and mentees to be flexible and willing to explore many developmental areas,’ Deanne continued. ‘Some people were looking for the best ways to achieve their next career step, while others wanted guidance on how to excel in their current role.
‘The pilot has just come to an end and we are in the process of reviewing the feedback to help shape the mentoring programme at Tarmac going forward. The responses we’ve received throughout the pilot have been incredibly encouraging and it’s been interesting to discover that the mentors themselves have also really benefitted from the experience.’
Unit manager Iain Blackaller was one of the first people to get involved with the mentoring pilot scheme. Commenting on his experience, he said: ‘The mentor I was paired with is extremely knowledgeable of our business and was easy to communicate with. The scheme is about personal development, and my mentor helped me set objectives in addition to the personal objectives set with my line manager.
‘The process has really helped me focus on areas where I was not as confident and appreciate my decision-making and communication skills. During the mentoring sessions we discussed my learnings, both positive and negative, and these debriefs have equipped me with additional tools to help me reach my long-term goals.’
Iain’s mentor, Nick Shires, regional director south, added: ‘I have found the experience truly valuable. It has not only given me the opportunity to interact with someone who I would normally not have the chance to, but to see and exchange knowledge and experiences on wide-ranging topics. It has also given me an insight into Iain’s day-to-day challenges and enabled me to support him through the process.’
Ensuring staff remain enthusiastic, are given support and are encouraged to embrace new ways of working are equally key elements of the business’ long-standing apprenticeship programme. Abby Finney, an apprentice mechanical fitter based at the company’s Tunstead cement plant, in Derbyshire, had not always considered a future in engineering, but was inspired to make a career change when she learnt of the opportunities available.
She said: ‘I was working in an office for an events management company when I heard about Tarmac’s apprenticeship programme. I was really impressed by the training and career progression on offer, so I pushed myself to do something different.’
In the first two years of her apprenticeship Abby gained a BTEC in Mechanical Engineering, taking modules on electrical systems and welding, after which she successfully completed an HNC course. Now in her fourth year, she is working towards an HND qualification while working full time at the cement plant.
‘One moment I’ll be dealing with maintenance on a raw-mill, then the next I’ll be fixing a conveyor belt – the variety of skills I’ve developed is one of the things I love about this job. The support is definitely one of the most rewarding parts of my apprenticeship, and now I’m in my final year I’m being encouraged to go on to do a degree or management qualifications. The opportunities for development are great, and I’ve not only gained technical qualifications, but the confidence to get stuck in as well.’
The skills shortfall figures that dominate the national debate are undeniably significant and the challenge to shake off the incorrect and negative perceptions of the sector as low skilled and low paid remains. However, the overriding message from those on the ground – especially those in the early stages of their careers – is one of enthusiasm and optimism for the future.
The industry has a responsibility to reposition its offer, think creatively and make quarrying and construction more aspirational careers. It is, nevertheless, critical that this is achieved while nurturing existing talent and championing better worker engagement. Helping employees develop their skills and stay motivated will only work if they continue to feel valued and supported.
- Subscribe to Quarry Management, the monthly journal for the mineral products industry, to read articles before they appear on Agg-Net.com