Primary Breaking - The Viable Alternative
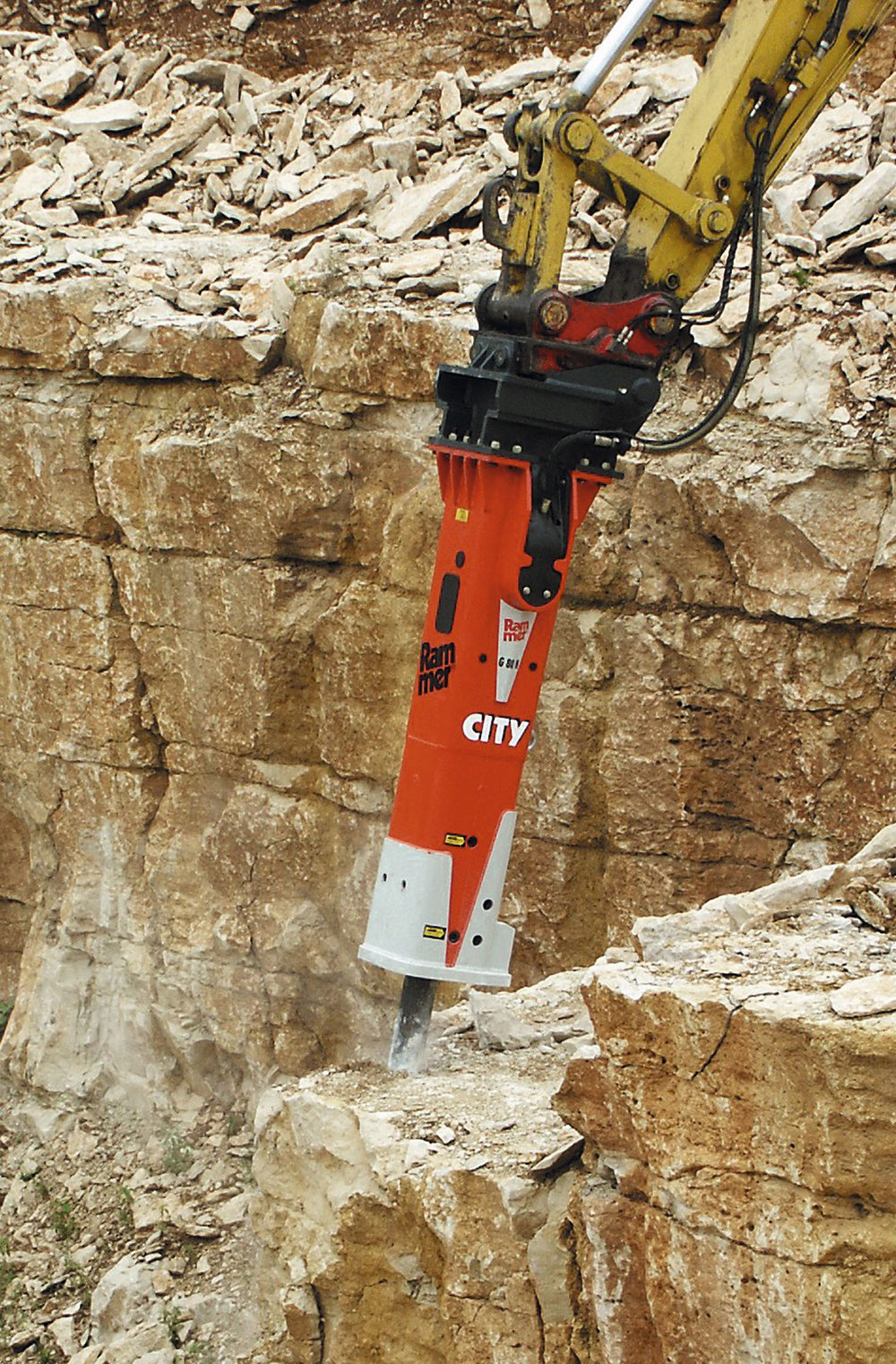
Primary breaking with hydraulic hammers is not the panacea for all drill and blast problems. But, in the right application, it can be a viable economic and environmental alternative. Alan Matchett, business manager – Rammer, Metso Minerals (UK) Ltd, explains
Explosives have been an integral part of the extractive industries for more than a hundred years, and today drilling and blasting techniques are commonplace in quarries and mines the world over. But explosives bring with them a variety of obvious and unseen hazards and potential problems. The potential hazards of flyrock, evidenced by damage to machinery and injuries to site personnel, are all too real, as are complaints from nearby residents that have grown tired of the highly disruptive noise pollution, dust and vibration caused by blasting.
Perhaps less well known is the potential hazard of nitrogen oxide (NOx) releases from blast sites as a result of incomplete combustion, caused by a lack of proper confinement or the ingress of water into the blasting agent. Industry experts have also suggested that residual nitrates from an explosive detonation have the potential to contaminate groundwater.
As the extractive sector becomes ever more environmentally aware, many mine and quarry operators are seeking a viable replacement for drilling and blasting. Numerous alternatives have been postulated, ranging from the use of high-pressure water cutting, through the deployment of concentrated microwaves, to the as yet unproven use of high-powered lasers.
Yet while such techniques remain the stuff of dreams and drawing boards, in many applications only one method has proved to be a truly viable economic and environmental solution – primary breaking using hydraulic breakers.
What is primary breaking?
Essentially rock breaking is about making pre-existing cracks larger. Crack propagation depends on the type and strength of the material, and the length of pre-existing cracks. Material strength depends strongly on stress state: the tensile strength of rock is typically 10–20% of its compressive strength. This is used when breaking rock with a hammer; the stress state inside the rock actually is tension, even though the load appears to be compressive.
Rock will not break if the applied stress, in this instance hammer blow energy, is too low. If the stress applied to the rock is really low virtually nothing happens; the rock simply acts like a spring and all the energy is returned to the hammer. This can also be seen in primary breaking compact hard rock when tool penetration stops; in laboratory tests this is shown to be typical for stress levels below 30% of material strength. In the next stage, 30–60% of material strength, the rock may be broken to dust at the tool tip – creating large cracks with insufficient power will take a long time or prove impossible. If the given stress created by the hammer is more than 60% of the rock strength, the breaking threshold has been reached and efficient rock breaking is possible.
Rock breaking threshold
Every rock has a breaking threshold, and usually the harder the rock the higher the threshold. With softer rocks that have a low breaking threshold, a low-impact-energy hammer will break the rock relatively quickly because it delivers its blows rapidly. A high-impact hammer may take slightly longer because its blows are delivered more slowly. However, it will break the rock into smaller pieces and so could be considered more efficient in some applications.
In the case of harder rocks with a high breaking threshold, a high-frequency hammer will take many more blows to complete the job because of its lower impact energy, and on very hard material may not break it at all, but merely drill a hole. The high-impact-energy hammer will be more productive not just because it has the power to overcome the breaking threshold of the rock, but because it will get there much sooner.
Application matching
It is, therefore, very important to ensure that the correct hammer and tool combination is selected to match both the application and, of course, the carrier to suit the hammer. The set-up of the hammer can also be ‘tuned’ to suit the application and type of material, as stress waves created by the hammer will vary according to power and blow rate. To achieve optimum application compatibility, a major Italian supplier of hydraulic hammers for primary breaking employs qualified geologists as part of its team, with great success.
Operator skills can also have a major input. Knowing where to place the tool for effective crack propagation and when to reposition it during the breaking process can have a significant impact on productivity.
The quality of construction of the hammer is also important. Primary breaking is a tough and demanding application requiring: high impact energy; a high-power hammer; and the design, construction and materials to withstand the enormous working forces.
A robust, wear-resistant housing is important for moving material around, and the hammer should include an effective vibration-damping system to protect the carrier and operator from unnecessary stress and strain.
Moreover, the hammer is as much a machine as the carrier, so a structured service and maintenance package will pay dividends in terms of availability and operating costs.
More than just quiet
The steady growth in the size, power and durability of hydraulic hammers over the past 20 years has seen their popularity increase and their diversity of application spread. Equally important, significant breakthroughs in sound attenuation have helped reduce the noise emissions from even the largest hammers to less than 85dB(A), considerably less than the noise from blasting, and with a fraction of the dust. It is for this reason that the majority of hydraulic hammers sold into primary breaking applications reside in quarries close to residential or commercial properties, or where blasting is restricted or totally prohibited.
Another environmental advantage of primary breaking with hydraulic hammers is that they generally work on considerably lower bench heights, which can reduce significantly the ultimate cost of site reclamation.
However, there is more to primary breaking than merely lower noise levels and reduced environmental impact.
Enhancing rock value
Blasting can cause the formation of micro-cracks in quarried rock that may decrease its quality and, therefore, saleable value. Blasting also often causes high levels of unwanted fines, driving down sales values still further.
Both of these pitfalls can be overcome by the use of primary breaking. By reducing fines, the saleable production volume in the required grain sizes can be increased as much as 5%. In addition, in the hands of an experienced and well-trained operator, a hydraulic hammer can be significantly more selective, avoiding lower-value rock, reducing the mixing of different material grades and enhancing the sales value of the end product.
Furthermore, a well-trained and experienced operator can determine the fragmentation of the rock before initial crushing. Not only can this reduce wear and maintenance costs at the crusher, in some instances it has allowed a large primary crusher to be replaced with a smaller, more cost-effective unit.
Matched to modern methods
Probably the largest single factor in favour of primary breaking over blasting, however, is its ability to match the working methods favoured by an increasing number of modern quarries.
The introduction of tracked crushers has been responsible for a major reconfiguration of many of today’s quarries. In the past, dumptrucks would have hauled shot rock sometimes hundreds of metres to a static crushing plant for processing. Today, however, those long hauls have been superseded, with a single wheel loader or hydraulic excavator feeding a mobile crushing plant stationed close to the quarry face.
It is true that mobile crushing systems are often used in quarries where blasting is commonplace. But the exclusion zone stipulated by current health and safety legislation dictates that crushing, screening and conveying equipment, together with their respective operators, be removed several hundred metres away from the blast site, interrupting production and reducing both efficiency and plant utilization.
By switching to primary breaking methods, crushers, screens and other equipment can remain at the face during rock breaking, eliminating interruptions, allowing continuous production and thereby raising production levels.
Cost-effective?
The safety, environmental and logistical advantages of primary breaking over drilling and blasting are obvious. But in these days of cost-per-tonne analysis and wafer-thin margins, is primary breaking actually cost-effective?
Experience in one Finnish limestone quarry certainly suggests so. When primary breaking techniques were used to replace secondary blasting, the quarry operator saw a 67% reduction in costs together with increased production levels and greater accuracy. And this figure does not even take into account other indirect costs associated with blasting, such as interruptions to other work, machine downtime, safety measures etc.
But against this highly positive background, even the most vocal advocate of primary breaking would struggle to suggest that it offers a universal alternative to the use of explosives. It is also true to say that comparatively low production rates and hammer and carrier owning and operating costs can combine to make primary breaking unsuitable in many applications.
Yet, as many users around the world are proving, primary breaking is an essential weapon in the armoury of the modern quarry operator. In applications where the rock formation, compressive strength and fragmentation are conducive to the percussive breaking characteristics of a large, powerful hydraulic hammer, it most certainly is an alternative.
For any quarry operation bordered by residential or commercial property, restricted by noise, dust or vibration legislation, or facing closure due to environmental pressures, primary breaking using hydraulic hammers could prove to be the only viable means of getting rock from ground to customer.