Smiths Bletchington - Innovation in Action at Gill Mill Quarry
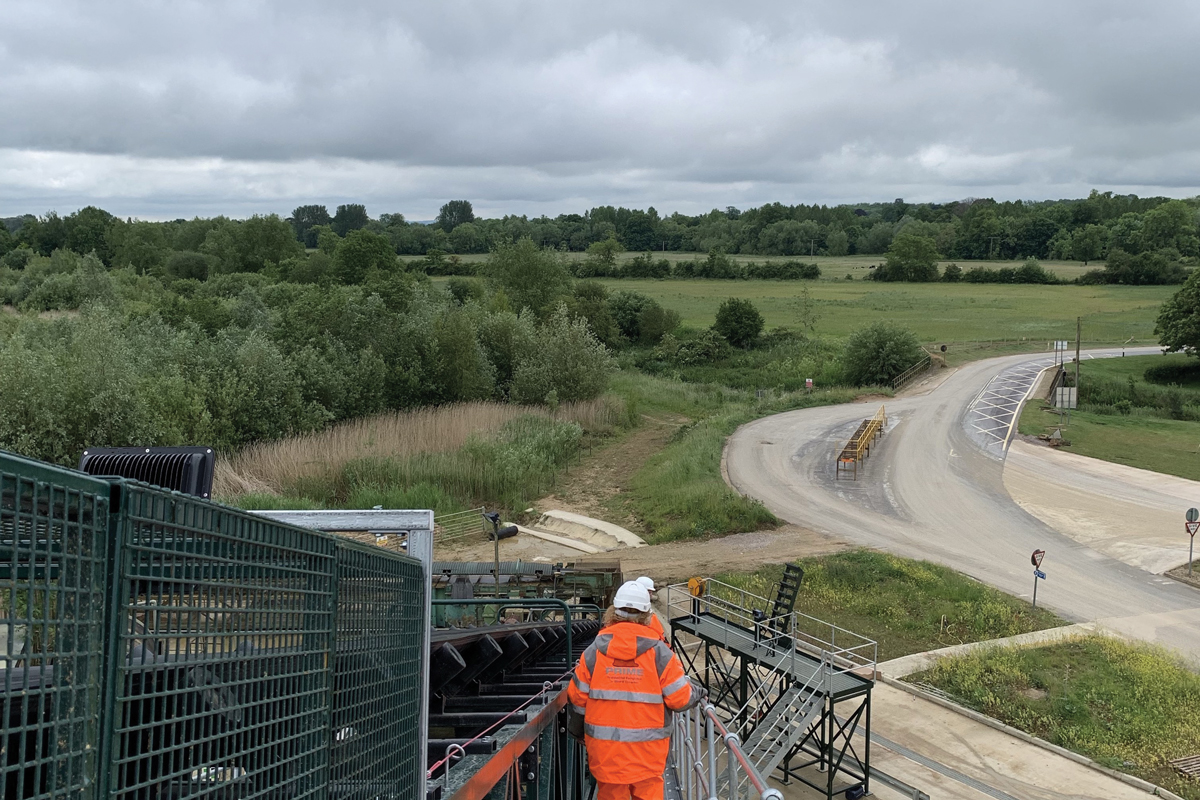
First published in the July 2019 issue of Quarry Management
How an independent sand and gravel extractor is leading the way with investment in intelligent plant to deliver measurable improvements in performance
Knowledge and innovation drive the quarrying and mineral products industries. Discovering smarter ways of doing things is at the heart of the sector’s search for meaningful performance improvements that deliver a real difference to the bottom line.
People working within the quarrying industry need a range of skills and expertise to be effective beyond the basics of the job itself. Investment in individual skills development varies from formal academic courses to on-the-job training, all with the goal of equipping employees with the competencies to do their job to the best of their abilities. The Institute of Quarrying’s (IQ) Skills Wheel shows the core skills and areas of knowledge that all employees should aim to develop as part of their commitment to lifelong learning.
James Thorne, IQ’s chief executive officer, says: ‘The Skills Wheel attempts to map the core competencies required for success in our sector. The four segments cover Standards and Professionalism; Engagement, Influence and Impact; Personal Effectiveness; and Knowledge and Innovation.
‘We’re seeing increasing levels of innovation being introduced into working practices and operational procedures by quarry operators large and small. What that looks like can vary from simple time-and-motion reviews to the application of artificial intelligence that is a potential game changer.’
The digital revolution of the mineral products sector continues to gather pace. Often perceived as technology out of reach of independent operators, sand and gravel extractors Smiths Bletchington are leading the way with investment in intelligent plant that is delivering measurable improvements in performance.
Smiths Bletchington
Smiths Bletchington is a long-established, family-owned group of companies serving the construction industry in and around Oxfordshire and the surrounding counties. The company’s Gill Mill Quarry is its flagship operation. Its aggregate and recycling processing plants are situated next to the river Windrush at Ducklington, near Witney.
With an operational capacity of 450,000 tonnes/year, the primary plant produces a wide range of washed sands and gravels for use in many different projects, from the construction of roads and bridges to building homes and hospitals. The recycling plant, which diverts inert construction and demolition waste away from landfill, is located alongside the primary plant and produces c.100,000 tonnes of recycled products per year.
Ben Strickland is the quarry manager at Gill Mill Quarry, prior to which he worked as quarry manager at Hanson plc’s Sutton Courtenay Quarry, in Oxfordshire. Having made the move from global producer to an SME operator, he sees the many benefits derived from close access to the key decision-makers when it comes to investment in new kit and new technologies.
‘My brief when I started at Smiths Bletchington was to take a long hard look at the way the site operates and identify opportunities for improvement,’ he says. ‘The whole process of developing a business case and getting the green light to proceed is short-circuited when you have closer access to the decision-makers, so the business is able to make swift decisions that deliver rapid returns.
‘My goal is to achieve optimum production levels alongside commercial activity at the lowest production cost. That’s about continual advancements in operational efficiency. Central to this has been our partnership with CDE, one of the world’s leading manufacturers of wet-processing plants. CDE were already familiar with our Gill Mill operation, having installed and commissioned our 250 tonnes/h turnkey sand and gravel processing plant back in 2015 and the 100 tonnes/h recycling plant in 2013. But the challenge we presented them was to do with smarter working and being able to measure improvements using real-time reporting through the introduction of smart telemetry.’
Ben’s quest for finding innovative new ways of doing things stems from previous training and his studies at the University of Derby’s Centre for Mineral Products. He now holds a 2:1 Bachelor of Science Degree in Minerals Management. His dissertation, entitled ‘Investigation into the use of continual data gathering within the accepted process to better assist in operational decisions’, forms the basis of the technology project that CDE have driven forward and which is now being piloted at Gill Mill Quarry.
Ben continues: ‘The main area of interest for us was the efficiency of our static plant, so we installed a remote telemetry system on our recycling plant and our main plant. The recycling plant is producing c.100 tonnes/h and the main plant is around 260 tonnes/h with maximum plant availability allied to maximum process coefficient.
‘The telemetry has enabled us to monitor the performance, in real time, of both static plants, identifying bottlenecks and downtime. Analysis of the data means we are then able to identify actions to improve performance. That might be labour optimization or an engineering solution. Quite simply, the telemetry gives us invaluable intelligence on which to base decisions and take actions. That has led to some extraordinary improvements delivering significant cost savings and performance gains.
‘In addition, all plant operators have instant access to performance metrics via a smartphone app. This means they can make on-the-spot operational decisions based on real-time data.’
Restoration of the Gill Mill site post extraction by Smiths Bletchington is a further working example of innovation in action. Ben explains: ‘We are working closely with a number of experts to ensure that how we restore the site matches exactly to the detailed plans for creating the largest reed-bed habitat in the south of England.
‘Our mobile plant uses GPS technology to match exact profiles as agreed as part of the restoration plans. In-cab technology guides operators to achieve agreed gradients, taking out the guesswork. This attention to detail is only possible through the application of innovative new technologies. We know that once the habitat is created it will be fit for the purpose envisaged by the planners and experts.’
But, as with all innovations, the application of new technology as an enabler for improved performance is only as good as the engagement it receives from the operatives on the ground. Ben continues: ‘The mobile fleet has been equipped with all sorts of telemetry for a good number of years now, providing useful insight into fleet efficiencies and individual performance. The application of telemetry on static plant is relatively new, so making sure operators are trained properly is key to maximizing its effectiveness.’
‘I’m convinced the application of artificial intelligence in our sector will continue to increase, driving even greater efficiencies and improving safety for all.’
Tom Houston, CDE’s director of CustomCare, said: ‘We are delighted that Smiths Bletchington have chosen CDE CORE SmartTech to assist with the optimization of their plant. We have found Ben Strickland and the team to be progressive in their approach to managing and optimizing the performance of their plant and Smiths have seen the benefits of this in terms of improved productivity and profitability. We are already working with Ben on future developments which will see the Smiths Bletchington plant become a fully intelligent wet-processing facility.’
Skills Wheel
The Knowledge and Innovation segment of the IQ Skills Wheel focuses on all areas of site operational issues, as well as general management advice. Its core areas cover innovation, technical and systems across health and safety, productivity and efficiency. For further information, visit: www.quarrying.org
About Ben Strickland, MIQ
After completing an HND in Construction Management at the University of Salford in 2011, Ben signed up to the trainee management/LEAD programme with Hanson Aggregates. As he was keen ‘to earn while you learn’, the Hanson LEAD scheme was the ideal option.
Over the years, Ben has had many opportunities to work at different quarry sites across the UK. He started as a management trainee with Hanson UK at Pateley Bridge Quarry and Criggion Quarry near North Wales. He then progressed to assistant manager at Shap Beck Quarry in Cumbria in 2014 and then on to a quarry management role at Sutton Courtenay Quarry in Oxfordshire, before joining Smiths Bletchington at Gill Mill Quarry in August 2017.
Alongside a full-time job, Ben has completed the Foundation Degree in Mineral Extraction and recently completed the Bachelor of Science Degree in Minerals Management through the University of Derby, as well as Level 4 and 6 qualifications in Safety, Health and Environment. To further his knowledge, he is currently completing the WAMITAB waste-management certificate. All of the above have served to broaden his experience and knowledge of the quarrying industry.
- Subscribe to Quarry Management, the monthly journal for the mineral products industry, to read articles before they appear on Agg-Net.com