Blasting Barriers to Entry in Quarrying and Construction
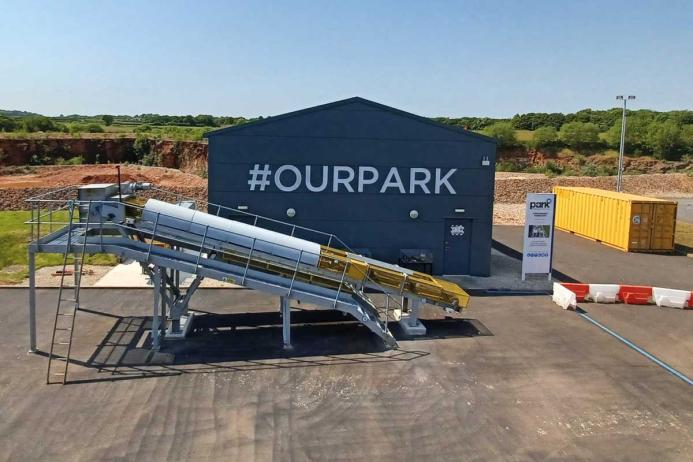
First published in the June 2024 issue of Quarry Management
At Hillhead 2024 Tarmac are celebrating the changing face of quarrying and construction – from improving equality, diversity and inclusion, through to the latest technology-led solutions. The company’s award-winning National Skills and Safety Park is playing an active role in the industry’s evolution by improving skills and boosting social mobility
Emblazoned in large letters on the side of one of the buildings at Tarmac’s National Skills and Safety Park at Nether Langwith Quarry, near Mansfield, are the words ‘#ourpark’. They serve as a visual reminder that this unique and state-of-the-art training facility, which provides apprenticeships and training courses, is for everyone at every level across the business.
Equality and equity in training and development are vitally important elements for creating a more diverse construction industry and address the industry challenges of upward socio-economic movement and skills shortages.
The UK’s lack of social mobility is well documented and in real terms limits access to good career opportunities for people from all backgrounds. According to the Social Mobility Commission’s ‘2023 State of the Nation’ report, overall trends of upward mobility have shrunk in recent decades and chances of long-range upward mobility have also declined. Across the UK significant advantage and disadvantage continue to coexist – the creation of equal employment opportunities and education are key to boosting social mobility.
Socio-economic challenges are not the only hurdle the industry is facing. The skills gap is by now widely acknowledged, and recent data from Randstad has estimated that the industry will need to hire 500,000 new recruits to keep up with the demands of the major infrastructure and construction pipeline. Major projects such as HS2 and Tideway are a significant draw for talent in their geographic regions, putting increasing pressure on an industry that, according to the CITB, is seeing more of its workforce leave than new recruits join.
The CITB ‘Workforce Skills and Mobility in the Construction Sector 2022’ report revealed that 25% of the current UK construction workforce is made up of people aged 45 to 59, 50% are aged 25 to 44, and just 19% are under 25. This ageing population and lack of younger construction workers is a big contributor to the skills shortage.
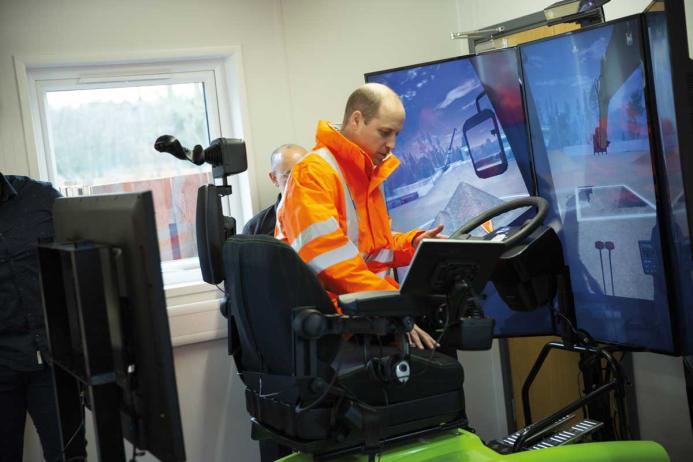
Upskilling, tackling the challenge
Opened in 2020 by His Royal Highness, Prince William of Wales, the National Skills and Safety Park is testament to Tarmac’s commitment to removing barriers to success and creating opportunities for recruitment, training, and progression for their employees. In 2023, the park received the Purpose Coalition ‘Breaking Down Barriers’ award, recognizing the training school’s progressive solutions to the challenges of social mobility.
Matt Gibbs, senior manager of operational competence at Tarmac, explained: ‘Not only is the park helping to address some industry-critical challenges, but it is doing so in a way that really keeps our employees at the heart of it. The apprenticeships that we offer are a great opportunity to give new starters and individuals coming to us from other industries the foundation to a career in materials and construction.
‘The park was founded on the principle of investing in our people to leave a legacy of safety through equal recruitment and learning opportunities. Its success in the years since it opened show how valuable the park is, and how much our employees benefit from the knowledge and experience they gain.’
With its people-first focus, the National Skills and Safety Park is providing people with the right attitudes and behaviours, equipping them with the knowledge and skills to succeed. Over a third of delegates that have successfully completed an industry apprenticeship have subsequently been promoted to front-line leadership or supervisor roles, evidence that the business is doing things differently to facilitate career progression for its operatives.
As the only industry-specific facility of its type, the park is training and developing thousands of employees annually, to the benefit of the wider sector. Last year the park saw almost 6,000 visitors receiving training.
With upskilling opportunities for the younger generation of new entrants and equal focus on encouraging workers with transferrable knowledge to reskill into quarrying and construction, the park is addressing the industry-critical skills gap in what is an essential sector for the UK economy.
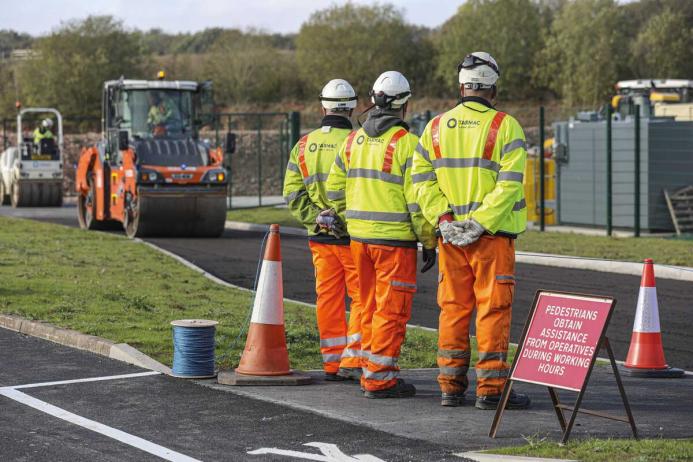
A new set of skills and behaviours
Comprised of training areas to replicate real-life conditions in a controlled environment, the site offers three different apprenticeship standards as part of its Professional Operator Development Programme (PODP), all of which are employer delivered and have been tailored to go above and beyond the national occupational standards.
The three learning avenues include Level 2 apprenticeships across materials processing, road surfacing, and mineral and construction sampling. Covering more than 90% of Tarmac’s operating requirement for employees, the three apprenticeships provide resilience for the company’s workforce. Not only do they maintain skills and succession within the business, but also boost skills availability across a vital industry.
The PODP was awarded Ofsted ‘Outstanding’ status in 2023, in recognition of the high quality of training offered and delivered, which has been designed to give apprentices experience of mineral processing mobile and static plant operation, prioritizing practical on-the-job training.
From apprenticeships and graduates through to the retraining of entrants from different sectors with transferable skills, comprehensive training and development opportunities are offered across various levels and roles within quarrying and construction.
One overarching theme across all of Tarmac’s training programmes is to encourage behavioural change, as the company aims to make sure that the right people are given the right skills for the job. Crucially, learning is available for everyone – it is open to all ages and backgrounds, encouraging diversity and inclusion and helping to retain talent as the company works to change the face of construction for the better.
Another key aspect in the offering of improved social mobility for Tarmac employees is that the park allows for working and learning simultaneously, a critical factor to make sure that opportunities to learn and develop are accessible to all.
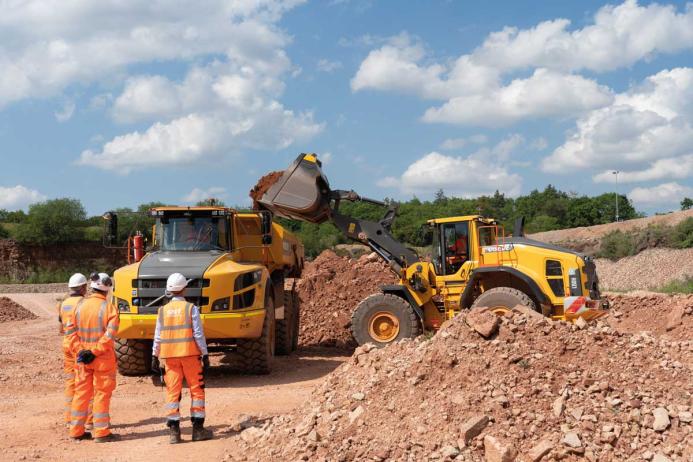
Linking skills and safety
Across quarrying, road building, and construction in general, safety is a top priority for Tarmac – as it is for the industry as a whole. Almost five years after first opening its doors, encouragingly Tarmac have seen evidenced improvements in their safety record. The Safety Park has been a major contributing factor to the business’ sreduction in lost-time incidents from 25 in 2020 to two in 2023, and there has been an increase in proactive safety observations by almost 60% over the same period. As park-leavers progress and graduate into different roles, their skills, knowledge, and behavioural approaches to safety are embedded across operations.
Another notable change that the company has seen as a result of employees taking learning and behaviours from the facility is the effect on sustainability and reducing emissions. Acknowledging that no one individual alone can meet the challenge of climate change, the company needs all employees to adopt the correct behaviours to help play their part in reducing carbon.
Tarmac have also recently partnered with SMT to roll out a dedicated eco-operator training course for their front-line heavy mobile plant operators, increasing awareness and understanding of the impact of everyday decisions that are made on sites to reduce emissions.
The changing face of quarrying and construction
The challenges of addressing social mobility and the industry skills gap are not simple issues that will be easily overcome. Whilst sector-wide efforts are needed to make real change, Tarmac are aiming to play their part in creating a more inclusive industry that is underpinned by a skilled workforce with the right behaviours to prioritize safety and sustainability. Individuals from all backgrounds and walks of life can benefit from the learning and development offered by sites such as this, bringing equality, diversity, and inclusion to life.
Case study 1
Kelsey South, weighbridge operator
Mineral Processing Mobile and Static Plant Operator Apprenticeship
One thing I’ve learnt a lot about is fuel efficiency; I have driven mobile plant for years but before the apprenticeship I never realized just how much it helps the lifespan of the machine, the environment, and the costs, just by monitoring and switching off the plant when possible.
‘I’ve met a lot of other people which has given me a lot more confidence. The people within my cohort were from various backgrounds, both in terms of work (from various parts of the business and sites) and different backgrounds in life – across ages, different parts of the country, and different personalities. It was amazing to spend nine months with people who I’d likely have never met if I hadn’t joined this course and have had the pleasure of working together and creating long-lasting friendships.’
Case study 2
Thomas Macklin
Mineral and Construction Product Sampling and Testing Operations Apprenticeship
‘Being on the PODP programme has helped me learn new skills and develop a lot of other knowledge. I came on to the course after nearly two years with the company as a lab technician. This meant there have been areas of the course I had some experience and knowledge of already, but it has certainly helped give me more of a foundation and understanding of all things in the technical department and the company as a whole.’
Case study 3
Ben Wisniowski
Mineral and Construction Product Sampling and Testing Operations Apprenticeship
‘I’ve now been working at Tarmac for just over a year. I wasn’t in work before coming into this job – I came straight from school and came to work for the company as a technician.
‘While being on the PODP course I’ve learnt a lot, we have only been on the course for 13 months bit it feels like I’ve gained 3–4 years’ worth of knowledge in that time. It’s also helped me to really develop my technical knowledge. I’ve really enjoyed the course and it’s been a great opportunity to meet other people in the wider business who have recently joined.’
Subscribe to Quarry Management, the monthly journal for the mineral products industry, to read articles before they appear on Agg-Net.com