Going For The Top
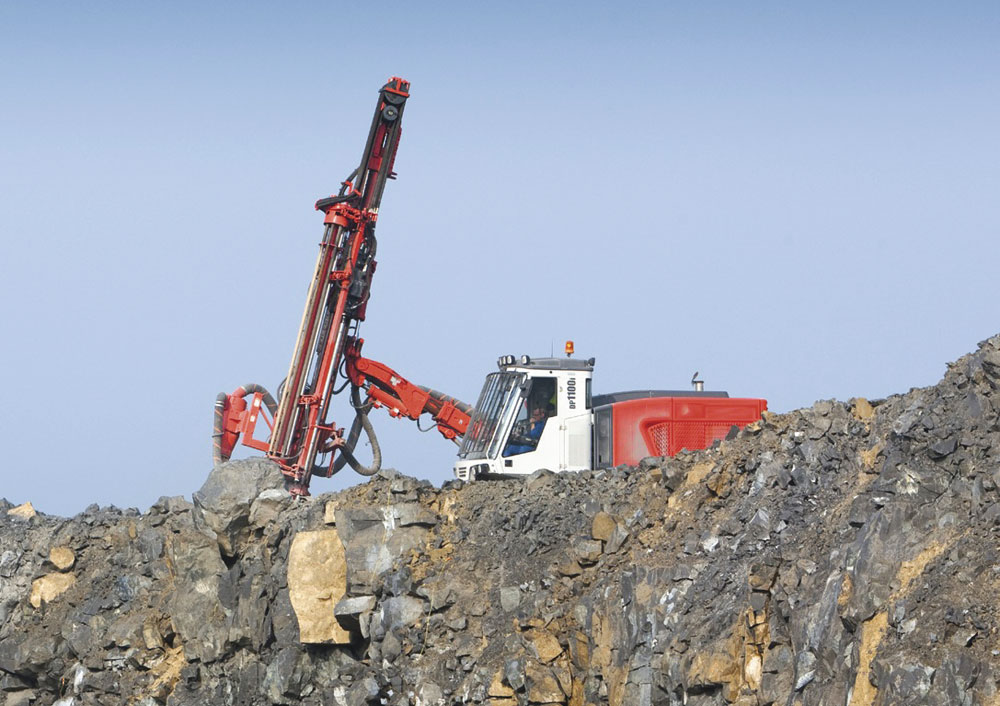
Top-hammer drilling sees new interest in the UK
During the 1960s and 1970s many UK quarries were littered with drilling tool scrap in the form of bent and broken extension rods, extracted after becoming stuck in the hole. At this time the majority of holes drilled by top-hammer rigs were between 89mm and 115mm in diameter, and the small 38mm diameter extension rods were soon exchanged for the down-the-hole (DTH) method using tubes, hammers and bits.
Meanwhile, the rest of Europe and Scandinavia continued with top-hammer drilling, largely due to a preference for smaller hole diameters of 64–92mm, and today this method of drilling still predominates on the continent, while DTH drilling remains the preferred method in the UK.
However, according to Sandvik, who have a long history and considerable expertise in the field of top-hammer drilling, today’s top-hammer drills are far removed from those associated with the rigs of three or four decades ago. Currently, more than 450 Sandvik DP rigs (formerly Pantera) are operating around the world with Sandvik GT60 drilling tools, and Germany alone has more than 70 units in operation.
And Sandvik say they are now seeing a renewed interest in top-hammer drilling in the UK, with sales of these rigs slowly increasing as drilling contractors, in particular, add them to their fleets.
‘There has been a long-held belief in the UK that DTH is the superior method,’ said Sandvik Mining and Construction capital equipment sales manager Mark Haywood. ‘Often this is just a comfort-zone approach, with DTH generally accepted as best practice. But technology has moved on and DTH is not necessarily the right solution for many applications.’
According to Mr Haywood, the reduction in bench heights in UK quarries, coupled with smaller hole diameters, means the power and faster penetration rates of a top-hammer drill can be fully utilized. Moreover, hole quality is now very good and fuel consumption is low, making top-hammer drilling a cheaper option than DTH, which is an important consideration in times of rising fuel prices.
‘A couple of significant UK drilling contractors have realized this and are working closely with us as we seek to change the perception of top-hammer drilling in the UK,’ explained Mr Haywood. ‘We are making strong inroads but there is still a big job to be done. However, with our top-hammer product range, we believe we stand a good chance of changing the market.’
Sandvik currently offer the DX (former Ranger) top-hammer series for construction and small-to-medium size quarries, while their DP range is available for larger, high-production quarry applications. Key advantages of Sandvik’s top-hammer drilling machines include:
- a RockPilot drilling system that automatically adapts feed and percussion pressures to suit varying rock conditions, giving straighter holes, longer tool life and reduced maintenance costs for the rock drill
- greatly improved drill steels offering longer life, straighter holes, fewer jammed steels and increased production
- high versatility – the same DP rig can drill hole diameters from 92mm up to 152mm
- reduced carbon footprint – typically, a DTH drill will use 50–60 litres of fuel per hour, whereas a top hammer will use only 25–35 litres/h
- straighter holes and long service life with GT60 extension rods and Retrac bits
- fast penetration rates and improved drilling tool life with HL1000 and HL1560 rock drills
- a power extractor should withdrawal of the drill string become difficult.
Case study
At a recent site demonstration at Lafarge Aggregates’ Mountsorrel Quarry, the quality of the holes drilled by a Sandvik DP1100 top-hammer rig equipped with an HL1560T rock drill was found to be significantly better than those drilled by a competitor’s high-pressure, high-volume down-the-hole drill.
Utilizing an 87mm diameter, 4.3m GT60 pilot tube, GT60 4.3m extension rods, 115mm ballistic and HD Retrac bits and an HL1560T shank adapter, holes were drilled in the Mountsorrel granite to a depth of 20m at an angle of 15°.
A number of the resulting 115mm diameter holes were checked by Glyn Barnes, contracts manager – drilling and blasting with BAM Ritchies, who confirmed that a torch was visible at 20m, whereas in the DTH-drilled holes the torch was not visible at 18m. Moreover, hole inclination was found to be more accurate and hole quality, especially at the top, was significantly better than the DTH-drilled holes.
Significantly, fuel consumption for the Sandvik DP1100 rig was 42 litres/h, while the DTH drill worked out at 78 litres/h.
Commenting on the trial, Mr Haywood said: ‘Not only were the top-hammer holes of a higher quality, the fuel used to drill them was almost half that required by the DTH rig. Down-the-hole territory is now definitely under threat from the top hammer.’
For further information, contact Mark Haywood on tel: (01283) 818400; email: mark.haywood@sandvik.com