Stemming Ejection Control in Blastholes
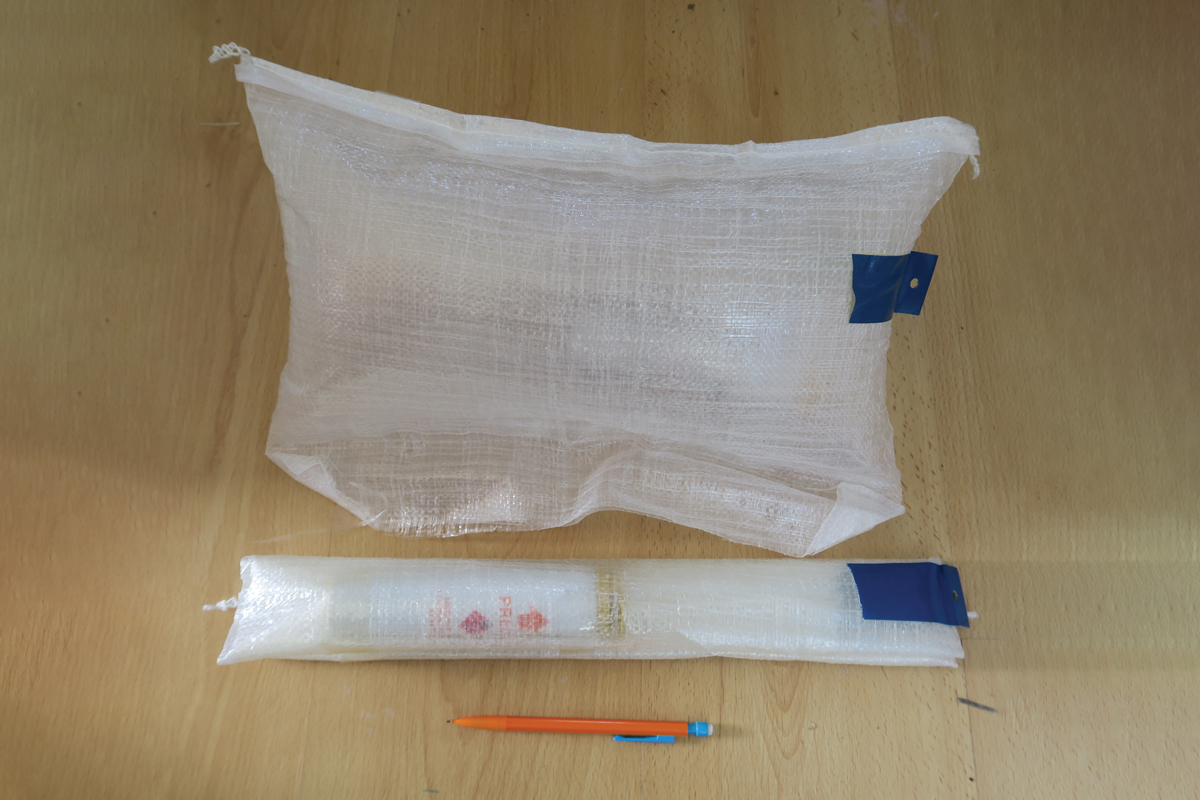
First published in the April 2020 issue of Quarry Management as Stemming Ejection Control
Julian Cleeton, director of Stemtek, looks at how to reduce the likelihood of stemming ejection from primary production blastholes
The use of stemming in blastholes enhances fragmentation and rock displacement by reducing premature venting of high-pressure explosion gases to atmosphere. There is an optimum stemming length beyond which further increments in heave energy effectiveness are not achieved.
Optimum stemming length depends mainly on hole diameter, stemming material, surrounding rock properties and other blast parameters, particularly the burden.
Inadequate stemming increases collar rock breakage, but decreases overall fragmentation and displacement because explosion gases vent to atmosphere more easily and rapidly. It also creates more flyrock, surface overbreak, noise and airblast.
Dry granular materials are best for stemming because they have inertial resistance and high frictional resistance to ejection. Materials which behave plastically or which tend to flow are not suitable for stemming, eg water, mud or wet clay. For blasthole diameters in the 50mm to 130mm range, angular crushed rock (chippings) in the approximate size range of 6mm to 14mm is the most effective stemming material.
When impulsively compressed at its lower end by the tremendous pressure of the explosion gases, crushed stone arches and wedges into the blasthole walls and provides better interlocking and confinement of the gases than, for example, relatively fine drill cuttings. This confinement maintains peak pressures in the blasthole for a longer period of time. The longer these gases can be bottled up, the more they will be able to fragment, heave and loosen the ground.
Even when all these factors are taken into account, there is still no guarantee that stemming ejection will not occur. When blasting takes place, a danger zone of sufficient size is set up such that if there is any stemming ejection, it will not cause damage and/or danger to personnel and/or equipment.
In the case of production blasting (or even toe holes) in sensitive areas such as near power lines, pipelines, cables etc, to reduce still further the likelihood of stemming ejection, the use of stemming plugging devices should be considered. There are a number of devices on the market that could be used, including aerosol-type gasbags, mocaps and rocklocks.
Aerosol-type gasbags can be easily deployed and produce a very tight seal below the stemming area. They are available in the UK and are widely used for this purpose. They can easily cope with the inevitable small variations in hole diameters found in production holes. Average cost: £7–£8 per unit.
Mocaps are hollow plastic plugs that need to be inserted into the hole using a stemming rod to push them down to the desired depth. Since they need to be an interference fit, the choice of size is critical. In broken ground it can be difficult to obtain an effective seal. In cold conditions they become very rigid making it difficult to create a seal. They are available in the UK. Average cost: £4 – £5 per unit.
Rocklocks have the appearance of a hollow plastic ball with a small hole to allow them to be filled with stemming material. They are made from a special plastic which deforms/flexes when gases begin to move through the stemming. They reduce the likelihood of stemming ejection by creating a frictional gas impermeable seal. They are easily deployed simply by dropping them into the blasthole, close to the bottom of the stemming. They have been widely used in the UK but are no longer manufactured here. They are now made in the US and could be shipped here, subject to a minimum order (probably c.3,000 units). Anticipated the cost per unit: c.£5 – £6.
The use of such devices should only cost a few pence per tonne for the quantity of rock expected to be extracted in the vicinity of sensitive structures. It may also mean that areas that have been effectively sterilized could be blasted safely in future.
Further measures that could be employed to reduce the likelihood of stemming ejection include:
- Suitable initiation patterns and timings to allow adequate forward movement of the blast
- Sleeving of the top of the hole if it is broken/cracked
- The use of scaled depth of burial calculations (SDOB)
- Doubling up of devices, eg a gasbag and a rocklock if conditions are considered marginal
- Placing extra confinement on top of the stemmed hole.
- Subscribe to Quarry Management, the monthly journal for the mineral products industry, to read articles before they appear on Agg-Net.com