Mapping The Future
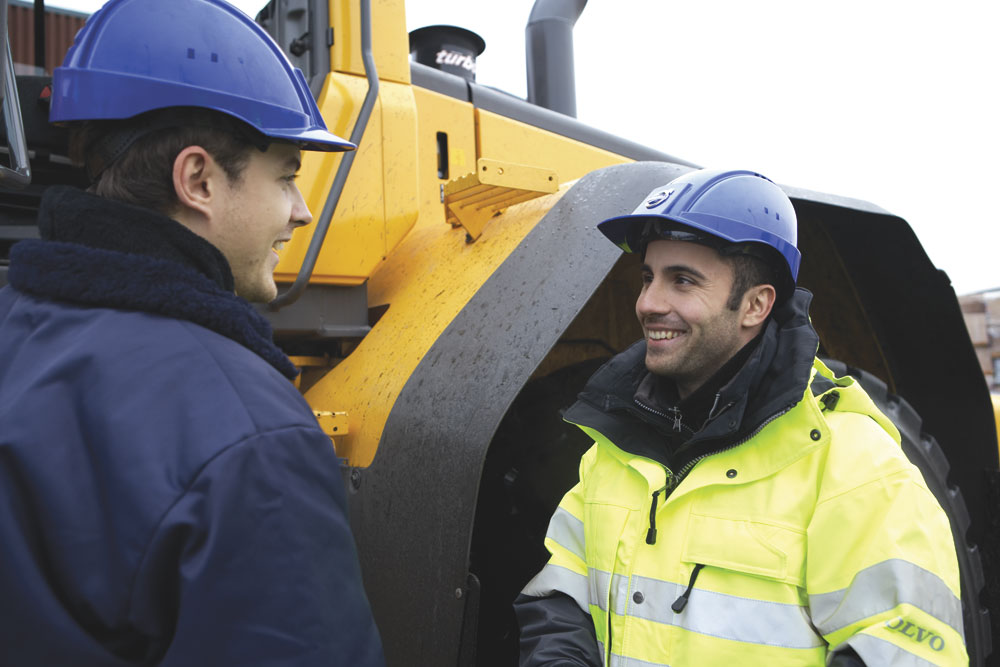
One of the key areas of responsibility for Volvo Construction Equipment is to develop a fully trained and competent workforce. Quarry Management recently visited the company’s brand new training centre in Duxford to see how employees are gaining the necessary skills and competence for the future
The importance of training and development with the aim of raising staff competency levels has been a key strategic objective for Volvo CE for many years.
The Volvo Group see training as an integral part of their business and, as such, have invested heavily to ensure that every employee has the right level of skills, knowledge and, more importantly, competence to do their job properly. The investment is also a positive indication of increased commitment to training in the future, as the company recognizes that skills gaps still exist within its workforce and this could have an adverse effect on business.
As the quarrying industry aims to have a fully competent workforce by the end of the year, one of the growing concerns is that the accident rates for contractors and suppliers on site remain alarmingly high.
With a strong safety culture embedded in the organization, Volvo CE are one of the most health and safety-conscious construction equipment manufacturers in the supply chain. The company’s long-term commitment to training and raising employees’ skills levels means that it can achieve the necessary competence and safety performance required on site.
In addition, Volvo CE have made significant progress towards other key areas of competence, including top-level leadership, workforce engagement and internal risk assessment, all of which are essential components of good health and safety management.
Developing skills for the future
With the current global economic conditions, these are challenging times for the quarrying sector and related industries. The effects of the severe downturn have greatly affected the level of investment that companies have been able to make in the training and development of their staff over the past year. At Volvo CE, however, investment in training is still very much on the agenda.
‘During these difficult and uncertain times, our commitment to training and CPD remains the same to ensure that we have a highly skilled and competent workforce,’ explained Jonathan Hurley, business process development manager at Volvo CE.
‘Like many other manufacturers coping with the global recession, there have been significant cutbacks throughout our business, but training is one important area in which we continue to invest a lot of time, money and resources. It gives us a competitive edge that differentiates us from other construction equipment manufacturers while staying true to our core values of quality, safety and environmental care.’
The company’s strong commitment to staff training and development could not come at a better time, as there is an alarming shortage of skills across the quarrying, construction equipment and related extractive and processing industries. More qualifications-led training, graduate trainee schemes and apprenticeships have, therefore, become increasingly important to help tackle the skills shortages in these sectors.
‘If the right courses and training programmes are not available to engineers, mobile plant operators, quarry managers, shot-firers and other operating roles, there will be an even greater skills gaps throughout the supply chain,’ said Martyn Brawn, engineering manager for Volvo CE.
‘To recruit and retain new starters in our industry, we currently have an apprenticeship programme with 17 apprentices working across the UK, with an additional four trainees to join the company by the end of the year.’
Training day
Each company and unit within the Volvo Group is responsible for identifying and developing its own skills and competence for the future, which ties in with the overall strategic objectives for 2010-2012 throughout the organization. At Volvo CE, training has always been, and remains, a fundamental part of the company’s Integrated Management System (IMS).
‘Over the next few years we are going to focus more on training and up-skilling our workforce,’ said Mr Hurley. ‘Along with sustainability, this is an area in which we can see real potential for growth and improvement for the business. If we are going to fulfil our strategic objectives and stay ahead of the game, we must ensure that our employees have the necessary skills, knowledge and competence.’
Mr Brawn pointed out that this requires important long-term planning, and the recently opened training centre at Volvo CE’s Duxford headquarters represents a significant step forward towards securing the right skills and competence for the future.
‘The new facility has doubled our training capacity,’ he said ‘It is a huge investment that was earmarked as part of our development plan two-and-a-half years ago. Despite the recession, we still went ahead with the project, which now provides a stimulating and high-quality learning environment for trainees and apprentices.’
As the focal point of all Volvo-led training in the UK, the purpose-built school houses two workshops (totalling over 300m2), two fully equipped seminar rooms, a reception area and a common room/kitchen. There is also a larger teaching room, a storeroom and a component workshop that will allow instructor-led courses to focus on specific areas, such as electrics, advanced hydraulics, engines, transmissions and drivelines.
The outline design for the facility was drawn up by Graham Paflin, training centre manager for Volvo CE, who is also one of two fully qualified and experienced full-time instructors based in Duxford.
‘As technology becomes more and more specialized and Volvo’s range of products increases, the skills and competence the engineers require are also changing,’ explained Mr Paflin. ‘If we want to maintain our leading position in customer satisfaction, it is important that employees cannot fall behind with their training. They need to develop new skills to meet the ever-increasing demands of our customers. With the new training centre staffed by myself, Mark Armsworth and three other part-time trainers, we can now deliver suitable courses in the classroom and provide practical hands-on experience in the workshop.’
The in-house training courses cover all the company’s construction equipment and road machinery range, including excavators, articulated haulers, motor-graders and pavers. As well as the machine-based training, Volvo CE are looking to develop more competency-based courses at the training school to ensure engineers stay abreast of the increasingly rapid developments that are taking place.
The company is also delivering a comprehensive programme of online training courses to employees, which cover a wide range of topics such as health and safety, environmental awareness, legislation and effective machine operation. The training modules can be tailored around the individual and form part of a ‘progressive educational package’ being offered to all Volvo CE staff.
‘Before anyone can take an instructor-led course at Duxford, they need to have completed a certain amount of online training,’ explained Mr Brawn. ‘It is an important prerequisite because the training school represents a step forward in their training and development.’
Mr Paflin added: ‘No matter how experienced you are, everyone at the Volvo Group is progressively trained and assessed. Nobody can move up to a Step Two training module without having done Step One.’
Implementing sustainability
As the aggregates industry focuses on operating in a more sustainable way, there is now increasing pressure, in most cases driven by government legislation and targets, for equipment and materials to meet the ever-increasing environmental demands. Volvo CE have a clear responsibility for not only reducing the environmental impact of their products, but also strengthening their own sustainability credentials.
‘Environmental care is a corporate value for the company,’ said Mr Hurley. ‘As well as minimizing the negative environmental impact of our products, we are also focusing on reducing the impact of our production operations, for example, lowering carbon emissions from our factories. We also impose the most stringent environmental requirements on all our suppliers.’
In 2007, the Volvo Group opened the world's first carbon dioxide neutral automotive plant in Ghent, Belgium, and the long-term ambition is to make all their plants CO2 neutral.
Volvo were also the first commercial vehicle manufacturer in the world to develop seven different specially modified diesel engines that demonstrate the potential for carbon-neutral mobility. These engines can be run on a number of renewable fuels, including biodiesel, biogas, synthetic diesel, ethanol/methanol and hydrogen gas in combination with biogas.
Thanks to these technological developments, Volvo CE are well advanced in producing engines that significantly reduce emissions and developing machinery that operates at low noise levels.
The substantial investment in innovations, such as hybrid technology and engines optimized for renewable fuels, demonstrates the company’s commitment to helping customers meet their sustainability goals. As part of this ongoing strategy, Volvo CE have recently launched the Eco-Operator initiative – a training programme that teaches fuel-efficient and environmentally friendly methods of operating machinery.
The Eco-Operator training package is designed to help lower the end-user’s fuel consumption, reduce fuel bills and improve operator efficiency without compromising productivity. At the same time, this will help reduce machine wear and tear and significantly reduce the impact of emissions on the environment.
The training – which takes just one day to complete and includes both practical and theoretical exercises accommodating up to six candidates at a time – is held at the customer’s premises and uses their existing machines in order to minimize disruption and to demonstrate the possible savings on site in real-time.
Fuel consumption is measured and monitored (if possible) via MATRIS – Volvo’s machine tracking and information system. After a period of six weeks, a second visit is made to the site to establish precisely how the training has benefited the operation and to determine the resultant fuel savings.
Shared value
As the demand for more efficient and environmentally sound construction machinery increases, the future challenge for Volvo CE will involve more than just producing better and more effective machines than their competitors.
Mr Hurley explained: ‘Performance is obviously critical for any piece of construction equipment. That is why many machines in the marketplace do exactly what they are required to do. But our customers want a lot more than just a product with proven reliability and capability.
‘They want to know about the core values – quality, safety and environment care – which are fundamental to our business, as well as what we’re doing to strengthen our own competitiveness. These include recent achievements in reducing carbon emissions from our operations, minimizing lost-time accidents, the safety programmes we have in place, and quality control.
‘More importantly, satisfied customers are interested in our continued investment in training; for example, we aim to have all our service engineers trained to NVQ level 3 by the end of the year. There is also the Duxford training centre, which will ensure all Volvo CE employees gain the right skills and competence for the future. By focusing on these key areas of the business, we can share value with our customers and this benefits everyone in the long term.’