Pre-Split Techniques: A Review
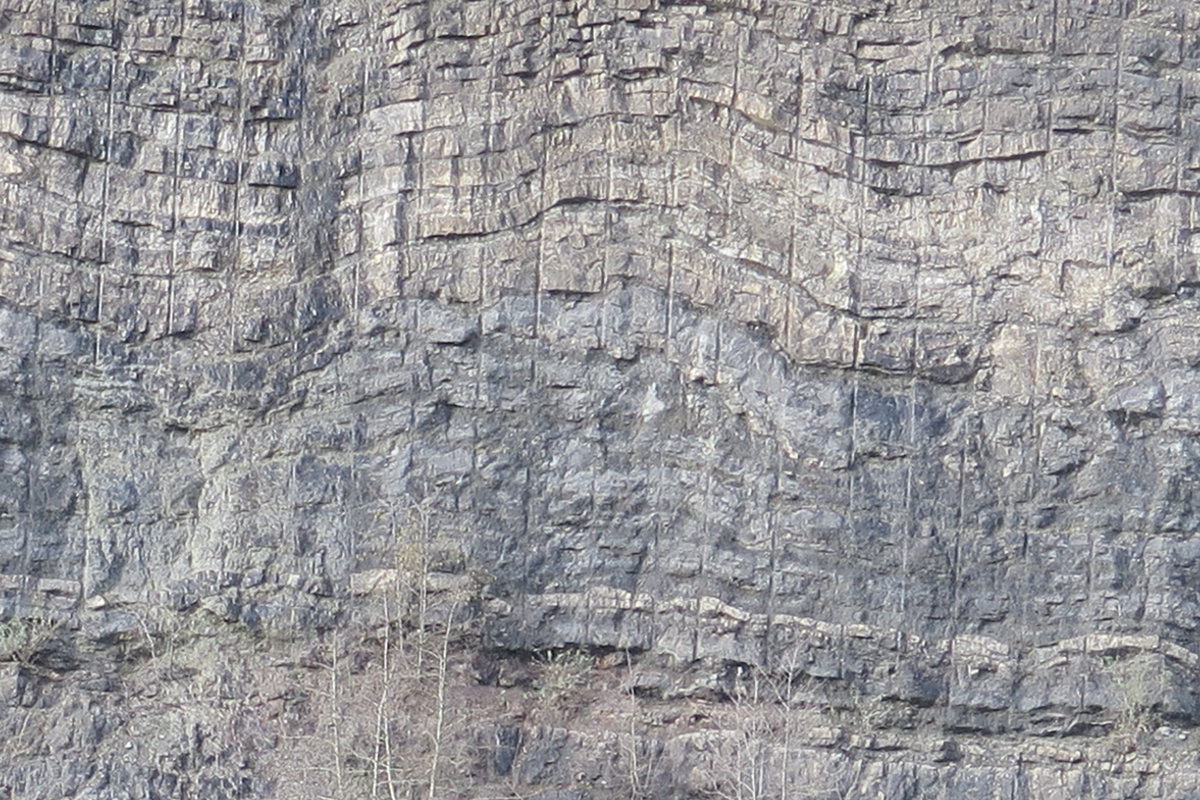
First published in the April 2020 issue of Quarry Management
Julian Cleeton, director of Stemtek, examines the conventional and alternative methods for achieving a stable face
Pre-splitting can be defined as ‘a technique using lightly charged, closely spaced holes to induce a fracture plane along a required design profile, which isolates the rock to be blasted from the surrounding rock mass’. The holes are generally fired instantaneously well in advance of any blasting in the adjacent rock. Alternatively, by suitable delay sequencing, they can be fired in conjunction with the same blast. The main objective is to produce a stable face that requires little or no maintenance over its design life.
The use of pre-splitting to create a smooth final wall in rock excavations has been well established for many years. Whilst it is common in road and rail cuttings and other civil engineering operations, it has been used a lot less in quarries. However, with a general duty to ensure safety of excavations as required by the Quarries Regulations, and the often pressing need to maximize reserves, operators are looking more closely at the benefits of good-quality final faces and the means of achieving them.
Conventional methods
Whilst several manufacturers have produced bespoke pre-split products, most users have gone down the route of employing a single line of high-energy cord (100g/m) or two/three strands of 40g cord taped together. This is lowered down the hole usually with a pill of packaged explosive taped on the end. The cord is cut so that it is a couple of metres shorter than the length of the hole. A length of 10g cord is then taped on to the end of it and connected to a length of similar cord running along the top of the holes. A plastic bag is pushed down about 2m to block the hole and support the dust or chippings used to stem it. In order to cut down the noise and reduce stemming ejection, the surface cord and line of holes is usually covered with old conveyor belting, considerable quantities of dust and maybe netting as well. For pre-splitting to be effective, as well as firing the holes instantaneously it is preferable to fire as many as possible in a single event.
A number of other methods are used, generally involving spacing explosives throughout the hole either by decking or taping them on to a line of detonating cord.
With regard to spacing and hole diameter, the most common parameters are 1m and 105–115mm respectively, the former chosen almost regardless of the rock type and the latter since these are the most common diameters used in conventional UK drilling operations.
A significant factor which has limited the use of pre-splitting is the cost involved. Drilling holes at 1m spacings and then charging them with detonating cord is a very expensive and labour-intensive procedure. Most quarries do not have the drilling capacity to cope with both production and pre-split holes, so hiring in may be necessary. Even if it is considered, the results cannot always be guaranteed, further inhibiting its use.
Alternative methods
In many large overseas opencast operations, it is common practice to pre-split the high wall of the excavation, principally for safety reasons. Given the temporary nature of these high walls and the expense of conventional pre-split operations, these operations developed a much more cost-effective system. Since they are using large-diameter holes, the same drills are employed for the pre-split line. Large spacings are adopted, typically 15–22 x hole diameter. In order to load the holes quickly and cheaply, they use a small base charge of ANFO, initiated with shocktube or long-lead electric detonators, and block off the hole near the surface using a gasbag. The explosive column is typically 10% of the hole length. If the holes are in excess of 20m, the usual practice is to split the charge with 60% in the base and the remainder halfway up, supported by a gasbag.
UK experience of alternative methods
The above method was used in a major trial at a limestone quarry some years ago. The quarry had used the conventional method for many years with good results. An area of the quarry was identified as being suitable for the trials. It satisfied the main criteria of being long enough to accommodate at least three good-sized blasts and that the pre-split would be uncovered quickly.
The 20m face was split into three sections. The first section consisted of 40 holes, 23m deep, 100mm diameter at 20º on 1m spacings. These were charged in the conventional manner, as previously described. The holes were covered with pieces of old conveyor belting and considerable quantities of dust. On firing, significant movement of the covering was detected.
The second section of 40 holes used exactly the same parameters. The only difference was that the 100g cord stopped 3m from the top of the hole, with the 10g cord being replaced by zero-delay 5m long electric detonators taped on to the top of the 100g cord. A gasbag was placed at 2m and the hole stemmed off with 10/14mm chippings. No covering was placed over the holes. The main drawback with this method was the need to tie a length of rope to the end of the 100g cord to support it in the hole. On firing, no stemming ejection of any consequence was observed. The quality of the pre-split was no different from the first trial.
The third section consisting of 20 holes was designed using the alternative method guidelines. The spacing was increased to 2m (20 x hole diameter). A base charge of 10kg of packaged emulsion was used due to the wet conditions, with a 5kg charge of the same explosive at 12m sitting directly on a gasbag. Gasbags were placed at 2m and the holes stemmed off. Initiation was by means of shocktube and zero surface delays. In order to reduce any possible delay effects due to the speed of the signal passing through the tube, the holes were fired from the centre with 10 holes either side. No covering of any kind was used. On firing, no stemming ejection was observed. The result achieved was of the same quality as the other two sections. It may be argued that with holes at 2m spacings the face might be expected to be more stable over the long-term.
Conclusions
The main difference between conventional and air-deck methods is the time and cost involved. Drilling may be reduced by 50%. The cost of consumables is dramatically reduced too. The time taken to load holes is about a third of that for conventional ones, with much less manual handling, so more holes can be loaded per shift. Subject to suitable ground conditions, there may be no need for covering with belting and large quantities of dust, which involves a lot of time, effort and equipment to put in place.
- Subscribe to Quarry Management, the monthly journal for the mineral products industry, to read articles before they appear on Agg-Net.com