Raising the Power and Extending the Lifecycle of Rock Drills
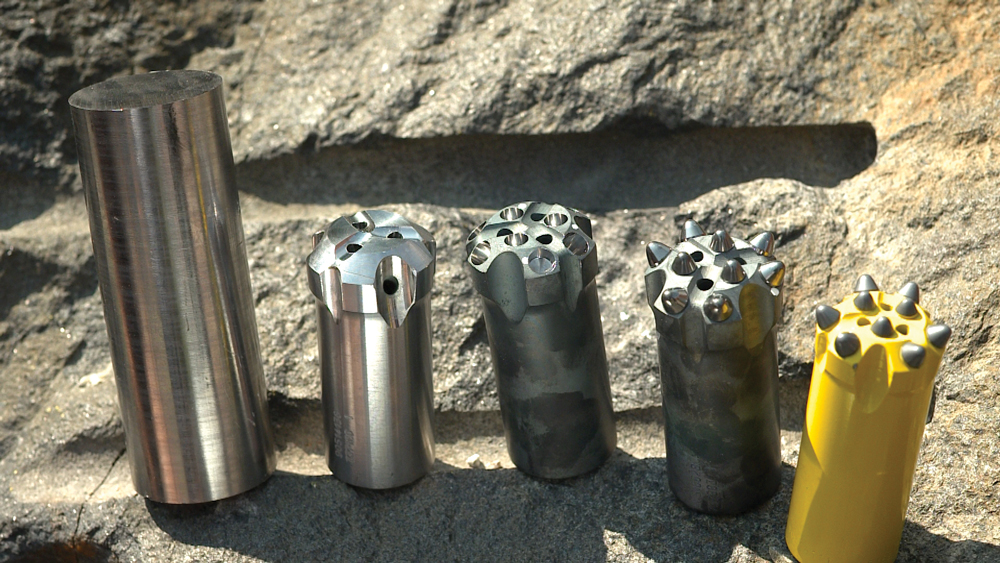
First published in the March 2016 issue of Quarry Management as Achieving Higher Grades
Raising the power and extending the lifecycles of rock drills with advanced clean engineering steels
Atlas Copco’s mining and construction equipment operation needed to reduce its running costs yet also realized that cost-cutting alone would not be enough. Instead, with advanced isotropic IQ-Steels by Ovako, the company has raised the output power of its rock drills so its customers can now eliminate breakdowns and achieve more cost-effective operations, as Patrik Ölund, head of research and development at Ovako, explains.
Constant pressures on margins and declining prices are forcing the mining and metals industries to find and adopt new ways to increase their efficiency and productivity, while also reducing energy use, improving safety and cutting costs. Such demands require that projects are built economically, on time and to scale with either minimal changes to the design or a flexibility of design that reduces risks.
These objectives have, however, been hindered by inadequate performances in conventional steels. Standard materials are failing due to exposure to the kinds of cyclic stresses over long periods that are typical in demanding mining and construction applications. Fatigue is normally the limiting property in these instances, and its influence on the lifecycles of components is a foremost concern for companies.
One way in which companies can solve these issues is by levering new technologies. Steel innovations are crucial in helping mining companies to cut costs and increase efficiency, and can also help them get ahead of the competition by advancing their exploration capabilities.
The Rock Drilling Tools division of Atlas Copco Secoroc, producers of mining and construction equipment headquartered in Nacka, Sweden, realized that mere cost-cutting alone would not be enough to deliver the levels of sustainability that its customers require.
Instead, the manufacturer understood that the real answer was in producing rock drilling tools capable of longer service lifecycles. For Atlas Copco’s customers, this would mean longer intervals between any major equipment overhauls, thereby reducing the number of stoppages needed to perform maintenance or replace vital parts.
The result would be more efficient and cost-effective operations, but to achieve this successfully Atlas Copco would require better-performing engineering steels from which to manufacture their products, which is why the company entered into a partnership with Ovako.
Decades of fatigue research
Ovako, Swedish manufacturers of advanced engineering steels, are among the companies that are leading significant innovations in the research and development of advanced engineering steels. The company has continually devoted itself to fatigue research over decades and, in doing so, has steadily built an extensive database of detailed performance data.
Based on analysis of thousands of fatigue failures with scanning electron microscope (SEM) technology, Ovako engineers are able to demonstrate how the quality of steels significantly impacts the fatigue life of components. The quality of steel pertains specifically to its cleanliness, or the presence of defects such as non-metallic inclusions – foreign substances that are produced by chemical reactions during melting and pouring processes and disrupt the steel’s structural homogeneity – within the metallurgy.
Non-metallic inclusions are shown to create cracks and fatigue failures in steels. This causes many conventional steels to fail when subjected to the non-steady, continuously varying loads and cyclic stresses such as those which occur in demanding mining and quarrying applications.
For the end customer, the most important concern is how the cleanliness of a steel effects its practical performance. This is why Ovako make fatigue testing a frequent and integral part of their process development and benchmarking. Figure 1 illustrates how the manufacturer uses ultrasonic testing to develop cleanliness in its bearing-quality BQ-Steels. This technique is applied on a statistical basis to ensure that high quality is maintained from batch to batch.
Ovako are able to determine the exact amount of stress that is required to initiate a fatigue crack. Generally, the stress required to cause a failure is significantly lower than the steel’s yield or fracture strength – ie the static strength of a structural component. Analysis of fatigue data reveals that a larger defect will require lower stress to initiate fatigue failure compared with a smaller defect.
Factors affecting fatigue strength
The problems with conventional engineering steels arise from the fact that steel is normally anisotropic, or directionally dependent, by nature. Metalworking processes, particularly at the rolling stage, deform inclusions formed in the metal. The defects become elongated so, if the steel is loaded parallel to the rolling direction, then its fatigue strength will be higher than if it is loaded transverse to the rolling direction. This is shown in figure 2 as a complex loading model.
Ovako recommend that one step is to move from conventional steel to BQ-Steel in which fatigue strength can be dramatically increased. A second step is to use a clean IQ-Steel with properties in all directions that can upgrade the performance of, for example, a gear in a transmission, a high-pressure diesel injection component or any other component that is subjected to a high and complex loading and safety critical applications. IQ-Steel can also help avoid the need for costly re-melting processes.
BQ-Steel has a significantly smaller inclusion size distribution compared with conventional grades which greatly improves its fatigue strength, and these properties are further enhanced in isotropic-quality IQ-Steel. The inclusions are fragmented into small and, therefore, harmless particles such that the grade exhibits excellent properties regardless of the direction in which it is loaded.
Smaller-sized inclusions are less harmful for fatigue and are isolated to prevent them interacting as one large stringer, as occurs in standard steels. The result is that IQ-Steel exhibits a greatly reduced difference in fatigue properties in the most and least favourable loading directions.
The findings plotted in the graph (fig. 3a) show that a lower stress is required to initiate fatigue failure in components with larger non-metallic defects. By drawing a line on the graph, separating instances where failure was observed from those where there was no failure, it is possible to identify a correlation between fatigue strength and defect size and how these factors affect fatigue failure.
Removing the data points leaves the simple graph shown in figure 3b with two areas separated by a curve, a ‘safe zone’ where there are no fatigue failures, and a ‘fatigue failure’ zone. From this simplified graph, it can be better understood why the industry has encountered performance deficiencies with conventional steels.
Raising the output power of rock drills
Atlas Copco’s requirements were specifically centred on the impact system, in which the major parts include rock drills that are used in the impact piston. These parts are routinely exposed to high fatigue stress, as shock waves are transferred through the drill string to the drill bit in order to create the rock drilling action.
With limited inclusions compared with standard steels and better fatigue strength, cleaner steels from Ovako are well suited to mining applications and for the manufacturing of drill bits, shank adaptors, drill rods, coupling sleeves and other high-stress components. Ovako identified IQ-Steel as the best solution for Atlas Copco, and the isotropic-quality material was implemented in the major parts of the impact system.
‘Ovako steels have stable properties, thereby allowing us to keep appropriate stress levels in the parts in the impact system without excessive safety margins,’ explained Per Jonsson, mechanical design engineer for R&D Rock Drills within Atlas Copco’s Rocktec division.
An advantage of IQ-Steel is that the stress levels can consistently be kept near the maximum limit of the material, so the shock waves produced by the impact system remain at such a high level that Atlas Copco can get the best performance out of their rock drills.
Mr Jonsson said: ‘The selection of IQ-Steel grades from Ovako has allowed us to achieve our objectives. It has made it possible for us to raise the output power of the rock drills due to the increased fatigue limits resulting from the reduced number of impurities in the IQ-Steel material. The quality and low impurity content helps us to eliminate breakdowns and increase the service life of the impact system parts. This has reduced the running cost.’
Going forward, the most pressing challenge for Atlas Copco is further reduction of their customers’ running costs by helping them to achieve even longer service intervals between major overhauls or replacement of vital parts, while also maintaining or increasing the performance of the rock drills. Ovako continue to work closely with the company and have regular co-operation meetings where current production matters, improvements and future developments are discussed.
Moving towards a renewable future
Aside from the performance advantages, Ovako have also developed their IQ-Steel and BQ-Steel engineering steels in response to the mining and construction sector’s increasing evaluation of renewables as a possible source of cost-effective and reliable energy.
Many of the world’s largest mining companies are examining greater use of renewable energy plants, and this trend is set to intensify rapidly as companies seek to deliver long-term fixed electricity prices and availability while also minimizing their exposure to regulatory changes, market pricing and external fuels.
Ovako are the largest recyclers of steel scrap in the Nordics, and their devotion to climate-friendly products and manufacturing processes is already evident in their working relationships with mining and construction customers. ‘Ovako and Atlas Copco both strive to reduce the environmental impact of their enterprise and products by using environmentally friendly production methods. These methods reduce energy consumption for our rock drills, extend the service life of parts, as mentioned, and secure the possibility to recycle used parts,’ said Per Jonsson.
The end-to-end strategy adopted by Atlas Copco will be the best approach for companies as the mining and metals industries increase their reliance on renewables. With the use of renewable energy plants set to intensify rapidly, managing cost sustainability will be the major priority as the cost of renewable energy declines and conventional energy increases.
Conclusions
For influencers across the mining and materials sectors, decisions as to whether cleaner steels are best for achieving greater efficiency and productivity will depend very much on whether the economics are proven. In the case of Atlas Copco, the role of IQ-Steels in eliminating breakdowns and increasing service lifecycles offers a clear demonstration of how engineering steels by Ovako can improve upon standard grades in mining and drilling applications.
The improved fatigue strength of cleaner and better-quality grades such as BQ-Steel and IQ-Steel can help customers towards operational, weight, safety and cost-saving advantages – all as part of a broader strategy.
- Subscribe to Quarry Management, the monthly journal for the mineral products industry, to read articles before they appear on Agg-Net.com